- Technical Guide
Lean Manufacturing
Everything you need to know about Lean Manufacturing
Table of Contents
Introduction
Lean manufacturing happens to be one of the buzzwords in the business of manufacturing. As the market gets increasingly competitive, growing number of manufacturers are seeking to establish lean manufacturing system for production. However, aiming to become an efficient manufacturer with optimized resource utility is no overnight achievement. Hence, exploring the many facets of lean manufacturing are critical in the journey of adoption and transformation.
What is Lean Manufacturing
Lean manufacturing is a production process ideology that focuses on maximizing efficiency by minimizing waste in brief. The first chapter of this technical guide will introduce you to Lean manufacturing and key components that serve as an ideal beginning to delve into exploring Lean manufacturing concepts.
Lean Manufacturing Definition
Lean manufacturing philosophy propagates value addition into systems of production. As a framework that is systematic in nature, Lean manufacturing aims to eliminate waste from a manufacturing system or value stream without forgoing or abandoning productivity.
The value stream in manufacturing comprises of all activities and information channels of raw material vendors, business benefactors, production processes, tools and techniques of manufacturing till final product reaches the possession of consumers. Lean emphasizes the empowering people of all levels in the organization to identify and eliminate waste that depletes value to consumers and instead add value that will contribute to customer deliverables.
A culture that encourages activities that adds to manufacturing credibility whilst eliminating activities that hinder productivity and operations are identified as lean framework.
Example of Lean Manufacturing
Lean manufacturing examples aid the understanding of lean principles. It can equip the analysis of implementation process in a traditional manufacturing atmosphere.
Example 1: MicroMetl, Nevada based heating and air conditioning manufacturer, aimed to achieve high efficiency, sustain high quality of product consistently using lean principles / framework. This triggered to conduct an analysis of the workflow.
A workflow analysis revealed that a single heating and air conditioning part traveled 1.5 miles in the plant during assembly. The travel distance was seen as a waste element in ensuring efficiency. To eliminate this waste, the company cellularized the manufacturing process that enabled the part to be assembled within a radius of 100 feet instead of 1.5 miles.
Example 2: Another lean manufacturing example could be that of a customer service in manufacturing. Customer service in manufacturing can find it challenging to keep up with organized demand for orders. Upon an analysis of workflow, the issue was that pre-production lead times were time consuming and administrative tasks that were non-value adding kept the orders reaching the floor. The management can then be prompted to implement lean manufacturing activities, starting with mapping of existing customer service process to identify value points and eliminate waste.
To better manage customer services, workers were trained in Kanban, pull system of manufacturing and 5S. With this training, 20% increase in the capacity to accommodate orders can easily be achieved along with a significant scale-up of on-time-delivery (85% – 90% approx).
What is the goal of Lean Manufacturing?
The goal of lean manufacturing can be summarized in 4 pointers besides grasping from a formal definition. The four main pointers are:
a) Improve the quality of products by adding value to manufacturing
b) Eliminate unnecessary waste
c) Decrease product lead time
d) Reduce total incurred costs
8 Wastes of Lean Manufacturing
This section elaborates the 8 wastes of lean manufacturing. In a manufacturing organization, processes, event or activities can be ideally identified into one of the 3 categories:
a) Brings value to business / Business value add-on.
b) Offers value to customer / Customer value add-on.
c) Does not provide value. Simply in place to be adhered
The 8 wastes of lean manufacturing are the ones identified under category (c) as they do not add any value to the processes of manufacturing.
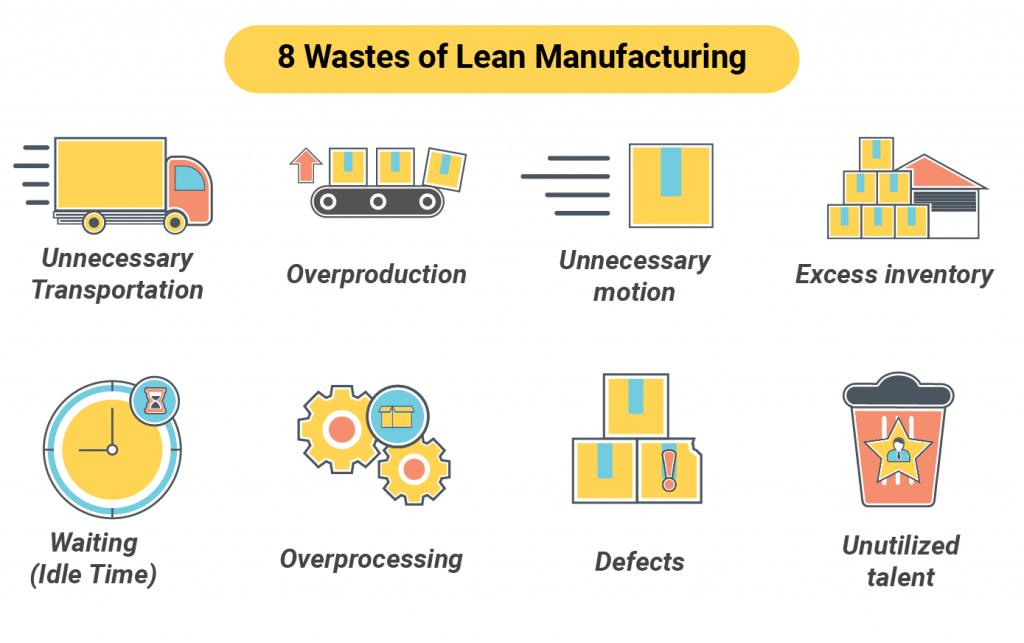
Overproduction
Although the idea of producing excess may seem appealing to serve as safety buffers, it cannot that be denied that at an initial stage, it over utilizes valuable resources. Monetary investments remain fixed during work-in-progress (WIP) and inventory along with increasing overhead / operating expenses.
Lean manufacturing system on the contrary, emphasizes on the production based on customer demands. The single-flow system is upheld, where only at the completion of work at one phase does it move to another keeping different phases ready to execute work.
Waiting (Idle Time)
In manufacturing, several processes / activities / events accompany in the making of a product. When these events / processes are not well-synchronized, waiting (idle time) becomes an issue. Some of the examples of idle time include, bottlenecks in production that reducing scalability / efficiency, operators waiting for assets or tools, machine faces unexpected downtime, active unplanned maintenance and so on. Analyzing idle time events can help navigate to the root cause of reoccurring faults in production. Identifying the root cause of these issues are critical in eliminating waste.
