In the intricate symphony of production, lead time acts as a conductor, orchestrating the rhythm of operations from initiation to completion. The significance of lead time extends beyond a mere metric; it’s a critical determinant of customer satisfaction, operational efficiency, and competitive advantage. This expansive blog aims to traverse the nuanced terrain of lead time in production, unravel its profound importance, dissect common challenges, and delve deeply into strategic approaches for its reduction, offering manufacturers a comprehensive guide to operational excellence.
What is Lead Time?
Lead time refers to the duration it takes to complete a process or deliver a product from the initiation of an order or request to its fulfillment. It encompasses the entire timeline, including order placement, processing, production, and delivery. Lead time is a critical metric for businesses as it influences inventory management, production planning, and customer satisfaction. Short lead times are often desirable as they enable companies to respond quickly to customer demands and market changes, reducing the risk of stockouts and improving overall efficiency. However, achieving optimal lead times requires effective coordination and streamlined processes across various stages of a supply chain or production cycle.
Importance of Streamlining Lead Time in Production:
Lead time is the duration between the initiation of a process and its completion. In production, lead time refers to the time it takes to manufacture a product from start to finish. It includes all stages of production, including sourcing raw materials, manufacturing, quality control, packaging, and shipping.
To understand the imperative of reducing lead time is to grasp the linchpin of manufacturing success. A truncated lead time translates into heightened customer satisfaction, increased adaptability to market dynamics, and a streamlined cash flow. Pursuing shorter lead times is not merely an operational enhancement; it’s the strategic positioning of manufacturing entities at the forefront of a dynamic business landscape, ready to seize opportunities and navigate challenges with agility.
Common Challenges in Reducing Lead Time:
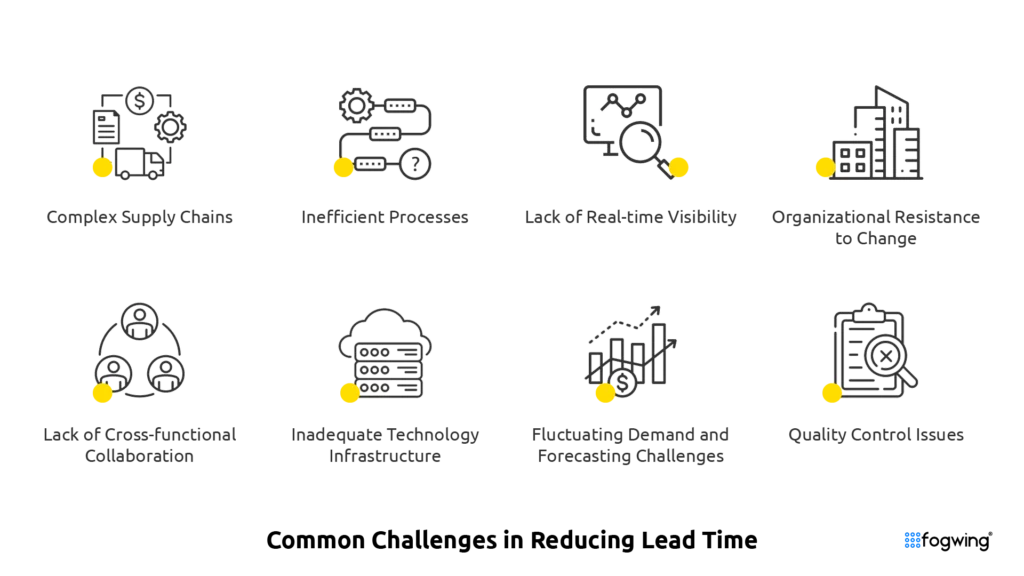
Reducing lead time in production is a pursuit laden with potential benefits but comes with its fair share of challenges. Recognizing and overcoming these hurdles is essential for organizations aiming to streamline operations and enhance overall efficiency. In this section, we’ll explore the common challenges encountered on the road to reducing lead time:
1. Complex Supply Chains:
Modern supply chains are often intricate networks spanning multiple regions and involving numerous stakeholders. Coordinating and synchronizing these complex supply chains can be a significant challenge. Delays in procuring raw materials or components can cascade down the production line, elongating lead times. Addressing this challenge requires a strategic approach to supply chain management, including real-time visibility and collaboration with suppliers.
2. Inefficient Processes:
Inefficiencies in production processes can contribute to extended lead times. These inefficiencies may manifest as redundant steps, unnecessary handling, or bottlenecks in the workflow. Identifying and eliminating these inefficiencies often involves a thorough analysis of the entire production process, employing tools such as value stream mapping to visualize the flow and identify areas for improvement.
3. Lack of Real-time Visibility:
A lack of real-time visibility into the production process can impede the ability to respond swiftly to changes and disruptions. Without accurate and up-to-date information, decision-makers may struggle to make informed choices, leading to delays in addressing issues that could impact lead times. Implementing sensors, IoT devices, and advanced analytics can provide the real-time insights necessary for proactive decision-making.
