CNC (Computer Numerical Control) machines are critical to modern manufacturing, as they allow for precision and efficiency in various industries. To ensure that these CNC machines have a long life and perform at their best, it is essential to establish a comprehensive CNC machine maintenance routine as preventive maintenance. This guide will cover the specifics of maintaining different types of CNC machines and their preventive maintenance differences.
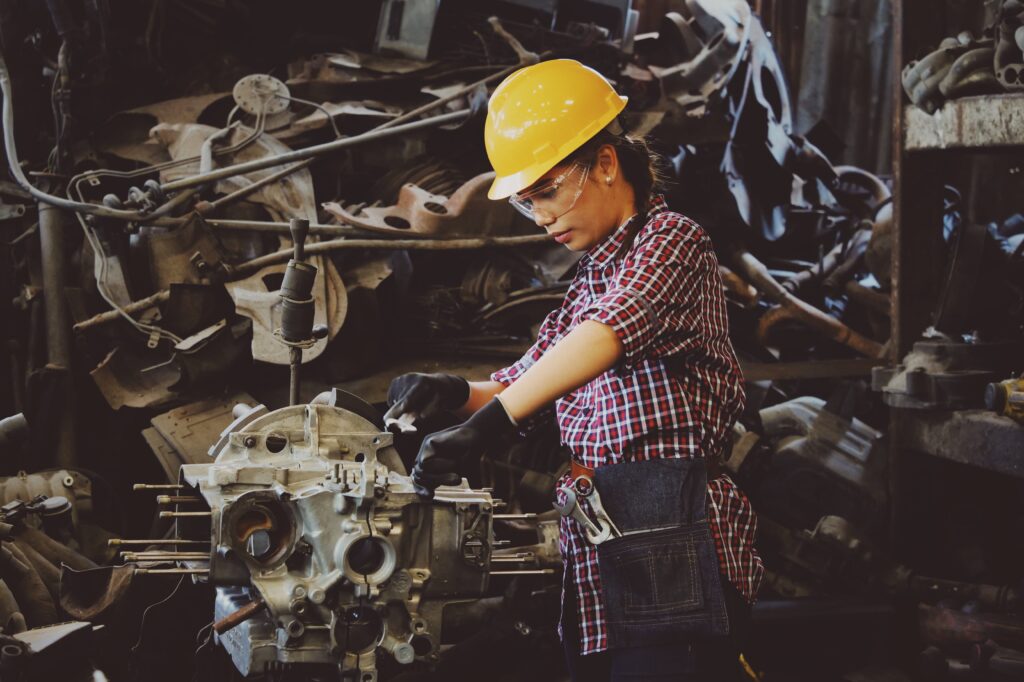
Understanding CNC Machine Types:
The following are some common types of CNC machines used in the manufacturing environment:
1. Milling Machines:
Milling CNC machines are widely used for cutting and shaping materials. CNC Maintenance for milling machines often involves careful inspection of the spindle, tool holder, and guide rails. Regular lubrication and monitoring of coolant systems are crucial to prevent overheating and maintain the machine’s accuracy.
2. Turning Machines:
CNC turning machines are employed for shaping cylindrical components. Maintenance for turning machines focuses on the spindle, turret, and tailstock. Regular checks on tool holders, coolant systems, and the accuracy of the lathe’s movements are essential for optimal performance.
3. Routing Machines:
CNC routing machines are utilized for cutting and shaping wood, plastic, and composites. Maintenance involves regularly checking the router bits, vacuum, and dust extraction systems. Keeping the guide rails clean and well-lubricated is crucial to prevent wear and maintain precision.
4. Plasma and Laser Cutting Machines:
CNC machines for plasma and laser cutting require specific maintenance due to the intense heat generated during the cutting process. Regularly inspecting and cleaning the cutting nozzles, checking gas pressures, and ensuring proper ventilation is vital for these machines. Also, maintaining the integrity of laser optics is crucial for laser-cutting machines.
Learn about effective preventive maintenance guide
Maintenance Differences Across CNC Machine Types:
CNC maintenance varies depending on the type of CNC machines, operating procedures, materials in production, tools’ life terms, etc.
1. Tooling Considerations:
CNC machines utilize various tools, such as milling cutters, lathe tools, or laser heads. Understanding the specific maintenance requirements of each tooling system is crucial. For instance, milling tools may need more frequent wear and tear checks than laser cutting heads.
2. Coolant and Lubrication Systems:
The type of material being processed and the cutting method influence the coolant and lubrication requirements. While milling machines may require a coolant system to manage heat generated during cutting, turning machines might rely more on efficient lubrication systems. Understanding these nuances is key to effective maintenance.
3. Environmental Considerations:
CNC machines operating in different environments face unique challenges. For instance, a milling machine in a metalworking shop may encounter more metal shavings and coolant residue, necessitating more frequent cleaning. On the other hand, a CNC router in a woodworking shop may face challenges related to wood dust and chip accumulation.
