With the world rapidly digitalizing, multiple adjacent technologies enhance and integrate innovation into the manufacturing industries. Digital Twin Technology in manufacturing industry is one such technology, that can create a revolution in manufacturing operations management. It serves various practical purposes like system simulation, integration, testing, maintenance, and monitoring.
What is Digital Twin Technology?
A Digital replica of the real-world physical system, product, process, or service is known as Digital Twin Technology. Digital Twin software includes the technologies like Augmented Reality, Internet of Things (IoT), cloud computing, Artificial Intelligence, and many more which are combined to solve the digital simulation requirements efficiently. The Digital Twin Technology simulates the current and previous conditions of the physical entities, for organizations to analyze the working of physical asset.
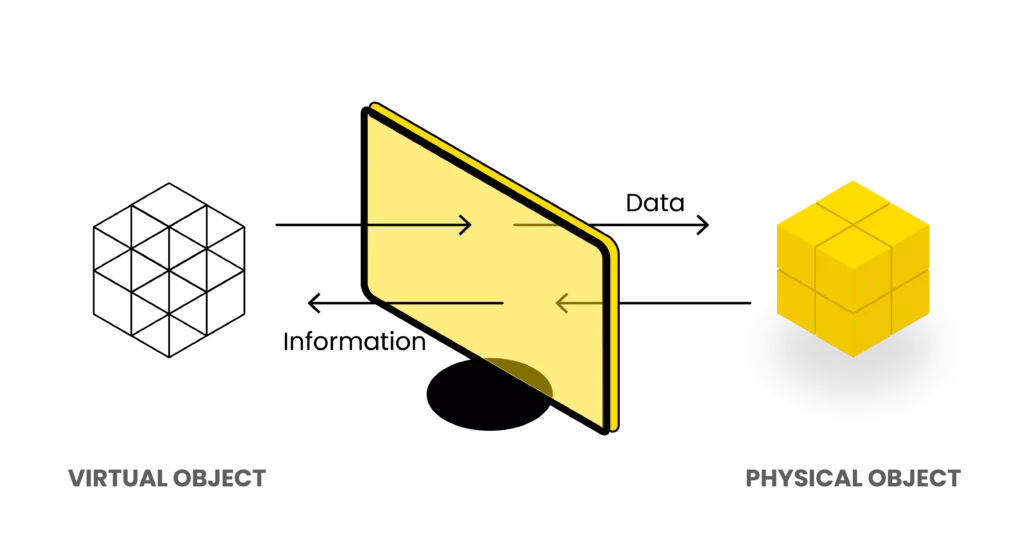
Digital twin Ecosystem
Let’s familiarize ourselves with a few concepts of the Digital Twin ecosystem.
Digital Twin platforms provide long-term benefits for asset performance and optimizations. The technologies like Artificial Intelligence, Sensors, Machine Learning, Internet of Things enable data transmission between the physical and digital twins. Digital Twin Technology can learn, update, and communicate with its physical counterparts and enable, data learning at any given time.
Digital twin platforms are not restricted to a single instance. The integration of multiple Digital Twin solution empowers the creation of the Digital Twin ecosystem.
The Digital Twin ecosystem consists of various stages of the twin model:
- Digital Twin Prototype
- Digital Twin Instance
- Digital Twin Aggregate
Digital Twin Prototype (DTP)
DTP is the prototype of the product or the physical asset. It is a master copy for the product reference that’s presented even before the existence of the product in the real world. It consists of design, analysis, and process, which will be utilized to build physical products in the given time. So, DTP is generally known as the recipe for creating an asset. The DTP involves data regarding physical attributes, properties, operating parameters, part numbers, and bills of materials.
Digital Twin Instance (DTI)
DTI in Digital Twin Technology is linked to the product throughout its lifecycle and runs tests on various use-case scenarios. It generally includes the data related to in-use conditions captured through the previous state, predicted state, sensors, asset information, service records, etc. DTI initially utilizes the baseline data from the product prototype and will later get enriched with the operational information generally.
Digital Twin Aggregate (DTA)
DTA gathers DTI data to determine the product capabilities and to run multiple test operation parameters and prognostics in Smart Manufacturing. Digital Twin Aggregate in Digital Twin Technology is a collection of DITs, which might be co-located within one entity or across the entity.
For Example: 100 machines located in a single factory, or 100 machines located across 15 different factories
Types of Digital Twin Technology
The following are some of the types of Digital Twin technology applicable in Manufacturing Industry:
Parts Twining
Parts Twining is the virtual representation of the individual components of a product. At this stage, the individual components or parts of a product are virtually represented with the help of digital twin technology. It empowers engineers with the ability to understand the physical, electrical, and mechanical characteristics of the given individual component.