4. Organizational Resistance to Change:
Introducing changes to established processes can be met with resistance from employees and stakeholders. The reluctance to embrace change can hinder the implementation of new strategies to reduce lead time. Overcoming this challenge requires effective change management strategies, including clear communication, employee training, and a commitment to fostering a culture of continuous improvement.
5. Lack of Cross-functional Collaboration:
Reducing lead time often requires collaboration across different organizational departments and functions. Siloed approaches, where each department operates independently, can hinder the seamless flow of information and coordination. Breaking down these silos and fostering cross-functional collaboration is essential for addressing challenges that span multiple aspects of the production process.
6. Inadequate Technology Infrastructure:
Outdated or inadequate technology infrastructure can pose a significant challenge in reducing lead time. Manual or outdated systems may result in data errors, communication delays, and overall inefficiencies. Investing in modern technology solutions, such as ERP systems and automation tools, is crucial for creating a foundation that supports streamlined production processes.
7. Fluctuating Demand and Forecasting Challenges:
Variability in customer demand and inaccurate forecasting can lead to challenges aligning production schedules with actual market needs. Sudden spikes or drops in demand can disrupt production planning and lead to either excess inventory or stockouts. Implementing robust demand forecasting models and adopting flexible production strategies can help mitigate the impact of demand fluctuations.
8. Quality Control Issues:
Ensuring product quality is paramount, but stringent quality control processes can sometimes extend lead times. Striking the right balance between rigorous quality checks and efficient production is crucial. Implementing advanced quality control techniques, such as statistical process control, can help maintain high-quality standards without unduly delaying production.
Strategies for Identifying and Eliminating Bottlenecks:
Bottlenecks, akin to hidden adversaries, lurk within production processes, silently elongating lead times. Identifying and eliminating these bottlenecks becomes a foundational expedition in pursuing streamlined production. Techniques such as value stream mapping and process reengineering serve as investigative tools, enabling organizations to scrutinize their workflows, pinpoint areas of delay, and strategically intervene to optimize the overall production trajectory.
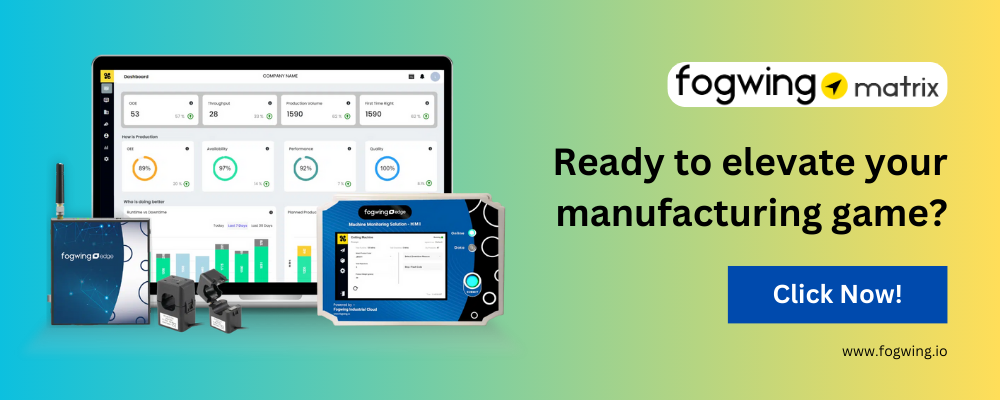
Utilizing Technology and Automation:
In the dynamic landscape of modern manufacturing, staying competitive requires more than traditional approaches. Utilizing technology and automation is a cornerstone for achieving operational excellence and reducing lead time. This section will explore the transformative power of technology in streamlining production processes:
1. Automation in Production:
Automation, often synonymous with increased efficiency, is pivotal in reducing lead time. By automating repetitive and time-consuming tasks, organizations can accelerate production cycles and minimize the risk of errors. Robotics, robotic process automation (RPA), and automated guided vehicles (AGVs) can be integrated into the production line to enhance efficiency and consistency.
2. Internet of Things (IoT) Integration:
The integration of IoT devices provides real-time insights into various aspects of the production process. Sensors on machines, equipment, and products can collect data, allowing for proactive maintenance, quality monitoring, and optimized production scheduling. IoT-enabled systems create a connected ecosystem that fosters agility and responsiveness to changing conditions.
3. Advanced Analytics for Decision-Making:
Harnessing the power of advanced analytics transforms raw data into actionable insights. Predictive analytics, machine learning, and artificial intelligence (AI) enable organizations to anticipate potential issues, optimize resource allocation, and make data-driven decisions. This proactive approach empowers decision-makers to address challenges swiftly, contributing to a reduction in lead time.
4. Enterprise Resource Planning (ERP) Systems:
An integrated ERP system is the nerve center of manufacturing operations. It consolidates data from various departments, providing a unified view of the entire production process. From order processing to inventory management, an ERP system streamlines communication and facilitates real-time collaboration, enabling organizations to respond promptly to changes in demand.
