Manufacturers must constantly monitor and measure their performance in the fast-paced and competitive manufacturing world. Key Performance Indicators (KPIs) provide valuable insights into a manufacturing operation’s efficiency, productivity, and overall performance. By monitoring these manufacturing KPIs, businesses can identify areas for improvement, make data-driven decisions, and strive for continuous improvement. This blog post will discuss some key manufacturing KPIs every manufacturer should monitor.
Introduction to Key Performance Indicators (KPIs) in Manufacturing
Key Performance Indicators (KPIs) in manufacturing are measurable metrics that help evaluate the performance and effectiveness of manufacturing processes, operations, and overall business goals. These indicators provide insights into different aspects of the manufacturing process, such as efficiency, productivity, quality, cost, and customer satisfaction.
By consistently monitoring the KPIs, manufacturers can strive for continuous improvement, enhance productivity, optimize processes, and ultimately achieve long-term success in a highly competitive industry.
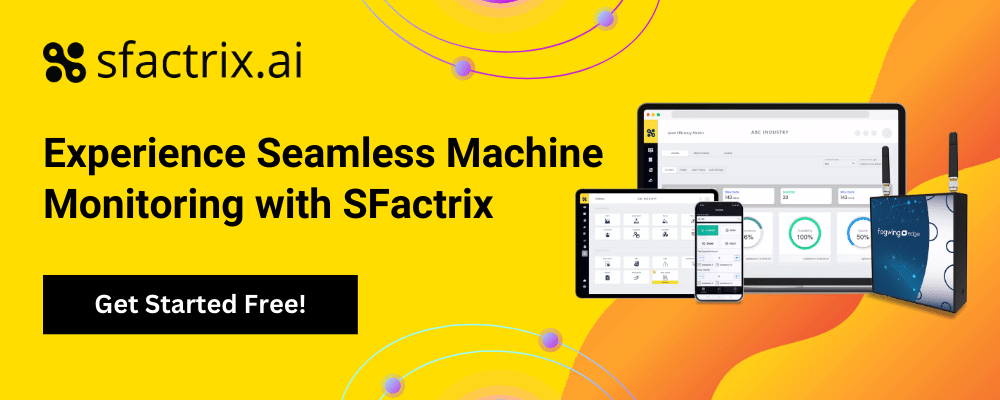
A Few Important Manufacturing KPIs?
In the intricate tapestry of manufacturing, KPIs are the threads that interconnect various aspects of operations. While specific KPIs may vary based on industry nuances, strategic goals, and operational processes, several important KPIs universally stand out as paramount:
Overall Equipment Efficiency (OEE): It is one of the multifaceted manufacturing KPIs that gauges the utilization of equipment and resources across production processes, encompassing dimensions like availability, performance, and quality. OEE offers a panoramic view of manufacturing efficiency. OEE is calculated as,
OEE Percentage: (Total Production Time – Downtime) / Total Production Time
Example: Let’s say you’re monitoring the performance of a factory machine over 24 hours.
- Total Production Time: 24 hours
- Downtime: 2 hours (the machine was not operating due to maintenance or other issues)
Now, plug these values into the formula:
OEE Percentage = (24 hours – 2 hours) / 24 hours
OEE % = 22 hours / 24 hours
OEE % = 0.9167 (rounded to four decimal places)
To express in percentage, multiply by 100.
OEE %= 0.9167 x 100
OEE % = 91.67%
In this example, the machine’s Overall Equipment Efficiency (OEE) for those 24 hours is approximately 91.67%. It means that the machine was operational and producing products for about 91.67% of the total time, considering the 2 hours of downtime.
To learn more about how to improve OEE, read this, 5 Ways To Improve OEE In Manufacturing Operations | Fogwing.io
Throughput is one of the most essential manufacturing KPIs that measures how much product a manufacturing process can produce in a given period. A high throughput indicates that the manufacturing process is efficient and can produce large product quantities. Throughput can be calculated as,
Throughput = Inventory (the number of units in the production process)/ F = The time the inventory units spend in production from start to finish.
