In today’s fast-paced industrial environment, effective supplier relationships ensure smooth operations and directly influence efficiency, reliability, and maintenance costs. A strong relationship with the suppliers is crucial to ensuring the timely availability of high-quality materials and reducing operational downtime. This blog explores the profound impact of supplier relationships on maintenance materials management, highlighting how communication, collaboration, and strategic alignment with suppliers can optimize inventory management, enhance supply chain resilience, and ultimately contribute to the overall success of maintenance activities.
What is Material Management?
Managing the parts for asset maintenance in an organization involves planning, procuring, and storing the required materials. These materials include spare parts, tools, lubricants, and other consumables for upkeep equipment and infrastructure. Efficient management of these materials with an efficient CMMS Platform like Fogwing CMMS ensures that asset management and maintenance tasks are performed promptly and efficiently, minimizing disruptions and maintaining operational continuity in an organization. Materials management is a multifaceted discipline that involves coordinating various activities to ensure an organization’s efficient flow of materials. It is crucial for providing production and maintenance processes to run smoothly. Here is a deeper dive into the components of maintenance materials.
Critical Components of Materials Management
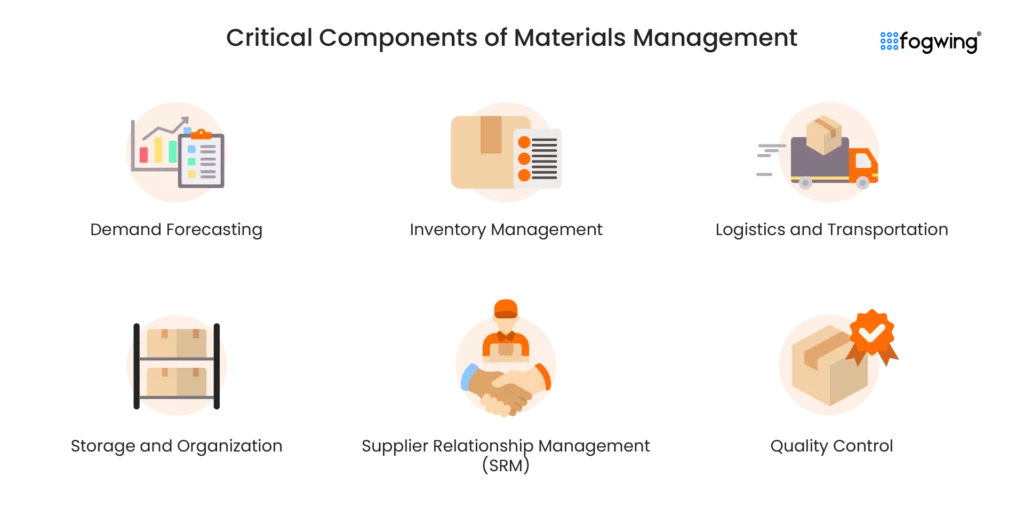
Demand Forecasting:
Demand forecasting sources and acquiring the material required for production and asset maintenance. It involves predicting needs, identifying suppliers, analyzing historical data, understanding the maintenance schedule, considering future projects or changes in operations, and purchasing the materials essential for asset maintenance activities. With Fogwing, CMMS, organizations can conduct effective demand forecasting to prevent stockouts and overstock situations, ensuring that materials are available when needed without wasting capital on inventory.
Inventory Management:
Inventory management in materials management involves overseeing the storage and handling of maintenance materials to ensure they are available when required while minimizing the holding cost. It employs the techniques like Just-In-Time (JIT) inventory, Economic Order Quantity (EOQ), and safety stock calculations. These techniques help organizations to effectively track inventory levels, forecast demand, and manage reorder points to avoid excess inventory. With maintenance management software like Fogwing CMMS, you can easily optimize inventory, reduce carrying costs, minimize waste, and improve cash flows, all while ensuring the availability of critical materials.
Logistics and Transportation:
Logistics and transportation are crucial to materials management as they guarantee timely delivery and availability, preventing production delays and reducing downtime. It focuses on moving materials from suppliers to the organization within different departments. It includes planning, supplier relationships, transportation, warehousing, and distribution to ensure timely and efficient materials delivery. By integrating these strategies, organizations can enhance supply chain agility, respond quickly to changing demands, and provide a smooth, cost-effective flow of materials, ultimately boosting overall productivity and efficiency.
Storage and Organization:
Managing inventory space in materials management requires proper storage and organization of materials. It includes implementing effective warehouse management systems, organizing materials logically, and maintaining adequate storage containers. A Smart CMMS Platform like Fogwing CMMS can help organizations manage storage effectively and reduce retrieval times and the risk of material damage. Overall, it enables the organization to improve material handling efficiency.
