Backorders can create significant problems for businesses and customers alike. When products go out of stock or are not yet available, they can create headaches for everyone involved. This article aims to provide a comprehensive exploration of backorders, their causes and impacts, and strategies to prevent them. Additionally, we will examine some technology solutions that can help businesses manage backorders more efficiently.
What are Backorder?
Simply put, backorder occur when a customer orders a product that is not currently available. This means that the product is out of stock or not yet manufactured. It can happen for many reasons, including poor demand forecasting, supply chain issues, and inadequate inventory management. They can affect businesses of all sizes, and their impacts can be significant.
Definition and Explanation of Backorder
Backorder occur when a customer places an order for a product that is not immediately available. This can happen for many reasons, including high demand or supply chain disruptions. When a product is backlogs order, the customer must either wait for the product to become available or cancel the order.
Backorders can be frustrating for both customers and businesses. Customers may have to wait longer than expected to receive their products, while businesses may lose sales and revenue due to the delay. However, it can also be a sign of high demand for a product, which can be a positive indicator for businesses.
Common Causes of Backorder
Backorder can occur for many reasons, including:
- Inaccurate demand forecasting: If a business underestimates the demand for a product, it may not order enough inventory to meet customer needs.
- Supply chain disruptions: Natural disasters, transportation delays, and other factors can disrupt the supply chain and cause delays in product availability.
- Inadequate inventory management: Poor inventory management practices can lead to stockouts and backlogs.
- Inadequate safety stock levels: Safety stock is the extra inventory that businesses keep on hand to prevent stockouts. If a business does not have enough safety stock, it may experience backlog.
- Inefficient communications between departments: If different departments within a business do not communicate effectively, it can lead to delays in product availability and backlog orders.
These causes can be addressed with careful planning, improved communication, and the implementation of technology solutions. For example, businesses can use inventory management software to track inventory levels and automate the ordering process.
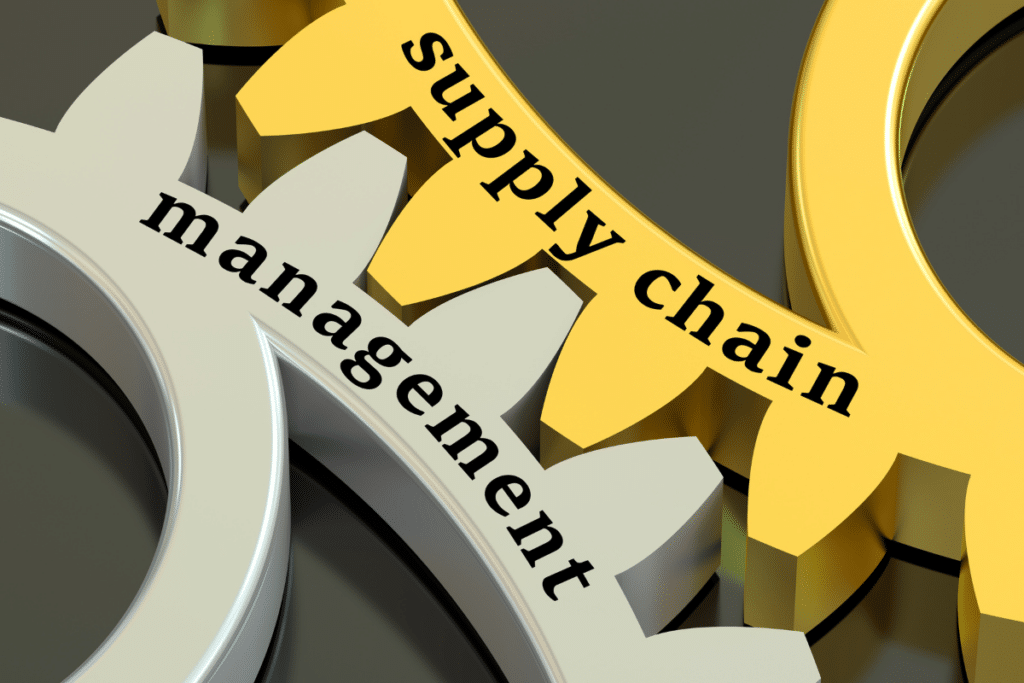
The Impact of Backorder on Businesses and Customers
Backorder can have a significant impact on both businesses and customers. For businesses, it can lead to lost sales, decreased customer satisfaction, and increased costs. Customers may become frustrated with long wait times or seek out competitors with better product availability. The impacts of back order can ripple through the supply chain, affecting everyone involved.
However, backorders can also present opportunities for businesses. They can be a sign of high demand for a product, which can help businesses make informed decisions about inventory management and production planning. It can also provide an opportunity for businesses to communicate with customers and manage their expectations.
In conclusion, they are a common challenge for businesses, but they can be managed with careful planning and the implementation of effective inventory management practices. By understanding the causes and impacts, businesses can take steps to minimize their occurrence and provide better customer service.