Defects
When a product fails to meet the quality and specifications, it is identified as defect. Once identified as defect, the product requires to be scrapped or reworked. With customer satisfaction as the crux of lean manufacturing, achieving zero defects in manufacturing is a priority.
It is advised to conduct a root cause analysis as part of lean manufacturing system to recognize and isolate possible reasons for defects in manufacturing. Lack of workforce training, mis or over handling of equipment, excess inventory, maintenance glitches are a few examples of root causes that can cause defects.
Overprocessing
Overprocessing are any activity, event, process or communication that does not contribute to value addition or is redundant in its value component. Examples of overprocessing can be; lengthy and unnecessary levels of review / approval, immoderate quality inspections, inadequate product and scope descriptions.
Mapping of manufacturing processes / steps is essential as it will help in recognizing and isolating redundant steps that do not serve to increase value to business and / or customers. Once such steps are identified, process re-configuration can begin with elimination of wasteful events.
Inessential Transport
Transport does not reflect the supply of inbound and outbound logistics alone but also extends the shifting of materials and people within processes. Inessential transport leads to unnecessary time consumption leaving no value addition to the product. Contrary to value creation, inessential transport can cause increase in damage rectifying issues, hinder communication, delay production time, and even cause inefficient material utility.
Inessential transport can be eliminated from manufacturing by planning the trajectory of raw materials and people movements within the manufacturing facility. The trajectory of resource movements must be product-oriented and grouped according to the flow of phases in manufacturing. It must also be cautious to not involve people efforts in non-value generating tasks.
Unnecessary Motion / Movement
Unnecessary motion refers to the unwanted migration / movement of people and machines in manufacturing. Unnecessary motion cause 3 primary issues; a) safety challenges, b) quality concerns and c) reduced productivity. Repetitive movements and poor ergonomics cause employee health crisis that negatively impacts the efficiency and incurs costs to employers. Simultaneously, safety challenges, quality concerns and wasted exertion causes a dip in overall factory operability and production.
Motion / movement or migration must be paced, natural, comfortable and flexible to operators / workforce. Mapping each step and observing people, receiving their suggestions to minimize motion of asset and people will enable the cut down of unnecessary motion across factory floor and within processes.
Surplus Inventory
When manufacturing business hold surplus inventory, the issue points straight at poor planning and tracking, errors in changeovers, imbalanced production cycles and inaccurate forecasting systems. Housing surplus inventory negatively impacts cash flow in businesses as it keeps the investments idle until sales and holding back resources that could have utilized elsewhere.
Surplus inventory increases risks of theft, unchecked quality issues with an idle batch and damage due to calamities. To keep watch of a surplus inventory would require a management in place for which excess costs will be incurred by employers.
Therefore, it in the best interests of the business to avoid surplus inventory and practice in-time delivery of raw materials and production streamlining to conduct manufacturing to meet the demands of customers whilst reducing WIP (work-in-process).
Unutilized Talent
Employing talent in the manufacturing business is a significant component. Less engagement of talent or underutilizing talent can take many forms such as; a) stagnant knowledge sharing, b) employees performing low-value or irrelevant tasks, c) lack of space for employee feedback and perspectives.
Frequent talent identifying and regular employee engagements to understand their perspectives and work satisfaction with career interests will enable to chart areas of underutilized talent. It keeps managers and leadership aware of gaps and likewise work towards harnessing employability skills and capability management.
Lean Manufacturing Solutions
Lean manufacturing solutions are closely knit to the application of lean manufacturing tools in addressing industry challenges with a problem-based approach.
Lean manufacturing tools would ideally include and aim to follow the trajectory of lean manufacturing solutions listed below.
a) Identifying the problem
b) Analysing the problem
c) Target setting for improvements
d) Conduct root cause Analysis
e) Developing countermeasures
f) Executing and fulfilling the countermeasures
g) Checking to see if there were any changes
h) Standardizing the solution to then share it
History of Lean Manufacturing
Although lean manufacturing offers ample benefits to manufacturers, it is critical to draw insights from the past to ensure ideal implementation standards to meet the requisites of efficient and optimized manufacturing. This section encapsulates brief episodes in the propagation, identificationand further development of lean manufacturing methodology.
Early Lean Concepts
Early concepts of lean can be tracked down to Benjamin Franklin, who still is pictured as a man ahead of his time. Franklin in the mid-1700s documented the waste reduction examples from his experiments.
Benjamin Franklin’s work, ‘Poor Richard’s Almanac’, written and published in volumes between 1732 and 1758, although aims at personal conduct in translation has served well to replicate and understand events in businesses and manufacturing. Franklin employed the persona of ‘Richard Saunders’ aka ‘Poor Richard’ to author the Almanac to reflect ideas of great stature.
Excerpts from the Almanac, ‘A penny saved is two pence clear….. save and have’ translates to spending less can bring in more value and revenue. ‘Lost time is never found again, speak little do more’ translates to focus more on implementation and action in ensuring efficient business / manufacturing than simply strategizing without action.
In ‘The Way to Wealth’, Franklin warns of the challenges that accompany unnecessary inventory in manufacturing.
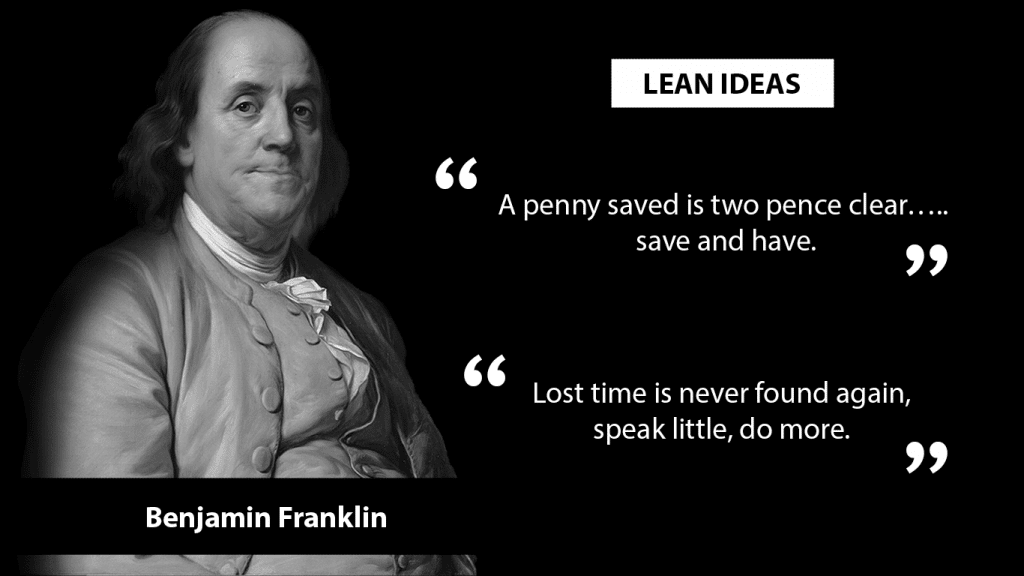
Frederick Winslow Taylor in 1911 introduced what would become recognized as Standardization and Best Practice Deployment. In the words of Taylor, “And whenever a workman proposes an improvement, it should be the policy of the management to make a careful analysis of the new method, and if necessary, conduct a series of experiments to determine accurately the relative merit of the new suggestion and of the old standard. And whenever the new method is found to be markedly superior to the old, it should be adopted as the standard for the whole establishment.”

