What is Factory 4.0?
The Factory 4.0 concept is a subset of industry 4.0 aka Industrial Transformation that has embraced the latest innovations in the field of advanced industrial-technological. The rapid growth of digital transformation is gaining ground and has been expanding its footprint in all aspects of businesses. With the rise of the fourth industrial revolution (Industry 4.0), manufacturing industries are upgrading themselves in digital technologies to be more dapper, flexible, and faster in every viable way.
Factory 4.0 is an innovation strategy that would create a productive transformation from traditional approach to modern factory operations. It helps traditional factories adopt the latest technologies that improve efficiency and productivity. The conventional linear operations in manufacturing sectors are slowly moving away, providing a way for an interconnected digital supply network.
The idea of the interconnected digital system network is gaining importance in industry 4.0. Factory 4.0 meaning empowers the concept of interconnected and intelligent manufacturing. Factory 4.0 solution enables the setup of smart factories, with features like automation of factory processes, digitizing factory operations, and connectivity throughout the factory floor for real-time monitoring through data collection and analysis.
The involvement of Smart Factories in traditional manufacturing units will improve product quality, security, and sustainability. It even empowers factory profitability and competence. The automated technology enhances the process and boosts the performance monitoring and decision-making approach, evading downtime, rework, bottlenecks, and defects. That would gradually improve customer service and gain productivity.
What is Smart Factory?
The ability to access the factory data and intelligence to create autonomous communication between the corporate functions within the factory floor operations is what makes the regular manufacturing unit as Smart Factory. The Fourth-generation industrial revolution or industry 4.0 is transforming factory to factory 4.0, which enables smart factory 4.0 operations. Smart Factory is a product of the fourth-generation factory revolution.
Smart Factory creates an extremely digitalized and connected factory environment, that converts legacy machines and equipment to advanced automated and self-intelligent machines and equipment. It enhances the working process by not just benefiting it in physical goods creation but by enriching functions like supply chain logistics, planning, and even product development.
The Smart Factory structure includes the combination of production, information, and communication, but the core value of the Smart Factory still happens inside the four walls of the factory unit. All disparate units of production are connected through the IoT (Internet of Things) or any other highly developed integrated circuits (ICs) that enables measurements, sensing, control, and communication of every function happening throughout the factories.
The sensors, monitors, and other devices used for communication with the central data system in the Smart Factory connect through Wireless connections. It enables data accumulation. The Computerized Maintenance Management System (CMMS) analyses the data to expedite proactive maintenance for better machine management.
Functional areas of Factory 4.0
The functional activities of Factory 4.0 refer the operations happening within the factory floor :
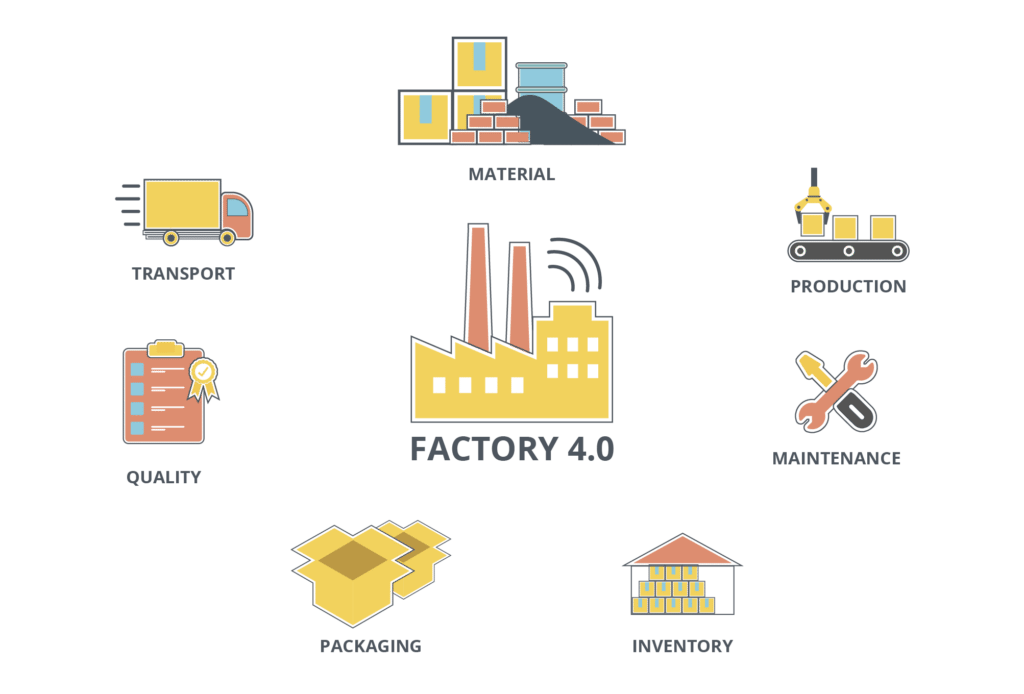
1. Materials Management
Materials Inventory management, supply chain management, and assuring stock, product quantity and quality are vital parts of any business. Raw materials are considered an integral component of many manufacturing industries. It’s divided into two types direct and indirect materials: Direct materials refer to products incorporated into finished by-products like furniture, and indirect materials are the components that are not necessarily incorporated into a final product but utilized in creating. Management of raw materials is then classified as Stock Management, procurement, and dispatching.
Stock Management
Stock Management referred to as materials inventory management. It is a process of managing raw goods, understanding the stock mix of an organization, and evaluating the various stock demands. Inventory management involves keeping records of changes in your raw materials stock over time, and it is often hard to keep track of supplies, suppliers, receivers, and payable budgets. Empowering digital factory 4.0 enhance the efficiency of your factory by proactively managing the materials availability through digital solutions.
Factory 4.0 solution will enable you to track real-time factory data and supports production with end-to-end traceability (materials to finished products). It may leverage cloud software-based management solutions to keep track of raw data produced.
Procurement
It is a way of discovering and agreeing to terms and conditions and purchasing raw materials from an external source, by involving in tendering or competitive bidding process.
The digital strategies involved with procurement always correlate to complete business objectives. So, professionals need to remain aware of how their actions can contribute to the smart factory. The involvement of digital factory 4.0 in procurement needs constant assessment like whether smart factory equipment aligns with business goals.