The Backorder Management Process
Backorder Management process should include the following:
Identifying and Tracking Items
A complete and up-to-date inventory management system is essential for identifying and tracking backlogs orders items. This process should be integrated with other systems, such as customer ordering and purchasing processes.
Modern software systems allow for easy identification of backordered items. This can help prevent delays in fulfilling orders and can also help businesses to identify trends and potential issues with their inventory management.
One way to identify backlogs orders items is to regularly review inventory levels and compare them to customer orders. This can help businesses to identify items that are in high demand and may need to be restocked more frequently.
Another way to track backlog order is to use a system that automatically updates inventory levels as orders are placed and fulfilled. This can help to ensure that businesses always have an accurate view of their inventory levels and can quickly identify any items that are on backlog orders.
Communicating with Customers about Backorder
Clear and timely communication with customers is critical. Businesses should provide realistic timelines for product availability and update customers regularly. Proactive communication can help to manage expectations and build trust with customers.
Customers send an order when the items out of stock, so it is important to communicate this information to them as soon as possible. This can help to manage their expectations and prevent frustration or disappointment.
Businesses should provide realistic timelines for when the item is expected to be back in stock and should update customers regularly on the status of their order. Proactive responses to customers can also help to prevent them from canceling their orders or choosing to shop with a competitor.
Fulfilling Backorder and Resolving Issues
Fulfilling backlogs orders requires a coordinated effort across multiple departments, including purchasing, production, and shipping. Timely and accurate fulfillment can help to build customer loyalty and minimize business impacts.
When fulfilling backlogs, it is important to have a system in place that allows for efficient communication and coordination between departments. This can help to ensure that all necessary steps are taken to fulfill the order as quickly and accurately as possible.
Businesses should also have a system in place for resolving any issues that may arise during the fulfillment process. This can include issues such as delays in production or shipping or errors in the order itself.
By having a clear and efficient process for managing backlogs orders, businesses can minimize the impact of backorders on their customers and their bottom line. This can help to build customer loyalty and ensure long-term success.
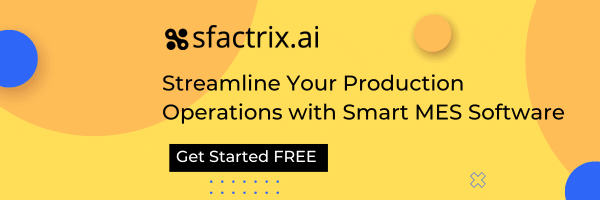
Strategies to Prevent Backorder
Preventing backorder requires a combination of accurate demand forecasting, efficient inventory management, and strong supplier relationships. Gartner identified 4 actions for supply chain team to prepare back order strategy to handle in future. Some strategies for preventing, include:
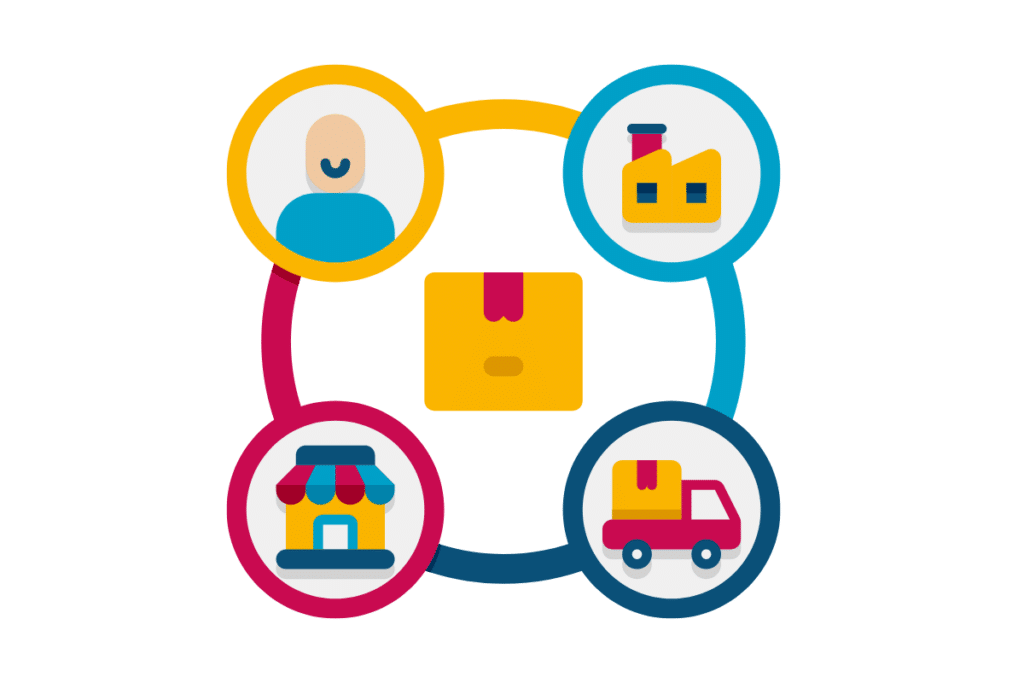
Accurate Demand Forecasting
Accurate demand forecasting is essential for preventing backlogs orders. This process requires careful analysis of past sales data, market trends, and the potential impacts of external factors such as seasonality and promotions.