Supplier Relationship Management (SRM):
Maintaining strong supplier relationships is critical to maintaining a constant and reliable supply of maintenance materials. It includes regular communication, performance evaluation, and supplier collaboration to enhance material quality and reduce cost. With the SRM in materials management on board, the organization ensures a reliable supply of quality materials, fosters collaboration, and drives mutual growth. With strong partnerships, organizations can negotiate better terms, improve communication, and gain insights into supplier capabilities and market trends. The Fogwing CMMS platform’s collaboration approach enhances supply chain resilience, reduces risks, and promotes innovation. They ultimately contribute to the consistent material availability, cost efficiencies, and the overall success of the organization’s supply chain operations.
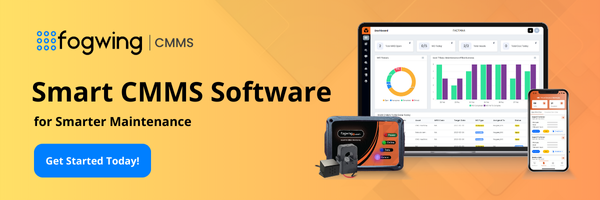
Quality Control:
Ensuring that the materials received meet the required quality standards is vital for maintaining product quality and operational efficiency. The quality control of maintenance materials involves testing and inspecting materials upon receipt and during storage. Quality control is the pivotal component of materials management, ensuring that all the materials meet the required standards and specifications before they are used in production. Effective quality control prevents the introduction of substandard materials into the production line, reducing the risk of product failures and ensuring customer satisfaction. Quality control thus plays a vital role in upholding the integrity and reliability of the entire materials management process.
The Importance of Supplier Relationships in Material Management
Supplier relationships are foundational to effective maintenance materials management. They influence various aspects of the supply chain, from procurement to the quality of materials received. It helps organizations to ensure a reliable supply chain, reducing the risk of delays and shortages. Here are a few reasons why supplier relationships in materials management are essential:
Enhancing Supply Chain Efficiency: Strong relationships with suppliers streamline the supply chain by ensuring timely and consistent delivery of maintenance materials. When suppliers understand a company’s needs and schedules, they can better anticipate and meet demands, reducing the risk of stockouts and delays. Efficient supply chains minimize downtime, enabling maintenance teams to perform tasks without interruptions.
Ensuring Quality and Reliability: In materials management, Reliable suppliers are crucial for maintaining the quality and reliability of maintenance materials. High-quality materials are essential for adequate maintenance, as subpar components can lead to equipment failure and increased maintenance costs. Suppliers with a track record of providing consistent quality help maintain operational standards and reduce the risk of equipment breakdowns.
Cost Management and Savings: Effective supplier relationships contribute to cost savings in several ways. Negotiating beneficial terms with suppliers, such as bulk-purchasing discounts or long-term contracts, can significantly reduce material costs. Additionally, reliable suppliers help avoid the hidden costs of delays and equipment failures caused by inferior materials. Strong relationships also open the door to collaborative cost-saving initiatives, such as joint materials management and process improvements.
Risk Mitigation: Supplier relationships play a crucial role in risk mitigation. By fostering strong partnerships, companies can better anticipate and manage risks associated with supply disruptions, price volatility, and quality issues. Suppliers who understand a company’s operations and requirements are more likely to provide timely support and solutions in times of crisis, ensuring continuity of maintenance activities.
Trust and mutual respect between organizations and suppliers in materials management foster long-term partnerships, enabling more beneficial terms and conditions. Additionally, strong relationships help manage risks and adapt swiftly to market changes. These relationships enhance operational efficiency, competitiveness, and customer satisfaction, making them vital to successful material management.
Building Strong Supplier Relationships in Material Management
Cultivating effective supplier relationships requires a proactive and strategic approach. Here are critical strategies for building and maintaining solid partnerships:
Communication and Collaboration
Open and transparent communication is the foundation of solid supplier relationships. Regular communication helps align expectations, address issues promptly, and foster a collaborative environment. In materials management, cooperative efforts, such as joint planning and problem-solving, enhance mutual understanding and trust. Companies and suppliers can develop innovative solutions to improve supply chain efficiency and material quality by working together.
Long-term Partnerships
Investing in long-term partnerships with suppliers yields significant benefits. Long-term relationships foster trust and loyalty, leading to more reliable and responsive service. Suppliers who view themselves as partners are more likely to prioritize a company’s maintenance materials needs and provide proactive support. Long-term partnerships also facilitate better planning and forecasting, enabling suppliers to anticipate and effectively meet future demands.