Dispatching
After stock management and procurement of the raw materials now it’s time to dispatch them to factory floor for production. With humans’ entry, there is always a possibility of having an error. Smart Factory introduces various advanced technologies that help them keep track of their raw materials and enables the utilization of diverse IoT technologies in identifying raw materials. Radio Frequency identification devices (RFID) convert various resources into Smart manufacturing objects (SMO). A laser scanner on the shop floor allows the display of real-time data.
2. Production Execution
Production Execution is the process that refers to the techniques and procedures that help to convert raw material or semi-finished goods into finished products or services. The production process involves multiple functions like planning, execution, recovery, and fulfilment.
Production Planning
Production planning involves the planning of production work orders and task modules in a factory or industry. There are multiple production methods like batch production, single-item manufacturing, mass production, continuous production, etc. All these production methods have their production planning.
Production Planning uses resource allocation of employees, materials, and production capacity, to serve various customers. The traditional factory functions might increase the process times and costs. The involvement of Smart Factory technologies minimalizes the production process time and costs. APS or Advanced planning system consists of three functions Real time production monitoring, Production Auto-Schedule, and Labour Auto Schedule.
Production Execution
The production execution process enables you to check for the availability of materials, view planned orders, create a batch if required, create products with the help of production orders, and record the output. With all this complicated process, humans are prone to make errors, which might result in loss. So, the involvement of Smart Factory technologies in factories will increase the efficiency of production execution.
The data platform utilizes production data provided by the sensors attached to devices and makes the execution process easier by automated checking for the availability of machines and raw materials. Smart Factory 4.0 solution has answers to every issue related to factory operations.
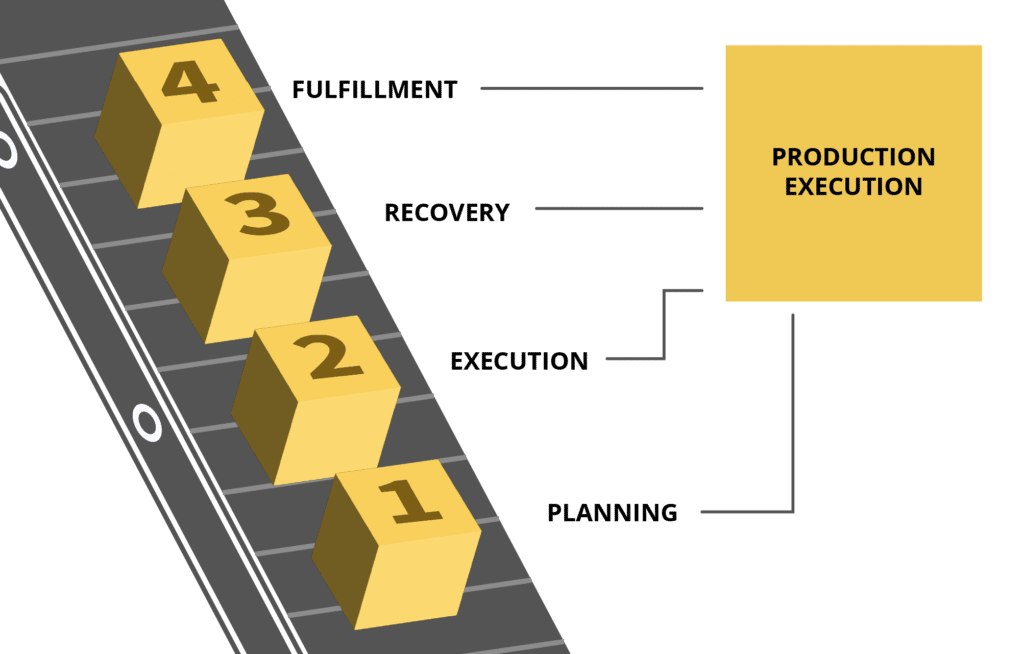
3. Machine Maintenance
The machine Maintenance process ensures that all the equipment or the machinery available for production work 100% efficiently. Four types of supervision involved are Corrective Maintenance, Preventive Maintenance, Risk-based Maintenance, and Condition-based plan Maintenance. Planning, Request allocation, Tool usage, Monitoring, Fixing, Prediction, and Part procurements are some of the maintenance functions. It is essential to conduct a maintenance process regularly.
Maintenance Planning
The maintenance planning process decides and prioritizes which maintenance job needs to complete first and how to complete it. The maintenance plan needs to be updated regularly. The factory 4.0 concept enhances the dynamic of maintenance planning in factories. With the involvement of advanced technologies like IoT, IIoT, Machine Learning, and Artificial Intelligence, it automatically plans and schedules the maintenance process with the help of data received from the devices.
Request allocations
Request allocation is a process that allocates various maintenance-related requests. Once you convert maintenance request into work order, the assigned requests need to be closed or ended to know that the maintenance request is no more active.
Maintenance Tracking
Monitoring the maintenance process will help factories to make more informed decisions about the conditions, performance, and maintenance needs. And it even informs factories about ways to improve their long-term asset health, to enhance the maintenance process. Thanks to the advanced software involved with Factory 4.0 concept, organizers can have an access to the data regarding their asset all the time.
Fixing
Fixing allows you to solve the issues you observed while conducting a monitoring process that enhances the factory processes. The Smart factories 4.0 solutions connects the factory devices which allows them to interact with other elements. It helps factories achieve an optimal performance every single time. The factory 4.0 concept collects information and analyses them to recommend required solutions, to ensure asset value and functionality.
Prediction
The prediction function in maintenance is a Smart technology utilized by factories to detect operational irregularities and possibly provide solutions for preventing or fixing the issues even before it occurs. Some of the industry 4.0 solutions helps machinery to adapt to the circumstances to achieve optimal performance while certain of the elements of factories are under the renovation.
