In today’s fast-paced manufacturing environment, efficiency, quality, waste reduction, and continuous improvement are essential for maintaining a competitive edge. The A3 problem-solving methodology, rooted in Lean manufacturing principles, offers a structured, visual approach to addressing complex problems. This methodology goes beyond fixing problems. It encourages collaborative thinking, root-cause analysis, and alignment with business objectives.
Developed by Toyota, the A3 methodology takes its name from the international paper size (11×17 inches) used to document the process. However, its significance lies in its power to drive continuous improvement, enhance collaboration, and promote a problem-solving culture throughout the organization. It emphasizes clarity, accountability, and actionable outcomes, making it a valuable resource for manufacturers looking to enhance productivity, reduce waste, and optimize operations.
Whether dealing with production bottlenecks, quality issues, or workforce challenges, A3 root cause analysis provides a strategic approach to addressing problems while promoting learning and growth across the organization. In this blog, we’ll explore the core concepts behind A3 problem solving, how it applies to the manufacturing industry, and how manufacturers can use this methodology to solve problems efficiently and sustainably.
What is A3 Problem Solving?
One of the questions manufacturers regularly ask is what is A3 thinking. It is more than just a tool—it’s a mindset. It encourages problem solvers to think critically, dive into the root causes of problems, and develop effective, sustainable solutions. Unlike other methodologies focusing on quick fixes, A3 prioritizes long-term improvement. It aligns with Lean Manufacturing’s goal of eliminating waste and creating more customer value.
The A3 report is a single-page document that tells the story of the problem-solving process. A3 problem solving is a roadmap that guides teams through identifying the problem, analyzing the root cause, brainstorming solutions, implementing countermeasures, and monitoring results. The power of A3 methodology lies in its simplicity and visual clarity, making it easy to communicate complex issues and solutions across teams.
Why A3 Problem Solving Is Essential for Manufacturing
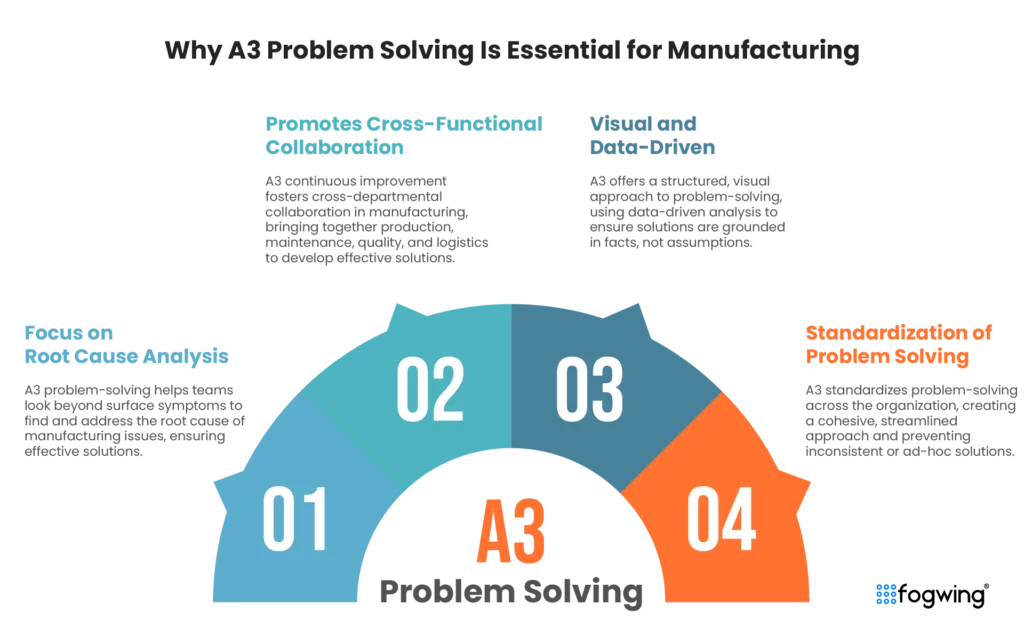
In manufacturing, small inefficiencies can lead to significant losses. Whether it’s equipment breakdowns, quality defects, or bottlenecks in production, the A3 root cause analysis approach offers a clear path to eliminating these issues at their root. Here are some key reasons why A3 is essential in manufacturing:
Focus on Root Cause Analysis:
Manufacturing problems often have deep-seated causes that are not immediately visible. A3 problem-solving forces teams to look beyond surface-level symptoms and identify the root cause of an issue, ensuring the problem is solved effectively.
Promotes Cross-Functional Collaboration:
Manufacturing challenges often span multiple departments, including production, maintenance, quality, and logistics. A3 continuous improvement encourages team collaboration, ensuring everyone contributes to the solution.
Visual and Data-Driven:
A3 provides a structured, visual format for documenting and solving problems. The reliance on data-driven analysis ensures that solutions are based on facts rather than assumptions or guesswork.
