In any industry, equipment is the backbone of day-to-day operations. Whether using heavy machinery on a construction site or CNC in a manufacturing plant, properly maintain equipment for efficiency, safety, and longevity. Manual maintenance operations can lead to costly repairs, downtime, and even safety hazards in the reliable equipment industry.
This comprehensive guide aims to provide insight into the importance of equipment maintenance and offer practical tips to ensure your machinery and tools remain in optimal condition.
What is Equipment Maintenance?
Equipment maintenance is the systematic process of inspecting, servicing, repairing, and preserving machinery, tools, instruments, or other assets to ensure they remain in optimal working condition. It involves a series of proactive measures to prevent equipment failure, minimize downtime, and extend the lifespan of assets.
Equipment maintenance typically includes routine inspections, cleaning, lubrication, calibration, and replacement of worn-out components. Proper equipment maintenance is essential for maximizing efficiency, safety, and reliability in various industries, from manufacturing and construction to healthcare and IT.
Maintenance is not just about fixing things when they break; it’s about preventing breakdowns in the first place. Regular preventive maintenance routines help identify potential issues early on, allowing for timely repairs and minimizing downtime. Additionally, well-maintained equipment operates more efficiently, reducing energy consumption and saving costs in the long run. Moreover, proper maintenance ensures compliance with safety regulations, protecting employees and the equipment from accidents and damage.
Types of Equipment Maintenance
For manufacturers, equipment maintenance is a critical aspect of operations that ensures the continuous functioning of machinery, tools, and production systems. Here’s what equipment maintenance entails for manufacturers:
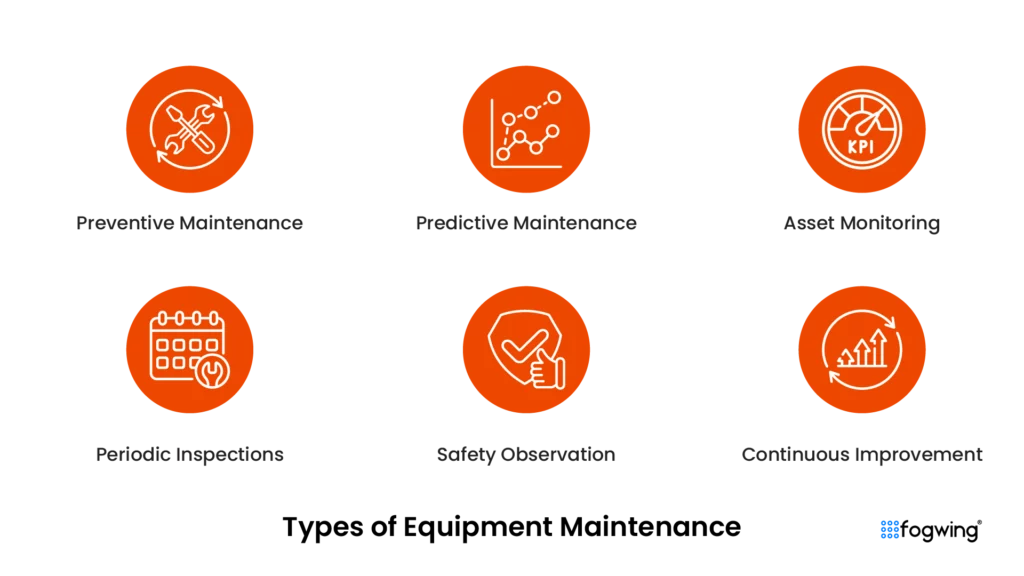
Preventive Maintenance:
Manufacturers rely on preventive maintenance strategies to minimize the risk of unexpected breakdowns and downtime. Scheduled inspections, routine cleaning, lubrication, and calibration are carried out to identify and address potential issues before they escalate.
