The manufacturing industry is constantly evolving with innovation and the development of software solutions to digitalize factory operations. From using water and steam to mechanize production processes to currently employing MES/MOM/ERP management tools along with software capabilities that help achieve Industry 4.0, smart manufacturing has been progressing with every phase of the industrial revolution.
With the growing scope of manufacturing, the challenges and smart manufacturing use cases associated with combat hurdles are significantly proving to be dynamic. You might have wondered what smart manufacturing use cases are, given the ever-evolving nature of the manufacturing industry. Well then, you are reading the right blog.
The article identifies and explores 5 smart manufacturing use cases primarily chosen for their capabilities in addressing and resolving challenges in manufacturing industries.
What are the top Smart Manufacturing Use Cases
This being the crux of the article, identifying and elaborating the smart manufacturing use case serves best in the pursuit of knowledge growing and perceiving the know-why of these use cases in manufacturing. This section of the article predominantly focuses on exploring 5 smart manufacturing use cases in three aspects particularly, Meaning, Features and Benefits.
- Predictive Maintenance
- Agile Production
- AI Driven Quality Inspection
- Connected Supply Chain
- Robotics Automation
Predictive Maintenance
Machines/equipment in manufacturing may break. It requires constant maintenance and repair from time to time to ensure optimized production and undeniably, it is an essential part of manufacturing operations management. Preventive maintenance has traditionally served as a strategic remedy in the life of manufacturing machine management, where prior planning of scheduled downtime on a routine basis to perform checks and repairs is practiced.
On the contrary, the modern approach of Predictive Maintenance also known as condition-based monitoring is a newer maintenance strategy that proactively monitors the condition and performance of assets in real-time to predict the requirement of maintenance prior to asset failure/downtime. Predictive Maintenance interrogates vast amounts of historical data to determine the set of circumstances that typically lead to equipment faults and unexpected machine breakdowns. This ability creates value for the manufacturing chain by replacing traditional methods of manual visual monitoring, reactive maintenance and others that increase product lead-time and lower optimized operations. Predictive maintenance models have to be curated that allow for analysis of several data points from machines executing a variety of processes for effective practice of maintenance ahead of asset failure.
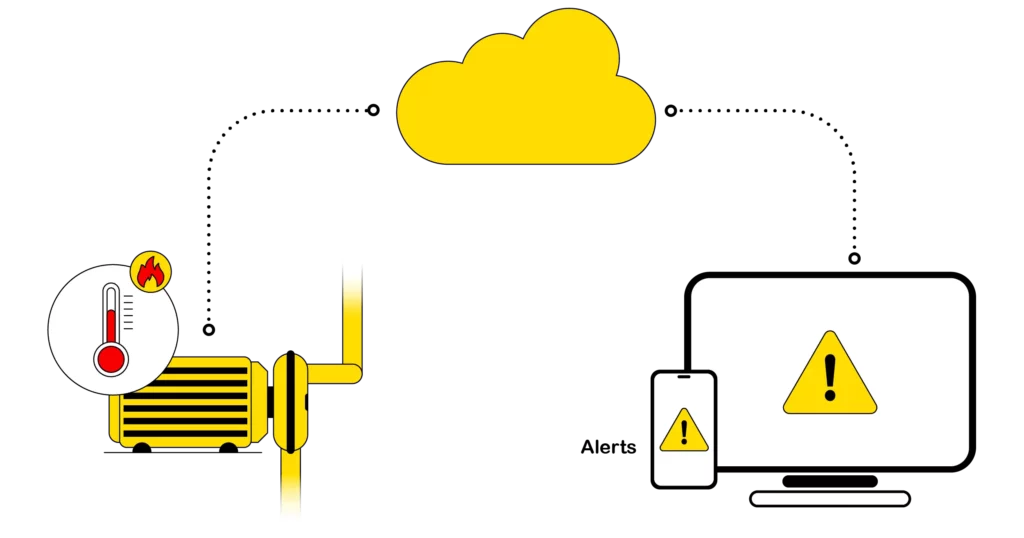
What is Predictive Maintenance Software
Predictive Maintenance is ideal to achieve smart manufacturing. It serves to effectively maximize equipment performance, minimize unplanned downtime, optimize production processes, and reduce costs incurred from unscheduled checks, repairs, and replacements. Listed below are some of the crucial features of Predictive Maintenance.
