Are you ready to revolutionize your manufacturing processes and boost productivity? Look no further! In today’s fast-paced world, cycle-time has emerged as a crucial Key Performance Indicator (KPI) that can make or break the success of any manufacturing operation. Whether you’re a seasoned professional or just dipping your toes into the manufacturing industry, understanding why cycle-time matters is essential for streamlining processes, reducing lead time, and maximizing profitability. Join us as we dive deep into this captivating topic and uncover the secrets behind how an optimized cycle time can catapult your business to new heights!
What is Cycle Time in Manufacturing?
It is one of the most important metrics in manufacturing, and it plays a critical role in ensuring the efficiency and productivity of a production process. In simple terms, cycle-time refers to the total time it takes for a product to move through all manufacturing stages and become ready for delivery. It starts when an order is received and ends when the finished product is shipped or delivered to the customer.
Understanding cycle-time isn’t just about tracking speed; it’s about assessing efficiency, resource allocation, and productivity optimization. It provides a foundational insight into process performance and offers a roadmap for refinement.
Cycle Time vs Lead Time
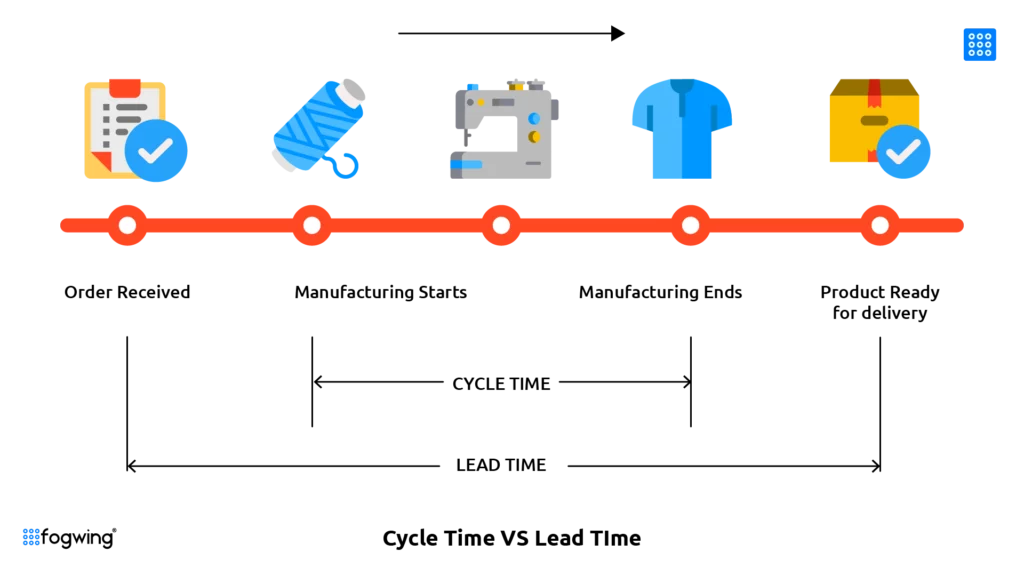
In manufacturing and process management, it’s imperative to grasp the differences between Cycle-Time and Lead Time. Cycle-Time measures the time required to complete a single task or unit, making it a valuable tool for identifying and enhancing the efficiency of specific activities within a process. Conversely, Lead Time takes a more encompassing perspective, considering the entire timeline, from the initiation of a process to its ultimate culmination. This broader view is instrumental in ensuring customer satisfaction by streamlining production planning and optimizing supply chain management. While Cycle-Time targets internal efficiency, Lead Time provides a comprehensive picture of the end-to-end process and its critical role in timely delivering products or services.
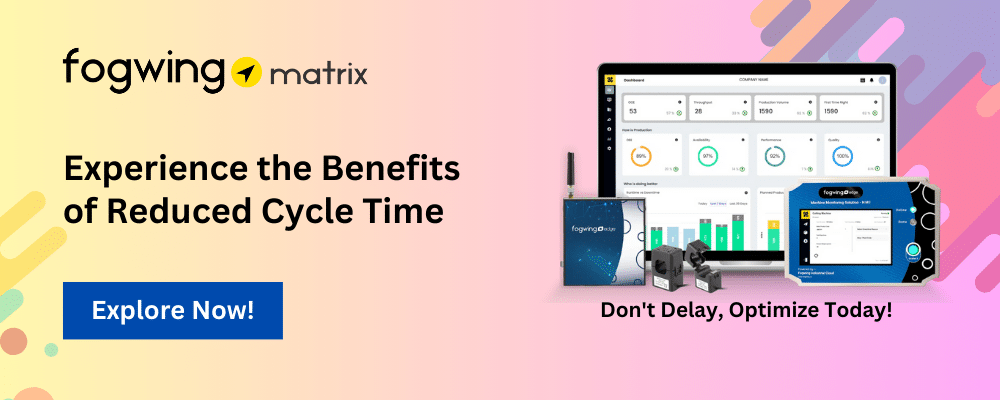
Why Cycle Time is critical?
