Do you know, how many manufacturers can actually claim that they have achieved 100% of Lean Manufacturing by eliminating all the 8 wastes? The no. is only a few. Lean Manufacturing brings a revolutionary change into the manufacturing industry. It is not just about implementing a few tools and techniques in the manufacturing process. It’s about adopting the transformation of the entire business’s operations and processes.
Lean Manufacturing is a methodology that can help to streamline and improve manufacturing processes to provide enhanced customer benefits while saving time and money by eliminating overall efficiency waste. The main objective of Lean manufacturing is to eliminate unwanted processes, tasks, complexities and reduce the efforts in managing large inventory, and produce the optimum quality products at a minimal cost.
‘Lean’ is the practice of implementing manufacturing processes that consider the expenses on resources which creates no value for the business. So, Lean manufacturing focuses on eliminating all 8 wastes and improving customer satisfaction throughout the manufacturing process.
8 wastes of Lean Manufacturing:
Wastes are an inevitable part of manufacturing processes which adds no value to the business for the spending. These wastes unnecessarily added up to the cost of the final finished products. The wastes can be identified and eliminated to increase efficiency, reduce operating costs, and improve customer satisfaction.
Following are the major 8 wastes of manufacturing:
- Defects
- Over Production
- Waiting
- Negligence of skills
- Transportation
- Inventory
- Motion
- Excess Processing
1. Defects
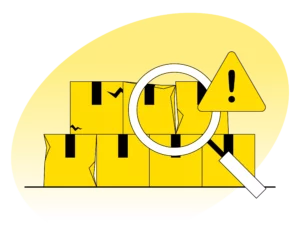
They are the scraps that occur during the production process which impact the final product and its cost. A defect refers to any instance wherein a product does not meet design or manufacturing specifications. The defects waste is so prevalent on production floors that the industries use a punch list system just to track those particular wastes. Poor fabrication, ineffective workmanship, improper sequencing, and inadequate inspections can all be described as defects in a production process. Whenever a defect occurs in the manufacturing process, it costs money, time, and effort to correct the defect, hence it is considered a waste of overall efficiency and adds no value to the end product.
2. Over-Production
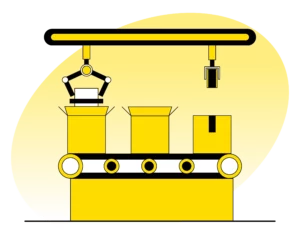
It is the excess amount of production that is not required to meet the current market demand. It is a terrible waste for businesses that lead to unnecessary investment. Over-production also has a significant impact on the success of any manufacturing business. Overproduction occurs when raw materials, parts, or assemblies are abundantly available on the production floor or due to inadequate materials and production planning. The waste of overproduction leads to many other wastes in manufacturing. The loss or waste of efficiency is a major concern when there is overproduction.
A company while producing more than the market demands, is overspending on resources like time, money, and raw materials. Thus, it leads to revenue loss for the company. The production managers need to find a way to produce the right amount of product to avoid waste of their valuable resources.
3. Waiting
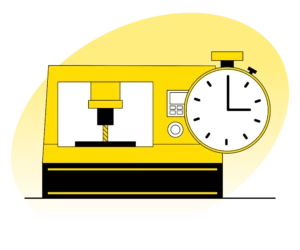
It is the unnecessary time spent while manufacturing a product or partand thus it is considered as a waste of manufacturing. This waste in the manufacturing process is a little difficult to identify among all 8 wastes, as it may be sometimes considered “necessary/part of the process’’. Production-on-hold or waiting period occurs due to unplanned machine downtime or material shortage which is considered a major waste hour among all the 8 wastes of lean manufacturing. The waiting time spent during the manufacturing process adds no significant value to the product which is why it is considered a waiting waste. Following are a few examples of waste of waiting.
- Operators / Machines not running whilst they wait for a previous process’ production to be sorted due to quality problems.
- Waiting for a machine failure to be resolved by the maintenance team.
- Waiting for a previous production process completion to complete the rest of the batch of material prior to movement.
- Waiting for the raw materials from the supplier due to poor supply chain planning.