SFactrix machine monitoring system simplifies and automates the ‘Throughput’ measurement at its dashboard level. It indicates production efficiency and helps the process calculate further manufacturing KPIs.
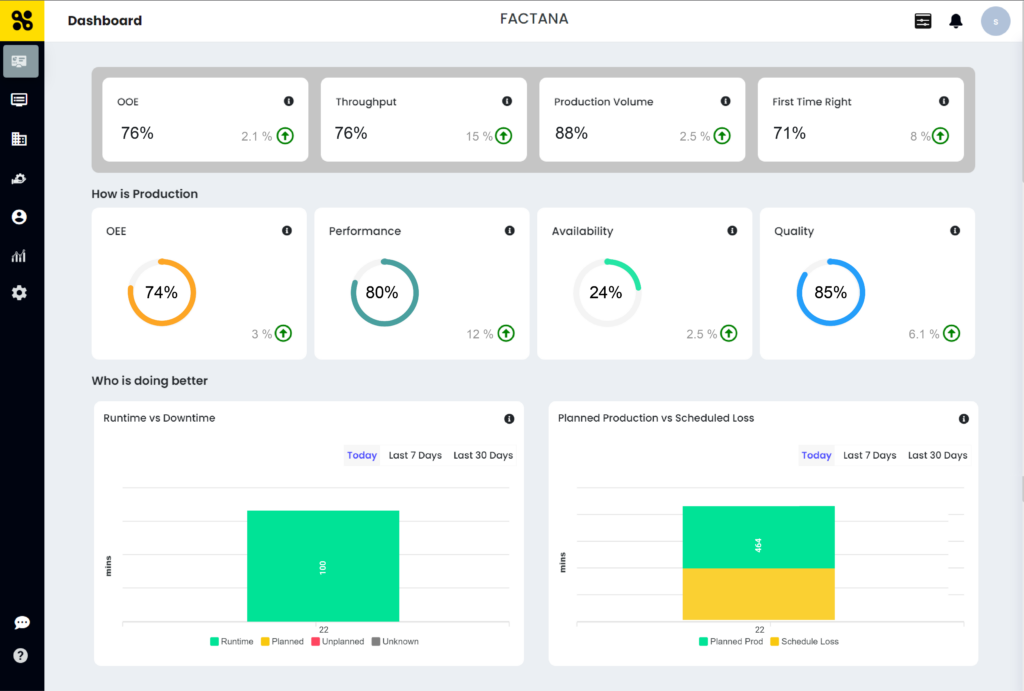
In the context of manufacturing KPIs, scrap rate measures how much material is wasted during the manufacturing process. A low scrap rate indicates that the manufacturing process is efficient and that little material is wasted. The scrap rate is calculated as,
Scrap Rate = Unusable Units / Total Units Produced
Example:
Suppose you are managing a production line in a factory, and during a production run, you encounter some defects. This is how you will measure the scrap rate,
Unusable Units: 50 units (defective or rejected units during production)
Total Units Produced: 1000 units
Now, plug these values into the formula:
Scrap Rate = 50 units / 1000 units
Scrap Rate = 0.05
To express this in percentage, multiply by 100:
Scrap Rate = 0.05 X 100
Scrap Rate = 5%
So, in this example, the scrap rate for the production run is 5%, i.e., Among the 1000 units produced, 50 were defective and deemed unusable, accounting for 5% of the total production.
Quality Production: At the core of manufacturing lies the pursuit of quality. Quality Production, one of the significantmanufacturing KPIs, quantifies the proportion of flawless products emerging from the production line, providing a tangible measure of quality control effectiveness. Quality production can be calculated as,
Quality products: (Number of Defect-Free Products / Total Products Produced) * 100
Example:
Suppose you monitor a production process and want to determine the proportion of quality products produced during a manufacturing run.
