In complex business operations, effective MRO (Maintenance, Repair, and Operations) inventory management is a foundation for ensuring smooth, uninterrupted workflow. MRO inventory management encompasses the materials and supplies used in business to perform upkeep, repair, and day-to-day functioning. It includes everything from spare parts and lubricants to tools and safety equipment. MRO inventory is essential for running operations smoothly and ensuring that machinery and equipment are maintained effectively to reduce downtime, maintenance costs, and operational disturbances.
This Blog will explore what it is and its impacts on business operations, as well as effective management strategies and best practices for optimizing MRO inventory operations. Organizations can enhance operational efficiency by understanding and implementing these insights. It reduces costs and ensures uninterrupted production.
What does MRO stand for?
MRO, also called Maintenance, Repair, and Operations, is a critical aspect of business management that safeguards the smooth functioning of production processes and operational efficiency.
Maintenance: Maintenance in the MRO inventory management involves regular asset maintenance activities to preserve equipment and systems in ideal working conditions. It includes routine inspections, lubrication, cleaning, and part replacements. Effective maintenance reduces unexpected breakdowns, prolongs the asset lifespan, and maintains consistent production quality.
Repair: Repair in the industrial MRO stands for fixing assets and systems when they malfunction. It includes replacing faulty parts, diagnosing issues, and restoring asset functionality. The repair activities are required to minimize asset downtime, enabling organizations to prevent extended disruptions in production processes.
Operation: Operation in the MRO inventory management refers to the daily activities essential to running a business. It includes production-related tasks and administrative, logistical, and facility management functions. Operations in Industrial MRO ensure the necessary tools, supplies, and resources are available to support maintenance and repair activities.
Understanding and effectively managing Maintenance, Repair, and Operations ensures operational continuity. Overlooking any element of MRO might lead to increased operational costs, minimized equipment lifespan, and potential safety hazards. Henceforth, organizations must prioritize managing MRO inventory to achieve operational excellence, enhance productivity, and ensure long-term sustainability. This Blog will further explore various types, impacts, and best practices of MRO inventory Management, providing insights that enable industries to optimize their operations.
Types of MRO Inventory
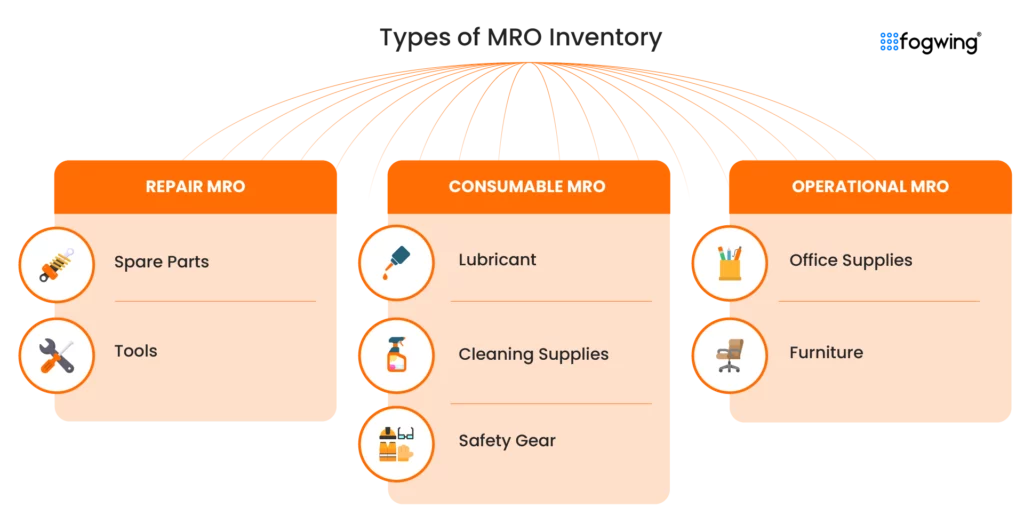
MRO inventory encompasses many parts or items essential for maintaining efficient business operations. These items are categorized into three main types: consumable MRO, Repair MRO, and Operational MRO. Understanding these types and their examples can help organizations manage MRO inventory Effectively, ensuring smooth operations and minimizing downtime.
Consumable MRO
The Consumable MRO Items are the suppliers and materials utilized for asset maintenance, repair, and operation. The consumable MRO items need to be refilled or restocked regularly as they are consumed. Here are a few examples of consumable MRO utilized in the MRO Inventory Management
- Lubricant: Lubricants are utilized by MROs supplying machinery and equipment to reduce friction, wear, and tear. They ensure smooth and effective asset operation in organizations. Examples include grease, hydraulic fluids, and oil.