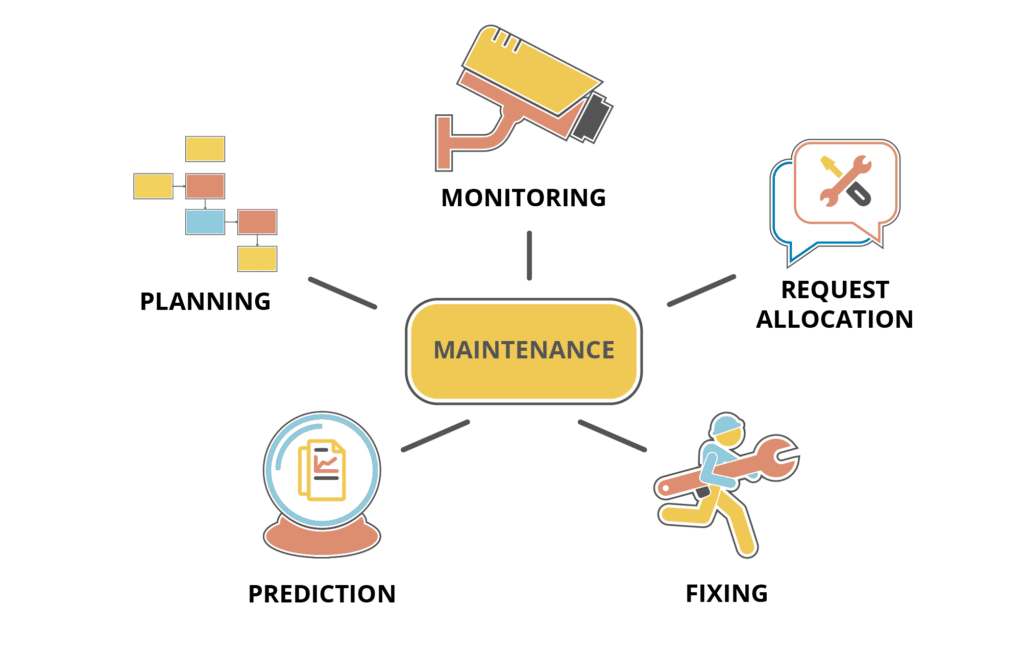
4. Tool List Management
Tool list management involves various functions like tools renting, recovery, refurbishment, recycling, usage metrics, procurement, and demand forecasting. The tool management software in factories generally involves two types of users Managers and Operators. Managers manage the tools renting and approval process and are permitted to create new tools and variants. Variants include parameters like colors and unique serial numbers generated by the device for the tools.
Tool Renting
The Tool Renting process is where an operator rents tools for work. It permits managers to approve and reject the Tool Renting request from the operator.
Rental Status
Tool renting status is divided into 4 phases pending, booked, dispatch, and Return.
The status as pending defines that the tools are not booked yet and are ready to book for work. The managers have the access to rent a tool for an operator. And each tool rented will have its specific serial number.
The status as booked defines that the operator has booked that specific tool, but the manager has not approved it yet. While booking a tool the operators need to mention the start time, start date, end time, and end date.
The status as dispatch defines that the manager has approved the tools for the rent. It incorporates the start date and the start time of the tool renting process.
The status as return defines that the operators have returned the rented tools. It incorporates the end time and the end date of the tool renting process. The tool rent is calculated based on the start and end time of the tool renting process.
Tool Refurbishment
Every tool will have a certain period of a lifetime; it is created by the manager while creating the tools. If the tool completes its lifetime, it will be refurbished and its status will be mentioned as service, during its refurbishment time. Operators are allowed to put tools for repair by posting a refurbishment request. And the managers have access to check and manage the issue.
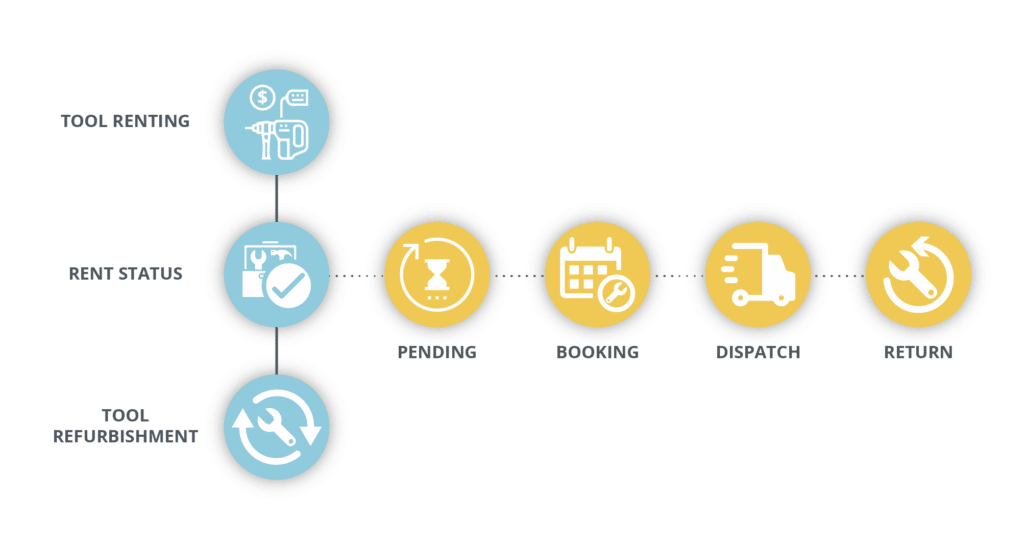
5. Quality Policy
A quality policy is a brief declaration or statement that supports an organization’s purpose and strategic direction. It provides a framework for quality objectives, customer demands and involves the commitment which meets the applicable requirement.
i) Checking SOP
Standard operational procedures known as SOP ensures that all the factory operations are always correct and operate in an identical pattern. Checking SOP assures that every factory element will work according to the clear-cut standard operation procedure.
ii) Sampling
Sampling ensures that clients will not receive a final product that falls short of their expectations. It blocks the complete production process until the completion of the sampling approval process. So, factories can ensure that there is no compromise in quality when outsourcing the products.
iii) Reporting
The reporting provides information on the status of operations. It allows users to see what is happening at an unparalleled level and help factories make data-driven decisions based on numbers and facts.
iv) Compliance management
It is a practice of monitoring and assessing systems to abide by industry and security standards with corporate and regulatory policies and needs.