Predictive Maintenance:
Many manufacturers have started implementing predictive maintenance techniques using IoT that utilize machine data reading through sensors, data analytics, and monitoring systems to anticipate equipment failures. By analyzing trends and patterns in equipment performance, predictive maintenance helps schedule maintenance activities at optimal times, reducing unplanned downtime and improving overall efficiency.
Asset Monitoring:
Equipment maintenance for manufacturers involves comprehensive asset management practices. These include keeping detailed records of equipment maintenance history, tracking component lifespans, and optimizing maintenance schedules to maximize each asset’s return on investment.
Periodic Inspections:
Equipment inspection for maintenance involves regular assessments to identify issues such as wear, damage, or malfunction. It ensures optimal equipment performance, safety, and longevity by detecting problems early, enabling timely repairs or replacements, and minimizing downtime. Inspection schedules are based on manufacturer guidelines, usage patterns, and industry standards.
Safety Observation:
Manufacturers must adhere to strict asset safety monitoring and standards to ensure the well-being of their workforce and compliance with industry requirements. Equipment maintenance is crucial in maintaining safe working conditions by promptly identifying and rectifying potential safety hazards.
Continuous Improvement:
Manufacturers often strive for continuous improvement in their operations, and equipment maintenance is no exception. By analyzing maintenance data, identifying areas for improvement, and implementing best practices, manufacturers can enhance their maintenance processes over time, leading to better equipment performance and reliability.
Equipment maintenance for manufacturers is a multifaceted process encompassing preventive and predictive strategies, asset management, safety compliance, efficiency optimization, quality assurance, and continuous improvement efforts. By prioritizing maintenance activities and investing in robust maintenance programs, manufacturers can achieve smooth operations, minimize downtime, and drive sustainable growth in their industry.
Key Activities of Equipment Maintenance
Equipment maintenance involves multiple activities and tasks that should be executed according to equipment types, makes, and models. The following are general activities that may or may not apply to all equipment.
Scheduled Inspections:
Establish a regular inspection schedule for all equipment, including visual checks for signs of wear and tear, leaks, or unusual noises. This can help catch minor issues before they escalate into major problems.
Routine Cleaning:
Keep equipment clean and free of debris, dirt, and dust. Buildup can hinder performance and lead to overheating or corrosion.
Lubrication:
Proper lubrication of moving parts reduces friction and prevents premature wear. Refer to manufacturer guidelines for recommended lubricants and schedules.
Replacement of Wear Parts:
Certain equipment parts will wear out over time and need replacement. Track these components and replace them according to the manufacturer’s recommendations.
Calibration:
Ensure equipment is calibrated correctly to maintain accuracy and precision. Regular calibration checks are necessary, especially for instruments and measurement devices.
Training and Education:
Equip your staff with the knowledge and skills required for proper equipment operation and maintenance. This includes recognizing warning signs, troubleshooting common issues, and following safety protocols.
How to Implement Equipment Maintenance Process?
Implementing an effective equipment maintenance process requires careful planning, clear communication, and a commitment to continuous improvement. Here’s a step-by-step guide to help you implement an equipment maintenance process:
Assess Current Equipment Status:
Begin by assessing the current condition of your equipment. Identify critical assets, prioritize maintenance needs, and document any existing issues or recurring problems.
Establish Maintenance Goals:
Define clear goals for your maintenance process, such as reducing downtime, improving equipment reliability, enhancing safety, or extending asset lifespan. These goals will guide your maintenance strategy and help measure success.
Create a Maintenance Schedule:
Develop a schedule based on manufacturer recommendations, industry best practices, and equipment usage patterns. Determine the frequency of inspections, cleaning, lubrication, calibration, and other maintenance tasks for each piece of equipment.
Allocate Resources:
Allocate the necessary resources, including personnel, tools, equipment, and budget, to support your maintenance activities. Ensure that staff members receive proper training and have access to the tools and materials needed to perform maintenance tasks effectively.
Implement Preventive Maintenance:
Implement preventive maintenance procedures to identify and address potential issues before they escalate proactively. Schedule regular inspections, cleaning, lubrication, and calibration per your maintenance schedule.
