Ensuring the availability of maintenance materials is considered a critical factor for asset maintenance operations. It is an essential factor that determines the success of organizational maintenance operations. Material availability can make or break an organization’s effectiveness. In today’s fast-paced industrial environment, ensuring the availability of suitable material at the right time and shape is crucial for minimizing asset downtime and maintaining smooth operations.
This blog will explore critical strategies that businesses can implement to ensure the availability of materials, from proper demand forecasting and inventory management to robust supplier management and advanced practices that keep operations running smoothly. Let’s show how emerging maintenance management software like Fogwing CMMS transforms the process with advanced technologies.
Why Does Material Availability Matter in Maintenance?
Before exploring the strategies, it’s essential to understand why material availability is critical in maintenance operations. Availability of the material is not just about the correct parts; it’s about minimizing unplanned downtime, repair time, operational continuity, and overall plant performance. Unplanned downtime can be highly costly in production and cause potential damage to assets. Moreover, material storages tie up capital in organizations, which can cause critical delays. Striking the right balance between material availability and cost-effectiveness is vital to an efficient maintenance operation.
The Impact of Material Shortages on Organizations
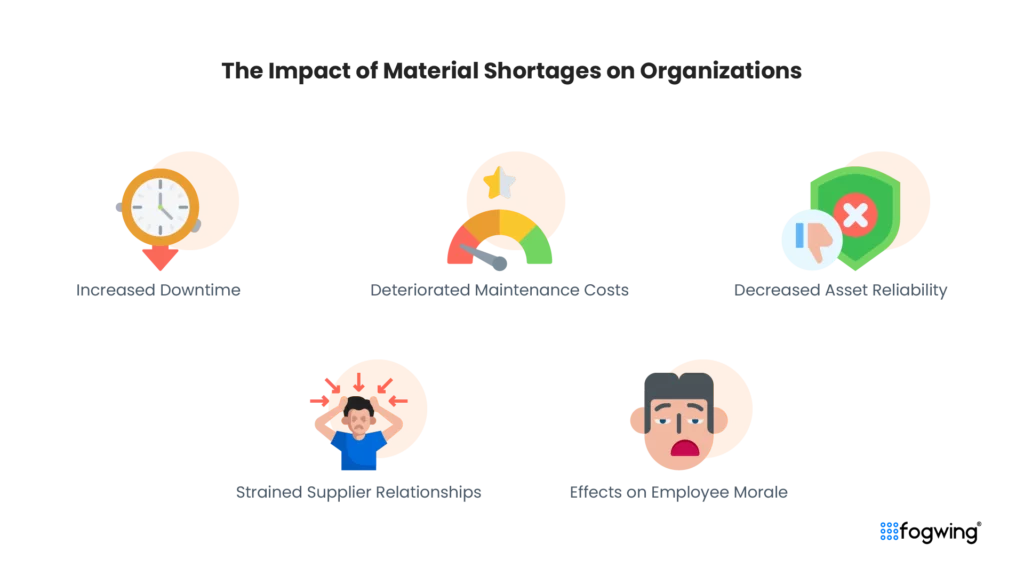
Material shortages can have far-reaching consequences in maintenance operations. Here’s how a lack of necessary material availability can impact your organization:
- Increased Downtime: In an organization, it is difficult for the maintenance team associated with asset maintenance to conduct the required repair or preventive tasks when there are material shortages or unavailability of critical parts. It eventually leads to increased asset downtime, halting the organization’s production line and disturbing the entire supply chain. The longer the asset downtime, the higher the financial loss due to the lost production and missed delivery deadlines.
- Deteriorated Maintenance Costs: The lack of material for asset maintenance often forces organizations to conduct expedited shipping or source maintenance-related parts from more expensive suppliers at the last minute to meet their maintenance needs and reduce asset downtime, eventually resulting in increased maintenance costs. The lack of material availability can also result in an inability to perform timely maintenance tasks, resulting in costly repairs.