4. Negligence of skills
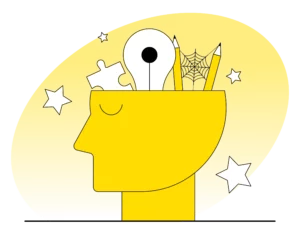
It refers to when employees are not utilizing their complete potential or skill set for a given task. This can lead to wasted time and resources which impact productivity. Negligence of skills among the workforce is prevalent in various stages of the manufacturing process. The workforce or employees are the true assets of a manufacturing organization, and utilization of this most valuable asset adds potential to the operational process. Negligence of skills occurs when management fails to ensure the utilization of their employee’s full potential & talent.
Lack of team grooming, lack of appropriate policies, and poor communication among teams, lead to the waste of negligence of skills. Here are some ways that employees could be under-utilized:
- Applicable skills from previous roles aren’t recognized and utilized.
- Manufacturers failing to provide proper training to develop new, higher-level skills for employees with a growth mindset.
- Opportunities aren’t available to employees showing aptitude.
5.Transportation
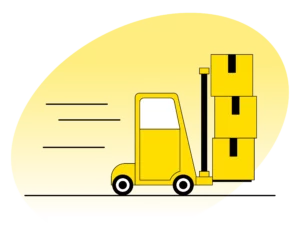
One of the 8 wastes of Lean Manufacturing, is defined as the unnecessary movement of raw materials and finished goods from one warehouse to another warehouse without proper dispatch planning. Transportation waste can arise from inefficient routing, poor scheduling, and other inefficiencies in the supply chain. Transportation waste occurs when materials are moved unnecessarily or inefficiently, resulting in time and cost inefficiencies.
Transportation waste can be costly to a manufacturing business as it increases the cost of products and reduces productivity. To reduce transportation waste in a Lean Manufacturing environment, companies must look for ways to optimize their supply chain and increase efficiency throughout their operations. By optimizing routes and streamlining processes, companies can reduce transportation waste while still delivering high-quality products on time. Following are a few examples of Transportation waste in the manufacturing industry.
- The unnecessary movement or transport of products from one functional area to another within the same factory unit.
- The unnecessary shipment of products from one “functional” factory to another.
6. Inventory
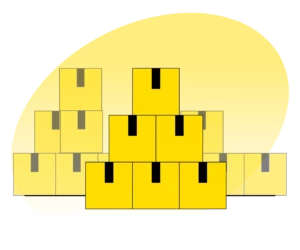
Inventory waste in Lean manufacturing refers to the actual inventory being wasted or inventory indirectly causing resource waste. Excessive inventory can actually become a waste over time. It can lead to delays in the detection of any problems in production because of the sheer quantity of products in the inventory. This can also lead to additional work being created to identify and manage the defects in the products. Inventory waste in manufacturing includes:
- Piles of materials and resources lying on the inventory floor for a longer period of time that are not ready to be placed on the shop floor.
- Overproduction leads to piling up products in the inventory is considered as common inventory waste.
The main cause of inventory waste is the waste of ‘overproduction’. It can also be caused by a lack of material planning, lack of inventory management, or a lack of balance in your workflow causing inventory to build up before or after different processes. It is essential to reduce inventory waste so that you can optimize the processes and boost your bottom line.
7.Motion
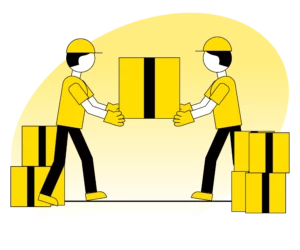
Motion in Lean manufacturing refers to any movement of operators, production managers, and other designated workers in a factory unit. Motion waste is defined as any movement that does not add value to the product or process and can be a major source of inefficiency and cost. Among all the 8 wastes, motion waste is an important factor to consider when implementing Lean Manufacturing. This waste can be found in many areas of manufacturing including assembly, packaging, and material handling.
Examples of motion waste include unnecessary walking or reaching out for tools, repeated motions, or waiting for materials to arrive at the workstation. By recognizing and eliminating motion waste, manufacturers can reduce costs while increasing productivity and efficiency.