5. Manufacturing Execution Systems (MES):
MES bridges the planning phase and production execution. By monitoring and controlling the production process in real-time, MES enhances visibility and ensures that operations align with the overall strategic objectives. It facilitates efficient resource utilization, minimizes downtime, and contributes to the overall reduction of lead time.
6. 3D Printing and Additive Manufacturing:
The advent of 3D printing and additive manufacturing technologies has revolutionized production processes. These technologies enable rapid prototyping, customization, and the production of complex components with minimal waste. By reducing the time traditionally associated with tooling and setup, 3D printing can significantly shorten lead times, particularly in industries requiring quick product iterations.
7. Cloud-Based Solutions for Flexibility:
Cloud-based solutions offer flexibility and scalability, allowing organizations to adapt to changing demands. Cloud computing provides the infrastructure for data storage, collaboration, and real-time access to information from anywhere. This flexibility is particularly valuable in scenarios where remote collaboration and quick decision-making are essential to streamlined production.
Implementing Lean Manufacturing Principles:
Lean manufacturing, a philosophy grounded in eliminating waste and optimizing processes, stands as a beacon for organizations aspiring to reduce lead time. Principles such as 5S (Sort, Set in order, Shine, Standardize, Sustain), Kanban, and Just-In-Time (JIT) manufacturing serve as the cornerstone of lean practices, fostering the creation of agile, responsive production environments. Embracing a culture of continuous improvement ensures that organizations not only eradicate inefficiencies but actively evolve to meet the market’s ever-changing demands.
Measuring and Monitoring Progress:
The pursuit of shorter lead times demands more than strategic implementations; it requires vigilant measurement and monitoring. Key Performance Indicators (KPIs) such as cycle time, on-time delivery, and production efficiency become the North Star, guiding organizations toward their operational objectives. This commitment to continuous monitoring serves as both a compass for timely course corrections and a mechanism for acknowledging and celebrating milestones achieved on the journey to more efficient production processes.
How Fogwing Matrix Reduces Lead Times
The Fogwing Matrix is pivotal in reducing Lead times within manufacturing processes. Seamlessly integrating IoT sensors, data analytics, and real-time insights enables manufacturers to optimize production efficiency.
Fogwing Matrix offers real-time data on machine performance, helping identify bottlenecks and inefficiencies promptly. This data empowers operators to make informed decisions, reducing downtime and speeding up processes.
The Fogwing matrix equipped with preventive maintenance capabilities anticipates equipment failures, allowing timely repairs, preventing unexpected breakdowns, and minimizing unscheduled downtime.
Fogwing Matrix reduces Lead Times by ensuring machines operate efficiently, minimizing downtime, and facilitating data-driven process optimization. This increases productivity, leads to cost savings, and enhances overall manufacturing competitiveness.
To know about how the Fogwing matrix helps to improve Cycle Times, read this, Cycle Time Is A Critical KPI For Manufacturing | Fogwing.io
Conclusion:
In the grand tapestry of manufacturing, reducing lead time is not a mere subplot; it’s a narrative of operational transformation. The amalgamation of streamlined processes, technological integration, and the infusion of lean manufacturing principles positions companies not merely as players but as architects shaping the future of production.
As industries traverse the path of evolution, those embracing and implementing these multifaceted strategies fortify their foundations for sustained success, ensuring they are not just keeping pace with change but actively steering the trajectory of operational excellence in the manufacturing landscape.
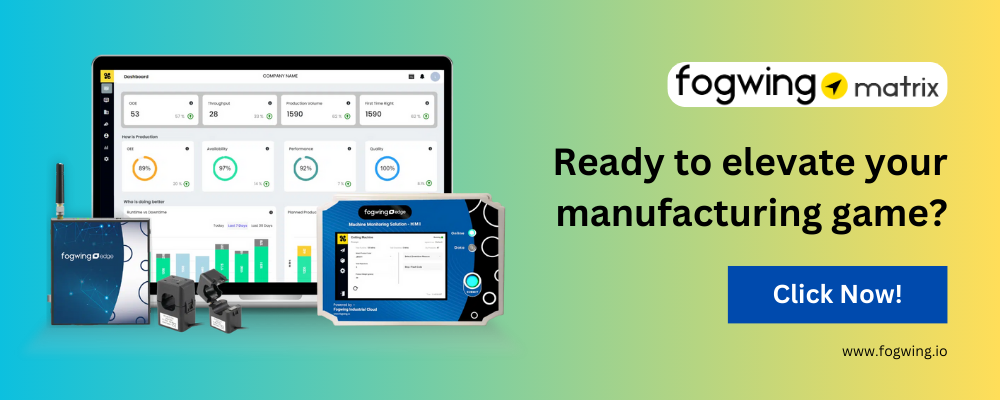