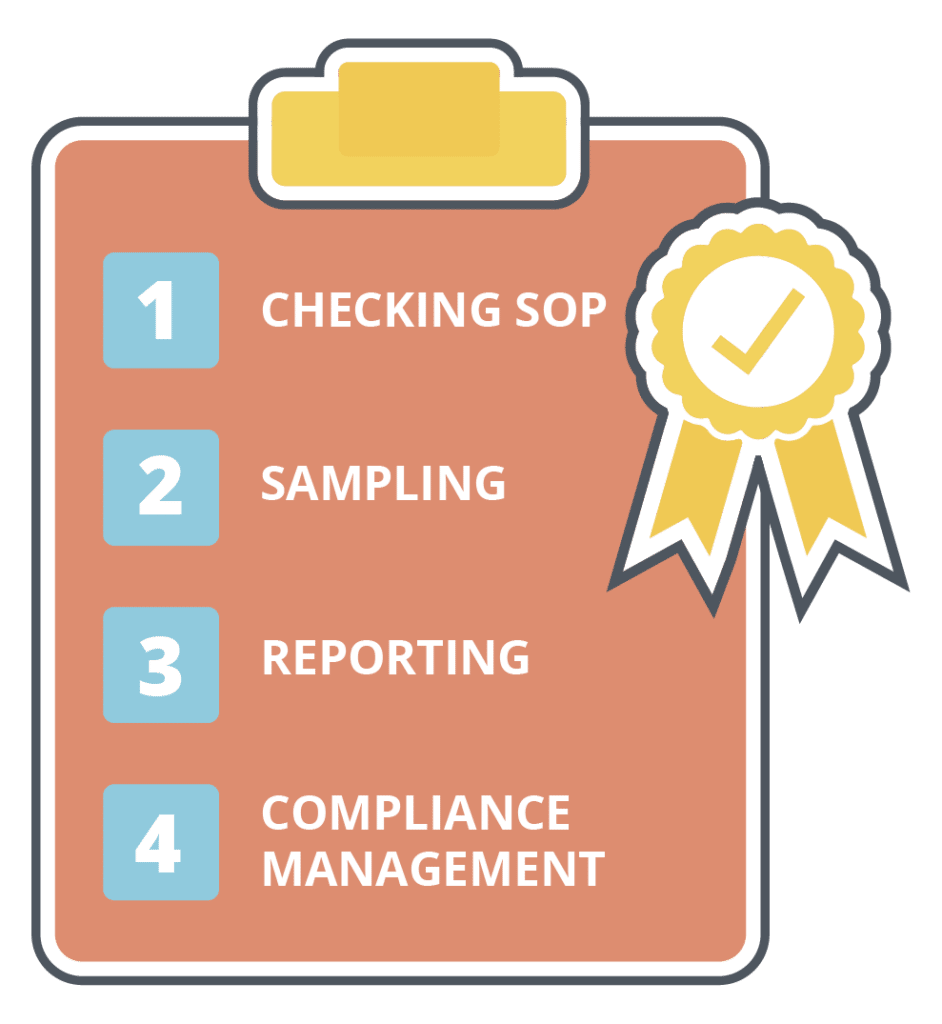
6. Packaging
Packaging is a process of evaluating, designing, and packaging for finishing goods. It organizes goods for transportation, organization, warehousing, and end-use. With the involvement of factory 4.0 technologies, the package sortation and placement process have sped up. It incorporates automation, communications, and manufacturing
technologies – making their way for the fourth industrial revolution.
Factory 4.0 concept increases the accuracy and functionality of packaging operations. With the new Industry-4.0 comes enhanced levels of integration and networking in the factory functionalities. The Factory 4.0 solutions operate on abundant types of repetitive tasks, assist factories with product reversals, and reduce the downtime associated with the packaging process.
Advanced Smart Factory technologies provide complete details related to packaging. The intelligent utilization of data considerably enhances the packaging functionalities and makes it easier to identify and improve quality issues. It provides visibility, traceability, and other data-driven approaches that help solve safety, conformity, and quality issues in the packaging process.
i) Package materials management
It is essential to manage the Packaging Materials as it is vital for performing the following tasks, such as the provision of the packaging material, automatic detection of short packaging material and requesting for replenishment and controlling of material provision processes based on the specification. The data transparency over the distribution channel allows factory optimization across internal and external ware hose locations. The information about the products will be linked. It contains data about where to coordinate and synchronize products.
Cyber-Physical Systems or CPS consist of digital models and physical production units. The CPS encompasses human-machine interface (HMI), automation, software mechanics, electronics, electricals, safety, maintenance, identity, and location-related data. The cyber-physical systems generate the network of Smart Factories where the production units are self-optimizing, self-healing, and self-aware. It monitors physical activity, makes a virtual copy of the physical world, and takes a decentralized decision.
ii) Sealing
From product quality check to output speed, design, and uptime, sealing is an essential aspect of brand image. The product outcome depends on how well the sealing technology work on the products. To be factory 4.0 ready, manufacturers re-evaluate the process and materials utilized in the packaging machinery. Advanced packaging machinery allows factories to think about materials employed in packaging.
The involvement of Factory 4.0 ensures error-free package sealing with the help of computerized Batch code. A batch code is also known as a lot number, or code number. Batch code in factories identifies the set of mass-produced products. It might include details like date/time of production, location of production that might be a line number and plant code, and Expiration data if required. These codes are generally placed on the outside of the package while sealing and helps factories to implement quality assurance checks and helps manufacturer perform a search all over inventory records in the case of a recall.
iii) Shipping:
Shipping is the final process involved with the packaging. Shipping the products involves multiple factors like order management, carrier relationship, and warehousing. The involvement of smart factory 4.0 will make the shipping process easier for factories by combining physical and digital technologies along with traditional and advanced strategies. Manufacturers are utilizing advanced technologies such as auto-boxing and robotics that enables faster shipping methods and eliminates frictions from the supply chain.
