Facility Maintenance is crucial to ensure smooth operational run and longevity of any built manufacturing environment. From industrial facilities to commercial spaces and residential buildings, implementing a proper maintenance strategy is essential for creating a safe, efficient, and comfortable environment for occupants.
Entering the world of facility maintenance is critical for making well-informed decisions and ensuring the optimal performance of buildings. In this blog, we will walk you through the fundamentals of facility maintenance, its importance, and various other essential particles and associated features.
What is Facility Maintenance?
Facility maintenance encompasses a comprehensive range of activities focused on ensuring the optimal functionality, safety, and longevity of physical spaces and infrastructure within an organization. It involves the regular inspection, upkeep, and repair of buildings, equipment, systems, and surroundings to create a conducive and efficient environment.
This multifaceted discipline spans various commercial, industrial, and institutional sectors. Facility maintenance services include routine inspections, preventive maintenance measures, equipment repairs, and addressing environmental concerns.
The goal is to enhance the longevity of assets, reduce downtime, and create a safe, comfortable, and operational space for occupants. Proactive facility maintenance contributes significantly to operational efficiency, cost-effectiveness, and the overall well-being of the occupants and the organization.
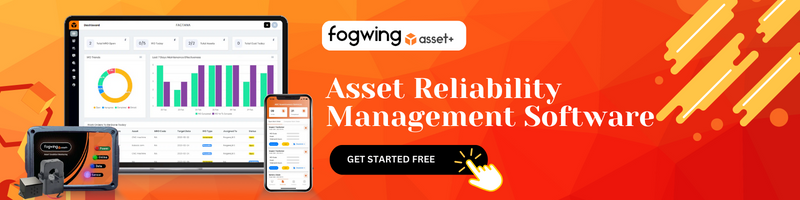
Importance of Facility Maintenance Services
Facility management is crucial for several reasons in this digitalized world. Selecting proper maintenance management software is vital to an organization’s overall functioning and success.
Fogwing Asset+, a smart CMMS software, can enable organizations to conduct comprehensive asset maintenance activities with its cutting-edge and advanced technologies.
Here are a few reasons why facility maintenance is essential in manufacturing:
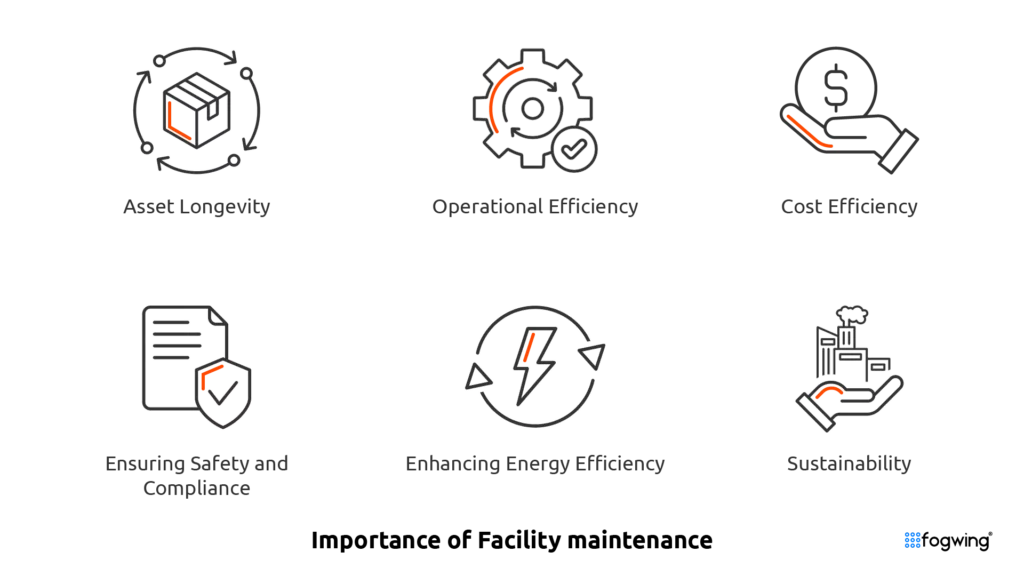
Asset Longevity
Regular maintenance is the bedrock of asset longevity, acting as a proactive strategy to preserve the health and functionality of facilities and equipment. By systematically inspecting, cleaning, and repairing components, potential issues are identified and addressed before they escalate, preventing premature wear and tear.
