In today’s fast-paced industrial circumstances worldwide, asset maintenance operations are crucial in reducing downtime and ensuring smooth production. Effective supplier management is one significant yet often underappreciated factor in maintaining this efficiency. It is pivotal in maintaining efficiency and directly impacts the company’s operational success. By optimizing the way you manage suppliers, you can enhance the reliability of your maintenance processes, reduce costs, and improve overall operational efficiency.
By understanding the connection between supplier management software and maintenance efficiency, businesses can reduce costs, enhance operational performance, and have a competitive edge in their respective industries. This blog explores the various aspects of managing suppliers and how they directly influence maintenance efficiency, incorporating key concepts like supplier risk management, supplier-managed inventory, and the use of software for managing suppliers.
The Role of Supplier Management in Maintenance Operations
Supplier management plays a crucial role in maintenance operations by ensuring that suitable materials and services are available when required, optimizing costs, and mitigating risks. Here’s how:
Ensuring Timely Supply:
Effectively managed supplier-managed inventory helps maintain an uninterrupted supply of essential maintenance materials. Working closely with suppliers enables you to make sure critical parts and tools are delivered on time, reducing downtime and keeping operations running smoothly. Timely access is crucial for maintaining the continuous operation of machinery and assets.
Cost Management:
Effective supplier relationship management and negotiation skills can help organizations achieve better pricing, bulk discounts, and beneficial payment terms, leading to cost savings in asset maintenance operations. Cost-efficient sourcing in supplier management enables organizations to maintain budgets and can improve overall business profitability.
Quality Assurance:
Managing suppliers involves monitoring the quality of their products and services. Building solid relationships with reliable suppliers helps ensure that the materials and parts supplied meet quality standards. Consistent quality is crucial for reliable maintenance operations in supplier risk management. High-quality inputs result in more effective maintenance, minimizing repairs and extending asset lifespan.
Risk Mitigation:
Supplier administration includes risks associated with the supplier’s performance in maintenance operations. It includes identifying potential issues like supply chain management system disruptions or financial instability and developing contingency plans to address them. Better supplier relationships enable better cost control through negotiated prices and terms, reducing financial risks. Proactive communication and collaboration in supplier management facilitate quick issue resolution, addressing potential before they escalate.
Supply chain management:
Careful selection and management of suppliers help organizations mitigate the risk of supply chain disruptions. Conduct regular supplier performance evaluations to ensure suppliers meet agreed-upon standards and contract terms. A stable supply chain management system ensures that maintenance operations are not hindered by sudden shortages or delays in receiving critical components.
Just-In-Time Inventory:
Organizations implement Supplier-Managed Inventory systems in which suppliers manage inventory levels. It leads to efficient inventory practices and reduces the burden on internal resources. Supplier management also enables Just-in-time (JIT) inventory practices, which reduces the requirement of extensive inventory stockpiles. It reduces the cost of storage and ensures that maintenance teams have access to the exact parts they need when they need them.
Effective supplier management enhances maintenance operations by ensuring reliability, reducing costs, and improving overall efficiency.
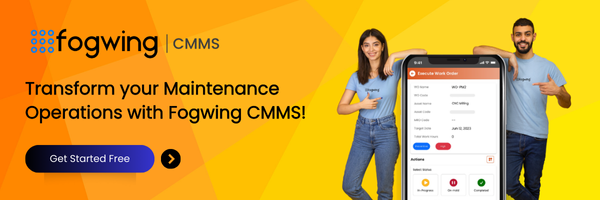
Supplier Risk Management: Mitigating Disruptions in Maintenance
Supplier risk management is crucial for maintaining operational continuity and efficiency in maintenance operations. Here’s how it helps mitigate disruptions:
Identifying Risks: Begin by assessing potential risks associated with each supplier. These include financial instability, supply chain vulnerabilities, geopolitical issues, or natural disasters. Identifying these risks allows you to understand which suppliers might pose a threat to your maintenance operations.
Diversification: Avoid reliance on a single supplier for critical materials. By diversifying your supplier base, you reduce the risk of disruption if one supplier encounters issues. In supplier management, having multiple suppliers for critical components ensures you have alternatives in case of unforeseen problems.
Developing Contingency Plans: Create contingency plans for different types of risks. It might involve having backup suppliers or stockpiling critical materials. Supplier management software, a well-thought-out plan ensures you can quickly respond to disruptions without significantly impacting maintenance operations.
Monitoring Supplier Performance: Regularly monitor and assess supplier performance to detect any signs of potential problems early. Key performance indicators (KPIs) like delivery reliability, quality control, and agreement compliance can help you gauge supplier stability and address issues before they escalate.
Establishing Strong Relationships: Building and maintaining solid supplier relationships can improve communication and collaboration. Good supplier relationship management can lead to quicker emergency responses and better risk management support.
Contractual Safeguards: Supplier contracts should include risk management clauses in supplier management. These clauses cover penalties for non-compliance, performance guarantees, and responsibilities in the event of supply disruptions. Clear contractual terms help ensure suppliers are accountable and prepared for potential risks.