Henry Ford, on the lines of Franklin’s idea of waste reduction, developed mass assembly manufacturing system, to a great success identified and eliminated material and motion waste contributing to efficient production, optimized resource utility and cost effective. Henry Ford in his autobiography, ‘My Life and Work’, encapsulates lean manufacturing in a single statement – “We will not put anything that is useless into our establishment.”
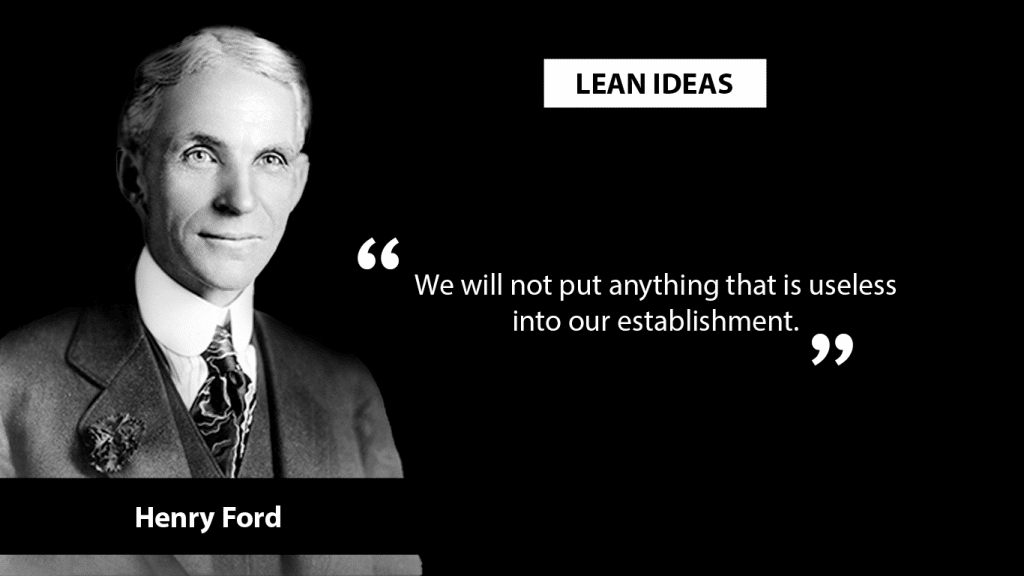
Training Within Industry
Training within Industry was created in 1940 by the United States Department of War. It was a service crafted to provide job training in war-related industries where shortage of skilled personnel had a negative impact. Four core programs together operated in the training within industry.
a) Job Instruction – Focuses on teaching a method to an operator regarding how to perform a job by adhering to compliances and safety, whilst performing the job correctly.
b) Job Relations – Engages in educating on the principles of employee relations, team building, effective employee engagement, promote employee motivation, cooperation and conflict resolution.
c) Job Methods – Teaches employees methods to evaluate their performance in work and suggest improvement.
d) Program Development – Educates trainers to further assist and help line-managers in problem-solving.
By the end of World War II in the year 1945, there were about 1.6 million workers certified in Training within Industry.
Toyota Production System
Post the end of World War II, Japan was strongly influenced by the Training within Industry that initiated the development of Toyota Production System by Taiichi Ohno and Eiji Toyoda, industrial engineers at Toyota. The Toyota Production System has been globally recognized and applauded for offering huge success and high stature to Toyota.
Toyota Production System stands on two pillars:
a) Just-In-Time: This principle emphasizes on producing only what is needed, when it is required and in what amounts / quantity it is required.
b) Jidoka: Refers to ‘Intelligent automation’ or ‘Automation with a human touch’ in the Toyota production system.
The main aim of Toyota Production System is to eliminate waste by designing out inconsistency and overburden.
CHAPTER 3:
Lean Manufacturing Principles
Lean manufacturing has evolved and been influenced over the years by many concepts. The Toyota Production System has been a powerful influence and contributor to the establishment and success of Lean principles in manufacturing. John Krafcik in his article title “Triumph of the Lean Production System”, 1988 first coined the term ‘Lean’. The article was based on narration of his experience as quality engineer Toyota – GM venture in California.
That having been stated, it’s a priority to identify and answer the question of ‘What are lean principles in manufacturing’ before delving into tools and techniques of implementation. Lean principles in manufacturing dictate the terms for a fully equipped set-up and efficient functioning of a lean manufacturing system. This section focuses exclusively on providing a holistic idea of the principles that govern lean operations in production.
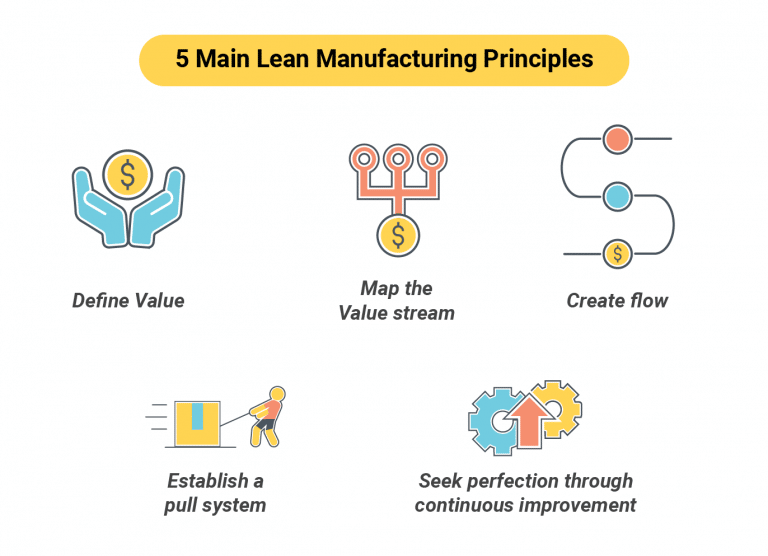
Define Value
Value of product or service is a distinguished priority to its end users. All customers hold value for different facets of a product or service. Lean philosophy emphasizes on the need to analyze and grasp components that are perceived valuable by consumers / customers along with recognizing the price they are willing to pay for that value.
