In today’s manufacturing landscape, streamlining processes, maximizing efficiency, and minimizing waste are paramount to operating profitably. Lean manufacturing system is a proven strategy for implementing best practices for better yield.
This blog delves deep into lean manufacturing system, exploring its core principles, components, advantages, and potential drawbacks. Whether you’re a seasoned manufacturer seeking to refine your operations or a newcomer eager to understand this powerful methodology, this guide has you covered.
What is a Lean Manufacturing System?
A lean manufacturing system is a continuous improvement strategy focused on eliminating effort waste and maximizing value in the production process.
It prioritizes customer requirements to deliver the right product at the right time and with the right quality. Developed by Toyota and refined over decades, lean manufacturing system has revolutionized production and impacted industries worldwide.
Core Principles of Lean Manufacturing System:
The lean manufacturing system approach is based on five key principles that are highly effective:
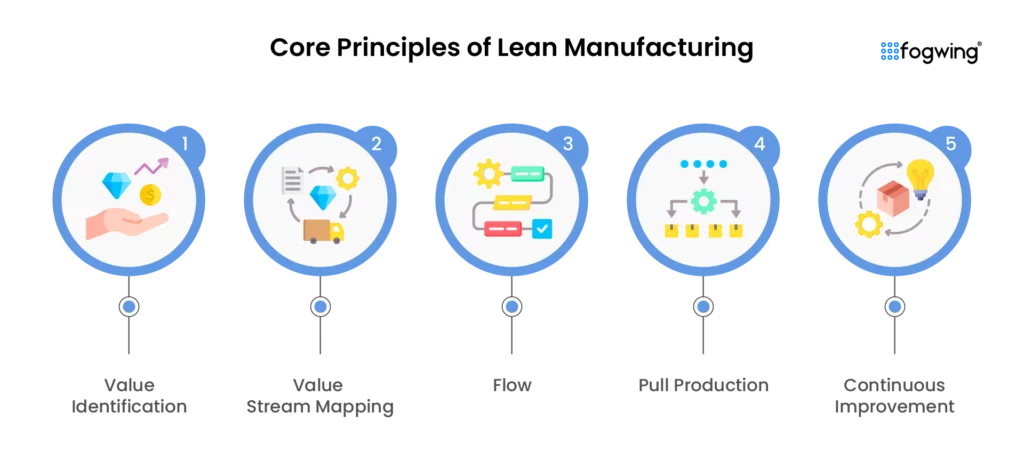
- Value Identification:
This goes beyond simply offering a product or service. The fundamental value identification principle is understanding your customers’ specific needs and expectations. What features or functionalities are most important to them? How can you deliver the product or service to maximize their satisfaction? This principle encourages manufacturers to focus on activities that directly contribute to customer value and eliminate anything that doesn’t.
- Value Stream Mapping:
Imagine a flowchart on steroids. Value Stream Mapping involves visualizing your entire manufacturing process, encompassing every step – from receiving raw materials to delivering the finished product to the customer. This map often includes processing times, inventory levels, and transportation requirements. By visualizing the entire flow, you can identify areas with bottlenecks, delays, or unnecessary activities that add no value for the customer. These areas become prime targets for improvement initiatives.
- Flow:
Think of a smoothly flowing river. In lean manufacturing system, “flow” refers to the uninterrupted movement of materials and information throughout production. Bottlenecks, delays, and waiting times disrupt this flow, leading to inefficiencies and increased lead times. Lean principles aim to eliminate these disruptions by optimizing layouts, balancing workloads, and minimizing non-value-added activities.
- Pull Production:
This principle challenges the traditional “push” production model, where production decisions are based on forecasts. Instead, JIT production focuses on making what is needed when it’s needed. This reduces the amount of inventory held, freeing up capital and minimizing the risk of obsolescence. Imagine a supermarket ordering only the milk they expect to sell each day rather than stocking a massive warehouse with unpredictable demand.
- Continuous Improvement:
Lean manufacturing is not a one-time fix; it’s a philosophy of continuous improvement. Kaizen, a Japanese term meaning “change for the better,” embodies this continuous pursuit of excellence. It encourages a culture of learning, experimentation, and problem-solving, where every employee is empowered to identify areas for improvement and suggest solutions.
Characteristics of Lean Manufacturing System:
- Customer Focus: The customer is king – or queen – in lean manufacturing. Every decision, from product design to production processes, revolves around meeting customer needs and expectations. This ensures that the company delivers value and stays competitive in the market.
- Waste Elimination: Waste comes in many forms in manufacturing – excess inventory, unnecessary transportation, waiting times, defects, and overproduction. Lean principles identify and eliminate all forms of waste, leading to efficient and cost-effective production.