Benefits of Predictive Maintenance
Holistic Management System
Implementing Predictive Maintenance becomes a value add-on in the management and execution of inventory, machine and labour operations in manufacturing. Predictive Maintenance solution facilitates a single entity for locating in real-time, the performance and condition of equipment in manufacturing along with data on supply chain and labour to predict stock requirements to ensure optimized resource utility.
Automated Scheduling of Maintenance
Software that offers Predictive Maintenance run based on artificial intelligence and analytics to advance prediction that supports generating valuable insights. These analytics prompt automated scheduling of service/maintenance based on machine usage, and performance statistics. It also enables automated job assignments and timeline management.
Safety and Compliance
Predictive Maintenance facilitates not only machine/asset maintenance but also ensures to notify/reminders on parameters concerning the safety of machines and operators. It helps companies prioritize the health of machines as well as workers’ safety along with sustaining compliance.
Optimize Workflow
Without elaborate insights on high productive hours, labour and machine availability, it is difficult to optimize production workflows. Employing predictive maintenance will provide insightful data on various machine parameters that suffice to optimize workflow.
Additional Values Added by Predictive Maintenance
Save Money
Predictive maintenance serves as a key driver to saving OPEX or operational expenditure in the manufacturing industry. With the help of predictive maintenance and health machine operations, power utility becomes reduced due to lowered frequency in unforeseen catastrophic machine breakdowns that contribute to optimized operating and production. Efficient maintenance and utility of supplies are ensured as a result of receded unplanned equipment maintenance.
Early Fault Detection
Fault Prediction is powered by the ability to interrogate vast amounts of historical data as well as present data in real-time. With the assessment of device and process data, insightful metrics based on various parameters summing the overall OEE performance of assets and processes are derived.
Enhanced Machine Performance
Prediction allows maintenance schedule prior to the unplanned breakdown of machines. This enables manufacturers to automate machine health checks and schedule maintenance when needed thereby enhancing machine performance in production cycles.
Efficient Inventory Management
Predictive Maintenance analyses huge amounts of data and predicts the timeline for the maintenance schedule to prevent unplanned downtime. This enables manufacturers to adopt just-in-time inventory of tools that allow effective management of stock and supply chain without creating unwanted wastage. Resources to sustain the production of a product are stocked adequately to meet demands without causing utility depreciation.
Having listed a few of the prominent benefits along with the features and definition of predictive maintenance, it’s about time to explore another smart manufacturing use case.
Agile Production Execution
Agile production refers to the ability of the manufacturing unit to dynamically change the product schedule and execution according to the demand within the shift/day of operations. Agile production might seem to work with the same tools and techniques of lean production, but there is a slight paradigm shift/change. While lean manufacturing focuses on eliminating waste to reduce operations costs and lead time, Agile production emphasizes rapid customer-centric response in production processes to meet changing demands. Speed and agility are the core elements recognized to offer a competitive advantage and are vouched for the same.
Agile production strategizes are employing production processes, tools and techniques that are flexible to adapt to changes quickly. With a goal to sustain a competitive advantage, ensuring customer satisfaction within a short frame is critical. Using an agile framework that accommodates change and personalizes products and services when required by customers. It allows large as well as SMBs to drive potential market stability and profits.