Upon thorough research of consumer / customer value and price, manufacturers aim and work towards delivering that value component at an optimum price. Throughout the process of manufacturing, eliminating waste and unnecessary costs to ensure maximum profit margins will be extensively focused.
Value Stream Mapping
It is essential to map a value stream to ensure value-based manufacturing. The production of a physical component / single unit is a small part of a complex web of manufacturing activities /events. While on the other hand, the value stream accounts for the mapping of the entire business lifecycle in the process of manufacturing, from input of raw materials, resource utility and administration to inventory, waste management and distribution channels.
In the active mapping of value stream, different activities, events, procedures and process in the entire manufacturing business cycle is charted and evaluated to establish whether it is a value addition to the process. If it is found to be zero value contributor, it will be discarded.
Create Flow
‘In the value stream mapping, if it is assumed that all events, activities and processes deemed unnecessary are eliminated, then each step / phase in the manufacturing adds value to the final product, in addition to cutting costs and optimizing resource utility.
Following a clear value stream, a continuous flow of processes in manufacturing is to be created and ensured. With an ongoing, continuous flow of processes, businesses are guaranteed the sequence of phases in manufacturing along with its duration. In creating a continuous flow of operations in manufacturing, all queuing, delays, unexpected asset downtime, excess inventory management challenges are removed.
Establish Pull Manufacturing System
As opposed to push system, lean principles operate on pull system of manufacturing. The push system produces certain quantities that go into storage. Historical customer demands and current production efficiency form the basis of storage capacity in push manufacturing.
With an aim to limit inventory and produce goods that customers are keen on buying, pull system of manufacturing focuses on synchronizing inputs on Just-in-Time (JIT) basis and manufacturing for a known demand. This system operates efficiently with good customer and supplier relationship along with strong internal and external communications, optimized production, flexible working teams.
Perfection through Improvement
Kaizen is a Sino-Japanese word for improvement, which is a core principle in lean manufacturing. Kaizen emphasizes on sustaining and further improving current processes and operations in manufacturing with small incremental changes now and then.
CHAPTER 4:
Tools of Lean Manufacturing
Lean manufacturing tools are frameworks to conduct workflow analysis, identify and solve problems, measure performance and optimize work processes whilst ensuring effective people and change management.
Lean manufacturing techniques, tools and concepts at the disposal of manufacturers are many. However, it can be perceived as tools in a toolbox, where the best suited tool / technique for your business is to be employed for effective implementation and practice of lean principles.
Implementing lean manufacturing principles requires to be a continuous and iterative process. This section further lists the different tools and techniques of lean manufacturing that can be employed at different phases of your manufacturing journey.
i) Poka-Yoke – Poka-Yoke refers to ‘error proofing’ a process, it is Japanese for ‘preventing inadvertent mistakes’. Poke-Yoke accepts that mistakes / errors are at times inescapable, but emphasizes that it is unacceptable to have these errors reach the customer. The ultimate goal of Poke-Yoke is to prevent product defects and errors from reaching customers by identifying, rectifying and eliminating faults at the source.
Integrating Poka-Yoke inline with manufacturing allows manufacturers to catch errors / defects as they occur or even better prevent errors instead of inspecting for defective products at the end. With Poka-Yoke defective products are identified and rectified or eliminated as when it occurs, thereby ensuring a flow of product quality excellence. MES software help in defective identification while implementing Poka-Yoke tool.
This system employs 3 control mechanisms:
a) Visual Management – directing behaviour by signalling deviations
b) Failsafes – Offering no alternative, force a behaviour.
c) Visual Aids – Permit an individual to visualize and direct the correct work way or method.
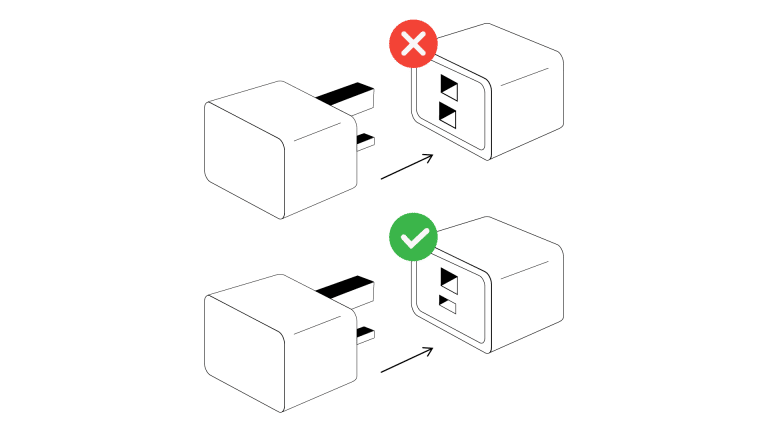
ii) 5S Lean Manufacturing – 5S is a systematic framework for organization of workspace. The 5S Lean Manufacturing is based on the idea that a better workspace contributes to efficient production that in turn ensures high quality of products being produced.
Creating a clean, uncluttered and safe workplace prevents accidents, misplaced or untraceable assets, enables easy locating of tools and assets and drives a focused mindset and encourages continuous process improvement.
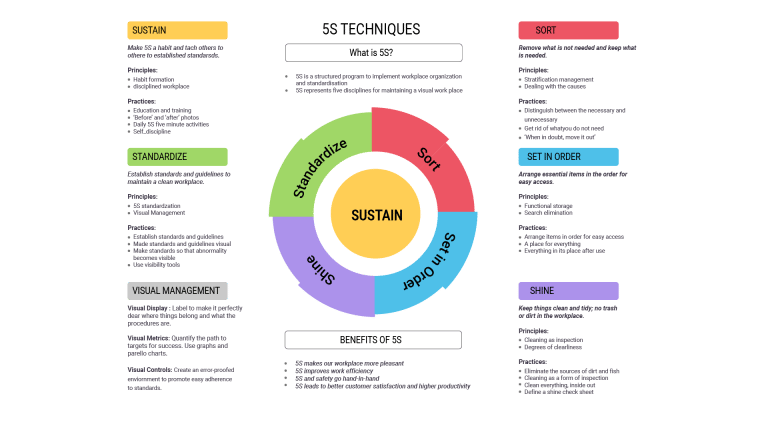
iii) Total Productive Maintenance – Total Productive Maintenance is a set a techniques / strategies employed in the manufacturing industry to ensure that all machines / assets in production are able to consistently perform its allocated functions or tasks whilst facilitating production efficiency.