- Cleaning Supplies: Industrial MROs use cleaning supplies to maintain cleanliness and workplace hygiene. These supplies prevent contamination and promote a safe working environment for maintenance employees. Examples include disinfectants, detergents, brushes, and cleaning cloths.
- Safety Gear: The safety gear in the MRO supply protects employees from hazards, ensuring their safety during asset maintenance and repair operations. Examples include helmets, gloves, safety glasses, respirators, and ear protection.
Consumable MRO items in MRO Inventory Management are crucial for day-to-day operations, ensuring that asset maintenance tasks are carried out efficiently and safely. Proper inventory management of these items is essential to avoid interruptions in maintenance activities due to stockouts.
Repair MRO
Repair MRO items include spare parts and tools for repairing and maintaining assets and machinery. These items in MRO supply replace worn-out or damaged parts, ensuring asset longevity and optimal performance. Here are a few examples of repair MRO utilized in the industrial MRO.
- Spare Parts: Spare parts are crucial components that replace faulty or worn-out machinery and equipment. Examples include belts, bearing filters, valves, and gears.
- Tools: Tools in MRO inventory management are the instruments and equipment used to perform maintenance and repair tasks efficiently. Examples include screwdrivers, wrenches, Spare Parts, pliers, diagnostic tools, and hammers.
Repair MRO Items are crucial in reducing asset downtime. It ensures that equipment and machinery are kept in optimal working condition. An adequate supply of spare parts and tools is vital for quick and effective repairs, preventing operational disruptions.
Operational MRO
Operational MRO items are materials and MRO supplies used in daily business operations. They are not directly involved in the production process but must maintain an efficient organizational workflow. Here are a few examples of Operational MRO utilized as an organization’s MRO supply.
- Office Supplies: The office supplies in the MRO inventory management are crucial for administrative tasks and daily business operations. Examples include pens, papers, toner cartridges, envelopes, and binders.
- Furniture: Furniture in MRO inventory provides a functional and comfortable working environment for an organization’s employees. Examples include chairs, desks, shelving units, and filing cabinets.
Operational MRO items support the workplace’s overall functionality and efficiency. Proper management of these parts or supplies ensures that administrative and operational tasks can be carried out smoothly, contributing to the business’s overall productivity.
What is MRO inventory Management?
As defined earlier, MRO refers to overseeing and controlling the supplies, spare parts, and tools essential for maintaining, repairing, and operating equipment facilities. The primary purpose of MRO inventory management is to ensure that all the critical items or parts are available when required, reducing asset downtime and maintaining operational efficiency.
Unlike regular inventory management, which focuses mainly on raw materials and finished goods used in sales and production, MRO inventory deals with items essential for the business’s maintenance and operation. Regular inventory management focuses on turnover rates and stock levels to meet customer demand. On the other hand, Industrial MRO prioritizes availability and readiness to prevent operational disruptions and extend asset life.
Regular inventory management is typically concerned with turnover rates and stock levels to meet customer demand. In contrast, MRO inventory management prioritizes availability and readiness to prevent operational disruptions and extend the life of assets. By understanding the importance of MRO meaning and its unique requirements, businesses can ensure smoother operations and prolonged asset lifespans. Effective MRO inventory management involves forecasting demand, optimizing stock levels, and implementing strategies to reduce costs and improve efficiency in maintenance and repair activities.
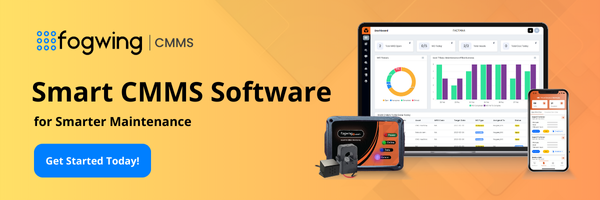
How to Manage MRO Inventory with Fogwing CMMS: A Step-by-Step Guide
Managing MRO inventory effectively is vital for maintaining the productivity and longevity of equipment in any organization. Fogwing CMMS, an innovative Computerized Maintenance Management platform, offers a streamlined approach to MRO inventory management, ensuring that all necessary parts and supplies are always available when needed. Here’s a step-by-step guide to help you manage your MRO inventory effectively using Fogwing CMMS:
1. Conduct a Thorough Audit of the Current MRO Stock
Before effectively managing your MRO inventory, it’s crucial to understand your current inventory status. Conduct a comprehensive audit of your existing MRO stock. It involves:
Physical Inventory Check: Perform a physical count of all MRO items and compare it with existing records.
