In the dynamic manufacturing world, efficiency is the heartbeat of successful manufacturing operations. Optimizing production processes is required to stay competitive and meet customer demands. One crucial aspect of this optimization is the management of Idle Time.
In today’s fast-paced world, in the manufacturing industry, every second counts, where efficiency is vital. That’s why we’re here to unveil game-changing solutions to revolutionize your operations.
This blog post will discuss how manufacturing processes can benefit from various technological tools to minimize waiting time and maximize productivity.
Join us on this journey to explore how leveraging technology can reduce the causes of idle time, enhance productivity, and set your business on the path to success.
What is Idle Time?
Idle Time, also called the waiting time in manufacturing, refers to when a system, machine, or individual remains inactive, without productive involvement, or in waiting time. It is the time lost due to obstacles at work where the employees and assets are available to work but cannot be productive.
In many contexts, it can manifest differently, such as the downtime of a manufacturing machine waiting for the next task, the time when a computer processor is not executing any charges, or the intervals when an employee is not actively working on assigned responsibilities. At the same time, idle time is distinct from planned or unplanned downtime.
In summary, the difference lies in the possibility of performing work. It implies that you could have got an output if performed. At the same time, downtime refers to not completing the job for various reasons. Understanding these variance concepts is crucial for managing organizational resources and optimizing productivity.
Types of Idle Time in Manufacturing
Idle tyme in manufacturing processes is a significant issue that can negatively impact organizations, causing decreased productivity, increased costs, and missed opportunities. Causes of idle time can lead to various factors like machine breakdowns, waiting for materials or parts, and lack of coordination among workers.
Organizations must understand the different types of idle tyme that may occur in manufacturing processes to reduce its effect effectively. Each waiting time variance has its unique causes and potential solutions. By understanding these different types of industrial idle time, organizations can better identify their root causes and implement effective strategies for reducing them.
Manufacturers can utilize various advanced maintenance management software like Fogwing Asset+, a smart CMMS software, to reduce the waiting time for the equipment or assets in the organization.
Equipment Idle Time:
Equipment idle time occurs when assets or machines cannot perform their intended functions due to breakdowns or maintenance issues. The cause will be wear and tear of organizational machines, inadequate maintenance practices, or unexpected malfunction.
Asset downtime is particularly problematic as it directly affects production output if not addressed promptly. To reduce industrial idle time, organizations can leverage technology such as predictive maintenance systems that use real-time data and analytics to predict potential breakdowns before they happen.
Maintenance software like Fogwing Asset+ can schedule maintenance activities at optimal times and proactively address any issues to prevent unplanned downtime.
Material Idle Time:
Material idle tyme occurs when there is a delay in receiving necessary materials for production processes. It might be due to supply chain disruptions, quality control issues with incoming materials, or inefficient inventory management practices.
One way to reduce material idle time variance is through the implementation of just-in-time (JIT) inventory strategies, where materials ordered and delivered are needed rather than stockpiled. It requires close collaboration and coordination with suppliers to ensure a constant flow of materials without unnecessary delays for effectively working on idle assets.
Fogwing Asset+, a smart CMMS software, is an advanced platform offering advanced parts inventory and supplier management features.
Worker Idle Time:
It happens when employees are not engaged in productive tasks, often due to poor scheduling or coordination practices. This waiting time can result from factors such as gaps in the production schedule, inefficient work processes, and lack of cross-training among workers.
To address these causes of idle time, manufacturers can implement employee training programs to enhance their skills and enable them to perform various tasks within the production process. It ensures that workers always have something productive to do, even during slower periods.
Organizational Idle Time:
Organizational idle tyme refers to any delays that stem from mismanagement or lack of communication within the organization. It could include problems with scheduling, inefficient use of resources, and poor coordination between different departments or teams.
Adopting lean manufacturing principles is one effective way to reduce these types of industrial idle time. These methodologies focus on eliminating waste and enhancing efficiency across all aspects of the manufacturing process, including organizational processes and procedures.