There are 8 strategies that are identified as pillars of Total Productive Maintenance that are identified as a lean manufacturing technique within a lean manufacturing system. From designing products that can be produced by existing machines and recognizing equipment potentials to maximum production to training workforce to handle processes / change and autonomous maintenance. Total productive maintenance can be efficiently practiced with the implementation of technologies of Industry 4.0, particularly, smart asset condition monitoring software.
The image below depicts the 8 pillars of Total Productive Maintenance.
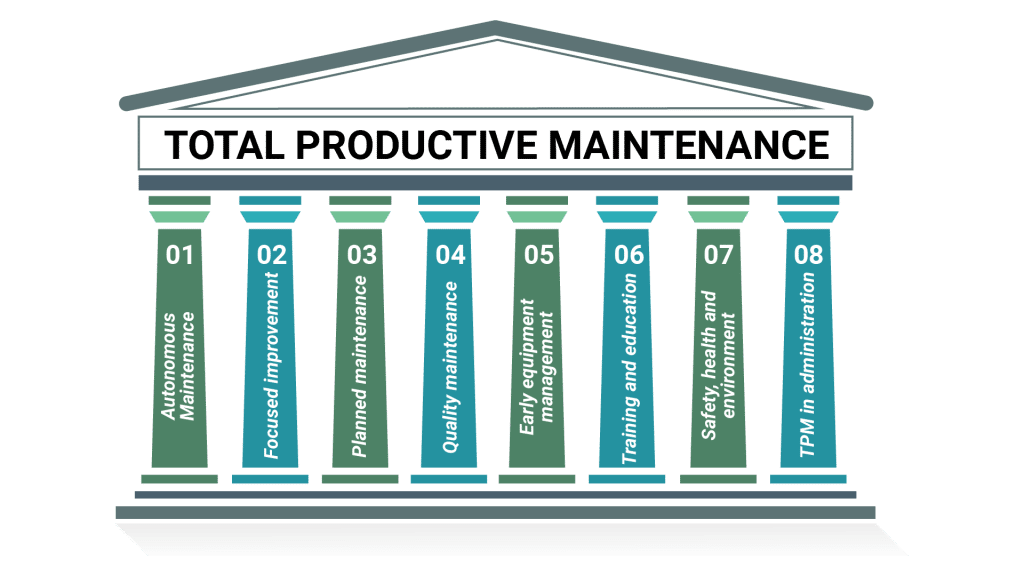
iv) PDCA Method – PDCA method is an acronym for Plan, Do, Check, Act. It is primarily focused on problem solving and describes four actionable steps for analytical thinking and problem solving in the manufacturing sector.
The PDCA tool operates with an aim of improving processes, activities, products and /or services in the manufacturing sphere on an ongoing / continuous manner. The goal of PDCA method is to engage in continuous process improvement.
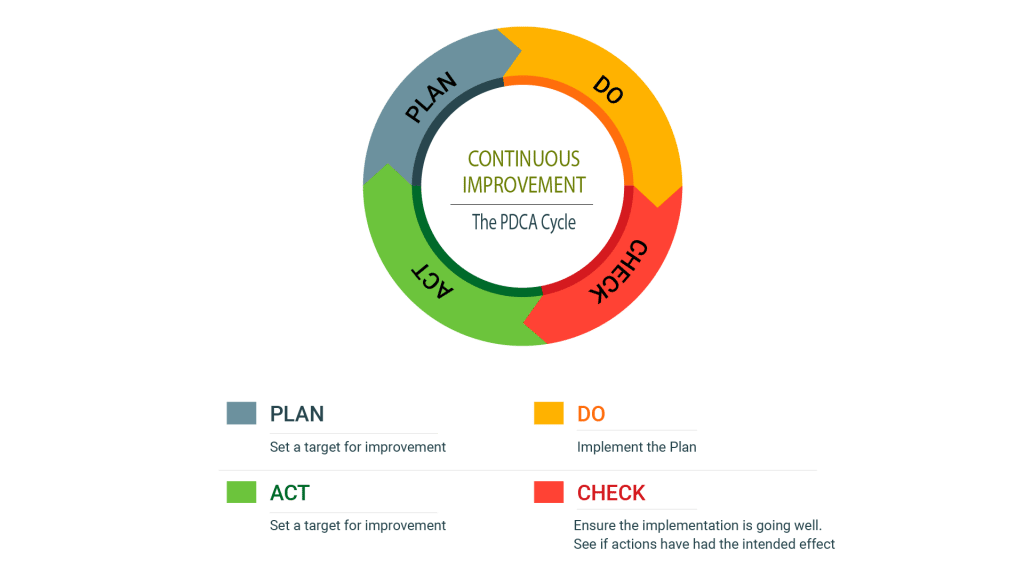
v) Visual Management (Kanban or Kamishibai Boards) – Kanban and Kamishibai are distinct visual control methods that support workflow visualization, work efficiency and quality control. These are actively employed as lean manufacturing techniques.
Kanban translates to visual signal. Kanban was developed by Toyota for part scheduling where workers filled out signal card as and when parts neared exhaustion, Kanban translates to visual signal. The goal was to order parts as and when required with emphasis on eliminating waste specific to time, materials and costs. Kanban since then has been appropriated into a broader methodology. In the broader sphere, it is applied to manage workflows, where cards are used to display work status and stage on a board.