This meticulous care extends the lifespan of assets and mitigates the need for costly and unplanned replacements. Whether it’s routine inspections, lubrication, or addressing minor repairs, the cumulative effect of these facility maintenance practices is a significant reduction in overall wear, ensuring that assets operate optimally and deliver enduring value over time.
Operational Efficiency
Operational efficiency is a direct beneficiary of proper facility maintenance, which protects against unexpected breakdowns. Facility maintenance companies minimize the risk of equipment failures by conducting regular inspections, proactive repairs, and adhering to preventive maintenance schedules.
This foresight ensures that operations run seamlessly, avoiding costly and unplanned downtime. A well-maintained facility or equipment is more reliable, allowing teams to focus on tasks without interruptions, meet production schedules, and deliver consistent output.
Ultimately, the commitment to proper facility maintenance translates into sustained operational efficiency, enabling businesses to meet their goals efficiently and remain competitive in their respective industries.
Cost Efficiency
Cost efficiency is a hallmark of proactive facility maintenance strategies, where addressing issues before they escalate proves more economical than reacting to emergencies. Regular, planned maintenance allows for identifying and rectifying potential problems early on, preventing them from evolving into more complex and costly issues.
Organizations can allocate resources strategically and circumvent the need for expensive replacements by controlling repair costs and avoiding unexpected breakdowns. The cost savings realized through proactive facility maintenance contribute significantly to a business’s overall financial health, fostering a sustainable and efficient approach to managing assets and facilities.
Ensuring Safety and Compliance
Safety assurance is paramount in a well-maintained environment, and regular inspections and maintenance play a crucial role in reaching this goal. Through systematic assessments, potential safety hazards are found and handled promptly, reducing the risk of casualties.
Proactive maintenance by facility management companies like Fogwing Asset+ ensures that equipment, machinery, and facilities meet or exceed safety standards and regulatory requirements. Organizations prioritizing safety through routine upkeep create a work environment where employees can confidently operate without unnecessary risks.
This commitment not only safeguards the well-being of individuals but also establishes a culture of compliance and diligence in meeting safety protocols in facility maintenance.
Enhancing Energy Efficiency
Energy efficiency is a natural byproduct of diligent facility maintenance practices. Well-maintained systems and equipment function optimally, requiring less energy to perform their tasks. Regular inspections, cleaning, and adjustments ensure machinery operates efficiently, minimizing energy wastage.
Organizations can promptly address issues such as wear and tear or malfunctions to avoid scenarios where systems consume excess energy. The result is reduced energy costs and a smaller environmental footprint. Energy-efficient operations contribute to sustainable practices, aligning with broader corporate responsibility goals while enhancing daily operations’ cost-effectiveness.
Sustainability
Sustainability and facility maintenance form a synergistic partnership where responsible practices contribute to environmental stewardship. By aligning maintenance strategies with sustainability goals, organizations can ensure the efficient utilization of resources, minimize waste, and adopt eco-friendly practices.
It may include using energy-efficient technologies, responsible waste management, and environmentally conscious procurement processes. Regular maintenance fosters a culture of longevity, emphasizing repairs and upgrades over unnecessary replacements.
By integrating sustainability into facility maintenance services, organizations contribute to a healthier planet and often realize long-term cost savings through reduced resource usage and waste output. It’s a strategic alignment that benefits both the environment and the bottom line.
Essential Facility Maintenance Practices
While entering the realm of facility maintenance, adopting fundamental practices is crucial for effective management and long-term asset preservation.
Here are some essential facility maintenance practices:
Scheduled Inspections
Conducting regular inspections forms a cornerstone of effective facility maintenance. By systematically conducting routine checks, facilities can swiftly identify potential issues before they escalate, encompassing a comprehensive review of equipment functionality and structural integrity.
These proactive examinations not only prevent unexpected breakdowns but also contribute to enhanced operational efficiency. Early detection allows for timely interventions, minimizing repair costs and ensuring the sustained reliability of assets.
