Are you tired of the constant setbacks caused by machine downtime? Well, you’re not alone! Whether you own a manufacturing facility or rely on machinery for your business operations, understanding the root causes of machine downtime is crucial to keeping things running smoothly. In this blog post, we’ll delve into the various factors that lead to malfunctioning machines and explore practical strategies to prevent such costly disruptions. By gaining insight into these issues, you’ll be armed with knowledge that will help maximize productivity and minimize those pesky downtimes. So, let’s get started on our journey towards uninterrupted efficiency!
Introduction to Machine Downtime
In the fast-paced world of industrial operations, machine downtime is a formidable adversary, capable of disrupting production schedules, decreasing efficiency, and incurring substantial financial losses. This comprehensive guide explains the root causes of machine downtime, its impact on businesses, and practical strategies to prevent it.
Machine downtime is any period during which a machine is not operational, whether planned or unplanned. While scheduled maintenance is necessary, unplanned downtime poses a more significant threat. Understanding the intricacies of downtime is crucial for implementing preventive measures and ensuring the uninterrupted flow of operations.
Common Causes of Machine Downtime
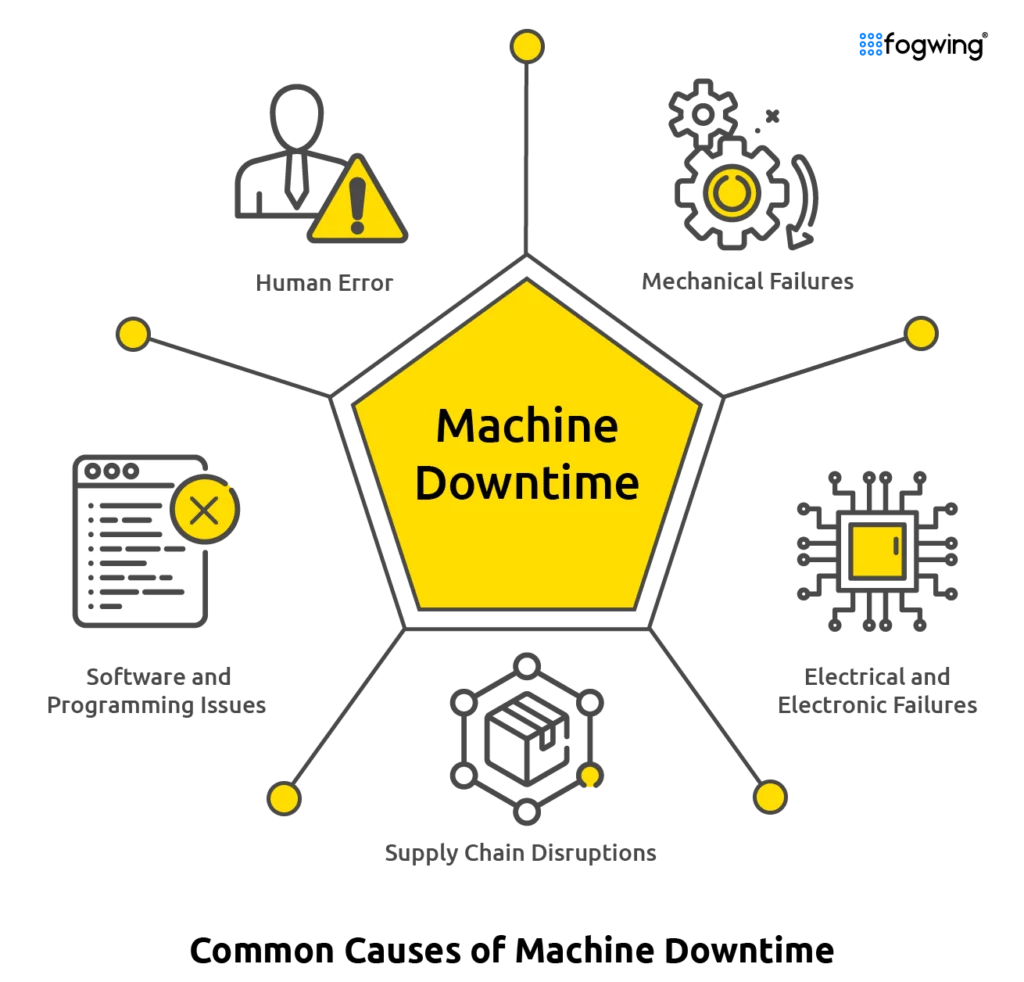
1. Mechanical Failures
Mechanical failures from equipment breakdowns, wear and tear, or component malfunctions primarily contribute to downtime. Regular maintenance, including lubrication, part replacement, and condition monitoring, is essential to prevent such failures.
2. Electrical and Electronic Failures
Issues with electrical components and electronic systems can lead to unexpected downtime. Regular inspections, electrical testing, and implementing preventive measures are critical to mitigating the risks related to electrical and electronic failures.
3. Human Error
Human factors, including operator errors, inadequate training, or insufficient skill levels, can significantly contribute to machine downtime. Investing in comprehensive training programs and creating a safety culture is vital in reducing human-related downtime.