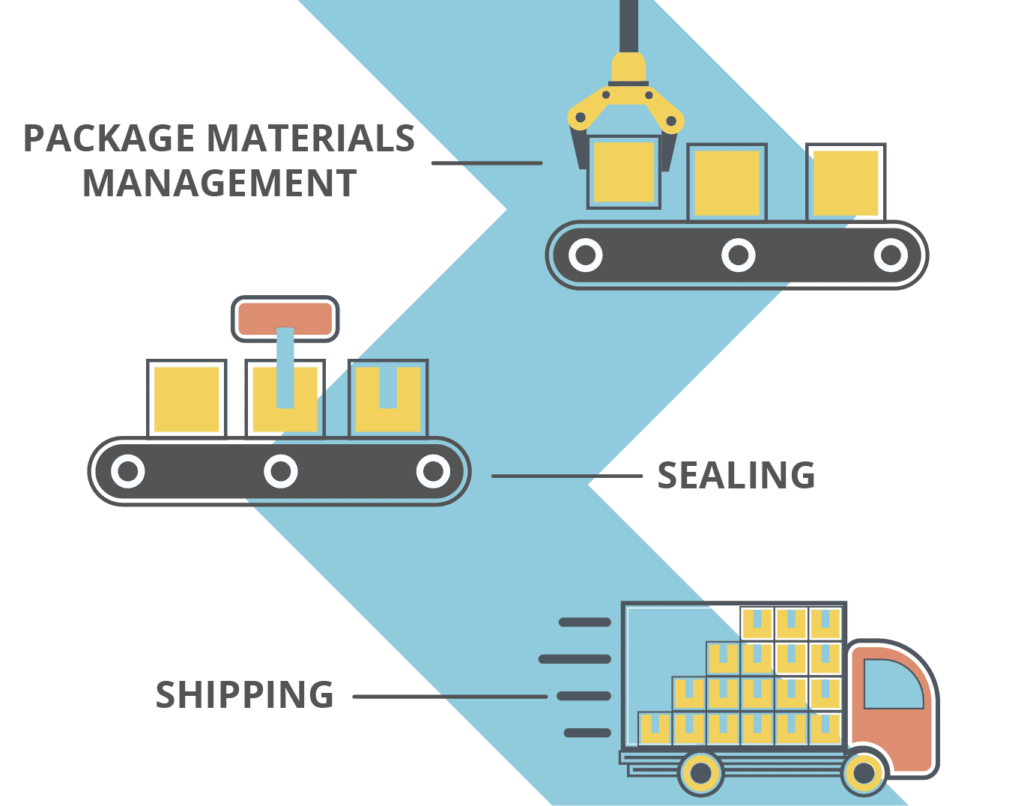
7. Inventory Storage
Storage is a marketing function that keeps the goods stored between the time of their production and their sale. Storage involves various functions, such as Warehouse management, Space management, Storage Planning, Dispatch, Environment monitoring, and movement. The factory 4.0 solutions amalgamate various advanced technologies like Machine learning, Artificial intelligence, and the Internet of Things, to tackle the challenges that arise in inventory storage.
i) Warehouse Management:
Warehouse management in factory 4.0 empowers the easy and efficient tracking of products and order-related data like expiry dates, serial numbers, and UPC. The Smart Factory eases customer experience enables a quick solving of stock-related issues and reduces additional expenditures. The Smarter Warehouse Management System (WMS) collects data via RFID tags, Bar code scanners, etc. It sends out instructions for mobile platforms and robots and reduces human interference. The WMS automatically controls every factory task.
ii) Space management:
Space management involves managing the factory’s physical space. It includes tracking factory space, addressing occupancies in factories, and generating the spital plans. Effective Space Planning, Effective Tracking, and Effective Implementation are three elements of space management, which can be effectively implemented with the help of Smart Factory.
iii) Storage planning:
Storage planning includes managing product storage areas. It reviews current storage needs and predicts future storage requirements. It makes sure that storage resources are available when required.
iv) Dispatch:
One of the functions of a factory or a warehouse is to dispatch products. This stage aims to ship goods ordered by the customers. It ensures that the customers receive their products at the ideal time and condition. Dispatching is one of the main pillars of lean manufacturing. Smart factories help makes sure that all the products ordered by the customers are shipped to them with the help of remote tracking
v) Environment monitoring:
Environment monitoring illustrates the activities and processes that monitor and describes environmental quality. The IoT technology involved in Factory 4.0 solution monitors the dust, gas, water, CO2, and other harmful essences to promote factory operations.
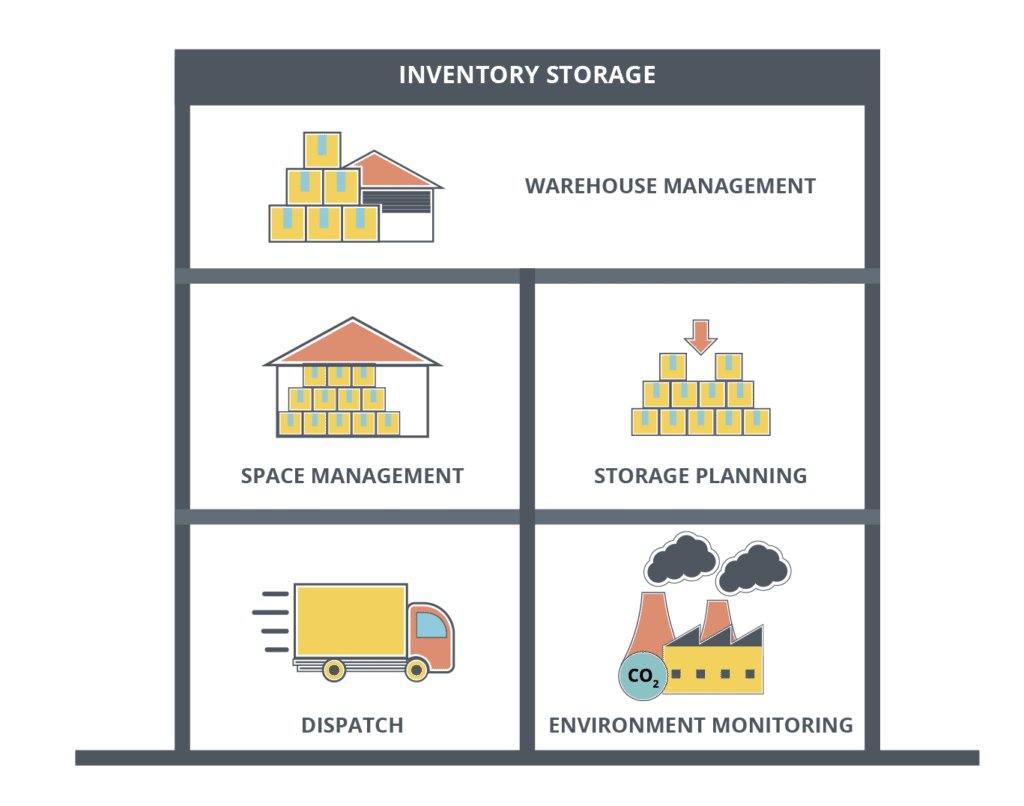
8. Transportations
The factory 4.0 concept involves smart transportation to the factories. It is a critical integrated application that manages strategies in transportation systems. It empowers users to be well informed and makes safer and shrewder use of transport networks. The transportation of goods in the Smart Factory, the factory of the future industry 4.0, involves functions like Vehicle Management, Contracting, Delivery Tracking, Loading, Unloading, Relocating, Driver management, and Insurance.