- Decreased Asset Reliability: Organizational maintenance is essential for asset reliability and extending lifespan. When maintenance material is unavailable, scheduled maintenance tasks are delayed or skipped, leading to increased wear and tear on equipment. Over time, material shortages can lead to frequent breakdowns, increased repair costs, and premature asset failure.
- Strained Supplier Relationships: Frequent material shortages can strain an organization’s relationship with suppliers, mainly if they result in frequent last-minute changes, rushed orders, or missed deadlines. Maintaining a good supplier relationship can help organizations negotiate beneficial terms and ensure material availability in the future.
- Effects on Employee Morale: Having inconsistent access to materials can prevent the maintenance team from fulfilling their responsibilities, eventually leading to frustration and decreased employee morale. The lack of materials can make them feel they are being set up for failure, affecting overall productivity and job satisfaction.
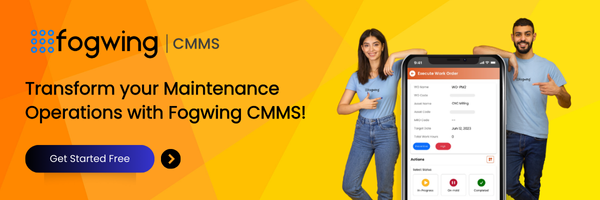
Understanding the importance of the availability of materials
The lack of material directly impacts the efficiency of asset maintenance operations in organizations. The need for more parts at the right time can delay the maintenance task, leading to asset downtime, decreased equipment reliability, and increased costs. Fogwing CMMS, an intelligent maintenance management software, understands the importance of material availability and helps organizations implement effective strategies to ensure it. Here are the reasons why the availability of materials is essential.
Impact on Productivity and Downtime:
Maintenance teams are forced to wait when insufficient materials exist, leading to prolonged asset downtime. Downtime cascades the production process by causing delays, potentially leading to missed deadlines. Material shortages and uptime are crucial in industries like manufacturing and utilities. Downtime can significantly affect the production time and supply chain. Software like Fogwing CMMS helps organizations minimize delays and keep production running smoothly.
Repercussions of material shortages on cost:
Lack of maintenance-related materials affects production and increases costs. When there is an issue with material availability, organizations must expedite orders, pay extra for shipping, or source materials from alternative suppliers at higher prices. The unplanned downtime and production stop due to the material shortages eventually lead to revenue loss and increased workforce costs as maintenance teams work extra to finish the delayed maintenance tasks.
A well-designed inventory management system like Fogwing CMMS enables organizations to manage maintenance operations effectively. It acts as a backbone to ensure the availability of maintenance parts. It helps organizations track inventory levels, forecast demand, and manage replacement effectively. The Fogwing CMMS platform aligns material orders with maintenance schedules. It helps organizations keep track of large quantities of materials on hand. It also enables a strong supplier relationship. Organizations can create a PO request and send it to the supplier whenever needed with the target date mentioned. Fogwing CMMS helps organizations manage material availability and ensures maintenance tasks are conducted without breakdowns.