Example: Electronic circuit simulation software shows how an electronic component will react when multiple electric signals are injected into a circuit. The mathematical model or the digital twin application predicts real-world behavior when tested under a variety of scenarios.
Product Twining
Integrating and twinning individual parts to know how they operate when incorporated together is known as product twining. It provides the proper insight into the working of products. How different components interact, and how the environment of the product affects the working. The product twining in Digital Twin Technology minimizes the Mean Time Between Failure (MTBF) and Mean Time Repair (MTTR).
System Twining
System Twining is the next higher level in Digital Twin Technology. It allows engineers to organize and maintain whole fleets of disparate products that work collectively to attain a result at the system level. System twining monitors and experiments with their systems, to gain unparalleled efficiency and effectiveness.
What is the difference between Simulation and Digital Twin?
The terms simulation and digital twin are often used interchangeably, but they are two different technologies.
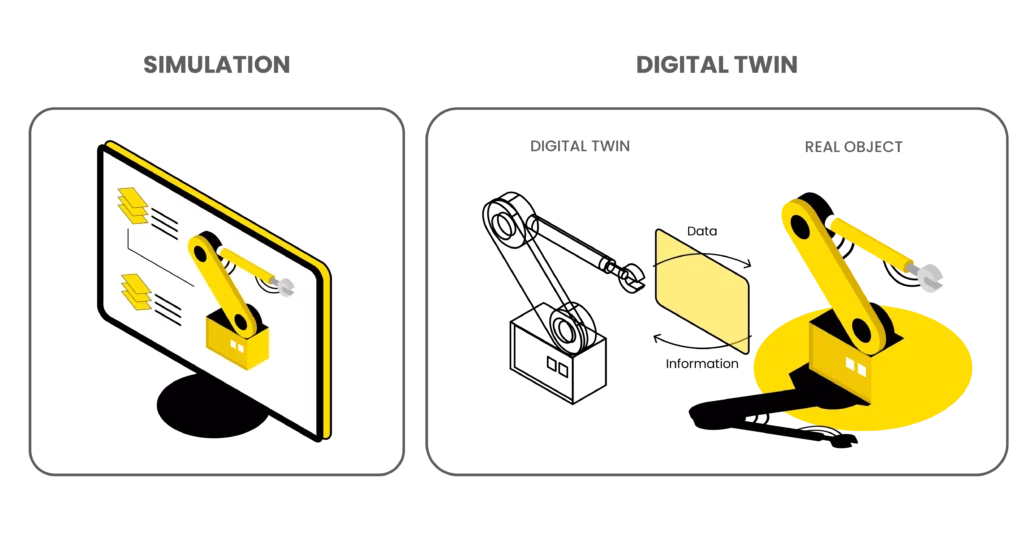
Simulation | Digital Twin |
---|---|
Simulation is designed with a CAD system or similar platform. | Digital twin application is built out of input from IoT sensors on real equipment |
It can be put through its simulated paces but may not have a one-to-one analog with a real physical object. | It replicates a real-world system and changes with that system over time in smart manufacturing. |
Simulations tend to be used during the design phase of a product’s lifecycle, trying to forecast how a future product will work. | Digital twin provides the business insight into how some product or system they’re using is working now |
Working of Digital Twin Technology
Digital Twin Technology collects and organizes all sorts of information, which includes manufacturing, physical, and operational data. This information is synthesized with the help of Artificial Intelligence analytics software and algorithms, which would result in the creation of a virtual mirror model of the physical system with the capabilities to analyze, evaluate, predict, and optimize data.
The Basic architecture of Digital twin Technology comprises four elements:
- The physical systems for which a Digital Twin will be created.
- The IoT sensors to collect and transmit the data.
- The virtual model that mirrors the real-world physical system.
- Software that monitors and profoundly analyzes data.
Steps involved in the creation of digital twin
- Physical to Digital data conversion: Sensors connected to the physical system capture all the sort data from the physical assets and convert it into digital data.
- Digital to Digital Data conversion: The twin technologies utilize advanced analytics, Artificial Intelligence, and scenario analysis to acquire and share information.
- Digital to Physical Data conversion: Algorithms in the Digital twin Technologies translate digital world decisions to data (in human-readable form) to spur-up action and change in the physical world or the real world.
Augmented Reality & Virtual Reality
While learning about Digital Twin Technology, we cannot skip the Augmented Reality and Virtual Reality technologies since they are the interface for human interactions.