Utilize Technology:
Explore maintenance management software, asset tracking systems, and predictive maintenance tools to streamline your maintenance process. These technologies can help automate tasks, track maintenance history, monitor equipment performance, and predict potential failures.
Establish Documentation and Reporting Procedures:
Develop standardized documentation and reporting procedures to track maintenance activities, record observations, document repairs, and analyze maintenance data. This documentation will provide valuable insights into equipment performance and help identify areas for improvement.
Promote Communication and Collaboration:
Foster open communication and collaboration among maintenance personnel, equipment operators, and other relevant stakeholders. Encourage feedback, share best practices, and involve team members in decision-making to ensure alignment and buy-in.
Monitor and Evaluate Performance:
Continuously monitor the performance of your equipment maintenance process by tracking key performance indicators (KPIs) such as equipment uptime, maintenance costs, mean time between failures (MTBF), and mean time to repair (MTTR). Use this data to evaluate the effectiveness of your maintenance efforts and identify areas for optimization.
Implement Continuous Improvement:
Embrace a culture of continuous improvement by regularly reviewing your maintenance process, identifying opportunities for optimization, and implementing corrective actions. Solicit stakeholder feedback, benchmark against industry standards, and stay informed about emerging technologies and best practices in equipment maintenance.
By following these steps and committing to a systematic approach, you can implement an equipment maintenance process that maximizes equipment reliability, minimizes downtime, and contributes to your organization’s overall success.
Common Challenges in Equipment Maintenance and Solutions
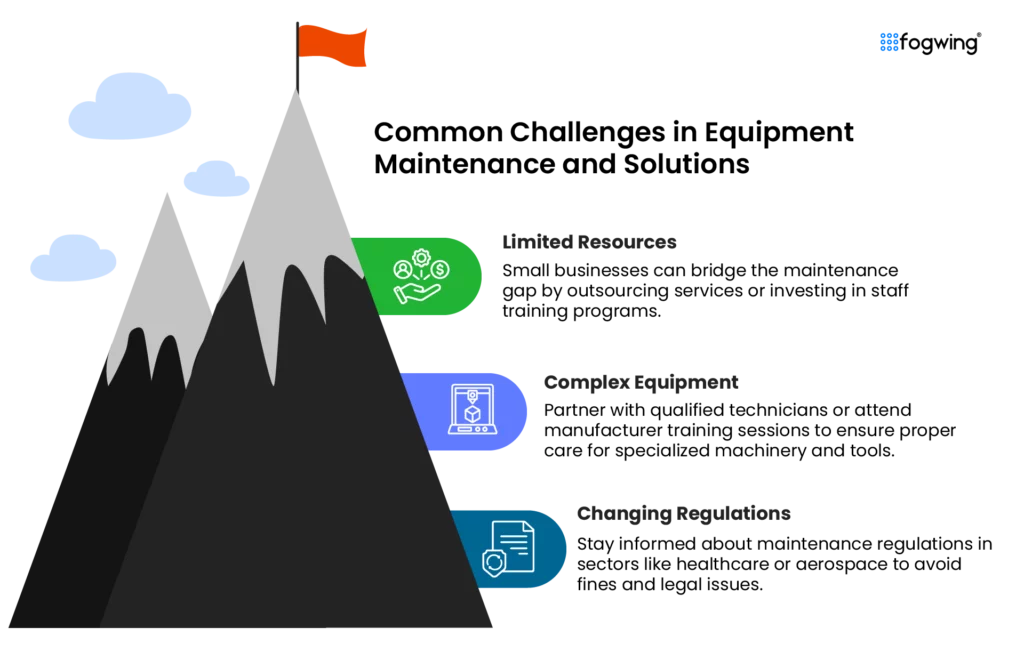
Limited Resources:
Small businesses or organizations with limited budgets and personnel may need help prioritizing maintenance. Outsourcing maintenance services or investing in training programs for existing staff can help bridge the gap.