Principles of Agile Production
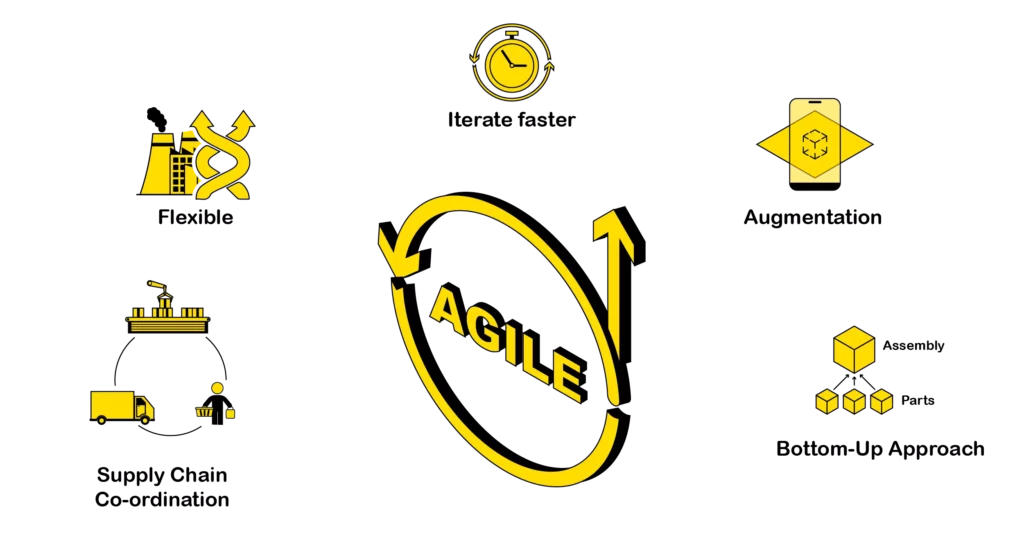
i) Iterate faster – The idea of delivering small pieces of value is the core of agile production methodology with key goals like customer response-oriented and flexibility. Instead of targeting to design, develop and produce a single product taken to be holistic, the objective of agile production is to rapidly produce multiple enhanced versions. Each iteration in the process of production allows identifying strengths and drawbacks of the product, giving new insights. These insights will certainly help in surpassing previous product limitations with updated qualities to meet customer demands. Agile production enables manufacturers to adopt incremental, iterative methods with ease.
ii) Flexible – Volatility negatively impacts manufacturers causing a faulty supply chain, incurring the surplus lead time and a deficit in finances. In the effort to stay unaffected by external factors that contribute to volatility, flexible systems are to be implemented in manufacturing companies. Internal systems of operation and processing in manufacturing require to be dynamic enough to rebound from factors causing performance deterioration. Agile production keeps manufacturers on their toes with multiple options/frameworks that can be accommodated in operating flexible systems.
iii) Supply Chain Coordination – Agile production methodologies include internal teams as well as external alliances connectivity that sustains coordination between the two components. Adequate information on production and product build-out is made known via connectivity in the supply chain management of manufacturing, this allows coordination and uniformity in availing materials/resources for production and incremental upgrades of product over development processes.
iv) Bottom-Up Approach – Agile manufacturing promotes and practices a bottom-up approach as opposed to a top-down approach in the passing and approving of goals and directives within an organization. The bottom-up approach in manufacturing serves as a medium for ideas and directives to flow seamlessly between hierarchies in the manufacturing business. This approach promotes collaboration and ensures effective operations that helps deliver higher value of products and processes.
v) Augmentation – Augmentation can be best understood in contrast to automation. While automation refers to automating work and tasks of workers’ that often result in replacing human intervention with automation via technology, augmentation refers to upgrading production performance by enhancing workers’ capabilities through technology, associated tools and techniques. From error-proofing work instructions, and computer-assisted quality checks to artificial intelligence governed maintenance and inventory management, augmentation is the ground rule in Agile production.
Let’s move to another smart manufacturing use case.
AI-driven Quality Inspection
Quality plays an important role in ensuring the success of manufacturing a great product. Manufacturing involves a variety of processes and requires ongoing quality checks for defect identification. It ensures that compliance and quality standards are being met constantly. Although traditional quality inspection methods are being employed, none of it has proven to be efficient with growing demand and quality standards over the years.
Computer Vision-based quality inspection refers to integrating AI inspection algorithms that analyse data gathered by visual inspection mediums like cameras, drones, sensors and so on. The AI-driven quality inspection involves asset management, data gathering, data analysis and inspection reporting, all of which function as automated operations. The integration of AI with visual inspection can be of immense help in the manufacturing business.