- Standardized Work: Imagine every car assembled on a production line being built similarly and consistently. Standardized work involves creating well-defined and documented procedures for each step in the manufacturing process. This ensures consistency, minimizes errors, and improves overall efficiency.
- Empowered Employees: Lean manufacturing system thrives on the active participation of its workforce. Employees are not just cogs in the machine but valuable contributors who can identify problems and suggest improvements. Empowering employees with the right training and tools fosters a sense of ownership and engagement, leading to a more productive and innovative work environment.
- Pull Systems: Just like supermarkets replenish inventory based on customer demand, pull systems in lean manufacturing ensure production occurs only when there’s actual demand. This avoids overproduction and minimizes unnecessary inventory holding.
- Continuous Improvement: As mentioned earlier, continuous improvement is the cornerstone of lean manufacturing. This involves constantly seeking ways to optimize processes, eliminate waste, and improve quality. It’s a never-ending cycle of learning, adapting, and evolving to stay ahead of the curve.
Components of a Lean Manufacturing System:
- Kanban System:
Imagine a visual cue card system for production. Kanban is a visual inventory control system that uses cards to signal material replenishment needs. These cards typically specify the type, quantity, and location of materials needed at each production stage. This ensures a smooth flow of materials without overstocking or creating shortages.
- 5S System:
This seemingly simple system—Sort, Straighten, Shine, Standardize, and Sustain—has a profound impact on a workplace’s overall efficiency. The 5S system creates a clean, organized, and safe work environment, minimizing waste and maximizing productivity.
Imagine a cluttered workspace with misplaced tools and unclear procedures. Now compare that to a clean and organized environment where everything has its designated place. The 5S system fosters the latter, creating a more efficient and enjoyable work experience.
- Total Productive Maintenance (TPM):
Unlike the traditional “fix-it-when-it-breaks” mentality, Total Productive Maintenance (TPM) is a proactive approach to equipment maintenance. It focuses on preventing breakdowns and ensuring optimal machine performance through regular preventive maintenance, employee involvement, and continuous improvement.
Imagine a car that receives regular oil changes and tune-ups instead of waiting for a major breakdown. TPM is the equivalent of manufacturing equipment, minimizing downtime and maximizing production efficiency.
- Cellular Manufacturing:
This layout strategy involves grouping similar machines and processes into focused work cells. This reduces travel time for materials and tools, improves workers’ communication, and fosters teamwork.
Imagine an assembly line for a toy car, where all the components needed for assembly are located within a designated cell. This eliminates the need for workers to walk across the factory floor to retrieve parts, streamlining the production process.
- Poka-Yoke (Mistake-Proofing):
Human error is inevitable, but lean manufacturing system strives to minimize its impact. Poka-Yoke, a Japanese term meaning “foolproof,” refers to techniques that prevent errors from occurring in the first place. Imagine a car designed to prevent you from starting it without your seatbelt fastened.
Poka-Yoke mechanisms in manufacturing can take various forms, such as jigs and fixtures that ensure proper part placement or sensors that automatically detect and stop production if an error occurs.
Objectives of a Lean Manufacturing System:
- Reduced Waste:
In lean manufacturing, every activity that doesn’t add value to the customer is considered waste. The system focuses on identifying and eliminating all forms of waste, such as overproduction, waiting times, transportation, and defects. This leads to a more efficient and cost-effective production process.
- Improved Quality:
Lean principles prioritize quality throughout the manufacturing process. By eliminating defects and implementing standardized procedures, lean manufacturing ensures consistent production of high-quality products. This reduces the need for rework and scrap, ultimately improving customer satisfaction.
- Increased Productivity:
By streamlining processes, eliminating waste, and optimizing flow, lean manufacturing system leads to increased productivity. This translates to producing more units with the same resources, ultimately boosting the company’s bottom line.
- Enhanced Flexibility:
In today’s dynamic market environment, manufacturers must adapt to changing customer demands and market trends. Lean principles promote flexibility by encouraging continuous improvement and focusing on efficient processes. This allows companies to react quickly to changes and adjust production accordingly.
- Reduced Lead Times:
Lead time refers to the time it takes to get a product from raw materials to the customer. Lean manufacturing aims to reduce lead times by minimizing delays and optimizing production processes. This allows companies to deliver products to customers faster, improving their competitive edge.
- Improved Employee Morale and Engagement:
Lean manufacturing system empowers employees to take ownership of their work and contribute to improvement initiatives. This fosters a sense of accomplishment and engagement, leading to a more positive work environment and improved employee morale.
Advantages and Disadvantages:
Advantages:
- Cost Reduction: Reduced waste leads to lower production costs, improved margins, and enhanced financial performance.