The Causes of Idle Time in Manufacturing:
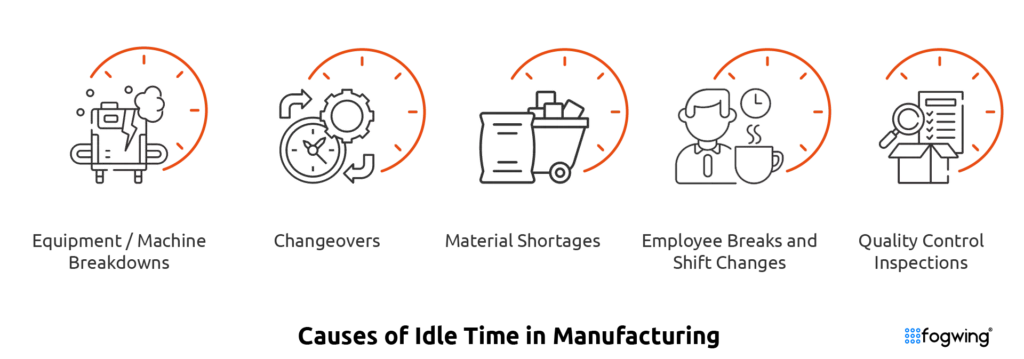
- Equipment / Machine Breakdowns:
Machine breakdown often results in unplanned idle time in manufacturing. It encompasses mechanical failure, electrical issues, and technical glitches that interrupt the production process in industries.
Proactive measures like predictive maintenance techniques, regular preventive maintenance, and system updates are crucial to mitigate these challenges. Rapid response and repairs minimize equipment downtime, backed by well-equipped maintenance teams and parts availability.
Conducting root cause analyses after breakdowns and investing in redundancy with backup systems or components will help organizations understand the causes of idle tyme in assets and enhance resilience.
- Changeovers:
Planned idle time in manufacturing linked to scheduled maintenance and machine setup for new production works frequently. Machines or assets often need to be reconfigured or adjusted when switching from producing one product to another.
Planned industrial idle tyme is linked to scheduled maintenance and machine setup for the new production runs. Even though this kind of downtime is deliberate, it impacts overall productivity. Efficient planning and streamlined changeover processes can reduce the impact of the scheduled idle time.
Strategic scheduling of the maintenance during periods of lower demand, utilizing predictive maintenance to anticipate issues, and optimizing machine setup procedures can streamline these processes in manufacturing.
- Material Shortages:
Material Shortages can pose a significant risk to manufacturing, resulting in idle time. The lack of essential raw materials or parts required for maintenance can cause industrial idle tyme.
Effective inventory management and supplier collaboration can help organizations prevent material shortages and keep production running smoothly.
A well-orchestrated supply chain ensures that production lines remain operational, reducing the likelihood of interruptions due to material scarcity and optimizing overall manufacturing efficiency.
- Employee Breaks and Shift Changes:
Schedule breaks, shift changes, and other personal-related factors related to employees can contribute to idle time in an organization. Proper workforce management and scheduling can help organizations smoothly transition between shifts and minimize downtime.
Strategically aligning break time with production breaks, implementing staggered shift changes, and employing predictive analytics to forecast staffing needs during peak periods are essential strategies.
Additionally, cross-training employees to handle idle assets and multiple tasks enhances flexibility, reducing downtime during shift changes. Fostering the adaptive work culture and leveraging technology for agile maintenance scheduling enable manufacturers to mitigate the impact of employee-related idle time, promoting a more efficient and continuous production flow.
- Quality Control Inspections:
The necessity for quality checks can introduce temporary halts in production, contributing to industrial idle time in manufacturing. Although the contribution of quality checks is vital in ensuring product quality, optimizing the inspection process is essential to minimize downtime.
However, if these quality control checks are not integrated into production effectively, they can lead to unnecessary idle tyme. Quality control methods such as in-line testing or automated inspection systems can streamline the verification of product standards without disrupting production.
Striking a correct balance between rigorous quality assurance and a streamlined inspection process is crucial for reducing the causes of idle time associated with quality checks while upholding the product integrity of idle assets.
Strategies to Minimize Idle Time:
- Predictive Maintenance:
Embrace the power of predictive maintenance by leveraging state-of-the-art sensors and data analytics, allowing for a proactive approach to foster idle asset failures. It anticipates the issues with assets before they escalate into idle time. It enables timely interventions, preventing unplanned downtime and enabling an uninterrupted production workflow.
Predictive maintenance optimizes operational efficiency, reduces repair costs, and extends the idle asset lifespan by harnessing real-time insights into asset health. The predictive maintenance approach transforms the manufacturing landscape, promoting a seamless synthesis of technology and maintenance practices for a more resilient and agile production environment.