4. Software and Programming Issues
Glitches, bugs, or programming errors in machine software can result in operational disruptions. Regular software updates, debugging processes, and thorough testing are essential to prevent software-related downtime.
5. Supply Chain Disruptions
External factors, such as delays in receiving necessary parts or disruptions in the supply chain, can lead to extended downtime. Managing and diversifying the supply chain is crucial in reducing the impact of external influences on machine availability.
Impact of Machine Downtime on Businesses
The consequences of machine downtime extend beyond the immediate disruption of operations. Financial implications include the direct costs of repairs, replacement parts, and labor and indirect costs like lost production, damaged customer relationships, and harm to a company’s reputation.
The impact on businesses goes beyond the financial realm; it can affect employee morale, customer trust, and overall competitiveness in the market. Recognizing these implications underscores the importance of proactive measures to prevent and minimize downtime.
Ways to Prevent Mechanical Failure
1. Predictive Maintenance
Implementing a predictive maintenance program allows businesses to anticipate and address potential mechanical failures before they occur. Monitoring machine health through sensors and data analytics can identify and resolve issues proactively, reducing the risk of unplanned downtime.
2. Regular Inspections and Audits
Routine inspections and audits are crucial in identifying potential issues and maintaining optimal machine performance. Establishing a comprehensive inspection schedule and keeping detailed audit records facilitate timely intervention and prevent machine downtime.
Importance of Proper Training and Human Error Prevention Strategies
In minimizing machine downtime, the significance of proper training and human error prevention cannot be overstated. These elements are pivotal in creating a resilient operational environment. Let’s explore their compact yet critical roles:
1. Operator Training
Investing in comprehensive training for machine operators is a linchpin in reducing human-related downtime. Well-trained operators are equipped to handle machinery efficiently, minimizing errors and contributing to a safer working environment. A skilled workforce can identify potential issues early, fostering a proactive approach to preventing disruptions.
2. Human Error Prevention Strategies
Beyond training, implementing targeted human error prevention strategies is essential. This involves creating standardized operating procedures, conducting regular safety drills, cultivating a workplace culture, prioritizing attention to detail, and adhering to protocols. Proactive measures significantly diminish the likelihood of errors that could lead to machine downtime.
In essence, proper training and human error prevention strategies serve as foundational pillars for a resilient workforce, reducing the risk of disruptions and contributing to a culture of continuous improvement.
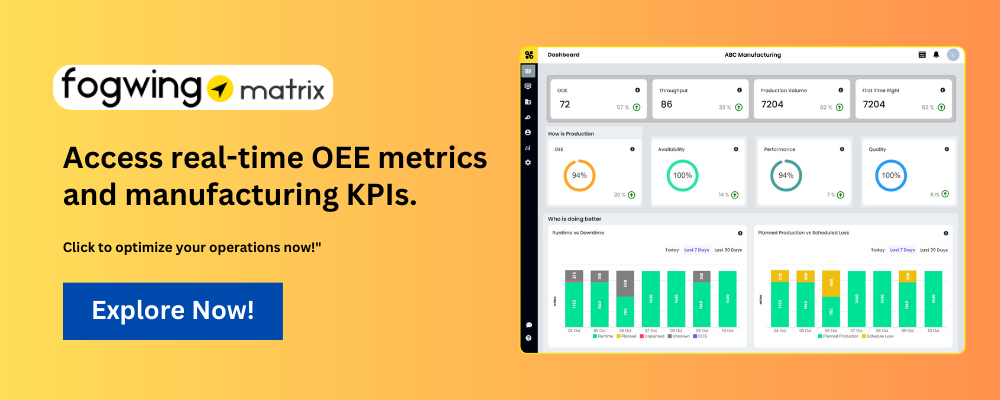
Utilizing Technologies for Reducing Machine Downtime
In the quest for minimizing machine downtime, the integration of cutting-edge technologies emerges as a game-changing strategy. Technological advancements offer a proactive approach to maintenance, real-time monitoring, and predictive analytics, empowering businesses to stay one step ahead of potential issues. This section will delve into various technologies instrumental in reducing machine downtime.
1. Internet of Things (IoT) Sensors
The Internet of Things (IoT) has revolutionized the industrial landscape by enabling machines to communicate, share data, and provide insights in real-time. IoT sensors play a pivotal role in monitoring the health and performance of machinery. These sensors collect data on temperature, vibration, energy consumption, and other critical parameters, allowing for predictive maintenance.
Implementing a network of IoT sensors on machinery enables continuous monitoring. Anomalies or deviations from normal operating conditions trigger alerts, allowing maintenance teams to intervene before a breakdown occurs. This proactive approach minimizes downtime, as potential issues are addressed during their early stages.
2. Predictive Maintenance Software
Predictive maintenance software leverages machine learning algorithms and historical data to predict when equipment will likely fail. By analyzing patterns and trends, these systems provide actionable insights into the condition of machinery. Predictive maintenance takes the guesswork out of maintenance scheduling, allowing organizations to perform maintenance activities precisely when needed.
This software considers various factors, such as equipment usage, environmental conditions, and historical failure data. By forecasting maintenance needs, businesses can plan downtime during periods of low demand, optimizing overall operational efficiency.