It is one of the critical production KPIs in manufacturing operations because it directly impacts delivery efficiency, cost, quality, and customer satisfaction. Manufacturers use this metric to optimize their production processes, reduce lead times, and remain competitive in an increasingly fast-paced and demanding market. It is deemed a critical KPI in manufacturing for many compelling reasons.
Efficiency Gauge: It functions as an unambiguous gauge of process efficiency, offering direct insights into the pace and effectiveness of operations.
Resource Management: It casts light on the judicious utilization of resources, including labor, machinery, and facilities, leading to optimized resource allocation.
Waste Mitigation: Optimizing cycle-time helps reduce waste by minimizing unnecessary delays and resource consumption, thereby contributing to cost savings.
Customer Satisfaction: Shorter cycle times translate into faster product or service delivery, positively impacting customer satisfaction.
Competitive Edge: A manufacturer with a shorter cycle-time gains a competitive benefit due to its ability to respond swiftly to market shifts and customer needs.
Read this blog to learn about essential KPIs in manufacturing Key Manufacturing KPIs To Be Monitored |Fogwing.io
What is the difference between Takt Time and Cycle Time?
Cycle-time and Takt time are closely related yet fundamentally distinct concepts:
Cycle-Time: As previously elucidated, it pertains to the duration for a unit to navigate a particular manufacturing process. It primarily focuses on quantifying the efficiency and pace of the process itself.
In contrast, takt time relates to the production rate necessary to meet customer demand. It is calculated by dividing the available production time by the customers’ needs, establishing the required production rate to align with demand.
The cardinal distinction lies in cycle time, representing the actual duration of a unit’s progress through a process. In contrast, takt time delineates the production pace necessary to meet customer demand effectively.
To learn about Takt time in detail, read this Understanding Takt Time And Optimizing Production | Fogwing.io
How to calculate Cycle Time?
Accurate calculation and measurement of cycle time encompass several steps:
Step 1: Process Selection: First, identify the specific process or task to be measured.
Step 2: Timer Initiation: Start the timer when the process begins for a unit.
Step 3: Timer Termination: Cease the timer when the unit concludes the process and is poised to advance to the subsequent phase.
Step 4: Unit Count: Ascertain how many units transited during the measurement period.
Step 5: Cycle Time Computation: Compute the cycle-time by dividing the total time by the number of units. The cycle time formula is as follows:

It’s imperative to note that measuring cycle-time necessitates consistent data collection and analysis. In contemporary manufacturing, software, and automation systems often provide actual cycle time measurements, yielding precise and up-to-date data to guide process improvements. Fogwing Matrix comes as a savior in this aspect, which helps to automate the data collection, analysis, and the entire production cycle-time measurement.
Factors Affecting Cycle Time in Manufacturing
It is an essential metric for measuring the efficiency and productivity of any manufacturing process. It refers to the total time to complete a production cycle, from receiving the raw materials to producing the final product. The faster a company can produce high-quality goods, the more competitive it will be in their industry. However, several factors can affect manufacturing cycle time, ultimately impacting a company’s overall performance.
1. Production Equipment and Technology:
The type and quality of production equipment play a significant role in determining cycle-time. Outdated or malfunctioning machinery can cause delays and reduce productivity. On the other hand, investing in advanced technology such as automation and robotics can significantly speed up production processes.
2. Material Availability:
One of the most significant factors affecting manufacturing cycle-time is material availability. A delay or shortage of raw materials will directly impact the production schedule, causing longer lead times and inefficiencies. Manufacturers must have reliable suppliers and proper inventory management systems to ensure an uninterrupted supply chain.
3. Labor Force and Training:
Employee skill level and training also play a vital role in reducing cycle time in manufacturing processes. Skilled workers who are trained in using advanced equipment can perform tasks more efficiently, resulting in faster production cycles.