Moreover, regular inspections conducted by facility maintenance companies foster a culture of preventive care, instilling a proactive mindset that safeguards facilities, promotes safety, and ultimately extends the lifespan of critical infrastructure.
Preventive Maintenance Schedule
Implementing preventive maintenance schedules is a strategic imperative in facility management. By proactively scheduling maintenance tasks for essential equipment and systems, organizations can systematically address wear and tear before it evolves into critical issues or unexpected breakdowns.
The preventive approach by facility management companies minimizes the risk of costly repairs. It ensures that assets operate optimally throughout their lifecycle. As outlined in these schedules, regular servicing, lubrication, and inspections contribute to equipment longevity, reduce downtime, and bolster overall operational efficiency.
In essence, preventive maintenance schedules are a proactive investment in reliability, cost-effectiveness, and the seamless continuity of operations.
Safety Checks
Safety checks are paramount in facility maintenance, prioritizing the well-being of occupants and compliance with safety regulations. Regular evaluations entail identifying and promptly addressing potential hazards, from electrical to structural issues.
This proactive approach mitigates the risk of accidents and ensures adherence to established safety protocols. Organizations create and maintain a secure environment through systematic safety checks, fostering a culture of diligence and compliance. Beyond regulatory requirements, prioritizing safety contributes to employee well-being, minimizes the likelihood of emergencies, and establishes a foundation for a resilient and secure working environment.
Documentation
Thorough documentation is a linchpin in effective facility maintenance, involving the meticulous recording of maintenance activities, inspections, and repairs. This comprehensive record-keeping serves as a historical log, offering information on the health and performance of assets over time. It facilitates trend analysis, anticipating potential issues based on past occurrences.
Additionally, well-maintained documentation informs future maintenance needs, ensuring that schedules are tailored to address specific equipment requirements. This organized approach enhances operational efficiency and proves invaluable for regulatory compliance and audits.
Ultimately, documentation becomes a strategic tool for informed decision-making and the sustained health of facility assets.
Training and Education
Training programs are pivotal in effective facility maintenance, empowering personnel with the skills and knowledge necessary for basic maintenance tasks and adherence to safety protocols.
By providing comprehensive training, organizations ensure that staff members are equipped to operate and maintain equipment properly and know safety procedures crucial for accident prevention.
This empowerment fosters a culture of shared responsibility for facility upkeep, encouraging proactive contributions from all team members. Well-trained personnel are not just employees; they become valuable contributors to the overall maintenance strategy, promoting a safer, more efficient, and collaborative working environment.
Why use a Facility Maintenance Checklist?
A comprehensive facility maintenance checklist is crucial for facility maintenance companies to be recognized as top-notch organizations. It ensures that all safety equipment is in good working condition and that no essential maintenance, inspections, or cleaning operations are disregarded.
The facility checklist also enables facility management companies to identify potential safety and security hazards. It helps to mitigate them with proper procedures.
It also stands as the comprehensive guide for the maintenance technician while considering the safety and security of the facility. It further enables organizations to manage essential tasks across the employees and teams involved in facility management.
It documents the work done at the organizations, which might be crucial for improving the management process or addressing the facility’s safety hazards.
What is the Facility Maintenance Checklist in the Automotive industry?
A Facility Maintenance Checklist in the automotive sector is a systematic and comprehensive tool used to manage and track facility maintenance activities within a facility or manufacturing plant that is part of the automotive industry.
This checklist is tailored to the unique needs and requirements of automotive facilities, often including complex machinery, specialized equipment, and adherence to stringent quality and safety standards.
Critical components of a Facility Maintenance Checklist in the automotive sector typically include:
- Equipment Inspection: The facility management checklist ensures peak automotive sector performance with meticulous equipment checks in facility maintenance. Regular inspections cover manufacturing and assembly machinery, including CNC machines, robotics, and automated equipment. Vigilantly monitor tool and Mold conditions, guaranteeing a seamless and efficient production process.
- Quality Control Systems: precise calibration checks on measurement and testing equipment ensure the accuracy of assets in every aspect. Verifies the functionality of quality control systems and sensors, fortifying our commitment to delivering high-performance and top-notch automotive solutions.