Performance Metrics and Evaluation
Monitoring performance metrics in materials management ensures that suppliers meet the necessary standards and expectations. Key performance indicators (KPIs) such as on-time delivery, quality compliance, and responsiveness provide objective supplier performance measures. Regular evaluations and feedback sessions on maintenance materials help identify areas for improvement and strengthen the supplier relationship. Companies can drive continuous improvement and maintain high standards by holding suppliers accountable and recognizing their achievements.
Technology Integration
Technology plays a pivotal role in enhancing supplier relationships. Automated ordering systems, shared databases, and collaborative platforms streamline communication and information sharing. Real-time data exchange enables better visibility into inventory levels, order status, and delivery schedules. Technology also facilitates collaborative planning and forecasting, allowing suppliers to align their production and delivery plans with a business’s maintenance needs. With materials management technologies, companies can optimize their supply chain and enhance supplier relationships by leveraging technology.
Integrating Supplier Relationships with Bill of Materials Management
A Bill of Materials is a checklist of raw materials, components, and assemblies needed to build or maintain a product in materials management. Effective bill of materials management is essential for accurate inventory planning and procurement.
1. Accurate BOMs: Working closely with suppliers ensures that BOMs are accurate and current, reflecting the latest specifications and available materials. This accuracy helps avoid discrepancies and ensures that maintenance materials are precisely needed.
2. Optimized Inventory Levels: Suppliers can provide insights into lead times and availability, aiding in optimizing inventory levels. It prevents overstocking and understocking, maintaining a balance that supports continuous operations in materials management.
3. Streamlined Procurement: Established supplier relationships simplify the procurement process. Automated ordering systems, often integrated with CMMS (Computerized Maintenance Management Systems) or SAP Materials Management systems, can streamline material requisition, reducing manual errors and saving time.
Leveraging Technology for Enhanced Supplier Management
Technology is crucial in enhancing supplier management and ensuring efficient materials management in the modern industrial landscape. By integrating advanced systems and tools, organizations can streamline their interactions with suppliers, improve procurement processes, and ensure the availability of high-quality maintenance materials. Here’s a more detailed look at how organizations can leverage technologies for enhanced supplier management:
Fogwing CMMS Integration
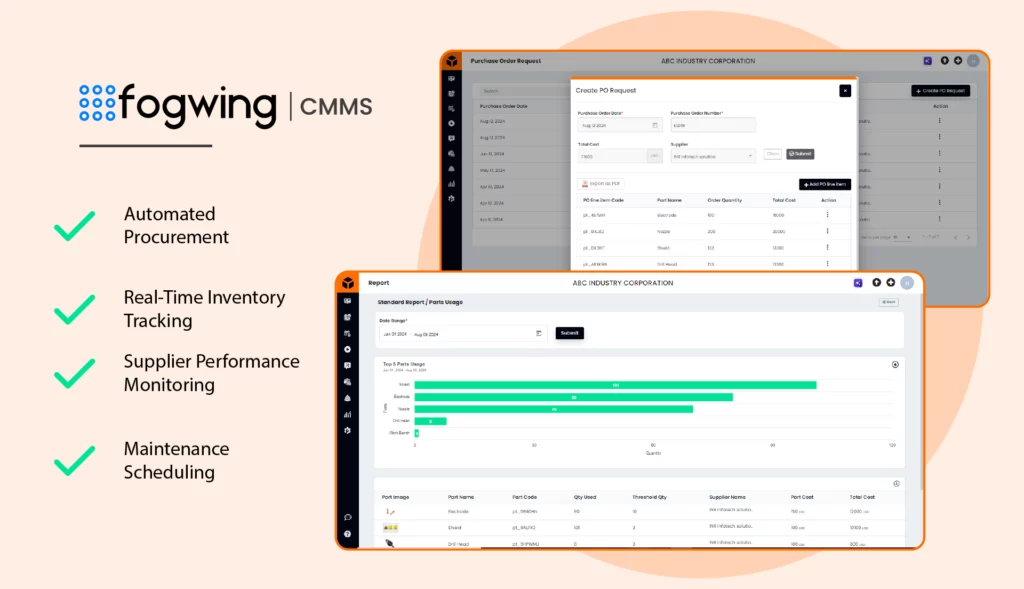
Computerized Maintenance Management Systems (CMMS) are pivotal in managing maintenance materials operations and tracking associated usage. Integrating supplier information into Fogwing CMMS can bring several advantages to the table for organizations:
- Automated Procurement
- Fogwing CMMS can automate the procurement process by generating Purchase Orders (PO) based on predefined inventory levels and maintenance schedules. It reduces the manual effort involved in ordering materials and minimizes the risk of human error.