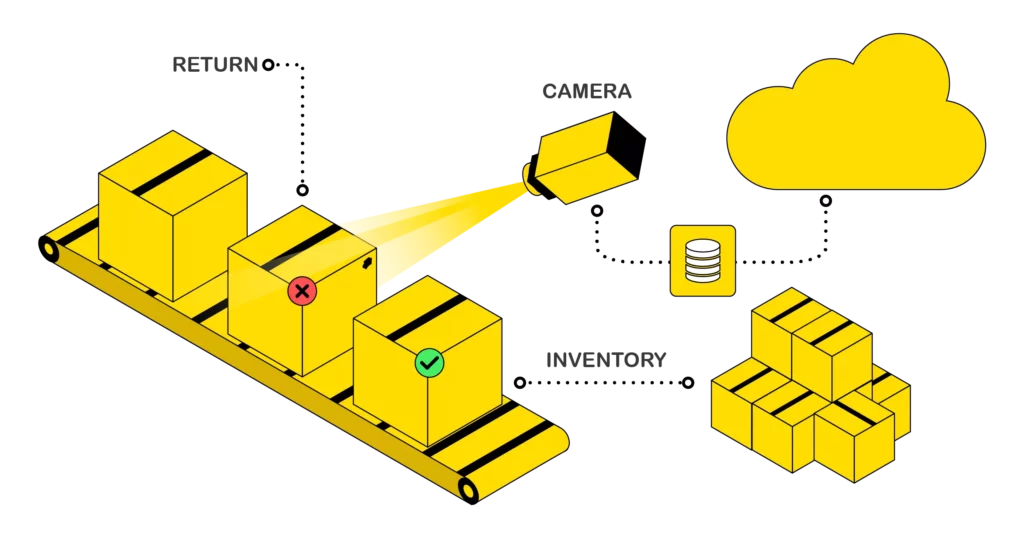
Benefits of AI-driven Quality Inspection
i) Obtain Visibility in Production Line– AI-driven quality inspection ensures that the production line is internet-enabled and connected in order to extract data at real-time. Once systems and processes are connected, computerized intelligent algorithms capture quality data and convert the same to insightful metrics. Production performance data is also investigated with established levels of quality standards that further helps to detect material/part faults in production.
ii) Identify Root Cause Defects – Connected cyber-physical systems that offer AI-enabled quality inspection helps to detect root cause defects within the different stages of manufacturing a product. Be it a material defect or asset performance defect, AI-driven quality inspection allows to tap the exact cause of quality issues in production processes. This is made possible with the advance programmed algorithms and analytics that assess, qualify and/ or reject a part/material that is causing the output to be faulty.
iii) Production Optimization and Waste Elimination – AI-driven quality inspection is integrated to manual testing tools and techniques that enhances quality assurance in production. Manufacturers are given insights beyond their visual capabilities to further examine and take cautious steps toward rectifying the error. Therefore, optimized production cycles are ensured with initial identification that omits re-doing of processes and eliminates excess waste generation.
iv) Time Saving – AI-driven quality inspection is time-saving to manufacturers who are looking for reliable, ongoing and effective solutions to maintain quality assurance. Since it runs on algorithms that run parallelly to investigate the performance and quality of materials through every production phase until end product is achieved as desired. AI-driven quality checks omit manual visual inspection that is otherwise time-consuming. It’s about time to explore another smart manufacturing use case.
Connected Supply Chain
One of the biggest challenges of manufacturing industries is fragmented supply chain systems. Systematic industry inefficiency is an output of a lack of horizontal and vertical connectivity of participants (suppliers, logistics companies, end-users/customers, value partners and so on) in the supply chain of the manufacturing industry. Though challenges in the manufacturing sphere might seem insurmountable, there is still hope with growing innovations powered by newer industrial revolutions.