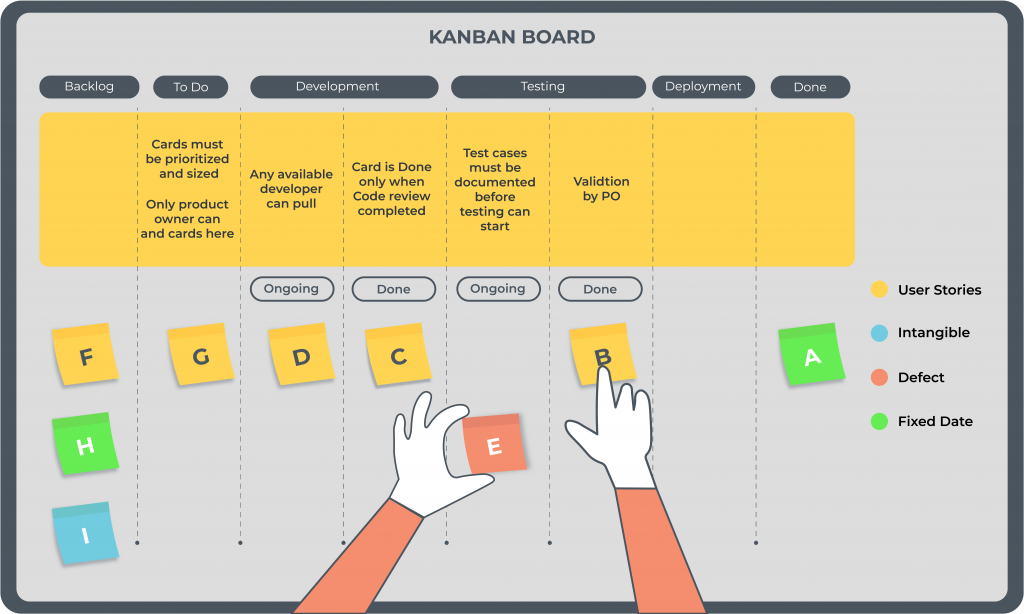
Another similar visual control board is Kamishibai that is employed to perform audits. Kamishibai is used to display status of audits (whether pending or completed) and indicate any abnormalities if found. The goal of using Kamishibai boards were to immediately rectify issues or eliminate waste as and when it was found. Management’s used Kamishibai boards as part of their standard work processes on shop floors to keep close watch on costs, resource utility and processes.
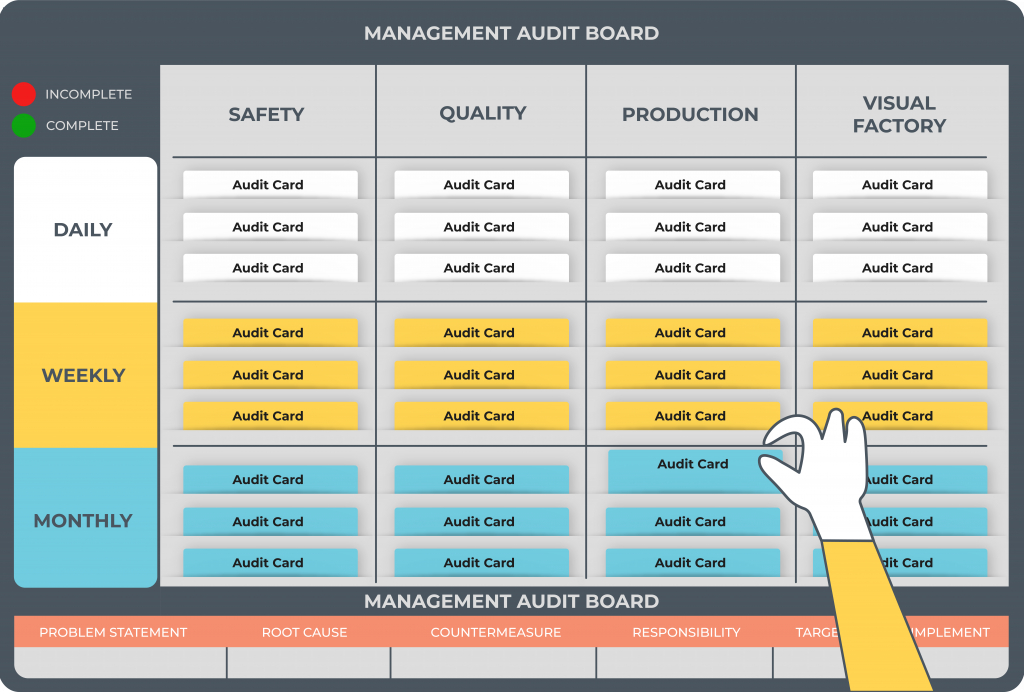
vi) Kitting – Kitting refers to assembling all parts, components and materials required to complete a task into a kit, ahead of delivering to the point of utility. These kits can further be given a single stock keeping unit code. Kitting ensures that all materials and parts for task completion on the production line are present in right quantity and quality.
Kitting can significantly help better inventory control, ensure effective personnel performance with production processes, reduce warehouse needs and conduct efficient onsite production.
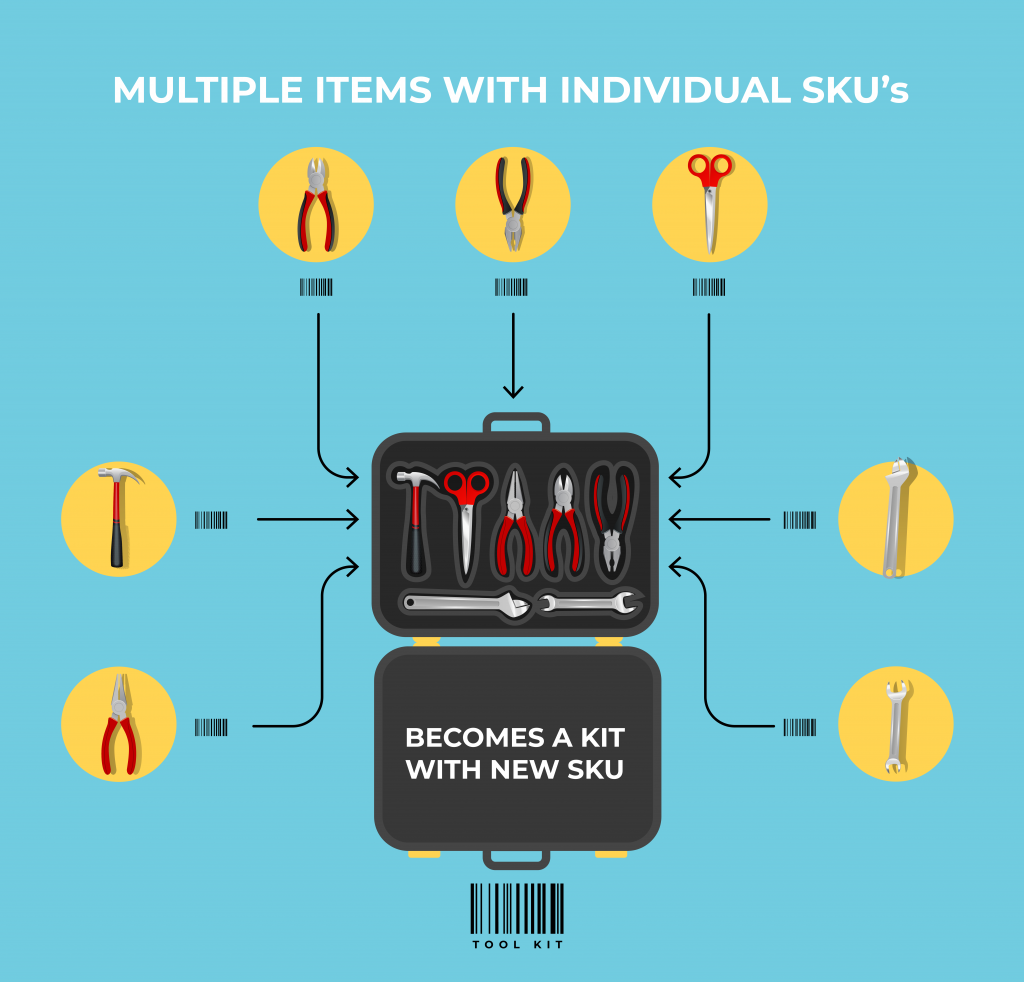
vii) Gemba Walk – Gemba Walk is Japanese for ‘the real place’ that translates to where the real work is happening. As with the manufacturing sector, the real work happens in the production line. This concept was designed by the Japanese to get their executives and management personnel out of offices and engage with onsite workers. It was aimed building relationships between executives and workers to understand first-hand challenges faced by workers in order to meet production needs. IIoT Platform, Smart MES and Asset Monitoring when incorporated with manufacturing processes add significant value to findings of Gemba walks.