Supplier Audits and Assessments: Conduct regular audits and risk assessments of your suppliers. It can include evaluating their financial health, operational practices, and adherence to quality standards. Regular supplier risk management assessments help identify any changes in risk levels and allow for timely adjustments in your risk management strategy.
Technology and Analytics: Utilize technology and analytics to gain insights into potential risks. Advanced data analytics can help predict disruptions and provide early warnings based on supplier performance data and market trends.
Continuous Improvement: Regularly review and update your supplier risk management practices to adapt to new challenges and changes in the supply chain landscape. Continuous improvement ensures that your risk management strategy remains adequate and relevant in supplier management.
Enhancing Efficiency with Supplier-Managed Inventory
Supplier-managed inventory (SMI) is a system where suppliers manage and replenish inventory levels. This approach can lead to more efficient maintenance operations by ensuring that critical parts and materials are always available when needed, reducing downtime and inventory costs. SMI streamlines inventory management, enabling maintenance engineers to focus on tasks without worrying about downtimes.
Here are five critical ways Supplier-Managed Inventory (SMI) enhances efficiency:
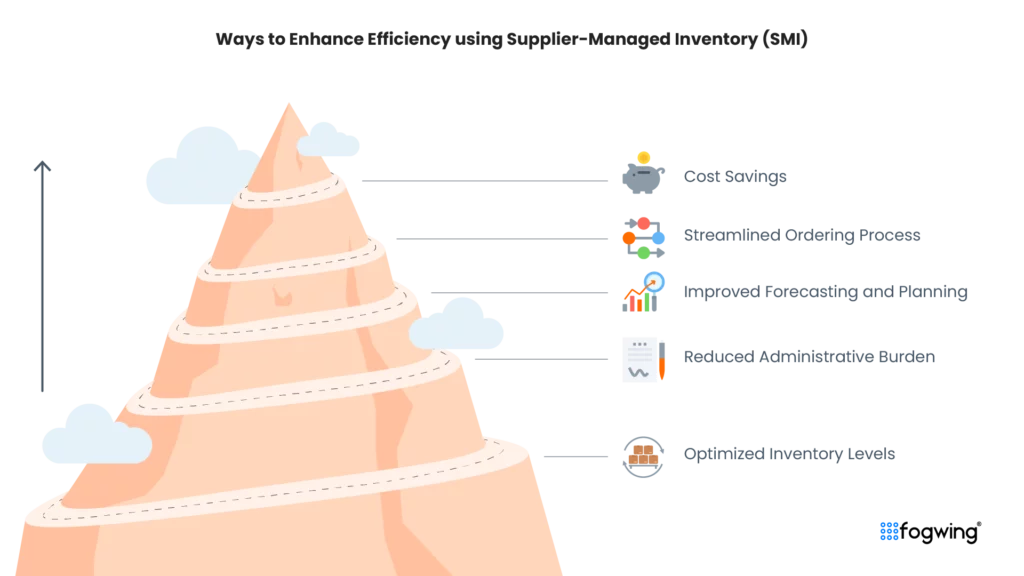
- Optimized Inventory Levels: Suppliers manage inventory based on real-time data and forecasts, ensuring optimal stock levels and reducing overstock and stockouts. The Fogwing CMMS, with a module dedicated to the supply chain management system, enables organizations to easily create and export purchase orders according to their requirements to optimize inventory.
- Reduced Administrative Burden: By having suppliers manage inventory, internal teams can focus on core activities, minimizing administrative tasks and overhead. Fogwing CMMS reduces administrative burdens in supplier management by centralizing supplier data, automating routine tasks, and streamlining communication.
- Improved Forecasting and Planning: Supplier use their expertise in supply chain management systems to provide more accurate forecasts, leading to better planning and fewer unexpected shortages or surpluses. Fogwing CMMS platform centralizes all supplier information for easy access, automates workflows like order tracking and performance monitoring, and offers real-time reporting, reducing manual tasks.
- Streamlined Ordering Process: Supplier management software enables organizations to automatically reorder materials based on pre-agreed triggers, simplifying the ordering process and ensuring timely replenishment. Fogwing CMMS platform’s built-in communication tools streamline interactions, and automated compliance management ensures suppliers meet standards without constant oversight.
- Cost Savings: In supplier management, efficient inventory management through SMI leads to reduced holding costs, minimized stockouts, and potential cost benefits from suppliers’ better pricing or terms. Fogwing CMMS platform’s advanced asset maintenance features enable organizations to prioritize strategic decision-making while maintaining efficient supplier relationships.