Eliminating motion waste is not a “one-and-done” proposition. Instead, it’s a continuous process that requires a review of your existing processes, buy-in from upper management and workers, and dedicated execution of your motion waste elimination strategy.
8. Excess Processing
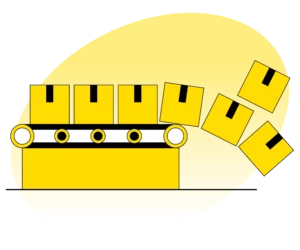
It means adding more work or value to a service or product than the end product requires. Over-processing or Excess processing involves making unnecessary labor, using more components, or adding more steps in a product or service than what is required by the end-user.
In Lean Manufacturing, excess processing is considered as one of the 8 wastes as it increases unnecessary production costs. Companies that are able to identify and eliminate this type of waste can improve their efficiency by reducing costs and increasing output quality. Following are a few examples of over-processing:
- Utilization of higher precision equipment than necessary.
- Using components with capacities beyond what is required.
- Running additional analysis on a process than needed.
- over-engineering of a product or solution.
- Repeated entry of processing data.
Benefits of Identifying the 8 wastes of Lean Manufacturing
Lean manufacturing is a process that helps companies reduce waste in production and become more efficient. The principle of Lean Manufacturing is to identify and eliminate the wastes of the manufacturing process that adds no value to the customer. Identifying and eliminating 8 Wastes can help organizations save time, money, and resources. It also gratifies the customers by helping them get the products they need faster.
Lean Waste identification is a crucial step in any Lean Manufacturing system. By identifying what type of waste exists within the production process, businesses can identify areas where they can improve efficiency and reduce costs. Additionally, it allows them to better understand how their processes are impacting their bottom line.
By identifying and eliminating 8 Wastes, businesses can create an environment of continuous improvement that leads to increased productivity and profitability. This will ultimately benefit both customers and the manufacturing organization as a whole by reducing costs while creating better products or services for customers.
How Industry 4.0 helps in reducing the 8 Wastes
‘’The primary objective of the lean approach and Industry 4.0 is operational excellence’’. If manufacturers hope to improve their processes, they need to know where opportunities for improvement lie. Industry 4.0 can provide that information by collecting data from sensors and connected machinery throughout the production floor. Industry 4.0 digitalization enhances the principles of lean six sigma. Industry 4.0 has lent a new suite of tools to aid manufacturers in production planning, predictive maintenance, and more to eliminate Lean wastes and embrace Lean principles into businesses.
With Industry 4.0, real-time data monitoring at the production floor helps manufacturers to eliminate disruptions and wastes by reducing machine downtime, managing supply chains, and more. Lean six sigma principles help manufacturers create smart factories equipped with advanced sensors, robotics, and software.
Lean manufacturing goals are highly beneficial for businesses, and Industry 4.0 makes these benefits attainable, enabling manufacturers to achieve the complete benefits of lean manufacturing principles.
The Future of Lean Manufacturing:
Lean manufacturing methods have been in practice over the years to maximize customer value while minimizing 8 wastes of lean and increasing productivity. The future of the Factory is an intelligent, flexible, and highly agile production environment that will equip plant operations and management with the real-time data, and in-depth information they need to maximize the production value, Return on Investment (ROI). Achieving lean is a continuous process of change that needs to be assessed and monitored in real-time.
The Future of lean lies in analyzing all the complexity and performance improvement scope of a project or a process in a short duration of time to pace up with the constraint of time deadline. Lean will develop a strong responsive system to progress with challenges and new opportunities.
With the help of digitalization, automation, machine learning, and big data, manufacturers can drive their lean manufacturing principles to the next level by leveraging their abilities to eliminate all the 8 wastes while increasing value for their business and their customers.
Conclusion
Understanding and eliminating the 8 wastes of Lean Manufacturing is important, as Lean methodology has been proven highly successful since it can reduce costs, increase productivity, maintain high levels of quality, and thus have a positive impact on the organization. It is critical for businesses to draw insights from the past to ensure ideal implementation standards of Lean practices to meet the needs of efficient and optimized manufacturing.