Three elements of Gemba Walk:
a) Go and See – Used to get all managers to regularly interact with workers, witness their work and challenges to further co-ordinate and solve wasteful activities / events in production.
b) Ask Why – It emphasizes to trigger questions, listen, analyse and learn. Finding points in the value stream to enhance efficiency or even solve problems.
c) Respect People – Respecting people reinforces that Gemba walk is not a boss walk looking to point errors and blame people. It is solely to bring executives and managers to listen, watch, learn and work with workers on the production frontiers to resolve inefficiencies and shortcomings.
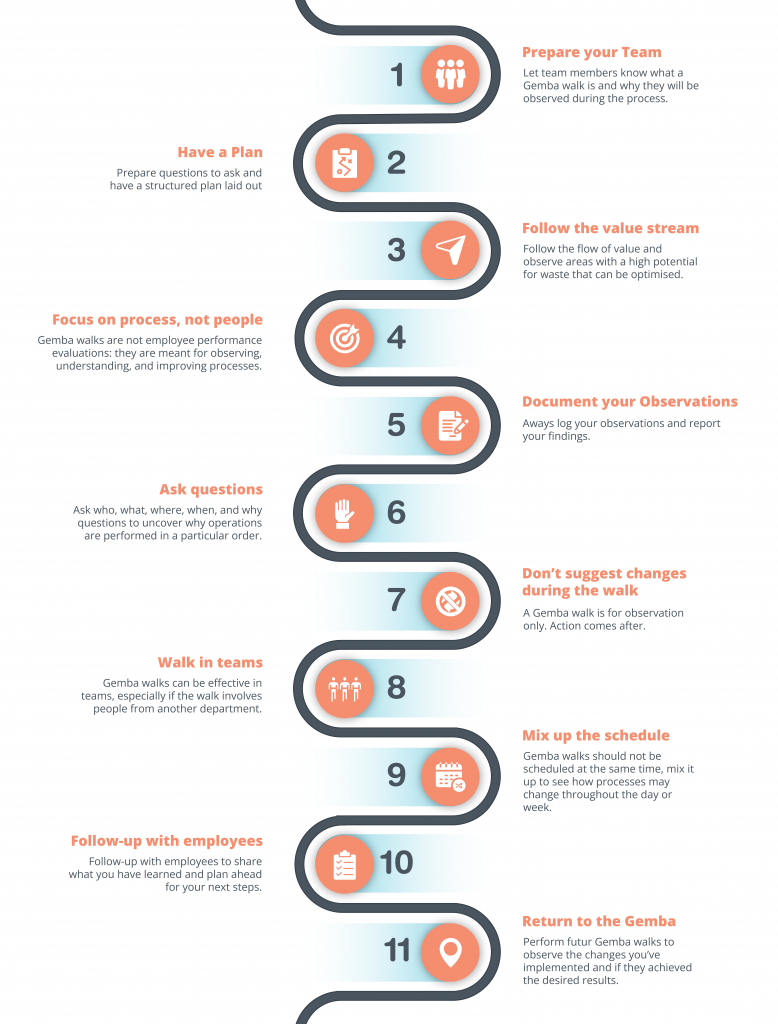
viii) Andon – Andon was developed by Toyota as a system that notifies management of a process or quality crisis or problem. Light stack is typically used in the event of alerting management of errors or issues and minimize wasteful activities / losses. A smart MES can digitalize Andon system of lean in manufacturing processes.
Just like the traffic light signals, green light meant no issues, assuring a smooth-running production. If the operator activated the yellow light, it meant that a minor issue has been detected, although now it has not required the production line to stop, if goes unaddressed it could become a big problem. Red light indicates that a major production or defect has been detected causing the whole production line to stop.
CHAPTER 5:
Benefits of Lean Manufacturing
Manufacturers continually seek ways to sustain progressive business of their products in the global competitive market. Lean manufacturing helps manufacturers and businesses to gain, sustain and progress a competitive edge. Some of the crucial benefits of lean manufacturing are jotted below.
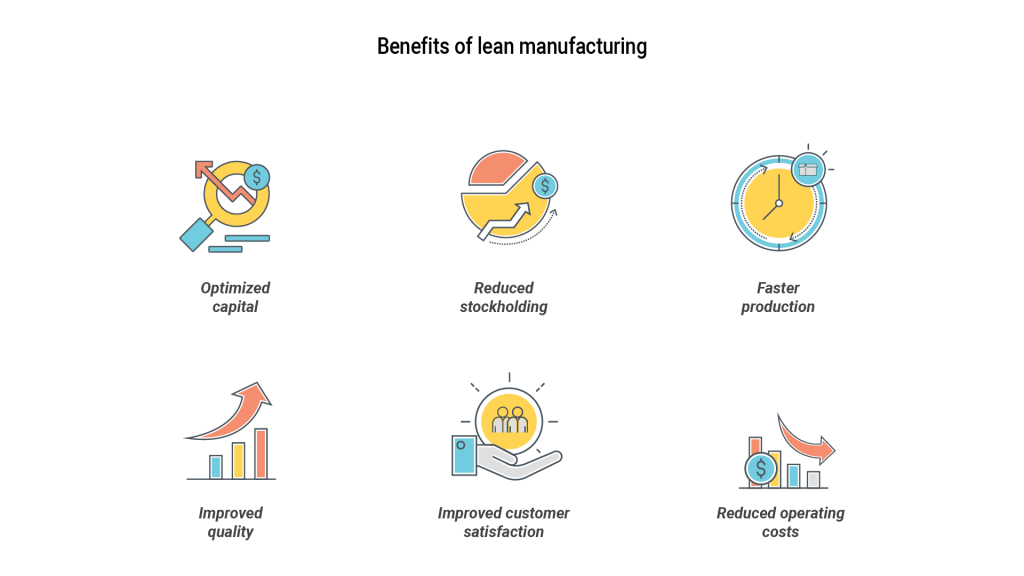
i) Enhanced Customer Satisfaction – The primary goal of lean manufacturing is to increase value to customers through fast, flexible production ensuring best product quality. With the onus upon the manufacturers to study what serves as ideal value for customers and deliver the same, businesses create opportunities for customer loyalty. Higher levels of customer loyalty indicate enhanced customer satisfaction that paves way for increased revenues.