Number of Defect-Free Products: 850 units
Total Products Produced: 1000 units
Now, plug these values into the formula:
Quality Products = 850 units / 1000 units
Quality Products = 0.85
This manufacturing KPI shows the proportion of quality products produced during the manufacturing run is 0.85. This means that out of the total 1000 units produced, 850 units were defect-free and considered high quality, accounting for 0.85 or 85% (0.85×100) of the total production in proportion.
Inventory Turnover: A high turnover rate among all the manufacturing KPIs signifies streamlined processes and economic advantages. For example, if you calculate the inventory turnover for a business over a specific period. It can be estimated as,
Total Cost of Goods Sold / Average Inventory Value = Inventory Turnover
Example:
Total Cost of Goods Sold (COGS) for the period: $400,000
Average Inventory Value for the same period: $100,000
Inventory Turnover = $400,000 / $100,000
Inventory Turnover = 4
So, in this example, the Inventory Turnover for the specified period is 4. This is one of the crucial manufacturing KPIs that shows that the company sold and replaced its entire inventory four times during that period. It measures how efficiently inventory is managed and turned into sales.
Downtime: The bane of productivity, downtime indicates periods when production halts due to equipment malfunctions, maintenance, or unforeseen events. Minimizing downtime is the focal point of enhancing overall productivity. Suppose you want to calculate the downtime percentage for a manufacturing process during a specific period. Downtime percentage can be calculated as,
Downtime Percentage: (Downtime / Total Production Time) * 100
Downtime during the period: 2 hours
Total Production Time for the same period: 24 hours
Downtime %= (2 hours / 24 hours) x 100
Downtime %= (1/12) x 100
Downtime Percentage = 8.33%
So, the downtime percentage for the specified period is approximately 8.33%. This means that downtime accounted for about 8.33% of the total production time.
Production volume: Unlike other manufacturing KPIs, this indicates the overall health of your manufacturing operation. It tells you how much product you can produce and can be an excellent early warning sign of potential problems. Your production process is three times safer with a connected system in place to measure the production volume in real-time.
SFactrix production monitoring powered with IoT connectivity empowers your production unit and automates all the essential KPIs measurement. Harness the power of the Internet of Things (IoT), sensors, and interconnected systems to harvest real-time data on production volume, production efficiency, and other pivotal metrics.
What is the KPI in Quality Control?
Quality control means that every product that needs to be corrected the first time gets withdrawn from the process. Key performance indicators, or KPIs, are fundamental to quality management. KPI is a measurable value or metric used to assess the performance and effectiveness of quality control processes within an organization. Manufacturing KPIs provide objective evidence of whether quality control objectives are being achieved, help monitor progress, and identify areas for improvement. Key production KPIs in quality control encompass:
First Pass Yield (FPY) is an index of the proportion of products triumphantly passing quality assessments during their initial evaluation, reflecting the efficacy of quality control mechanisms.
Defects Per Million Opportunities (DPMO) is a metric quantifying the prevalence of defects in a process relative to the total opportunities for defects. DPMO quantifies quality issues, serving as a launchpad for enhancement endeavors.
How do you Measure Manufacturing KPIs?
Measuring Manufacturing Key Performance Indicators (KPIs) involves a systematic approach to collecting, analyzing, and interpreting relevant data to assess the performance and effectiveness of various aspects of the manufacturing process. Here’s a step-by-step guide on how to measure and monitor KPIs:
Define Your KPIs: Clearly define the specific KPIs you want to measure. Each KPI should be aligned with your manufacturing goals and objectives. For example, if you focus on production efficiency, your KPI might be ‘Overall Equipment Efficiency (OEE).’
Identify Data Sources: Determine where and how you will collect the necessary data to measure your manufacturing KPIs. Data sources include sensors, equipment logs, production records, quality control reports, and other relevant sources.
Data Collection: Collect accurate and consistent data from the identified sources. This process may involve manual data entry, automated data collection systems, or manufacturing software and systems integration.
Data Processing: Clean and organize the collected data. This process may involve removing outliers, correcting errors, and transforming data into a defined format for analysis.
Calculation: Calculate the manufacturing KPIs based on the collected and processed data. Use the predefined formulas or measures associated with each KPI. For instance, you would need data on downtime, production time, and quality yield to calculate OEE.