3. Automation and Robotics
Integrating automation and robotics enhances the efficiency of manufacturing processes and contributes significantly to reducing machine downtime. Automated systems can perform routine maintenance tasks, inspections, and repairs without human intervention.
Robotic systems with advanced sensors can navigate intricate machinery, detect anomalies, and perform corrective actions. The result is a reduction in the frequency and duration of manual maintenance tasks, leading to increased overall machine availability.
4. Machine Learning and Artificial Intelligence (AI)
Machine learning algorithms and AI applications excel in analyzing large amounts of data to identify patterns and anomalies. In reducing machine downtime, these technologies can predict when equipment will likely fail based on historical data and real-time inputs.
Machine learning algorithms become more accurate in predicting potential issues over time by continuously learning from new data. This enables organizations to adopt a preventive rather than reactive maintenance approach, minimizing unplanned downtime.
5. Cloud Computing for Data Storage and Analysis
Cloud computing is crucial in handling the massive volumes of data generated by IoT sensors, predictive maintenance software, and other technologies. Cloud platforms provide scalable and cost-effective solutions for storing, processing, and analyzing data in real-time.
Cloud-based analytics allow businesses to derive meaningful insights from their machine data, facilitating informed decision-making. Accessing data remotely also streamlines collaboration among maintenance teams, enabling them to work together seamlessly and respond promptly to emerging issues.
Is 100% Availability Possible with Technology?
While integrating these technologies significantly reduces machine downtime, achieving 100% machine availability remains a lofty goal. Factors such as the inherent complexity of machinery, external environmental influences, and the occasional unpredictability of inevitable failures make absolute availability challenging.
However, the combination of advanced technologies, predictive maintenance strategies, and a proactive approach to addressing issues comes remarkably close to optimizing machine availability. The goal shifts from perfection to continuous improvement and adaptation to emerging technologies.
How Fogwing Matrix helps in Preventing Machine Downtime?
Fogwing Matrix Machine Monitoring solution plays a crucial role in reducing machine downtime by providing real-time data on the health and performance of industrial machines. Seamlessly integrating IoT sensors, data analytics, and real-time insights enables manufacturers to prevent unplanned downtimes. Here are several ways in which Fogwing Matrix contributes to minimizing downtime:
Downtime Trends and Pareto Analysis
Fogwing Matrix downtime Pareto analysis guides strategic decision-making optimizes resource allocation, and minimizes downtime, contributing to a more resilient and high-performing production operation.
Preventing Maintenance Capabilities
Fogwing Matrix’s preventive maintenance capabilities anticipate equipment failures, allowing timely repairs, preventing unexpected breakdowns, and minimizing unscheduled machine downtime.
Condition Monitoring:
Fogwing Matix and its real-time data collection feature continuously collects data from sensors attached to the machines, monitoring parameters such as temperature, vibration, and pressure. The software can identify abnormal patterns or deviations from normal operating conditions by analyzing the collected data, allowing maintenance teams to address potential issues before unplanned downtime occurs.
OEE Monitoring:
The Fogwing Matrix tracks key performance indicators (KPIs) such as OEE (Overall Equipment Efficiency) to assess the overall effectiveness of equipment or machines. Identifying and addressing factors that impact efficiency can reduce machine downtime.
To learn more about OEE Monitoring, read The Role of OEE in Total Quality Management
Conclusion:
As industries evolve and technologies continue to advance, the landscape of machine maintenance will undergo further transformations. The key lies in embracing these changes, staying informed about emerging technologies, and fostering a culture of innovation that prioritizes the reduction of downtime as a critical business objective. By doing so, businesses can position themselves at the forefront of efficiency, reliability, and sustained success. The commitment to minimizing machine downtime remains a cornerstone of sustainable and successful operations.
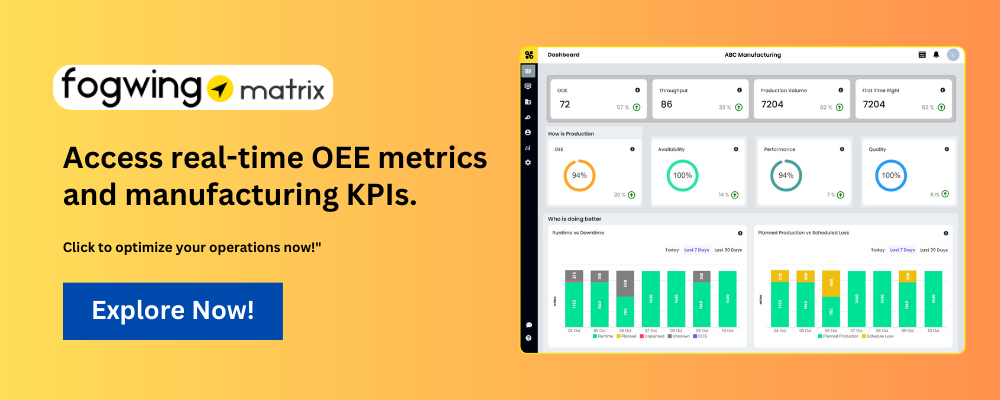