ii) Improved Product Quality – The principles of lean manufacturing emphasize on the pursuit of optimization and perfection along with people empowerment at different levels of the organization. Teams for quality assurance and control are encouraged to look into product quality at different phases in manufacturing. Manageability being the linchpin of equipment modularity for quick change is practiced. With this flexibility, managers / operators can significantly reduce scrap count and ensure improved product quality.
iii) Capital Optimization – One of the major lessons with Toyota was that automation for its own sake seemed wasteful and impacted little on operating performance. The implementation of lean focused more on holistic product design and development, trained and equipped workforce with a supportive network of suppliers and stakeholders. With the lean mindset, capital investment in automation for its sake without understanding it’s potentials to match the manufacturing needs will be eliminated.
iv) Optimized Production Time – Getting rid of wasteful and unnecessary processes, actions and environments in the manufacturing helps streamline the entire production process. James P Womack, the then director of International Motor Vehicle Program (IMVP) noticed this very benefit of process streamlining through elimination of wasteful events in manufacturing that led to Toyota producing two times more than Ford’s production.
When production line operates faster, customer satisfaction increases along with creating more space for completing new orders without keeping customers wait. Increased production levels generate more revenue by raising the contribution margin of each product manufactured.
v) Shrink Inventory Stocking – Pull manufacturing is one of the many core principles of lean framework. Pull manufacturing simply reflects the idea of manufacturing to attend to the demand of customers than to manufacture and stock goods waiting for its purchase / sale. In addition, suppliers are encouraged to supply materials as and when required, thus saving excess inventory stocking. With reduced inventory hoarding, capital investment associated to floor space occupancy, asset handling and warehouse workforce can be significantly lessened.
vi) Cut Operating Costs – Wasteful events, processes can be understood differently depending on the commodity being manufactured. From producing scrape materials, dodging excess inventory to employing surplus labor and prolonged maintenance mechanisms can be cited as examples of wasteful events. Adopting lean principles will ensure that such events are minimized thereby contributing to the decrease in overhead and other operating costs. It also helps create sharp pricing models in business.
CHAPTER 6:
Lean Manufacturing In Industry 4.0
While the lean manufacturing methodologies have been tried and true for decades, the onset of Industry 4.0 with newer sophisticated technologies are at the wake of revolutionizing traditional lean strategies and principles.
a) Sensors and Devices at Source to Conduct Error Proofing and Ensure Quality – Error proofing manufacturing processes have become so much easy with the accessibility of sensors, integration of devices and deployment of manufacturing software. Here are a few examples of ensuring quality through smart sensors and devices.
i) Employ digital weigh scale to check the weight of a product in a manufacturing phase to ensure it meets requirements, prior to moving it to the next phase of the process.
ii) Tools integration (torque drivers, bore gauges, calipers) to perform operations to exact specifications.
iii) Enable machine vision inspection with devices and sensors that prompt the detection of quality of product at each phase in the manufacturing process.
b) Digitizing Standard Work Procedures – The traditional methods of paper instructions running pages together every time there is a process update is not a competitive procedure anymore. There are ample digital software specific for work instructions and communications that improve experience of operators. Digitalize work instructions allows manufacturers to incorporate multimedia and IoT devices for better management and engagement of operators and procedures across the factory floor.
There are benefits of digitizing standard work. One of which is the ability to accommodate customizable work while allowing changes to be automatically updated across a plant. Digitizing standard work also enables the maintaining of up-to-date work instructions and does not miss on inculcating change management.
c) Customer Centric Approach – One of the primary lean principles is the emphasis on customer centric production. Digital technologies of the industry 4.0 are empowering manufacturers with an elaborate picture of customer needs. For example, advanced data analysis or even artificial intelligent can be applied to customer data to better understand customer needs and in-demand goods / services.
A simple example can be that of an App use behavior analysis, or when and where the product origin is accessed via labels. Mass customization is also practiced with semi-automated robots that cope with high degree of change are integrated into production lines to accommodate customized orders. These are some methods og how the customer centric or ‘Just-in-time’ principle of lean is integrated with Industry 4.0.
d) Value Stream Integration – Another core lean principle is to eliminate waste in the value stream, from customer order through raw material acquiring, processing, production and delivery. In this chain of events in manufacturing, industry 4.0 enablers like data analysis and analytics, connectivity, vertical and horizontal system integration are great contributors in the pursuit of achieving value stream integration.
Integration and connecting of your enterprise, IT, OT, machines, assets, and tools creates a holistic view of the entire value stream in each phase of manufacturing. Connecting and integrating value stream in manufacturing enables managers and operators to identify patterns, recognize errors and determine scope for improvement.
e) Continuous Improvement – Continuous improvement through elimination of waste and addition of value into the production line is a lean principle. Industry 4.0 adds to the effective implementation of this lean principle within manufacturing with powerful simulation tools. Digital twin an industry 4.0 tool enables manufacturers to initially test their designs and assumptions in a virtual world, prior to testing or implementation in the physical world. In this way, the scope for continuous improvement is ensured within manufacturing.
Conclusion
Lean manufacturing is a vast topic in manufacturing. It has been subject to development over many years. The ability of lean principles to integrate with emerging technologies makes it more appealing to manufacturers to adopt lean system of production. The scope of lean extends to achieving holistic experiences in the realm of manufacturing by emphasizing on eliminating waste, adding value to production and delivering customer-centric products / services.
The scope of this guide does not limit itself to the contents provided herewith but is open to extend the area of research and addition of growth-oriented knowledge.
This technical guide is contributed by Sancia Catherine, Sharathkumar Subramani and Team.