Normalization: In some cases, it’s important to normalize the data to account for variations in factors like production volume, periods, or different production lines. Normalization helps ensure fair comparisons and accurate insights.
Data Analysis: Analyze the calculated KPI values to gain insights into your manufacturing performance. Compare current KPI values to historical data, industry benchmarks, or established targets to assess performance trends and areas for improvement.
Visualization: Present the KPI data visually using graphs, charts, and dashboards. Visualizations make it easier to comprehend and communicate the insights derived from the data.
Interpretation: Interpret the results of your analysis. Identify trends, patterns, and anomalies that indicate areas of strength or need attention through manufacturing KPIs.
Continuous Improvement: Use the insights from your KPI measurements to make informed decisions and implement changes to improve manufacturing processes. Regularly review and update your KPIs based on changing goals and priorities.
Feedback Loop: Establish a feedback loop where you continuously monitor, measure, analyze, and adjust your manufacturing processes based on KPI monitoring data. This iterative process drives ongoing improvement and optimization.
Types of Data Analysis for a Manufacturer’s KPI Dashboard
Data analysis consists of evaluating, cleansing, transforming, and modeling data to discover helpful information, suggest conclusions, and support decision-making. Data mining is a method used to analyze data, with the primary objective of uncovering patterns and gaining insights to make predictions and not just describe the data.
A manufacturing KPIs dashboard should include both types of data analysis to provide the most comprehensive picture of performance. The KPIs monitored will vary from organization to organization. Still, some common ones include production costs, quality KPIs, delivery times, scrap rates, and safety incidents.
Manufacturing is a complex process with multiple moving parts, so it’s essential to have a robust data analysis strategy to identify issues and opportunities for improvement. The right mix of KPIs will give you a clear picture of how your operation is performing and where there is room for improvement.
Best Practices for KPI Monitoring
To optimize the effectiveness of monitoring manufacturing KPIs, it is essential to follow these best practices:
- Align KPIs with the overall manufacturing goals to ensure a coordinated effort toward achieving objectives.
- Keep the manufacturing KPIs simple and focused, allowing stakeholders to gain valuable insights.
- Conduct regular reviews of the KPIs to stay proactive in addressing issues and taking advantage of proper decision-making.
- Engage relevant stakeholders in the KPI monitoring process to encourage collaboration and make informed decisions.
Monitor your manufacturing KPIs with SFactrix.
SFactrix machine monitoring enables you to monitor your machine data most accurately and efficiently. SFactrix machine monitoring system automatically captures and analyzes all your factory machine data as well as production data and presents a comprehensive overview of manufacturing KPIs or key performance indicators at the dashboard level in real-time.
SFactrix machine monitoring system enables manufacturers to connect their machines to the software via IoT connectivity and monitor various key performance indicators of the machines.
SFactrix helps manufacturers optimize their factory assets’ performance and efficiency in various ways. The following are a few benefits of the SFactrix machine monitoring system.
- It ensures the factory machines run smoothly and efficiently by monitoring their performance and detecting downtime or availability.
- It provides real-time visibility of production operations by automatically capturing machine data.
- It provides real-time data on the machine’s availability and performance, improving its overall performance and efficiency.
- It offers an optimized dashboard with a comprehensive view of several manufacturing KPIs, such as Overall Equipment Efficiency or OEE monitoring, quality production, rejection count, cycle time, and more.
- SFactrix presents OOE (Overall Operations Effectiveness) monitoring as a powerful manufacturing KPI. OOE assesses the effectiveness of operations throughout a shift, irrespective of whether the allocated time was intended for job execution.