i) Vehicle Management:
Vehicle management is a logistic platform that utilizes technologies that involve smart, forward-thinking usage and tracking of every flotilla movement. It assists factories in tracking the physical motion of their goods and ensures that the shipment is obliging and every document is available when required.
ii) Delivery Tracking:
Delivery tracking functionality improves the overall delivery system. It helps factories accurately track their products and enhances the efficiency of the business.
Loading, Unloading, relocating: The functions like loading, unloading, and relocating utilizes Smart Factory technologies to keep track of the products. IoT technology will help you track the goods loaded and provides information on where, how, and when they will be unloaded or relocated.
iii) Driver management:
Involvement of IoT and edge computing in Smart Factory 4.0 can minimize the risk associated with vehicles and transportation, which increases efficiency and productivity. Real-time data generated by edge devices like dashboard cameras helps factories monitor drivers’ behavior in real time. It enables factories to know the exact location of their vehicles and drivers.
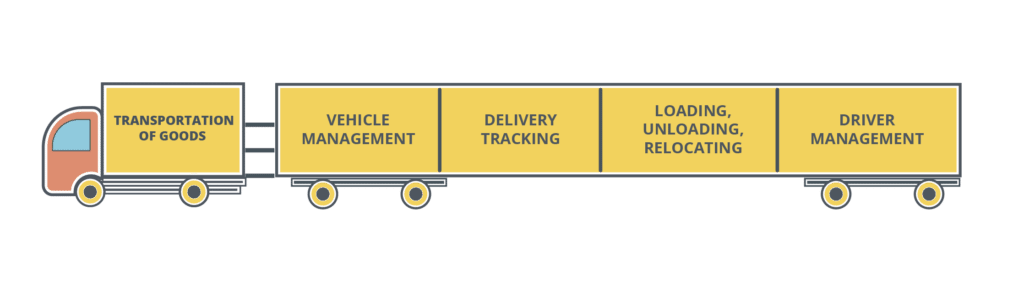
Steps to Build Your Smart Factory
a) Identify your needs: The manufacturing industry needs to know why they want to update their traditional factory functions to Smart Factory Functions. The Smart Factory implementation generally happens in phases, and proprietors need to identify and analyze your priority so that they can invest their time and power in the right direction.
b) Train your Employees: With modern technologies on board, it might intimidate the workers in many ways. The fear of not knowing the technology or lack of skill or knowledge might create a panic in employees. An employer needs to get their personnel on board by providing the proper reason for the shift towards Smart Factory. Providing appropriate training ensures that the employees can adapt to modern technology or Smart factory.
c) Security: Security issues come hand in hand with the digitalization of the asset. It is essential never to overlook cyber security. as it is the factor that could hinder the success of Smart Factory. So, it is vital to undertake the proper provisions to guarantee that the data is protected.
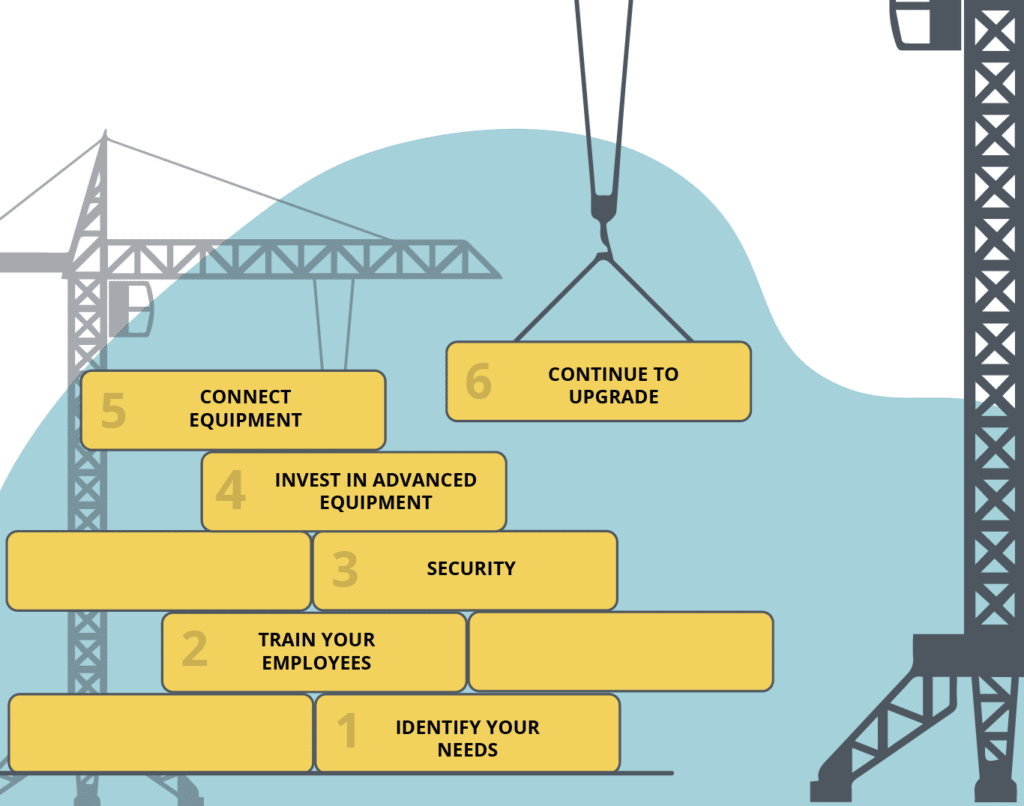
d) Invests in advanced equipment: Advanced equipment like sensors and monitors play a vital role in enabling the Smart factory. It is essential to take care of infrastructure upgrades like faster internet, Wi-Fi, and other advanced computer equipment to analyze store, and manage the large amount of data accumulated.
e) Connect your equipment and start accumulating the data: Once you start collecting the Smart equipment like sensors, you can connect it with your existing machine. So that once you have everything ready, it will be easy to work.
f) Continue to upgrade the Smart Factory Implementation: It is always essential to upgrade your device functionality to cope with the rapidly changing technology. With employees becoming similar to Smart Technology, it becomes easier for factories to spread out to different areas of Smart Factories.