Standardization of Problem Solving:
By using a consistent approach across the organization, A3 helps standardize how problems are solved. A3 methodology creates a more cohesive, streamlined method for addressing issues, preventing inconsistent or ad-hoc problem-solving practices.
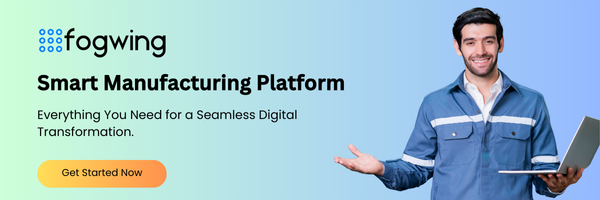
The A3 Problem-Solving Process in Manufacturing
The problem-solving process typically consists of seven steps, each building upon the previous one to create a clear problem-solving pathway. Let’s take a deeper look at each step and its application in manufacturing:
1. Identify the Problem (Problem Statement)
The first step in a3 process improvement is clearly and concisely defining the problem. In manufacturing, this could range from high defect rates, excessive downtime, production delays, or supply chain disruptions. The key here is to avoid vague language and focus on quantifiable problems. For example, rather than stating, “We have too many defects,” you would define the problem as “Defect rate for Product X has increased by 25% over the last three months, causing customer dissatisfaction.” A well-defined problem statement sets the stage for the entire process, ensuring all team members understand the scope and the importance of resolving the issue.
2. Understand the Current State
In A3 problem solving, it’s crucial to understand the current state of the process or system in which the problem occurs before jumping to solutions. It involves collecting data, observing the manufacturing process, and speaking with operators or other stakeholders who interact with the process daily. In this step of the a3 methodology, tools such as process flowcharts, value stream mapping, or Gemba walks (where teams observe work on the factory floor) help identify where inefficiencies or waste may occur. For example, in a machining process, you might discover that machine setup times are much longer than expected due to inefficient tool management, contributing to production delays.
3. Perform Root Cause Analysis
Root cause analysis is perhaps the most critical step in A3 problem-solving. Many manufacturing problems are symptoms of deeper issues, so digging deeper is essential to find the cause. Standard tools used in a3 root cause analysis include:
- The 5 Whys: A simple but powerful technique where the team asks “why” five times (or more) to drill down into the underlying cause of the problem.
- Fishbone Diagram (Ishikawa): A visual tool that helps categorize potential causes of a problem, typically examining factors like people, machines, methods, materials, and the environment.
For example, if the root cause of increased defects is improper machine calibration, asking “why” several times might reveal that there is no standard operating procedure (SOP) for calibration or that operators are not receiving regular training on calibration procedures.
4. Develop Countermeasures
In A3 problem-solving, once the root cause is identified, the team can brainstorm countermeasures to eliminate it. In manufacturing a3 root cause analysis, countermeasures are typically practical, data-driven solutions designed to address the specific problem without causing further disruption to the production process. For example, suppose machine calibration was the root cause of defects. Countermeasures might include creating a standard operating procedure (SOP) for calibration, scheduling regular maintenance checks, or implementing operator training programs. It’s essential to evaluate potential solutions based on their feasibility, cost-effectiveness, and possible impact on production. The goal is to find a countermeasure that solves the problem and improves the overall process.
5. Implement the Solution
With a clear action plan for a3 problem solving, it’s time to implement the chosen countermeasures. The team needs to be precise when executing the solution. It may involve changing production schedules, retraining employees, updating standard work instructions, or adjusting machine settings in a manufacturing setting.
Assigning responsibilities and timelines is crucial to ensuring that everyone involved knows their role in implementing the solution. In this phase of the a3 methodology, change management techniques may also be helpful to ensure a smooth transition to the new processes.
6. Verify Results
After implementing the solution in A3 problem solving, the next step is to monitor and verify the results. Did the countermeasures work? In manufacturing, this typically involves tracking key performance indicators (KPIs) such as defect rates, machine downtime, or cycle times to ensure the problem has been resolved. Gathering feedback from operators and supervisors on the shop floor is essential to ensure the new process runs smoothly in the a3 methodology. Suppose the solution does not achieve the desired results. In that case, the team may need to revisit earlier steps to identify additional root causes or develop new countermeasures.
Common Manufacturing Challenges Addressed by A3 Problem Solving
A3 problem solving is versatile and can be applied to a wide range of manufacturing challenges, including:
- Reducing Machine Downtime: Frequent machine breakdowns or unplanned maintenance can cause significant production delays. A3 process improvement helps identify the root cause of downtime and implement preventive measures, such as improving maintenance schedules or upgrading equipment.
- Improving Product Quality: Quality defects can damage a company’s reputation and lead to costly rework or customer returns. A3 process improvement allows manufacturers to investigate the causes of defects, whether related to materials, processes, or human error.