Augmented Reality
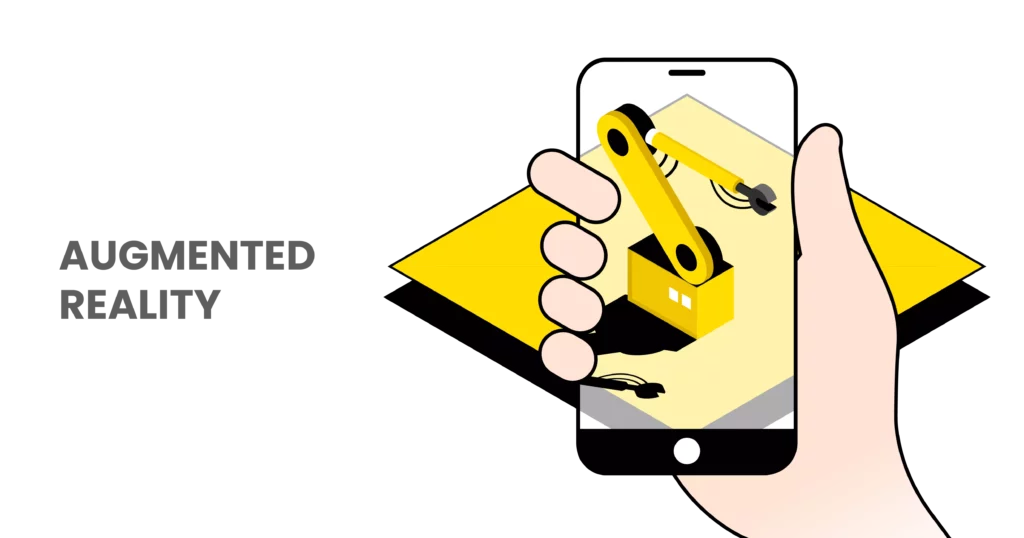
Augmented reality utilizes the existing real-world environment and puts the virtual data to enhance the user experience. It is a type of technology that allows digital images and information to be displayed in the physical world.
Example: In Pokémon Go, users search for the animated character that pops up on their phone in their real-life neighborhoods.
Virtual Reality
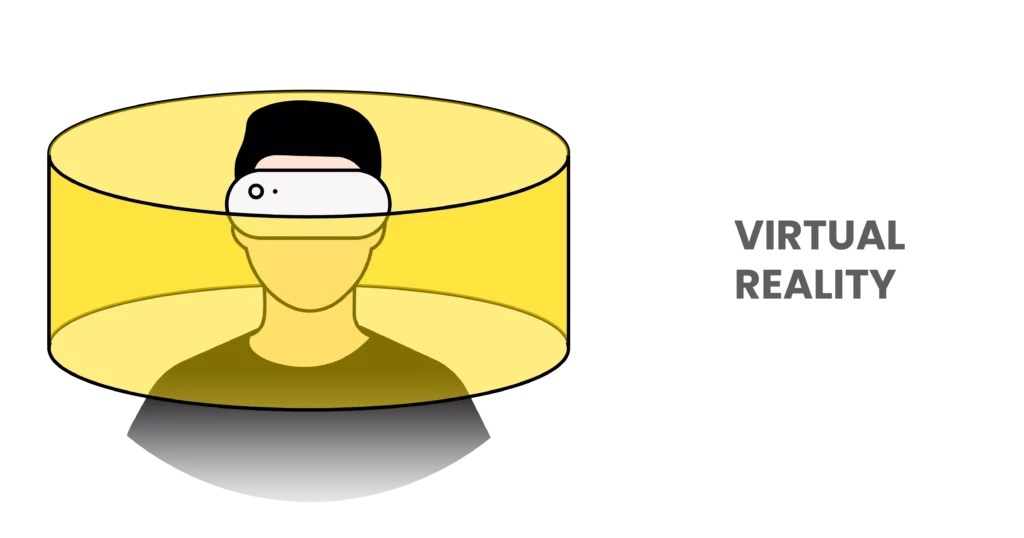
Virtual Reality or VR is a computer modeling and simulation that enables a person to interact with an artificial 3D visual or sensory environment. Virtual reality immerses the users in an animated scene. It replaces the real-life environment with a simulated one.
Example: Through a virtual reality headset, a person can walk around Italy as if they were present there.
What are benefits of Digital Twin Technology in Manufacturing industry ?
The level of benefits created by digital twin in manufacturing industry is depending on the use cases and how digital twin technology leveraged at the factory setup.