Condition Assessment: Check the condition of each item to ensure it is fit to use.
Documentation: Document any discrepancies during the audit and update your CMMS inventory database accordingly. It will provide a clear picture of your supply MRO and help you identify gaps or excesses.
Minimum Threshold: Determine a maintenance team’s minimum inventory level to reorder parts or items. Fogwing CMMS offers a feature that sends an email alert notification if the stock is below the specified minimum threshold.
Experience the user-friendly Fogwing CMMS interface to effortlessly input audited data into the database, ensuring precise and thorough record-keeping for your MRO inventory management and asset maintenance activities.
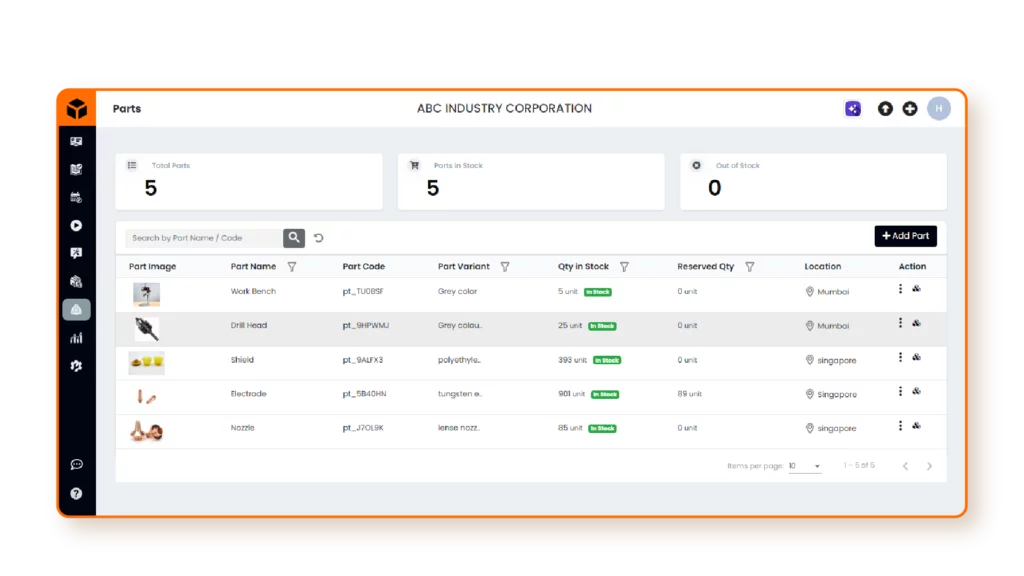
2. Categorize and Classify MRO Items
Once you understand the status of your MRO supply, the next step is categorizing and classifying your MRO Items. Fogwing CMMS helps you organize your inventory for better management and tracking. It involves:
Part Variant: Fogwing CMMS allows users to mention the parts based on their variant type, for example, electrical, mechanical, material type, size, etc.
Part Image: With Fogwing CMMS, you can now upload images of the parts on the platform, making it easier to identify the parts.
Part Code: The Fogwing CMMS provides its users with a unique ID to identify critical items essential for operations and MRO inventory management.
Categorizing and classifying your MRO supply enables the Fogwing CMMS users to Prioritize inventory management efforts and streamline the tracking and reordering process.