Importance of Improving Cycle Time
The importance of cycle-time improvement in manufacturing is paramount for several reasons:
- Cost Reduction: Shortening cycle times directly leads to lower production costs, bolstering overall profitability.
- Resource Optimization: Efficient resource allocation results in superior labor, machinery, and materials utilization.
- Rapid Responsiveness: Swift responses to market fluctuations and customer demands confer a competitive edge.
- Waste Minimization: Minimizing idle time and excessive resource usage is synonymous with waste reduction.
- Enhanced Quality: Shorter cycle times require more frequent quality checks, obviating defects and recalls.
- Customer Contentment: Accelerated product or service delivery translates into heightened customer satisfaction.
- Enhanced Adaptability: Manufacturers equipped with shorter cycle times possess the capacity to promptly adapt to shifting production requirements and unforeseen disruptions.
Strategies for improving Cycle Time
In this section, we will discuss a few effective strategies for reducing cycle-time in manufacturing. Implementing these strategies can help businesses improve their production process and achieve better results.
1. Identify Bottlenecks and Streamline Processes: The first step towards reducing cycle-time is to identify any bottlenecks or delays in your production process. Inefficient processes, lack of resources, or equipment breakdowns could cause this. Once these issues are identified, steps should be taken to streamline processes and eliminate unnecessary steps.
2. Implement Lean Manufacturing: Lean principles focus on minimizing waste and maximizing value-added activities in the production process. Manufacturers can significantly reduce cycle times by implementing lean techniques such as 5S methodology (Sort, Set-in-order, Shine, Standardize, Sustain) and Just-in-Time (JIT) inventory management by eliminating non-value-adding tasks and maintaining optimal inventory levels.
3. Invest in Automation: With advancements in technology, automation has become an essential tool for improving cycle times in manufacturing. By automating repetitive tasks using robotics or other automation technology, manufacturers can significantly reduce processing times while increasing accuracy and efficiency.