- HVAC and Environmental Systems: The facility maintenance checklist optimizes the working environment with meticulous attention to HVAC and Environmental Systems. Conducts thorough inspections of heating, ventilation, and air conditioning (HVAC) systems, ensuring optimal functionality. It monitors environmental control systems for precise temperature and humidity management, creating an atmosphere conducive to top-tier automotive production.
- Safety Systems: Upholding safety standards is paramount in automotive facility maintenance. Rigorously verify emergency shutdown systems, ensuring swift and secure responses. Inspect safety sensors and interlocks on machinery for optimal functionality, fortifying our commitment to employee well-being. Conduct thorough checks on fire suppression systems, providing a secure manufacturing environment.
- Materials Handling Equipment: Efficient automotive operations begin with well-maintained Materials Handling Equipment. A facility maintenance checklist enables organizations to conduct thorough inspections on forklifts, conveyor systems, and automated guided vehicles (AGVs) to ensure seamless logistics. It prioritizes performance by diligently lubricating and maintaining materials handling equipment, guaranteeing optimal functionality.
The checklist is designed to cover preventive maintenance, routine inspections, and any necessary repairs to ensure the efficient and safe operation of the automotive facility.
Adhering to a comprehensive Facility Maintenance Checklist is essential to minimize downtime, enhance productivity, maintain product quality, and comply with regulatory standards within the dynamic and demanding environment of the automotive sector.
Top Facility Maintenance Service Providers
Fogwing Asset+ boasts robust features and capabilities designed to streamline asset maintenance processes comprehensively. It covers preventive maintenance, work order management, asset tracking, and reporting, providing a holistic solution for facility management software needs.
The platform’s versatility is evident in its ability to cater to various maintenance requirements. The user experience with Fogwing Asset+ is highly intuitive and user-friendly, enhancing the efficiency of facility maintenance processes. The platform offers a well-designed interface that is easy to navigate, enabling maintenance technicians to access and utilize its various tools quickly.
Integration is a crucial strength of Fogwing Asset+, a smart CMMS and one of the top facility maintenance companies. It seamlessly integrates with other systems, and its compatibility with IoT devices and sensors enables real-time monitoring and maintenance, contributing to proactive asset management.
Regarding reliability and performance, Fogwing Asset+ is recognized for its stability and high responsiveness. The platform boasts impressive system uptime, quick response times, and overall robust performance, providing users with a dependable solution for facility maintenance.
Conclusion
Facility maintenance is a dynamic field that requires attention to detail, proactive planning, and a commitment to creating safe and efficient spaces. For beginners, developing a basic understanding of the importance of facility maintenance services and implementing essential practices will help the organization succeed in facility management.
By embracing a preventive mindset and staying informed about industry best practices, beginners can confidently navigate the world of facility maintenance services, ensuring the built environment’s longevity and optimal performance.
In conclusion, Fogwing Asset+, a cmms software, is a comprehensive, user-friendly, and scalable solution with seamless integration capabilities, high reliability, excellent customer support, and industry recognition. Its cost-effectiveness further strengthens its appeal, making it a top choice for those seeking an advanced facility maintenance and asset management platform.
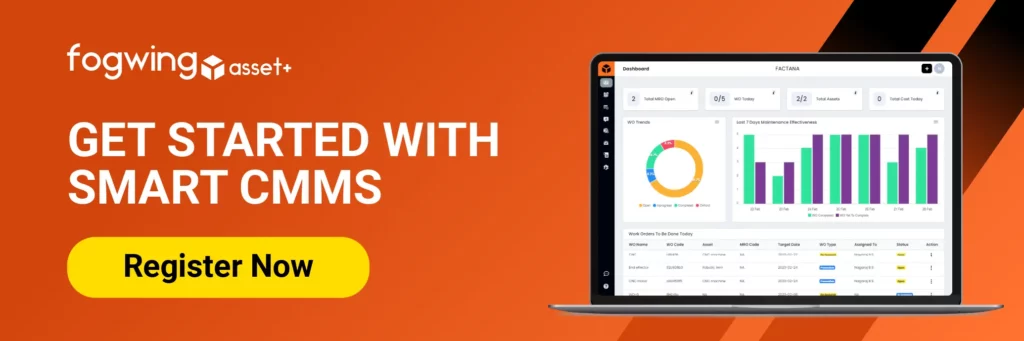