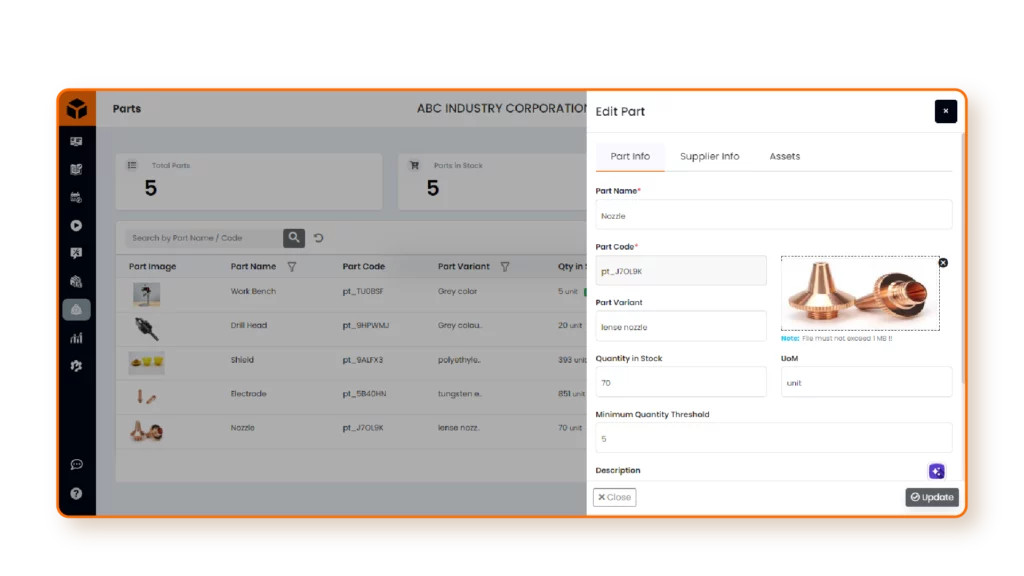
3. Set Up the complete Supplier Info
Provide complete MRO inventory parts supplier information to manage and track inventory using Fogwing CMMS effectively. The software allows users to input and attach parts to their respective suppliers. It involves:
Supplier Name: Specify the supplier’s name to ensure that the specific suppliers provide the items or parts. The Fogwing CMMS platform enables you to tag the supplier when creating parts in their inventory database.
Supplier Type: Specify the type of supplier from whom you purchase the necessary items or parts to maintain assets. Fogwing CMMS primarily supports the following supplier types: Reseller, Wholesaler, and Manufacturer. If your supplier type does not fall into these three categories, you can select ‘Other.’
Real-Time Monitoring: Remember to mention and monitor the inventory levels in real-time to prevent overstocks and Stockouts. Fogwing CMMS allows you to input details such as parts delivery time (in days), the minimum order needed, and purchase cost to conduct MRO inventory management effectively.
Implementing these details in your CMMS systems allows you to maintain an up-to-date MRO inventory and reduces manual errors when placing purchase orders.
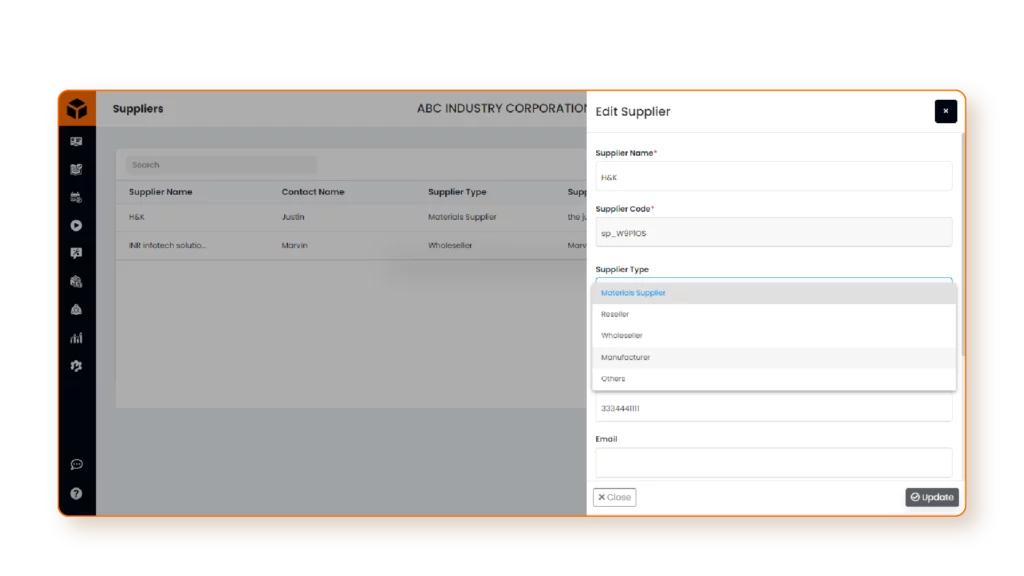
How Does MRO Inventory Impact Your Supply Chain Management?
Effective management of MRO inventory is essential for the seamless functioning of supply chain management. Adequate MRO supply encompasses Maintenance, Repair, and Operations supplies, which are vital to ensuring continuous production uptime. It gives organizations all the necessary tools, consumables, and spare parts for maintenance. It eases the issue of production halts due to asset failure or maintenance needs. Production lines can continue to operate smoothly without the risk of unexpected breakdowns when there is efficient MRO inventory management.