Implementing a Robust Inventory Management System with Fogwing CMMS
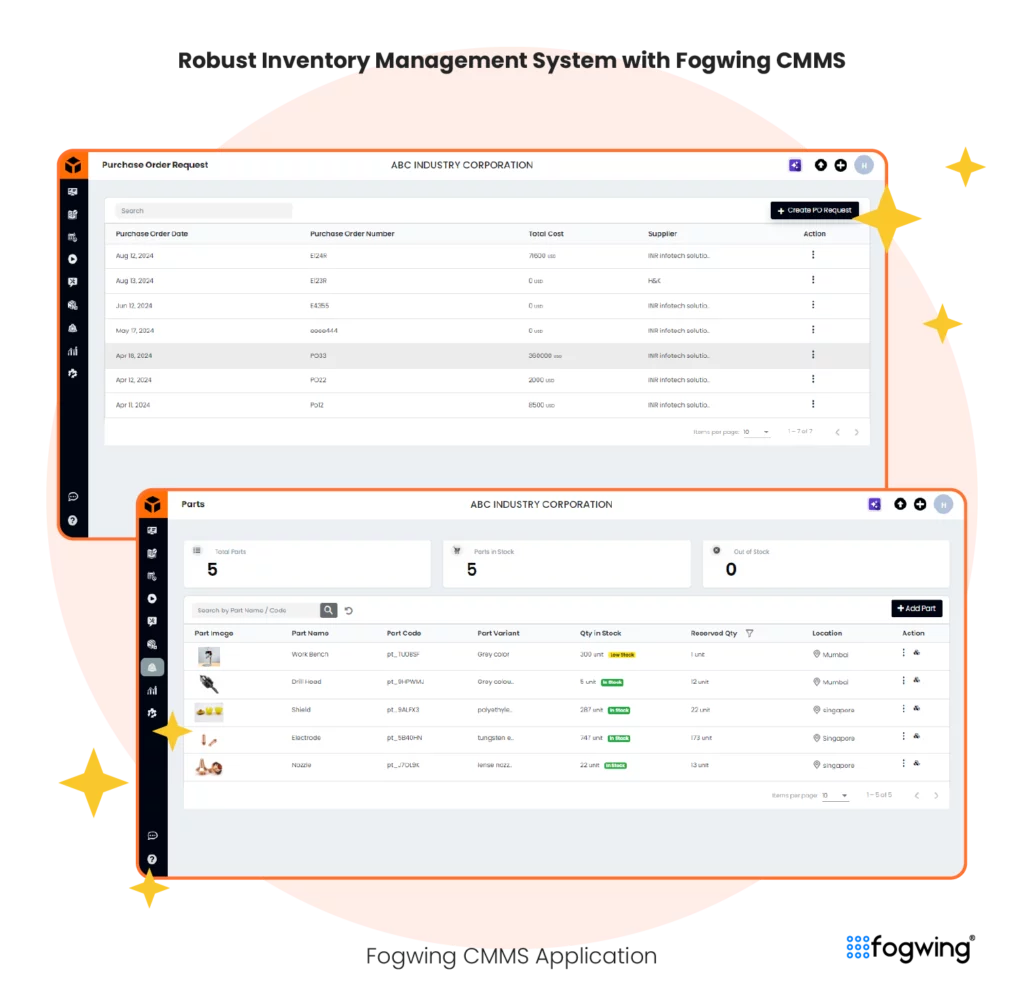
Fogwing CMMS software integrates inventory management and maintenance scheduling and helps businesses track, manage, and forecast material needs in real time. The centralized platform for maintenance management ensures the availability of materials when required by allowing the maintenance team to monitor stock levels, reorder details, and usage history.
Real-time tracking: With Fogwing CMMS, maintenance teams will be notified when the parts count reaches the Minimum Quantity Threshold mentioned while creating the parts on the platform.
Easy Reorder: The system enables the maintenance team to easily create purchase order requests when the quantity of parts exceeds the minimum quality threshold. The application will display a Low Stock symbol if the parts exceed the minimum quality threshold.
Centralized Inventory Management: The platform enables organizations to manage all maintenance-related inventory and material availability from a single dashboard. The data provided by the platform helps organizations minimize stockouts and overstocking.
Accurate Demand Forecasting with Fogwing CMMS
Fogwing CMMS enables maintenance teams to forecast material and demand availability and maintenance costs by analyzing historical data and integrating preventive maintenance insights. It allows for better planning and part availability.
Historical Data Analysis: Fogwing CMMS leverages past maintenance records to predict future material needs, helping to anticipate when specific components require replacement. It allows organizations to calculate the need for material availability, helping them effectively organize the necessary materials for asset maintenance.
Internet of Things (IoT) Integration: Using IoT sensors, Fogwing CMMS can forecast equipment failures, automatically generating maintenance tasks and material requests well in advance.