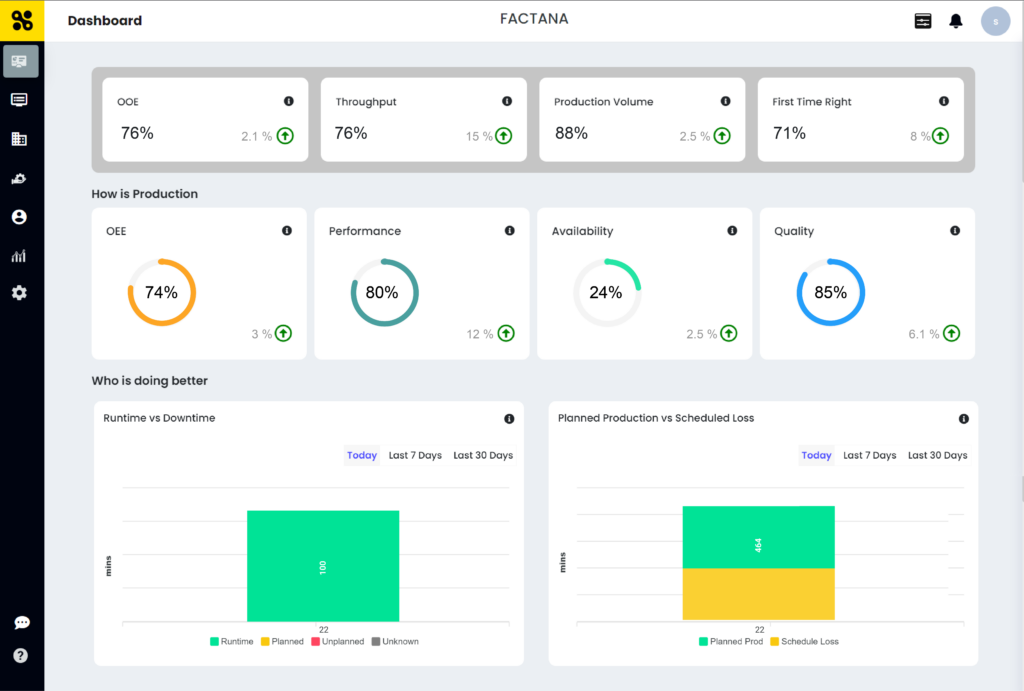
Businesses can effectively monitor their manufacturing KPIs using SFactrix machine monitoring software, improving efficiency, productivity, and overall performance in their manufacturing operations. Read this guide to learn more about how SFactrix machine monitoring provides a comprehensive and accurate visualization of your production metrics. Machine Condition Monitoring | Fogwing Platform.
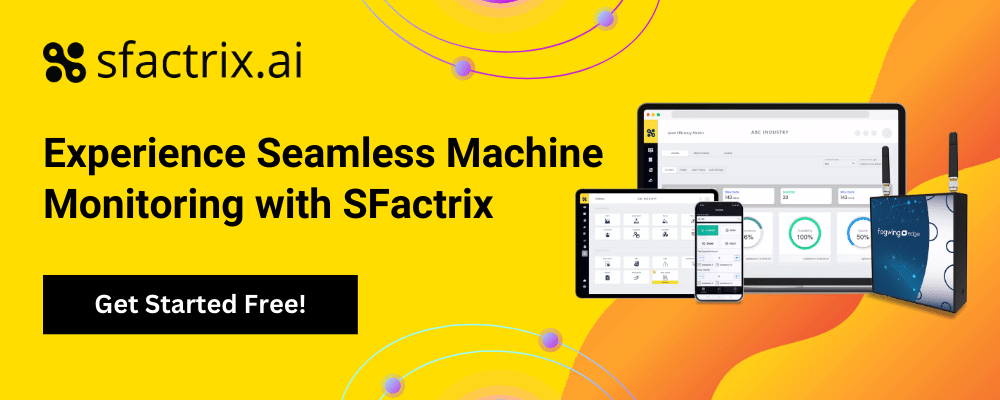
Conclusion
Manufacturing KPIs are essential tools for measuring the performance of a manufacturing business. By monitoring key indicators such as production throughput, quality assurance, efficiency, and cost control, manufacturers can identify areas that need improvement to increase their profitability and overall competitiveness. With the correct data, manufacturers can make informed decisions about optimizing their operations to meet customer demands while controlling costs.