Different Levels of Smart Factory
Smart Factories involve four levels of data structure, which will help you evaluate your progress in setting up a Smart Factory.
Level One: Available Data
The first level of the Smart Factory system is just the fundamental feature. At this phase, data will be available but in a raw form, which will be complicated to utilize, implement or decide on an improvement. The data accumulated requires manual work to integrate and transform data into useful information. Problem-solving consumes a lot of time at this level. For example: If an issue related to machinery arises, operators and engineers manually scramble the data to understand where the problem is from and what action needs to be taken. The manual approach is time-consuming and drains a lot of energy and resources from the factory.
Level Two: Accessible Data
Upgrading yourself from one level to the second level is to stop the risk of wasting resources because of unplanned downtime every day. It integrates complete discrete data sources into a single source of truth and gathers and regularly tracks production data. With data available under a single roof, it becomes easier for the operators to access information when required, with the help of data visualizations and dashboards. It helps engineers improve product functions and material improvement. It helps in adopting a mass customization strategy.
Proactive analysis enables factories to tackle the issue even before its occurrence, but it still demands time, effort, and commitment from the operators. But, updating from level one to level two needs a new data infrastructure.
Level three: Activate Data
Level three supports operators and engineers to be genuinely precautionary and proactive about solving issues that level two might not ablle to solve. A factory needs to add new capabilities like Artificial Intelligence (AI) or Machine Learning (ML) to the previous level data architecture to upgrade from level two to level three.
An AI and ML combined with the level two data architecture system accumulates all the production data to develop an intelligent system which will find vital insights and foresee failures accurately. With Machine Learning involvement, users do not have to perform manual process analysis or query the system to find the solution to solving production issues. But level three demands more human interference than the intelligent system recommends.
Level Four: Action-oriented Data
Level Four believes in action-oriented data. The system deploys the suggestions that it finds from analyzing factory manufacturing data. The ML will find an optimization, then generates and transmit the recommended new settings to the machine, which executes it automatically. With the involvement of artificial intelligence in Smart Factory time taken to achive an insight discovered by the system reduces. By attaining fourth level, it requires large database that is enough to have ample impact on a production change.
Smart Factory 4.0 examples in digitalization services
i) Convert paper and excel files to Smart files:
The utilization of Papers and Excel sheets is slow to document, expensive, and very much prone to human error. With the digital revolution called Smart Factory, there is a considerable transformation. Smart Factory reinforces the digital domine and enables transferring of physical media into the digital domine.
The advanced technology utilized for documentation in Smart Factories will provide more accurate and precise data than excel sheets or paper. Digitalization supports quick data extraction, decreases cost, achieves market benefit, and rapid decision-making. With the real-time monitoring and reporting of the data, technology enables data-driven decision-making.
ii) Connecting the Shop Floor to the business:
The Smart Factories enables the centralized factory system, which accumulates the complete factory data with the help of Sensors ERP, MES, quality systems, and excel/paper-based data to offer real-time operational visibility. It is known as a factory of the future industry 4.0. Factory 4.0 concept as introduced, various software modeling tools that support the product data analysis by digitally replicating the data, with the help of Digital Twin technology.
The MES systems are generally utilized in factories to produce digital documentation while controlling standard templates. The real-time machine data generated will help manufacturers to create essential insight. It helps them to know if there are any issues in the system beforehand. The manufacturers will have a complete vision of their business.
iii) Increase the machine efficiency:
The adaption of Smart factories will help manufactures to increase machine efficiency. Smart Technology ensures that the machines installed will work to their full capability.
Data integration and insights from the shop floor with the supply chain and entire factory provide multiple ways to improve operational efficiency. So, with the technologies utilized in the Smart Factory, manufacturers can increase machine efficiency and boost productivity.
iv) Data empowerment with Machine Learning
Machine Learning (ML) will enhance the factory data and boosts production value. Machine Learning permits computers to be taught without being explicitly programmed. With automated optimization, machines adapt to various changing conditions in real time and enable factories to run smoothly with minimal human intervention. ML foresees the required materials that factories need to run at maximum efficiency.
Technologies involved with Factory 4.0
Organizations need a dedicated approach to accept the evolving technologies, which would add value and simplify the complexity of work, combination of advanced technologies like IoT, IIoT, AI, ML, Cloud Computing, and many more make the Smart factory work smartly.
1. IoT
The term IoT or Internet of Things implies the connected devices or the group of networks that enables the communication between devices and the cloud over communication networks like the internet. A sensor attached to the devices like vacuums, car, machines, and many more collects the data and return it to users intelligently.
The Internet of Things (IoT) system integrates Seven layers or components on which it operates Perception Layer, Connectivity/Transport Layer, processing Layer, Application Layer, Business layer, security Layer, and Edge Computing Layer.
IoT Architecture consists of three layers Devices, Edge Gateway, and Cloud, and it utilizes sensors and actuators as a networking thing. Edge Gateway layer includes a sensor data aggregation system known as Edge Gateway that ensures connectivity to the cloud and data pre-processing with the help of an event hub, web sockets, and even edge analytics in some cases like fog computing.
The third layer involves a cloud application, developed using microservice architecture, that consists of a database system, which helps you store all the data received from the devices with the help of Edge Gateway.
2. IIoT
The Industrial Internet of Things (IIoT) utilizes Smart sensors and actuators to augment manufacturing and industrial process and gained fame with the fourth Industrial Revolution (industry 4.0).
Smart Machines and real-time analytics are employed in IIoT to receive and analyze the data received from the machines in manufacturing sectors.
The factories utilize the collected data to improve their productivity and efficency along with various other benefits. Cloud computing is associated with IIoT to enhance and optimize process controls. IIoT architecture consists of 4 layers Device layer, Network Layer, Service Layer, and Content Layer.
