Industries use Overall Equipment Effectiveness (OEE) as a performance indicator for evaluating efficiency and productivity. OEE is the critical metric for measuring and identifying the total percentage of productive manufacturing time, which include machine and operator performances. OEE focuses on the entire manufacturing shop floor, measuring equipment availability and production quality against machine availability.
OEE metric is a crucial tool for benchmarking progress in improving manufacturing productivity. OEE in manufacturing is a key performance indicator (KPI) that compares the manufacturing system’s ideal performance to its actual performance in terms of production. This blog will give a walkthrough on OEE calculations and how to improve the OEE for better efficiency.
How to calculate OEE in manufacturing?
Overall Equipment Effectiveness is a quantifiable method to figure out how well your equipment, people, and processes perform by measuring the three factors:
- Availability.
- Performance.
- Quality.
Hence, calculate OEE by multiplying equipment availability, performance, and quality. Here is the OEE calculation mentioned below.
OEE = Availability x Performance x Quality
For example, if the availability is 90%, performance is 85%, and quality is 95%, the OEE would be calculated as follows:
OEE = 90% x 85% x 95% = 72.67%
Therefore, the overall equipment effectiveness of the production process is 72.67%.
Check how to determine Availability, Performance, and Quality and know the OEE calculations more elaborately here. How To Calculate OEE Of Machine | Fogwing Industrial Cloud SFactrix.ai Solution
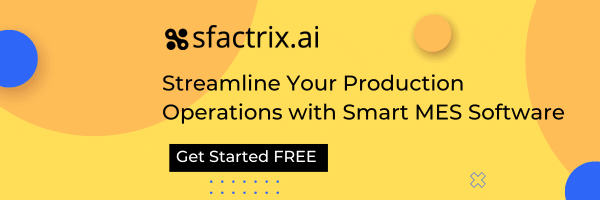
Benefits of improving OEE in manufacturing operations:
Monitoring Overall equipment effectiveness (OEE) has proven to improve availability, performance rate, and quality production while reducing unplanned downtime and wastage from the equipment. Tracking OEE metrics is beneficial for a manufacturing organization to analyze all aspects of asset performance to ensure they obtain the maximum benefit from a piece of equipment already paid for.
The implementation of OEE monitoring is automated through an IoT system for analyzing production data to identify potential areas of improvement and support lean initiatives. Therefore, OEE typically advances from a base measure for efficiency as the initial purpose to tool to improve the overall effectiveness of the entire production.
Listed below are the top benefits of OEE implementation in manufacturing:
- Improve productivity.
- Reduce downtime and enhanced availability.
- Improve the quality of finished goods.
- On-time delivery.
- Reduce operational expenditure.
- Higher ROI.
What are the 5 Ways to Improve OEE?
Improving the OEE is imperative to manufacturing efficiency. To achieve this, manufacturers should have access to accurate and real-time production data from machines. Improving the OEE helps reduce manufacturing lead/cycle times and improves performance to meet customer requirements on time. OEE improvement increases efficiency, reduces downtime, and cuts costs. Let us understand how to improve OEE in your manufacturing operations.
IIoT integration for Real-Time Data Collection
The potential uses of IoT technology within the manufacturing industry are substantial. IIoT integration gives access to machine data that is generally isolated on the factory floor, to understand equipment performance through instrumentation and analytics.
IIoT integration automates the shop floor connectivity, leads to real-time access of OEE metrics for improvement. IIoT automation provides real-time information, automates equipment monitoring, and helps plant managers to make informed decisions.
Performance Analysis
Efficiency and outputs are determined by analyzing historical data. Performance analysis facilitates real-time insight and provides the root cause analysis behind inefficiencies. With performance analysis and optimization, operators can optimize their efficiency, better understand how their machines work, and predict future Performance. This can ultimately lead to an improved OEE.
Preventive Maintenance
Preventive maintenance is approach to do maintenance through which factory assets or equipment are scheduled for service regularly to prevent unplanned breakdowns and unscheduled downtime. This approach helps improve the availability of machines, leading to Overall Equipment Effectiveness in manufacturing. Preventive or scheduled maintenance improves equipment reliability and availability and increases the factory assets’ lifespan, improving OEE.
Knowledge Management:
Enhancing machine operators knowledge about production processes and machine usage substantially improves the efficiency of OEE. Operators’ engagement drives improvement to the production activities. To avoid unplanned production stops, operators’ attention in work is essential. OEE tracking and sharing the real-time OEE results with operators at regular intervals helps them gain insight into areas that need improvement, leading to further improved OEE.
Quality Production
Quality productions are free from defects or wastage and do not require rework. Quality production helps the manufacturing process run smoothly without any interruption or delay. As a result, OEE increases when production meets the expected quality standards. Quality assurance enables the production line to run smoothly, with minimal downtime and breakdowns. It also maximizes equipment utilization and efficiency, resulting in improved OEE.
How does SFactrix help in improving OEE?
SFactrix.ai is a comprehensive MES solution for monitoring the OEE metrics and other performance, maintenance, and quality metrics to improve overall production efficiency. SFactrix MES enables capturing real-time production data from your machines and operators to monitor OEE metrics.