Leveraging Supplier Management Software for Better Coordination
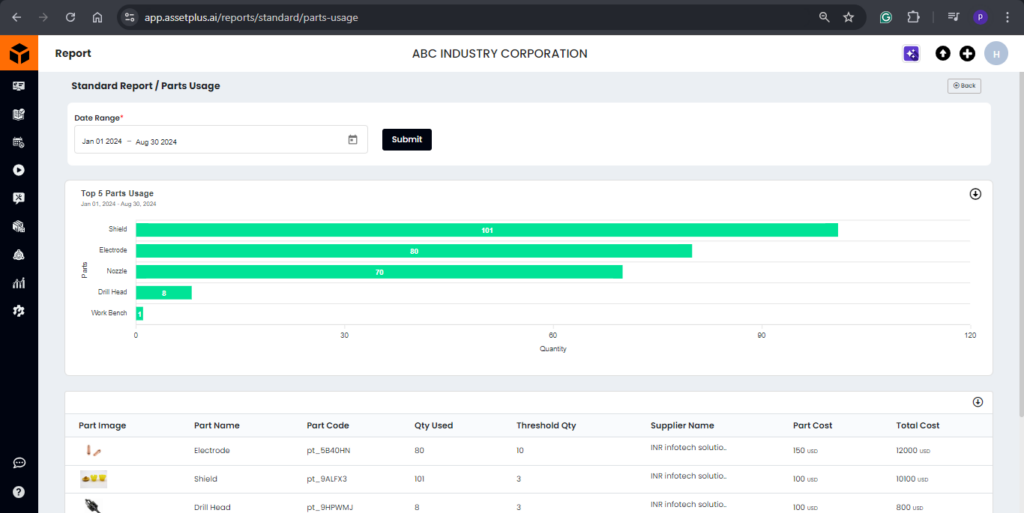
Supplier management software (SMS) acts as a tool that facilitates better coordination between suppliers and maintenance teams. This software helps track orders, manage contracts, and evaluate supplier performance, leading to more efficient and transparent operations. Leveraging SMS can significantly improve coordination and efficiency in supply chain and maintenance operations. Here’s how:
- Centralized Data Management: In Supplier management, SMS provides a unified platform for storing and accessing all supplier-related information. This centralization improves data accuracy and consistency, making managing supplier details, performance metrics, and communication history easier. The Fogwing CMMS enhances centralized data and supplier relationship management by consolidating all relevant information into a single platform, ensuring easy access, real-time updates, and secure storage. It automates supplier workflows, tracks performance, and ensures compliance, reducing manual tasks and improving efficiency in managing supplier relationships and organizational data.
- Enhanced Communication: Supplier management software facilitates better communication between your organization and suppliers through integrated messaging and notifications. It helps ensure that both parties are aligned on requirements, changes, and updates, reducing the risk of miscommunication and errors. Fogwing CMMS improves communication and supplier management by centralizing all supplier data, enabling seamless access and real-time updates. It automates communication workflows, ensures timely supplier interactions, tracks performance metrics, and manages compliance efficiently. It leads to better collaboration, reduced administrative efforts, and more robust supplier relationship management.
- Improved Performance Tracking: The software allows real-time supplier performance monitoring using key metrics such as delivery times, quality, and compliance. It enables you to identify issues promptly and take corrective actions to maintain high standards. Fogwing CMMS streamlines performance tracking and supplier management by automating the monitoring of supplier performance and quality standards. It centralizes supplier data, enabling real-time performance insights and compliance checks. It ensures consistent supplier evaluation, fosters accountability, and strengthens overall supplier relationship management, enhancing operational efficiency.
- Streamlined Processes: Supplier management software automates many aspects of supplier management, including order processing, invoicing, and compliance tracking. Automation reduces manual effort, speeds up processes, and minimizes the risk of errors. Fogwing CMMS streamlines process and maintenance management by enhancing routine tasks like order processing and performance tracking. It allows for easy access and efficient communication. This automation reduces manual effort, ensures consistent supplier evaluations, and enhances overall operational efficiency, leading to enhanced supplier management.
- Data-Driven Insights: The Supplier management software provides analytical tools to generate reports and insights on supplier performance, inventory levels, and procurement trends. These insights help make informed decisions, optimize supply chain strategies, and improve efficiency. Fogwing CMMS provides data-driven insights by analyzing real-time supplier performance and operational data, enabling users to make informed decisions based on accurate reports and trends. It allows organizations to identify areas for improvement. It optimizes supplier relationships and enhances operational efficiency, driving better business outcomes.
By leveraging Supplier Management Software, organizations can achieve better coordination, improve supplier relationships, and enhance operational efficiency.
Conclusion
In conclusion, effective supplier management is crucial for optimizing maintenance efficiency and ensuring smooth operational performance. By leveraging Fogwing CMMS, organizations can enhance communication, streamline processes, and gain data-driven insights that lead to informed decision-making. Fogwing CMMS centralizes supplier data, automates workflows, and provides real-time performance tracking, ensuring the timely availability of quality materials and services while reducing risks and costs.
Adopting Fogwing CMMS, for supplier relationship management as industries evolve helps organizations maintain a competitive edge and achieve long-term business objectives. This powerful platform directly impacts maintenance operations by reducing downtime and improving asset longevity. It mitigates operational risks and enhances asset performance in dynamic business environments.
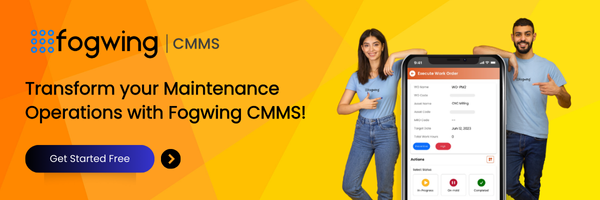