- Lean Manufacturing Principle:
Lean manufacturing principles aim to optimize processes and eliminate waste. Techniques like Single-Minute Exchange of Die (SMED) focus on reducing changeover times to minimize idle time during transitions between diverse products. It simplifies transitioning between manufacturing tasks, reducing downtime and improving efficiency.
Embracing lean manufacturing enables organizations to cultivate a culture of continuous improvement, honing their ability to identify and eradicate inefficiencies. Lean manufacturing enhances idle asset productivity and fortifies manufacturing systems’ adaptability, fostering resilience in the face of dynamic production demands.
- Effective Workforce Management:
Having effective workforce management is pivotal for an organization, as it offers the scheduling of breaks, shifts, and training sections while maintaining an uninterrupted production flow and reduced Idle Time.
Cross-training employees to handle diverse tasks fosters a versatile workforce and is a robust resistance against potential bottlenecks arising from skill gaps. Organizations can build resilient teams by aligning workforce dynamics with production demands and investing in skill diversification.It enables teams to adapt to evolving operational requirements, bolster productivity, and mitigate industrial idle time.
- Strategic Inventory Management:
Efficiently managing inventory mitigates idle time by ensuring an optimal stock of raw materials and components, preventing delays caused by equipment shortages. Collaborative partnerships with suppliers and implementing the inventory systems just in time contribute to a lean and responsive production process.
It reduces the likelihood causes of idle tyme due to insufficient parts or equipment. Organizations can maintain a continuous workflow by synchronizing inventory levels with the production requirements, reducing production interruption, and enhancing overall efficiency. This strategic approach fosters a dynamic and adaptable production environment and reduces industrial idle time.
- Integrated Quality Control:
Embedding quality control measures directly into the production process mitigates idle time by eliminating the necessity for distinct inspection stages.
This integrated approach ensures continuous monitoring of product quality without introducing unnecessary delays.
By seamlessly weaving quality control into each production step, organizations enhance efficiency and streamline the workflow, minimizing pauses associated with traditional inspection methods.
This strategic integration contributes to the timely identification and rectification of quality issues in idle assets.
It fosters a production environment where the pursuit of quality aligns seamlessly, intending to reduce industrial idle time and promote a more agile and responsive manufacturing paradigm.
The Importance of Minimizing Idle Time
Minimizing idle time has become crucial in today’s fast-paced and digital business environment. With the rapid development of Industry 4.0 technologies, increased customer demands, and heightened global competition, companies must continuously seek ways to improve their processes and reduce costs.
It is where technology comes into play – manufacturers can effectively minimize industrial idle time and optimize their operations by implementing the right tools and strategies.
One of the critical benefits of minimizing waiting time is its direct impact on production costs. When machines or resources are not being used efficiently, it results in wasted workforce hours and higher overhead expenses.
It directly affects the bottom line of any business and can lead to decreased profitability. Manufacturers significantly reduce operating costs and improve profitability by optimizing idle time through technology.
Additionally, minimizing idle tyme also leads to improved delivery times. In today’s age of instant gratification, customers expect quick turnaround times when receiving ordered products.
When there is excessive downtime in a manufacturing process due to idle time, it can lead to delayed deliveries, which can adversely affect customer satisfaction levels. Businesses can use technology to reduce idle tyme and streamline processes to meet customer expectations and maintain a positive brand image.
Idle Time Calculation in Manufacturing
The idle time formula is essential for organizations to optimize production processes and reduce costs. It is a mathematical equation calculating when a machine or equipment is not used during a specified period, usually hours or minutes.
The formula considers various factors such as scheduled maintenance, unplanned downtime, changeovers, and breaks. By understanding and utilizing this formula, manufacturers can identify assets where productivity can be improved and take action to reduce idle tyme.
The idle time formula can be written as follows:
Idle Time = Total Downtime / Total Production Time x 100%
To better understand this formula, let’s break down each component:
1. Total Downtime: This refers to the sum of all non-productive periods within a specified timeframe. These may include scheduled maintenance activities like cleaning or equipment repairs, unplanned downtimes due to breakdowns or malfunctions, changeovers between different products or batches, and even personal breaks taken by employees.
2. Total Production Time: In the idle time formula, the total duration that the production process was active within the same timeframe considered for calculating downtime. It includes both planned and unplanned production times.