How Fogwing Matrix helps to Improve Cycle Time?
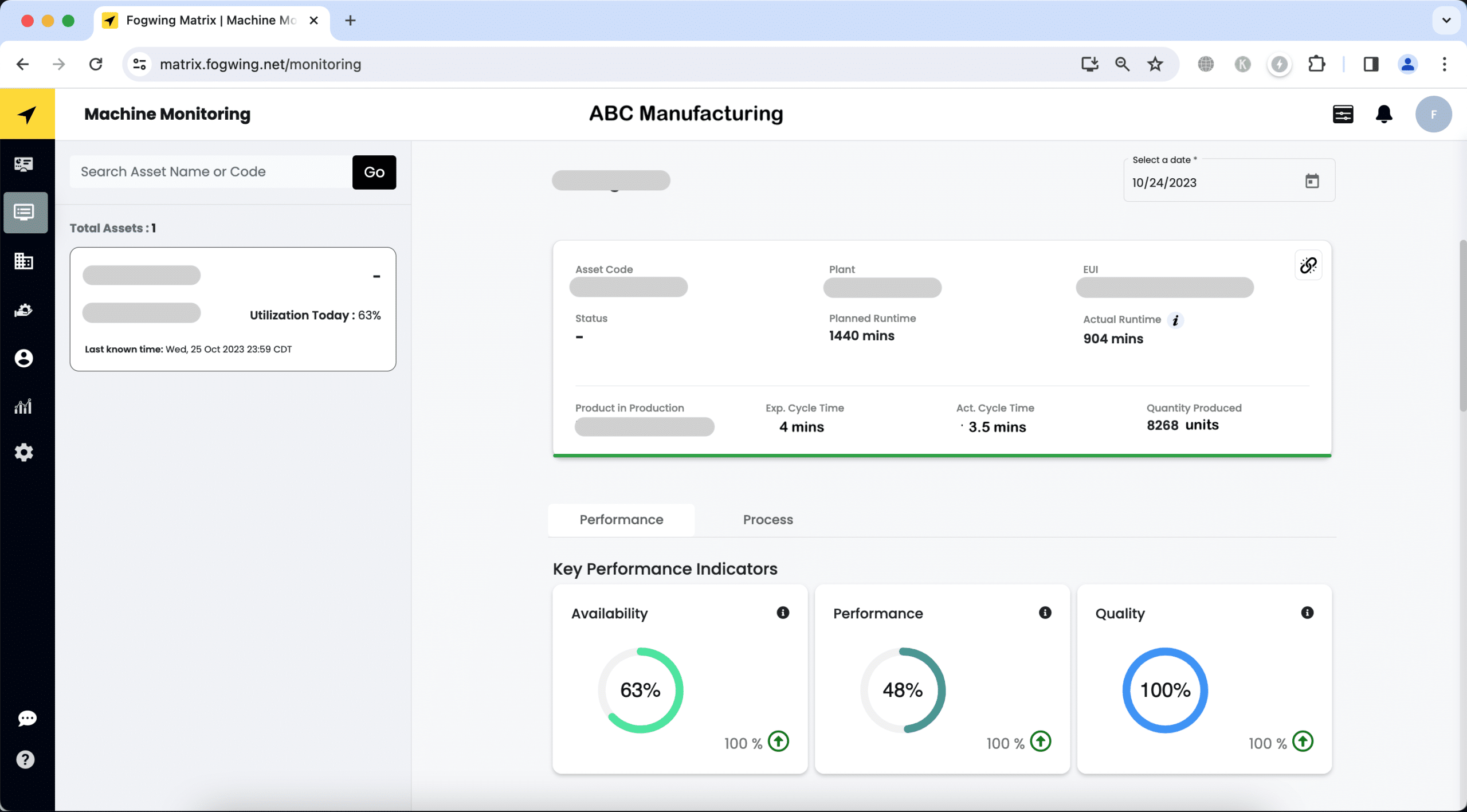
The Fogwing Matrix plays a pivotal role in enhancing cycle-time within manufacturing processes. By seamlessly integrating IoT sensors, data analytics, and real-time insights, it enables manufacturers to optimize production efficiency.
Fogwing Matrix offers real-time data on machine performance, helping identify bottlenecks and inefficiencies promptly. This data empowers operators to make informed decisions, reducing downtime and speeding up processes.
Secondly, preventive maintenance capabilities anticipate equipment failures, allowing timely repairs, preventing unexpected breakdowns, and minimizing unscheduled downtime.
Furthermore, Fogwing’s analytics tools provide actionable insights into production trends, enabling continuous process improvement and operational efficiency. With this data, manufacturers can fine-tune their operations, streamline workflows, and reduce unnecessary delays.
In summary, Fogwing Machine Monitoring improves cycle-time by ensuring machines operate at peak efficiency, minimizing downtime, and facilitating data-driven process optimization. This not only increases productivity but also leads to cost savings and enhanced overall manufacturing competitiveness.
To learn about how Fogwing helps in enhancing Overall Operations Effectiveness (OOE), read this blog. Understanding OOE : Key Concepts And Benefits | Fogwing.io
Conclusion
As we can see, cycle-time is a critical KPI for manufacturing companies as it directly impacts the efficiency and productivity of their operations. By tracking and reducing cycle times, manufacturers can reduce costs, increase output, and improve customer satisfaction. Businesses need to monitor this metric and implement strategies to optimize it regularly. With an emphasis on continuous improvement and lean principles, manufacturers can use cycle time as a key measure of success in today’s competitive market.
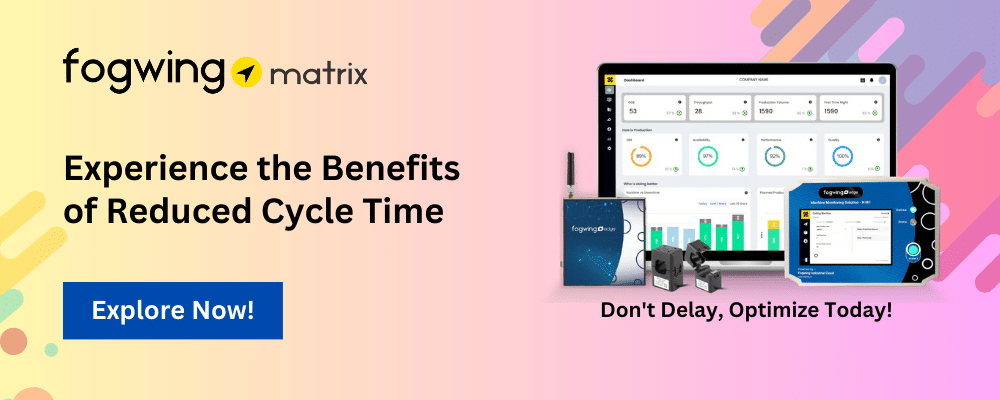