The following are some of key benefits identified in general:
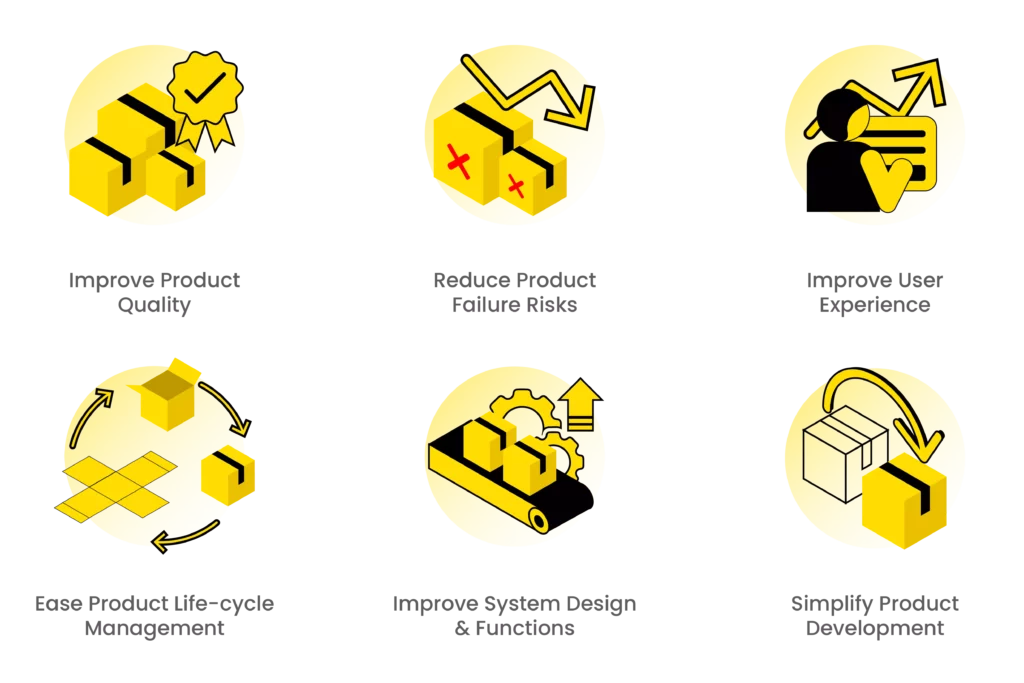
Improves the product quality
The Internet of Things (IoT) sensors attached to the physical asset generate real-time data, which can be accessed by the business to analyze and identify problems within their system. The asset generated data can be used to digitally simulate the asset performance and behavior to identify the predictable results. This approach enables organizations to improve production efficiency and reduce maintenance, which gradually will enhance the product quality with Digital Twin Technology.
Predicting product failures and Accelerate risk assessment
With the involvement of digital twins in the manufacturing industry, the system issues and the areas that require optimization can be known beforehand. The Digital Twin Technology enables organizations to determine the exact product test routine before manufacturing. It allows the operators to monitor the state of each physical asset, saving time and resources, and enables organizations to predict product failures and accelerate risk assessment.
Improves user experience
It is challenging to get a real-time, in-depth view of a physical system while it is in production. The real-time remote monitoring with Digital Twin Application improves user experience by virtually simulate it. As Digital Twin Technology can be accessed from anywhere, allowing users to monitor and control the system performance remotely. The all-time access to the system data enables the technicians to focus further on inter-team collaboration, which leads to enhanced operational efficiency.
Simplifying Product development
The Digital Twin Technology implemented in smart manufacturing facilitates testing and product engineering without building a prototype. The elimination of the physical prototype reduces development costs and time to market. The application of Digital Twin in manufacturing companies has proved to be beneficial. Digital twin technology can provide a virtual digital replica of upcoming products that simplifies product development.
Improved System Design
Digital twin application in smart manufacturing utilizes twin technology to plan and test new product lines. It uncovers the potential system issue even before creating the physical system. The advanced visualization technology involved with Digital Twin Technology helps organizations to identify system issues more accurately. Digital Twin Technology in the manufacturing system reduces the risk of miscalculation.
Asset lifecycle management
Utilizing Digital Twin Technology to analyze manufacturing data in smart manufacturing helps organizations manage the asset lifecycle. Augmented reality (AR) programs can help maintenance technicians to manage systems precisely. The AR glass helps them to view the updated models of the systems or machines.
Things to be considered before implementing Digital Twin Technology:
- Identify the purpose of Digital Twin implementation
- Update data security protocol
- Be aware of the purpose of implementing Digital Twin technology
- Keep an eye on data quality
- Train your team
- Involve the entire product value chain
Conclusion
Digital Twin Technology utilizes real-world data to illustrate simulation, which can help an organization foresee the working of a product or process. The application of digital Twin in manufacturing enhances the functional objectives of the manufacturing systems. It integrates technologies like the internet of things (Industry 4.0), artificial Intelligence, Software analytics, and many more. Digital Twin Technology drives innovation and enables organizations to merge the physical and digital environment to gain deeper visibility into their product.