3. Digital Twin
Digital Twin is a virtual representation of the objects, which serves as a real-time digital counterpart of any physical object.
For Example, A machine in cold storage is equipped with multiple sensors associated with essential areas of functionality. The sensors generate data on the various physical aspects of the machines, such as energy output, temperature, weather conditions, and more. The collected information will be then transmitted to a data processing system and applied to a digital copy to create a digital twin.
With the accumulated information about the physical object, a virtual model can be utilized to run simulations, study the issues, and take the required action against them to improve the machine’s performance. If the solution applied to the virtual simulation works, it can be applied back to the original machine.
4. Machine Learning
Machine Learning referred to as ML allows computers to learn without begin explicitly programmed. ML is nothing but programming computers to utilize example data or past experiences to optimize a performance criterion. The involvement of ML helps devices take decisions with minimal human involvement.
Machine learning employs Key AI technologies to work efficiently. Some of the Best technologies employed are Keras, Torch, Caffe, TensorFlow, Theano, and Microsoft Cognitive Toolkit.
5. Artificial Intelligence
Artificial Intelligence or AI implies the simulation of human intelligence in machines, which are programmed to analyze like humans and mimic their actions. AI rationalizes data and takes actions that have the best possibility of achieving the goal. ML or machine learning is the subset of Artificial intelligence. AI involves Deep Learning Technologies, that enables automatic learning via the incorporation of enormous amounts of unprocessed data like images, text, or video. Algorithms play an important role in AI. Different versions of Algorithms are utilized to develop multiple distinct kinds of AI functionalities.
Artificial Intelligence (AI) is generally categorized into four types –
i) Reactive AI:
Reactive AI utilizes algorithms to optimize the output based on input sets. Example: Chess-playing AI is considered the Relative AI, as it utilizes the input to provide the best-optimized strategy to win a game. These types of AI are usually static and cannot learn or adapt to different circumstances.
ii) Limited Memory AI:
Limited Memory AI can adapt to previous experiences or can update itself based on the latest observations. But generally, the updating of data is limited, and it relatively has a short memory phase. Example: Self-driving cars utilize limited Memory AI, as it takes data from recent experience. And gets adjusted to the novel situation by reading the road.
iii) Theory-of-mind AI:
Theory-of-mind AI can adapt to their surrounding completely and has an all-encompassing capacity to learn and preserve experiences from the past. Example: Chat-Bots are theory-of-mind AI technology that is generally utilized to interact with a human. It allows humans to interact with digital devices as if they are talking to a real person.
iv) Self-aware AI:
In Self-aware AI the machine will be aware of its existence. It is still in the state science frictions. Some experts even believe that an AI can never become conscious of itself.
6. Manufacturing Execution System
Manufacturing Execution Systems (MES) are automated systems utilized in factories to track documents. It works as a real-time monitoring system, that controls various elements of the production process. it also supports organizations in transforming raw materials into completed products. It helps manufacturers understand the current conditions of the plant floor and provides ideas to improve production output.
MES can work around multiple functional areas like management of products, Definition across the product life cycle, dispatch, resource scheduling, and order execution. It generates the records and obtains data, processes, and results of manufacturing practices.
7. Enterprise Resource Planning
Enterprise Resource Planning is software, that is utilized by various organizations to manage their day-to-day business activities like procurement, project management, accounting, risk management, and supply chain functionalities. It manages multiple businesses of all types and sizes.
ERP systems involve enterprise performance management software which helps organizers plan, cost, predict, and report about factories’ financial results. It ties various multitude of business processes and enforces the data flow between them, with the help of shared transactional data from multiple sources. It eradicates data duplication and offers data integrity.
8. Cloud Computing
Cloud Computing enables on-demand availability of computerized resources. It provides data storage space (cloud storage) and computing power, without any kind of direct active management by the user. It is a delivery of computing services that involve databases, networking, analytics, software, and intelligence over the internet or cloud. It enables faster innovation, flexible resources, and economies of scale.
Cloud Computing has three ways to employ cloud services public cloud, private cloud, and hybrid cloud. The public clouds are owned and managed by the third-party cloud. Private cloud service is generally utilized by an organization or single business. A hybrid cloud is a combination of public and private cloud, that offers great flexibility for business, more deployment options, and enables you to optimize your existing infrastructure, compliance, and security. IaaS, PaaS, SaaS, and serverless are four types of cloud computing services.
Conclusion
Factory 4.0 is considered a factory of the future industry 4.0 with the evolution of the fourth industrial revolution known as industry 4.0. The Smart Factory is the combination of multiple modern advanced technologies that create a self-adapting, hyperflexible manufacturing ability. It provides an opportunity to build flexible, efficient, and advanced processes and functions to run a factory.
FAQs
1.What is Factory 4.0 in manufacturing?
Factory 4.0, also known as Industry 4.0, represents the fourth industrial revolution, where smart technologies like AI, IoT, ML, and cloud computing are integrated into manufacturing processes. It focuses on automation, real-time data, and digital transformation to create efficient and intelligent factories.
2.What is a Smart Factory?
A Smart Factory is a highly digitized and connected production environment that relies on technologies like sensors, AI, machine learning, and the Industrial Internet of Things (IIoT) to self-optimize operations, adapt in real time, and enhance overall production efficiency.
3. How is a Smart Factory different from a traditional factory?
Traditional factories rely on manual processes and isolated machines, while Smart Factories use connected systems, data analytics, and automation to monitor, predict, and optimize operations in real time.
4. What are the key steps to build a Smart Factory?
To build a Smart Factory, manufacturers should:
- Identify operational goals and priorities
- Train employees on new technologies
- Ensure cybersecurity measures
- Invest in IoT-enabled devices and sensors
- Connect machinery for data collection
- Continuously upgrade systems with emerging technologies
5.What are the four levels of Smart Factory data maturity?
- Level 1 – Available Data: Data exists but is unstructured and hard to analyze.
- Level 2 – Accessible Data: Data is centralized and visualized for analysis.
- Level 3 – Activated Data: AI and ML are integrated to predict issues.
- Level 4 – Action-Oriented Data: The system automatically implements optimized decisions based on insights.