How does the MRO inventory level affect the maintenance schedule and cost?
The supply directly influences maintenance schedules and costs associated with asset maintenance. Properly stocked maintenance, repair, and operations (MRO) supplies enable scheduled preventive maintenance, reducing the need for expensive emergency repairs. The availability of the right parts and tools helps organizations perform scheduled maintenance effectively. It significantly lowers workforce costs and asset downtime. On the contrary, insufficient MRO inventory can delay maintenance activities, increasing wear and tear on assets, repair costs, and potential production losses.
The role of MRO in minimizing downtime and unplanned disruptions
MRO inventory management is crucial in reducing downtime and unplanned breakdowns within the supply chain. Maintaining an optimal MRO stock enables the companies to address maintenance needs swiftly, avoiding lengthy production interruptions. Effective management of MRO supply ensures that unexpected asset failures are resolved quickly, reducing significant operational disruptions. This reliability fosters a stable production environment, enhancing overall supply chain efficiency.
Critical Components of MRO Inventory Management
Efficient MRO supply management is crucial for ensuring that maintenance activities run smoothly. It minimizes operational downtime and enhances the overall productivity of assets in an organization. Here are the critical components of MRO inventory management that help achieve these goals:
Demand Forecasting: Predicting MRO Needs
Accurately predicting the MRO supply requirements for asset maintenance is the foundation of effective MRO management. Demand forecasting requires analyzing historical usage data, considering the forthcoming maintenance schedule, and factoring in variables such as seasonality and equipment lifecycle stages.
Organizations can more precisely anticipate their industrial MRO needs by implementing robust demand forecasting techniques. This proactive approach helps prevent stockouts, reduce excess inventory, and ensure that essential items are available when needed. Advanced tools such as predictive analytics and ML (Machine learning) can enhance demand forecasting accuracy, allowing for better planning and resource allocation.
Inventory Optimization: Balancing Stock Levels
Inventory optimization involves finding the balance between maintaining adequate MRO stock to meet demand and avoiding excess inventory that ties up capital and storage space. This process in MRO inventory management focuses on sustaining optimal stock levels to support efficient maintenance operations.
Techniques such as ABC analysis, which categorizes inventory items based on usage and value, help prioritize high-impact items. The maintenance team can also retain Just-in-time (JIT) inventory practices to minimize holding costs while ensuring timely availability of maintenance inventory stock. Regularly reviewing and modifying reorder points and safety stock levels based on demand fluctuations and lead times further contributes to inventory optimization.
Procurement: Sourcing MRO Items Efficiently
Efficient procurement processes are essential for ensuring the timely and cost-effective acquisition of MRO items. This component involves selecting reliable suppliers, negotiating favorable terms, and establishing long-term partnerships to secure a steady supply of critical materials.
Implementing e-procurement systems can streamline the procurement process by automating requisition, approval, and purchase order generation. Teaming up with suppliers can lead to better pricing, improved delivery times, and enhanced service levels. Strategic sourcing strategies, such as consolidating purchases and leveraging volume discounts, also contribute to more efficient procurement.
Storage and Organization: Managing MRO Inventory Space
Proper storage and organization of MRO inventory are vital for maximizing space utilization, ensuring easy access to items, and minimizing the risk of stock damage or loss. Practical storage solutions include implementing systematic shelving, binning, and classification practices to create an organized and efficient storage environment.
Using barcode or RFID technology can enhance inventory organization by enabling quick and accurate item identification and retrieval. Regularly reviewing and optimizing storage layouts, conducting periodic audits, and maintaining a clean and orderly storage area contribute to efficient MRO inventory management.
Tracking and Reporting: Monitoring MRO Usage and Trends
Tracking and reporting are critical components of MRO inventory management. They provide insights into usage patterns, trends, and areas for improvement. By monitoring MRO inventory usage, organizations can identify consumption trends, assess inventory turnover rates, and detect anomalies or inefficiencies.
Implementing inventory management software with robust tracking and reporting capabilities allows for real-time visibility into inventory levels, movements, and usage. Detailed reports on key metrics, such as stock levels, order history, and supplier performance, enable data-driven decision-making and continuous improvement of inventory management practices.