Dynamic Forecasting: The Fogwing CMMS platform’s advanced reports and metrics feature enables teams to adjust their material requirements and supplier-managed inventory based on real-time data, allowing for flexibility in stocking levels.
How SMI helps ensure material availability in maintenance operations
An inventory management system plays a critical role in maintenance operations. It ensures the availability of essential materials and spare parts, minimizing asset downtime and maintaining operational efficiency. One strategy that has been effectively established is SMIs. It is a process where parts suppliers monitor, manage, and replenish inventory on behalf of a company. This collaboration eventually reduces the burden on maintenance teams while ensuring that suitable materials are available when required.
Here is how SMI contributes to material availability in maintenance operations:
- With SMI, suppliers can closely monitor stock levels and take responsibility for replenishing items before they run out.
- SMI strengthens the relationship between the organization and its parts suppliers since they are directly involved in inventory management.
- Supplier-managed inventory enables the maintenance team to focus on core activities rather than managing stock levels. It saves the time and effort required for procurement.
- By reducing stockouts and eliminating the need for emergency orders, SMI lowers overall procurement costs. Suppliers can manage inventory more efficiently, often negotiating better prices through bulk ordering or reduced lead times.
In conclusion, Supplier-Managed Inventory is an effective strategy for ensuring material availability in maintenance operations. It enhances supply chain efficiency, reduces costs, and ensures that essential materials are always available, contributing to smooth and uninterrupted operations.
Leveraging Technology for Enhanced Material Management
Technology plays a crucial role in advanced inventory management systems and supplier coordination. By leveraging advanced tools and systems, organizations can enhance their ability to ensure material availability.
Implementing Enterprise Resource Planning (ERP) Systems
Enterprise Resource Planning (ERP) systems integrate various organizational functions, including inventory management, procurement, and maintenance planning. ERP systems provide real-time visibility into parts inventory levels, material usage, and supplier performance, enabling organizations to make informed decisions about material availability and replenishment.
Using Predictive Analytics and AI
Predictive analytics and artificial intelligence (AI) can analyze historical data to forecast future material demand. The technologies can identify patterns and trends, helping organizations anticipate material needs and maintenance costs more accurately and adjust their inventory levels accordingly. AI-driven systems can also optimize reorder points and inventory levels, reducing stockouts or overstocking.
Implementing the Internet of Things (IoT) in Inventory Management
The Internet of Things (IoT) can enhance material management with real-time data on parts inventory levels, material usage, and equipment conditions. IoT-enabled sensors can track material movement, usage, and availability, automatically triggering reorder requests when inventory levels reach a predefined threshold. This automation helps ensure that materials are always available when needed without manual intervention.
Conclusion
Ensuring material availability is a cornerstone of effective maintenance operations, directly impacting productivity, asset reliability, and operational efficiency. As industries evolve, leveraging modern strategies like Supplier-Managed Inventory (SMI) and advanced technologies such as predictive analytics and IoT has become crucial for success. Tools like **Fogwing CMMS** empower organizations to streamline inventory management, forecast material needs, and maintain seamless supplier relationships.
By implementing these strategies, businesses can reduce downtime, minimize maintenance costs, and ensure the smooth functioning of their assets, ultimately driving operational excellence. Businesses can significantly enhance maintenance operations by combining robust supplier management and tech-driven solutions. This holistic approach ensures minimal disruptions, improved asset reliability, and greater cost-effectiveness, ultimately contributing to sustained operational success in a highly competitive industrial landscape.
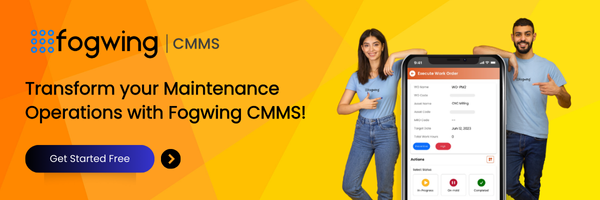