One way to improve demand forecasting is to use technologies like predictive analytics based on historical data and statistical algorithms to forecast future demand with a high degree of accuracy. This can help businesses to better anticipate demand and avoid stockouts.
Another strategy is to engage with customers and gather feedback on their purchasing behavior. This can help businesses to identify patterns and anticipate demand fluctuations.
Efficient Inventory Management
Efficient inventory management is critical for preventing backlogs orders. This process includes maintaining adequate safety stock levels, establishing reorder points, and optimizing inventory turnover.
One way to optimize inventory turnover is to implement a just-in-time (JIT) inventory system. JIT is a lean manufacturing strategy that aims to reduce waste and improve efficiency by only producing or ordering goods when they are needed. This can help businesses to minimize inventory holding costs and avoid stockouts.
Another strategy is to use inventory management software. Inventory management software can help businesses to track inventory levels in real time, automate reorder processes, and optimize stock levels based on demand forecasts.
Building Strong Supplier Relationships
Building strong supplier relationships can help to prevent backlogs orders by ensuring timely and reliable deliveries. This process involves proactive communication, regular performance evaluations, and the establishment of contingency plans.
One way to build strong supplier relationships is to establish clear communication channels. This can include regular meetings, conference calls, and email updates. By fostering open communication, businesses can better anticipate supply chain disruptions and avoid stockouts.
Another strategy is to conduct regular performance evaluations. This can help businesses to identify areas for improvement and provide feedback to suppliers. By working collaboratively, businesses and suppliers can improve delivery times and reduce the risk of backorder.
Implementing Safety Stock and Reorder Points
Safety stock and reorder points are critical for preventing backlogs orders. Safety stock serves as a buffer to absorb unexpected demand spikes, while reorder points trigger replenishment orders when inventory levels reach a certain threshold.
One way to determine safety stock levels is to use statistical methods such as the service level method or the statistical safety stock method. These methods use historical data and statistical algorithms to calculate the optimal safety stock level for a given product.
Another strategy is to establish repeated order points based on lead time and demand variability. This can help businesses to avoid stockouts by triggering replenishment orders before inventory levels reach critical levels.
By implementing these strategies, businesses can prevent backorders and improve customer satisfaction. By accurately forecasting demand, optimizing inventory levels, building strong supplier relationships, and implementing safety stock and reorder points, businesses can ensure timely and reliable deliveries and avoid stockouts.
Technology Solutions for Backorder Management
Inventory Management Software
Inventory management software can help businesses keep track of inventory levels, identify backlogs order items, and optimize inventory turnover. Sophisticated software solutions can also provide real-time data analytics and reporting to support decision-making. This software can help businesses identify trends in product demand, track the performance of suppliers, and automate the reordering process.
Automated Reordering Systems
Automated reordering systems can help businesses minimize the risk of backlogs orders by triggering replenishment orders automatically. These systems can be customized to suit specific business needs, and many can integrate seamlessly with other software solutions. Automated reordering systems can also help businesses reduce the amount of time and resources required to manage inventory, freeing up staff to focus on other critical tasks.
Real-time Data Analytics and Reporting
Real-time data analytics and reporting can provide businesses with essential insights into their inventory management processes. By analyzing sales data, market trends, and other factors, businesses can identify potential risks and take proactive measures to prevent backorder. Real-time data analytics and reporting can also help businesses identify opportunities for growth and expansion by providing insights into emerging trends and customer preferences.
However, technology solutions are not a silver bullet for backorder management. Preventing backlogs order requires a combination of accurate demand forecasting, efficient inventory management, and strong supplier relationships. Businesses must also be prepared to adapt to changing market conditions and adjust their inventory management processes accordingly.
Conclusion
In conclusion, backorder can be a significant problem for businesses and customers alike. Preventing backorder requires a multifaceted approach that incorporates a range of strategies and solutions. Technology solutions can help businesses manage backorder more efficiently, but they are only one piece of the puzzle. By implementing these strategies and solutions, businesses can minimize the impacts of backorder and improve customer satisfaction.
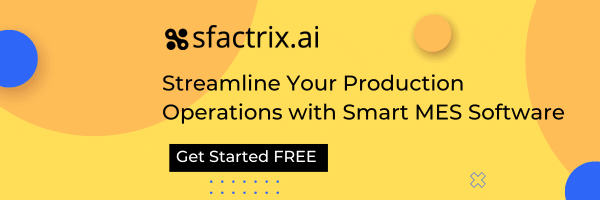