- Optimizing Production Flow: Bottlenecks in the production process can slow down overall output. A3 problem-solving can help streamline workflows and eliminate waste by studying the current state and identifying inefficiencies.
- Enhancing Workplace Safety: Safety incidents are a significant concern in manufacturing. A3 helps identify hazards, implement corrective actions, and create safer working environments for employees.
A3 Problem Solving and CMMS software
A3 methodology can be valuable for maintenance teams using CMMS (Computerized Maintenance Management System) software. By using the A3 approach, maintenance teams can:
1. Identify and prioritize critical maintenance issues.
2. Conduct root cause analyses to prevent recurring problems.
3. Develop effective maintenance strategies and procedures.
4. Track progress and measure the effectiveness of maintenance activities.
5. Collaborate with other departments to improve overall plant performance.
CMMS software can provide the data and tools to support the A3 process, such as work order tracking, preventive maintenance scheduling, and performance metrics. By integrating the A3 methodology with CMMS, maintenance teams can optimize operations, reduce downtime, and improve overall plant reliability.
Example of A3 Thinking: A Manufacturing Problem
A manufacturing plant faced frequent equipment breakdowns, causing production delays and rising costs. The team adopted the A3 problem-solving approach to address this, documenting the issue using an A3 template. They outlined the problem, emphasizing how unplanned downtime disrupted delivery schedules and increased operational inefficiencies. Using root cause analysis, they discovered that poor preventive maintenance practices were the key contributor to these breakdowns.
The team then implemented a predictive maintenance strategy supported by Fogwing CMMS, which provided automated alerts for timely equipment servicing. It not only helped reduce breakdowns but also improved overall efficiency. The A3 template helped track progress and ensured that corrective actions were consistently followed. Through this structured A3 methodology, the plant could streamline operations, improve equipment reliability, and achieve its production targets, demonstrating the effectiveness of this problem-solving methodology in a real-world scenario.
The problem-solving A3 examples from the manufacturing sector illustrate the power of structured frameworks. By visually mapping out issues and collaborating across departments, teams can address root causes and drive lasting improvements. These efforts often lead to A3 continuous improvement projects that focus on optimizing operations and preventing future problems. Whether it’s reducing downtime or improving product quality, the A3 problem-solving approach provides a disciplined method for tackling challenges and fostering a culture of continuous improvement.
Conclusion
Adopting a structured methodology like A3 is essential for sustainable growth and efficiency in a highly competitive manufacturing landscape. This approach empowers manufacturers to tackle complex challenges through root-cause analysis, collaborative problem-solving, and data-driven decision-making. The structured methodology addresses root causes and promotes teamwork and data-driven solutions. By embracing A3 continuous improvement, manufacturers can turn challenges into opportunities, enhance product quality, and reduce waste. Ultimately, A3 problem-solving aligns processes with business goals, creating a sustainable framework for long-term success and enabling a culture of continuous learning and optimization across the organization.
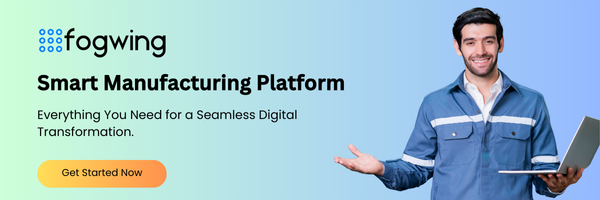
FAQs
1. What is A3 problem-solving in manufacturing, and why is it important?
A3 problem-solving is a Lean manufacturing methodology that helps teams identify, analyze, and resolve problems using a structured, visual one-page report. It’s essential because it promotes root cause analysis, cross-functional collaboration, and continuous improvement—resulting in reduced waste, improved product quality, and optimized operations.
2. How does the A3 process support root cause analysis in manufacturing?
The A3 process uses tools like the 5 Whys and Fishbone Diagram to uncover the root causes behind issues like equipment breakdowns or product defects. Instead of treating symptoms, A3 digs deep to eliminate problems at the source—ensuring long-term, sustainable solutions in production environments.
3. What are the key steps in A3 problem-solving methodology?
The Key steps in A3 problem-solving methodologies are
- Define the problem clearly
- Analyze the current state
- Perform root cause analysis
- Develop countermeasures
- Implement solutions
- Verify results
- Standardize improvements
This step-by-step approach ensures consistency and clarity in manufacturing problem resolution.
4. Can A3 problem-solving be integrated with CMMS software?
A3 works seamlessly with CMMS (Computerized Maintenance Management System) platforms. CMMS provides critical data like maintenance history, work order tracking, and asset performance, which supports each step of the A3 process and helps teams drive measurable improvements in reliability and plant performance.
5. What types of manufacturing challenges can A3 address?
A3 problem-solving can addresses
- Frequent equipment failures
- High defect rates
- Inefficient workflows or bottlenecks
- Workplace safety incidents
- Inconsistent maintenance practices
- It helps for fostering a culture of operational excellence and continuous improvement.