Complex Equipment:
Some machinery and tools require specialized knowledge for maintenance and repair. Partnering with qualified technicians or attending manufacturer training sessions can ensure proper care for these assets.
Changing Regulations:
Stay informed about industry regulations and standards regarding equipment maintenance, especially in highly regulated sectors such as healthcare or aerospace. Failure to comply with these requirements can result in fines or legal consequences.
How do you use CMMS Software for Equipment Maintenance?
Fogwing CMMS (Computerized Maintenance Management System) software plays a crucial role in streamlining equipment maintenance processes, enhancing efficiency, and maximizing the lifespan of assets in various industries. Here are some key roles that Fogwing CMMS software fulfills for equipment maintenance:
Asset Management:
Fogwing CMMS software allows organizations to efficiently manage their assets by providing a centralized platform for storing and organizing asset information. Users can easily track equipment details such as make, model, serial number, location, maintenance history, and warranty information.
Preventive Maintenance Scheduling:
One of the primary roles of Fogwing CMMS software is to facilitate preventive maintenance scheduling. It enables users to create maintenance schedules based on manufacturer recommendations, industry best practices, and equipment usage patterns. Organizations can proactively identify and address potential issues before they escalate by scheduling regular inspections, cleaning, lubrication, and calibration tasks.
Work Order Management:
Fogwing CMMS software streamlines work order management processes by allowing users to create, assign, prioritize, and track maintenance tasks efficiently. Maintenance personnel can access work orders from any location, view task details, update status, and record observations in real-time, ensuring timely completion of maintenance activities.
Inventory Management:
Fogwing CMMS software includes inventory management features that help organizations track spare parts, tools, and consumables needed for equipment maintenance. Users can maintain accurate inventory records, set reorder points, track stock levels, and generate purchase orders for replenishment, ensuring that maintenance operations are not hindered due to insufficient supplies.
Mobile Accessibility:
Fogwing CMMS software offers mobile accessibility, allowing maintenance personnel to access critical information and perform maintenance tasks from anywhere using mobile devices. This enables field technicians to receive work orders, update task status, access equipment manuals, and capture maintenance data on the go, improving productivity and responsiveness.
Data Analytics and Reporting:
Fogwing CMMS software provides robust data analytics and reporting capabilities, allowing organizations to analyze maintenance data, identify trends, and make data-driven decisions. Users can generate customizable reports on key performance indicators (KPIs) such as equipment uptime, maintenance costs, mean time between failures (MTBF), and mean time to repair (MTTR), enabling continuous improvement of maintenance processes.
Integration with IoT and Sensors:
Fogwing CMMS software can integrate with IoT (Internet of Things) devices and sensors deployed to gather real-time data on equipment performance and health. This enables predictive maintenance capabilities, allowing organizations to anticipate equipment failures, optimize maintenance schedules, and minimize downtime.
Compliance and Audit Trail:
Fogwing CMMS software helps organizations maintain compliance with regulatory requirements and industry standards by providing an audit trail of maintenance activities. Users can track maintenance history, document repairs, and demonstrate adherence to maintenance protocols during audits or inspections, ensuring accountability and transparency.
Conclusion:
In summary, Fogwing CMMS software is critical in optimizing equipment maintenance processes by providing asset management, preventive maintenance scheduling, work order management, inventory management, mobile accessibility, data analytics, reporting, IoT integration, and compliance capabilities. Organizations can improve equipment reliability, reduce downtime, and achieve operational excellence by leveraging these features.
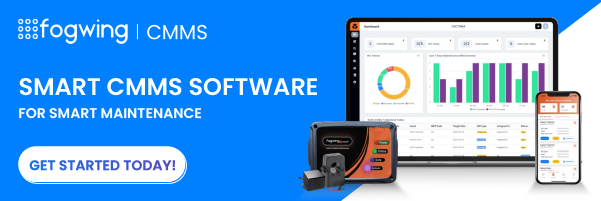