4. Electronics and Software Updates:
CNC machines are driven by sophisticated software and electronics. Regularly updating the software and ensuring the health of electronic components is critical for all types of CNC machines. However, the specific software used and the complexity of electronic systems may vary, requiring tailored maintenance approaches.
How to do Maintenance of CNC machine:
Regular maintenance is the key to preserving the efficiency and accuracy of CNC (Computer Numerical Control) machines. This comprehensive checklist guides operators and maintenance personnel to keep CNC machines in optimal condition. Customize the checklist based on your machine’s specific requirements and manufacturer recommendations.
Learn about various preventive maintenance checklist for CNC machines.
Daily Maintenance:
1. Visual Inspection:
– Check for loose or damaged components, including bolts, nuts, and fasteners.
– Inspect cables and wires for signs of wear or damage.
2. Cleanliness:
– Remove accumulated dust, chips, and coolant residue from the machine surfaces.
– Clean the tool changer and ensure it operates smoothly.
3. Coolant System:
– Check coolant levels and top up if necessary.
– Inspect coolant filters and replace them as needed.
– Verify the proper functioning of the coolant pump.
4. Lubrication:
– Check and replenish lubricant levels in all designated points.
– Ensure that lubrication systems are functioning correctly.
5. Tool Inspection:
– Inspect cutting tools for wear, damage, or chipping.
– Replace or re-sharpen tools as necessary.
– Check tool holders and tighten any loose components.
Weekly Maintenance:
1. Spindle Check:
– Inspect the spindle for any unusual noises or vibrations.
– Check for signs of wear or damage on the spindle.
2. Axis Lubrication:
– Verify that all axes are well-lubricated according to the manufacturer’s guidelines.
– Clean and grease linear guides and ball screws.
3. Electrical Components:
– Inspect wiring and connections for signs of wear or damage.
– Check emergency stop buttons and other safety features.
4. Backup CNC Programs:
– Regularly back up CNC programs and machine parameters.
– Store backups in a secure location to prevent data loss.
Monthly Maintenance:
1. Tighten and Adjust:
– Perform a comprehensive check of all machine components and tighten any loose parts.
– Adjust gibs and slides to maintain optimal clearances.
2. Coolant System Maintenance:
– Clean or replace coolant filters.
– Inspect and clean the coolant tank and lines.
3. Inspect Way Covers:
– Check way covers for any damage or obstruction.
– Clean and lubricate as needed.
4. Check for Software Updates:
– Ensure that CNC software is up to date.
– Update the operating system and any associated software as recommended.
Quarterly Maintenance:
1. Axis Calibration:
– Perform axis calibration to ensure accurate machine movements.
– Check and adjust backlash if necessary.
2. Inspect Hydraulic Systems (if applicable):
– Check hydraulic systems for leaks and proper pressure.
– Inspect hoses and connections for wear.
3. Review Machine Logs:
– Analyze machine logs for any recurring issues or error messages.
– Address any patterns of abnormal behavior.
Annually or as Recommended by the Manufacturer:
1. Spindle Maintenance:
– Schedule professional spindle maintenance, including bearing checks and replacements.
– Balance the spindle if required.
2. Ball Screw Inspection:
– Inspect ball screws for wear and backlash.
– Replace ball screws if necessary.
3. Replace Filters:
– Replace air filters and other filtration systems as recommended.
– Ensure proper ventilation for electronics.
Remember to refer to your CNC machine’s specific user manual and the manufacturer’s guidelines for detailed instructions on maintenance procedures. Regular and proactive maintenance ensures your CNC machine’s longevity and enhances its overall performance and reliability.
Learn about total productive maintenance (TPM) practice.
Fogwing CMMS Maintenance Software for CNC Machine Maintenance:
Fogwing CMMS emerges as a cutting-edge maintenance software designed to transform CNC machine maintenance and inspection, ensuring optimal performance, reducing downtime, and extending the lifespan of the equipment.
Fogwing CMMS software provides the following features to manage CNC maintenance operations effectively.
- Automated Preventive Maintenance Schedule
- CNC category-based maintenance planning
- Supports the create inspection, fault, and on-demand maintenance orders
- Provides comprehensive CNC Maintenace Checklist
- IoT-driven condition or predictive maintenance for CNC
Conclusion:
CNC machine maintenance is not a one-size-fits-all endeavor. Understanding maintenance nuances across different types of CNC machines is crucial for ensuring their longevity and optimal performance. By tailoring maintenance practices to the specific needs of each machine type, manufacturers can minimize downtime, maximize efficiency, and prolong the lifespan of their CNC equipment. Regular inspections, attentive cleaning, and adherence to manufacturer recommendations will keep CNC machines running at their peak across diverse manufacturing environments.
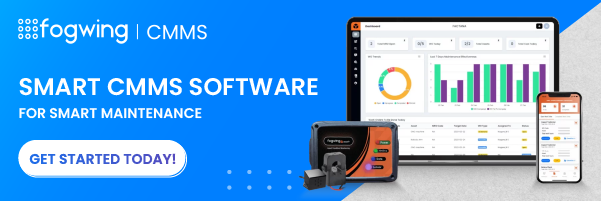