- Real-Time Inventory Tracking
- Fogwing CMMS provides real-time visibility into inventory levels in material management. It allows maintenance teams to track material availability and plan their activities accordingly. It ensures that maintenance materials are always on hand when needed, reducing downtime.
- Supplier Performance Monitoring
- By integrating supplier data, Fogwing CMMS can track suppliers’ delivery times, quality of materials, and responsiveness. The CMMS data helps organizations evaluate and select the best suppliers, fostering stronger relationships.
- Maintenance Scheduling
- Fogwing CMMS can align maintenance schedules with material availability, ensuring all necessary components are available before maintenance work begins. This coordination helps avoid delays and ensures efficient use of resources in materials management.
By understanding how CMMS platforms such as Fogwing CMMS can help organizations enhance their maintenance processes, organizations can intensify their associations with suppliers, improve operational efficiency, make cost savings, and increase reliability.
Future Trends in Supplier Relationships for Maintenance Materials Management
The landscape of supplier relationships is evolving, driven by technological advancements and changing business dynamics. Several emerging trends are shaping the future of supplier relationships in maintenance materials management:
• Digital Transformation: Integrating digital technologies, such as artificial intelligence and blockchain, transforms supplier relationships. These technologies enhance transparency, traceability, and efficiency in the supply chain.
• Sustainable Practices: Increasing emphasis on sustainability drives companies to collaborate with suppliers on environmentally friendly practices. Sustainable sourcing and green supply chains are critical priorities in maintaining supplier relationships.
• Resilient Supply Chains: The need for resilient supply chains prompts companies to diversify their supplier base and develop robust risk management strategies. Building resilience into supplier relationships in materials management ensures continuity in disruptions.
• Supplier Innovation: Companies increasingly seek innovative solutions from suppliers to improve maintenance processes and materials. Collaborative innovation drives continuous improvement and competitive advantage.
Conclusion
Effective supplier relationships are pivotal in materials management, ensuring the timely availability of high-quality materials and reducing operational downtime. Organizations can optimize inventory management, enhance supply chain resilience, and achieve cost efficiencies by fostering strong communication, collaboration, and strategic alignment with suppliers. Leveraging technologies like Fogwing CMMS further streamlines procurement, real-time inventory tracking, and supplier performance monitoring. As the industrial landscape evolves, embracing digital transformation, sustainable practices, and resilient supply chains will be crucial. Ultimately, robust supplier relationships in materials management drive operational efficiency, competitiveness, and overall success in maintenance activities.
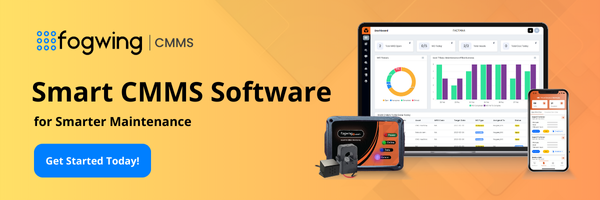
FAQs
1. What is maintenance materials management?
Maintenance materials management involves planning, procuring, storing, and controlling spare parts, tools, lubricants, and consumables essential for equipment upkeep.
2. How do supplier relationships affect maintenance materials management?
Strong supplier relationships ensure a reliable and consistent supply of maintenance materials, improve communication, enhance material quality, reduce costs, and mitigate risks associated with supply chain disruptions, directly impacting maintenance efficiency and operational continuity.
3. What are the critical components of maintenance materials management?
The main parts of maintenance materials management include forecasting the materials you’ll need, managing inventory to keep the right amount of stock, handling logistics and transportation to make sure materials arrive on time, organizing and storing materials properly, maintaining good relationships with suppliers to ensure quality and control costs, and checking the quality of materials to meet required standards.
4. Why do logistics and transportation play a vital role in materials management?
Logistics and transportation matter because they make sure maintenance materials show up right on time. When materials arrive as needed, it helps keep everything running without delays or downtime. This means planning shipments from suppliers, managing where materials are stored, and making sure everything gets to the right place without any hiccups.
5. How does technology integration improve materials management?
Technology like CMMS platforms, such as Fogwing CMMS, helps automate purchasing, track inventory in real-time, monitor supplier performance, and coordinate maintenance schedules. This makes the entire supply chain more efficient and strengthens collaboration with suppliers.