SFactrix MES provides three levels of OEE metrics, which help improve production efficiency :
- Assets Performance Metrics
- Maintenance Metrics and Fault Trends
- Quality Metrics and Rejection Trends
SFactrix MES capabilities help manufacturers to improve their OEE in the following ways:
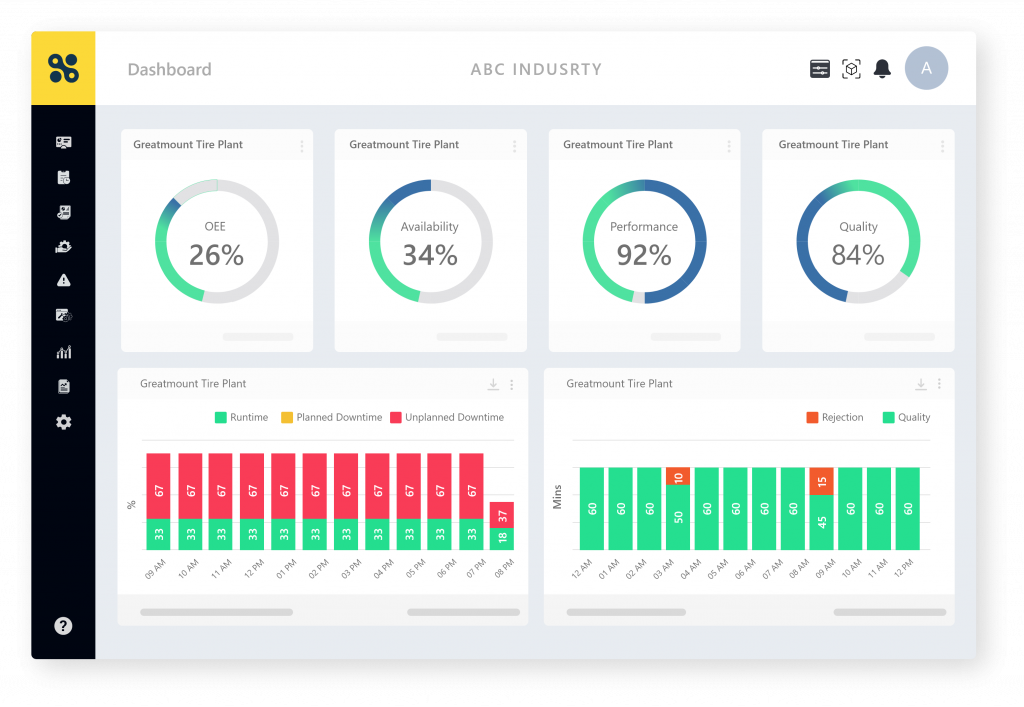
Real-time Monitoring
SFactrix.ai prvoides manufacturing metrics module and comparative analysis to continuously monitor equipment performance and provide real-time alerts when anomalies or potential issues arise. This approach helps maintenance teams take corrective action quickly, reducing downtime and improving OEE.
SFactrix also provides hourly production performance metrics report, which helps the plant users to identify the continuous performance data of running assets. This further improves OEE in a manufacturing plant.
Capacity Management
Tracking the total factory assets and understanding each asset’s capacity, run rate, lead time, and current status are critical in the creation of manufacturing plans and schedules accurately. Plant Managers can easily see the asset’s current status and other metadata as part of the asset management feature in SFactrix. This helps in improving the overall equipment effectiveness of a plant.
Key Performance Indicators
SFactrix.ai provides a detailed analysis of shift-based machine performance, availability, and quality production data. This helps operators and maintenance teams identify areas for improvement and track progress over time to enhance the Overall Equipment Effectiveness.
Process Optimization
SFactrix.ai can also identify opportunities for process optimization, such as reducing cycle times or minimizing changeover times. By streamlining these processes, businesses can improve productivity and OEE.
Maintenance Metrics
SFactrix MES provides a maintenance KPI feature that shows the data/information about asset maintenance and fault trend. This feature in SFactrix shows the total time spent on fault repairs, asset maintenance, the frequency of occurrence of faults in an asset, the type of fault that occurred, etc. This data helps the factory users look into the time wasted/downtime and the reason for downtime, enabling them to take necessary steps to avoid such occurrences in the future. This leads to the availability and reliability of assets and to have better and improved OEE.
Work Order Management
SFactrix enables the production operation process through its work order feature. The work order management in SFactrix allows the plant managers to plan, allocate and assign jobs to operators. This ensures maximum engagement of production operators. High-end visibility on the production floor and tracking work orders further help plant managers and supervisors change the course of execution more efficiently and reach OEE industry-standard goals.
Final thoughts on the OEE Improvement
As a manufacturing company, maximizing productivity is always a top priority. OEE is one of the essential measures to identify manufacturing productivity. It is one of the most important performance measurements in modern manufacturing facilities. By optimizing OEE, you can increase capacity, reduce costs, improve quality, and/or increase efficiencies in your production lines.
The higher the OEE, the more efficient the manufacturing process is. It is also necessary to understand that OEE is the only metric. Continuous improvement should be a never-ending journey for a manufacturing organization striving to be at the top of its industry.
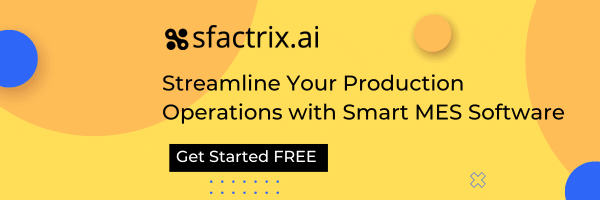