Best Practices for MRO Inventory Management
Effective MRO inventory management is vital for maintaining operational efficiency and minimizing downtime. Here are some best practices to ensure your optical MRO Inventory Management:
1. Centralize MRO Storage:
Consolidating all MRO items in a single, central location can significantly streamline inventory management. Fogwing CMMS platform’s centralized storage reduces the time spent searching for parts, minimizes duplication, and enhances the accuracy of inventory tracking. It also allows for better oversight and control over stock levels, ensuring that critical items are always available when needed.
2. Use Inventory Management Software:
Leveraging advanced inventory management software like Fogwing CMMS can transform your MRO operations. These systems provide real-time visibility into MRO stock levels, automate reordering processes, and offer detailed analytics on usage patterns. They help prevent stockouts and overstock situations, ensuring your inventory is maintained optimally.
3. Track Key Performance Indicators (KPIs) for MRO:
Monitoring KPIs such as inventory turnover rate, stockout incidents, and carrying costs is essential for understanding the efficiency of your MRO inventory management. Fogwing CMMS provides regular metrics tracking to help identify trends, uncover inefficiencies, and make data-driven decisions to improve inventory performance.
4. Regularly Review and Adjust Your MRO Strategy:
Your operations’ needs can change over time, making it crucial to periodically review and adjust your MRO strategy. Fogwing CMMS helps you conduct regular audits and assessments to identify obsolete or excess items, optimize reorder points, and adjust inventory based on current demand. This proactive approach ensures that your MRO inventory aligns with your operational needs and goals.
Implementing these best practices improves the management of Industrial MRO, resulting in reduced costs, enhanced efficiency, and increased reliability of your operations.
Conclusion:
Effective MRO inventory management is vital for the seamless operation of any business. It ensures that essential maintenance, repair, and operational supplies are always available, reducing downtime and operational disruptions. By understanding MRO inventory components and implementing best practices like centralizing storage, using Computerized maintenance management system software such as Fogwing CMMS, tracking KPIs, and regularly adjusting strategies, businesses can enhance efficiency, reduce costs, and ensure continuous production. Investing in robust Industrial MRO with the support of tools like Fogwing CMMS supports operational excellence and contributes to an organization’s long-term sustainability and success.
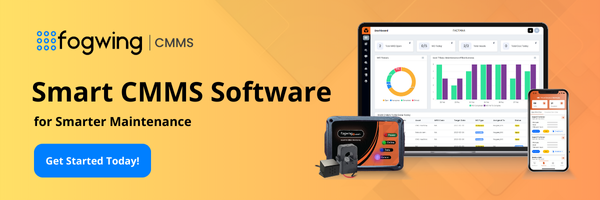
FAQs
1. What is MRO inventory management, and why is it important for industrial operations?
MRO inventory management refers to overseeing the maintenance, repair, and operations supplies required to keep machinery and business processes running efficiently. It includes items like spare parts, lubricants, safety gear, and tools. Effective MRO inventory management is essential because it reduces equipment downtime, lowers maintenance costs, and ensures uninterrupted production, all of which contribute to operational excellence.
2. What are the main types of MRO inventory in manufacturing and plant maintenance?
The three main types of MRO inventory include:
- Consumable MRO: Items like lubricants, cleaning supplies, and safety gear that are used regularly and need to be replenished.
- Repair MRO: Spare parts and tools used to fix or replace worn-out components.
- Operational MRO: Items that support business operations, such as office supplies and furniture.
- Managing each type efficiently helps avoid disruptions in maintenance and day-to-day activities.
3. How does poor MRO inventory management affect maintenance and costs?
Poor MRO inventory management can cause delays in maintenance when parts aren’t available, leading to unexpected breakdowns, emergency fixes, and higher repair costs. Keeping MRO stock organized helps avoid these issues and keeps maintenance on track and affordable.
4. Why should manufacturers use CMMS software for managing MRO inventory?
CMMS (Computerized Maintenance Management System) software like Fogwing CMMS automates and simplifies MRO inventory tracking, supplier management, and stock level monitoring. It helps set minimum stock thresholds, categorize parts, track usage trends, and generate alerts for reordering. This reduces manual errors and stockouts and improves overall asset maintenance efficiency.
5. What are the key parts of good MRO inventory management?
Effective MRO inventory management includes a few key steps:
- Forecasting demand so you know what parts will be needed ahead of time.
- Keeping stock levels balanced to avoid running out or overstocking.
- Buying from reliable suppliers to ensure quality and timely delivery.
- Organizing storage smartly using labels or barcodes for easy tracking.
- Tracking usage and trends to make better decisions and improve over time.