- Increased Efficiency: Streamlined processes, reduced lead times, and improved production flow translate to higher levels of efficiency.
- Improved Quality: Focus on eliminating defects and standardized processes, which results in products with consistently high quality.
- Enhanced Customer Satisfaction: Faster delivery times, better quality products, and increased responsiveness to customer needs all contribute to higher customer satisfaction and loyalty.
- Increased Innovation: A culture of continuous improvement encourages experimentation and problem-solving, fostering innovation in product development and process optimization.
- Improved Safety: Focus on streamlining processes and eliminating waste often leads to a safer work environment for employees.
- Enhanced Employee Morale: Empowering employees to contribute to improvement initiatives creates a sense of ownership and boosts morale.
Disadvantages:
- Implementation Costs: The initial investment in training, infrastructure changes, and implementing new systems can be significant.
- Cultural Shift: Transitioning to a lean culture from a traditional manufacturing mindset can be challenging and requires strong leadership support and employee buy-in.
- Potential for Employee Resistance: Some employees may resist changes to established routines or feel pressure to work faster. Effective communication and training are crucial to address these concerns.
- Difficulty in Complex Manufacturing Environments: Implementing lean principles in highly complex or customized manufacturing processes can be challenging.
- Potential Inventory Shortages: Just-in-Time (JIT) production requires precise planning and coordination with suppliers. Disruptions in the supply chain can lead to inventory shortages and production delays.
Implementation Considerations – A Roadmap to Success
- Current State Assessment: Before embarking on your lean journey, it’s crucial to understand your current state. This involves diagnosing your existing manufacturing processes, identifying waste areas, and assessing your workforce’s capacity and skillsets. Conduct process mapping exercises, analyze production data, and gather employee feedback to understand your baseline comprehensively.
- Define Goals and Objectives: What do you hope to achieve with lean manufacturing? Are you aiming for cost reduction, improved quality, or faster lead times? Clearly defined goals and objectives will guide your implementation efforts and help you measure progress.
- Develop an Implementation Plan: This roadmap outlines the steps in transitioning to a lean manufacturing system. It should include:
- Our training programs provide employees at all levels with lean principles and methodologies.
- Pilot projects to test and refine lean techniques within specific areas of your operation before full-scale implementation.
- Development of a performance measurement system to track key metrics and monitor the impact of lean initiatives.
- Leadership Commitment: Strong leadership buy-in is essential for successful lean implementation. Leaders must champion the process, communicate the benefits to the workforce, and provide ongoing support throughout the journey.
- Employee Engagement: Lean manufacturing system thrives on an engaged workforce. Actively involve employees in the implementation process. Create a culture where employees feel empowered to suggest improvements and participate in problem-solving activities.
- Metrics and Measurement: Establish clear metrics to track progress and measure the impact of lean initiatives. These metrics could include production costs, lead times, defect rates, and employee satisfaction. Regularly monitor and analyze this data to identify areas for further improvement and demonstrate the value of the lean system.
Conclusion
Lean manufacturing system offers a powerful and proven approach to optimizing manufacturing processes, minimizing waste, and maximizing customer value. By understanding the core principles, components, and objectives of lean manufacturing, you can assess its suitability for your business and develop a strategic implementation plan.
Remember, successful lean manufacturing system implementation is an ongoing journey requiring continuous improvement, employee engagement, and a culture of innovation. Embrace the challenge, and watch your manufacturing operation transform into a lean, efficient, customer-centric powerhouse.
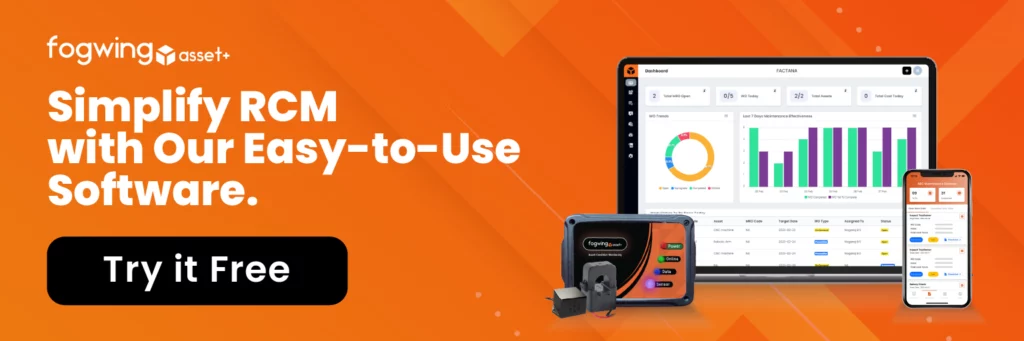