3. Percentage: The resulting value multiplied by 100% gives us the idle time percentage during a specific period.
Manufacturers must track planned and unplanned downtime separately to calculate their overall industrial idle time percentage accurately. By doing so, they can pinpoint which types of breakdowns or downtime are causing the most significant impact on their production and take measures to reduce them.
Furthermore, it is essential to track this metric regularly, preferably weekly or monthly. It will help businesses identify patterns and trends in idle times, understand the root causes, and make necessary adjustments to improve overall efficiency.
In conclusion, the idle time Calculation provides valuable insights into a manufacturer’s production processes. By using this formula to track and monitor downtime events, businesses can identify areas for improvement, optimize their processes, and ultimately increase productivity and profitability.
The Role of Technologies in Minimizing Idle Time
Technology continuously evolves and is essential for reducing idle time in manufacturing processes. With the right solutions and strategies, manufacturers can overcome unexpected breakdowns, material shortages, and human errors to achieve higher efficiency and productivity.
The Fogwing Asset+, a smart CMMS platform, is one such platform that enables manufacturers to reduce the waiting time for idle assets. The Fogwing Asset+ platform involves various advanced, cutting-edge maintenance management technologies that can help factories minimize waiting time.
Here are a few technologies integrated into Asset+, a smart CMS software:
- Real-Time Monitoring Systems:
Real-time monitoring systems use sensors and data analysis software to track machine performance and find potential issues that could lead to idle time. These systems continuously monitor equipment parameters such as temperature, speed, vibration, etc., providing real-time alerts if any deviations occur.
For instance, automated monitoring systems can detect abnormal vibrations in idle assets that indicate a potential breakdown or faulty component. Maintenance personnel can then take necessary actions to prevent downtime, reducing idle time.
- Automated Material Handling Systems:
Manual handling of materials significantly contributes to idle time in manufacturing processes. With automatic material handling systems, manufacturers can minimize the time spent loading and unloading products or raw materials.
Robotic material handling solutions have advanced significantly in recent years, offering increased flexibility and precision compared to traditional conveyor systems. These automated systems can handle various idle assets, reducing workers’ time on manual tasks and freeing up time for more value-added activities.
- Internet of Things (IoT) Solutions:
IoT technology integrates physical machines with digital sensors and communication networks, enabling them to collect and exchange data. In manufacturing, IoT solutions can monitor equipment performance, track inventory levels, and optimize production schedules based on demand.
For example, an IoT-enabled system can automatically order raw materials when inventory levels are low, ensuring no production delays due to a lack of supplies. It minimizes idle time caused by waiting for materials to arrive or manually placing orders.
- Real-time Monitoring:
The real-time monitoring system of the Fogwing Asset+ platform works alongside humans in manufacturing, taking over repetitive and physically demanding tasks. It enables human workers to focus on more complex and critical operations that require decision-making skills.
By incorporating a real-time monitoring system, manufacturers can reduce Industrial idle time caused by human fatigue, breaks, and manual errors. These real-time monitoring technologies can work 24/7 without rest, minimizing downtime and increasing productivity.
Conclusion
In conclusion, technology has been established to be a pricey asset in reducing idle time in manufacturing processes. Companies can significantly increase efficiency and productivity by implementing real-time data tracking, predictive maintenance systems, and automation solutions while minimizing costly downtime. Innovations like the Internet of Things (IoT) and artificial intelligence offer endless possibilities for streamlining operations and optimizing performance.
Embracing these advancements is crucial for manufacturers looking to stay competitive in today’s fast-paced market. With proper implementation and continuous improvement efforts, leveraging technology can save costs and enhance business profits. It’s time to embrace technology and take your manufacturing processes to the next level with idle assets.
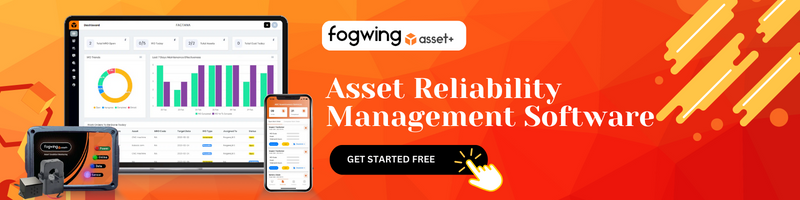