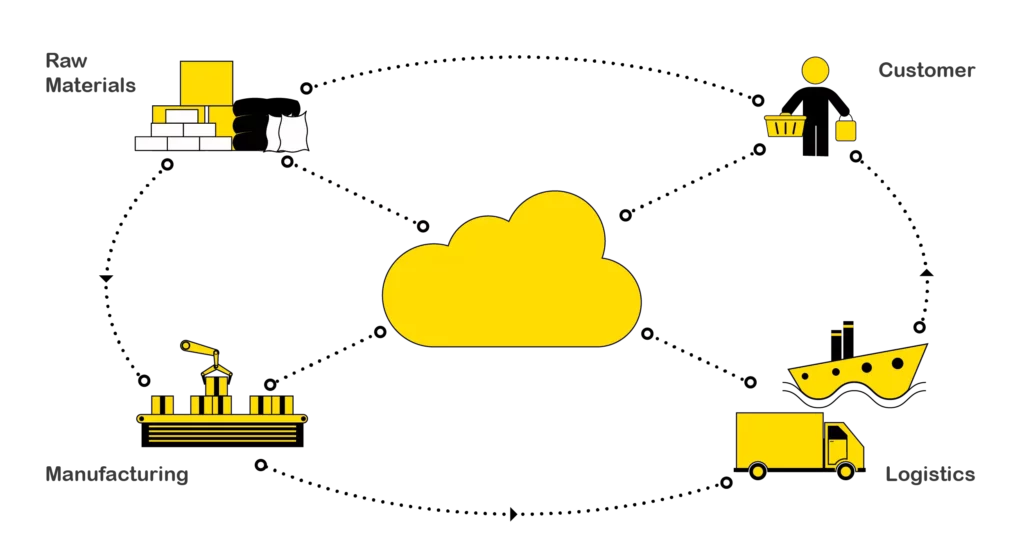
The latest is the fourth industrial revolution spanning the AI-enabled internet-connected cyber-physical systems within factories, aiming to transform legendary manufacturing to smart manufacturing. Enabling these technologies are key drivers of uniting fragmented ecosystems as they facilitate the connectivity of different players across the supply chain network.
Connected Supply Chain refers to bringing together the many participants involved in the network of the supply chain. It ensures that disruptive ecosystems are connected to facilitate the end-to-end flow of information in real-time, wherever and wherever needed. A connected supply chain implies that isolated ecosystems in the supply chain are integrated with an aim to offer maximum visibility. The connected supply chain is a single defined system that allows the sharing of data and insights for business profits. Connected supply chains add responsiveness and resilience to operations management by predicting and reacting to dynamic market/customer demands with the utilization of big data.
Benefits of Connected Supply Chain
Supply chain that was once seen as an investment burden is now considered a competitive differentiator that is to be strategically planned for effective business outputs. With high relevance in optimizing production and sustaining adequate supply chain, it’s demanding to understand the goals of a connected supply chain, a few are listed below.
i) Improved Visibility – By connecting and bringing together the various partners and players in the supply chain and ensuring the secure flow of information, tracking and monitoring of each component in supply chain become easy. With IoT, ML and B2B platforms that support improved supply chain visibility, industries can react faster to supply chain shocks, optimize efficiency and enhance customer experience.
ii) Demand Oriented Supply Chain – Connected supply chain does not only provide a treasure trove of information for operations management of factory, but also with metrics and data to fully understand customer needs and provides competitive advantage of efficient management of supply chain based on customer demands. With data that displays demand, manufacturers are given the advantage of assessing demand patterns and trends on particular components to enable accurate forecasting of inventory based on customer demand.
iii) Optimized Supply Chain – Connected supply chain enables continuous improvement and optimization of the supply chain and inventory with the availability, accessibility and reliability of process data and all participants involved in the supply chain. Manufacturers can improve efficiency, and business agility, and reduce wastage and costs with the help of a connected supply chain. Supplier chain performance management is optimized and well-handled at all levels of operations inclusive balance of adhering to ethical and sustainable inventory operations.
iv) Automate Processes – Inventory levels and consumption patters along with customer demands are monitored in real-time. As a result of the real-time monitoring ability that connected supply chains enable, replenishment of inventory and supply chain is automated based on customer demand, manufacturing consumption patterns and inventory levels.
v) Achieve Quick ROI – A connected supply chain introduces a track and trace approach in phased manners for quick ROI benefits in the transformation process of maturity of supply chain connectivity with advanced capabilities. ROI is faster as the manufacturers remain informed with real-time data/metrics of the production processes/procedures, customer demands and inventory requirements without having to do guess-work.
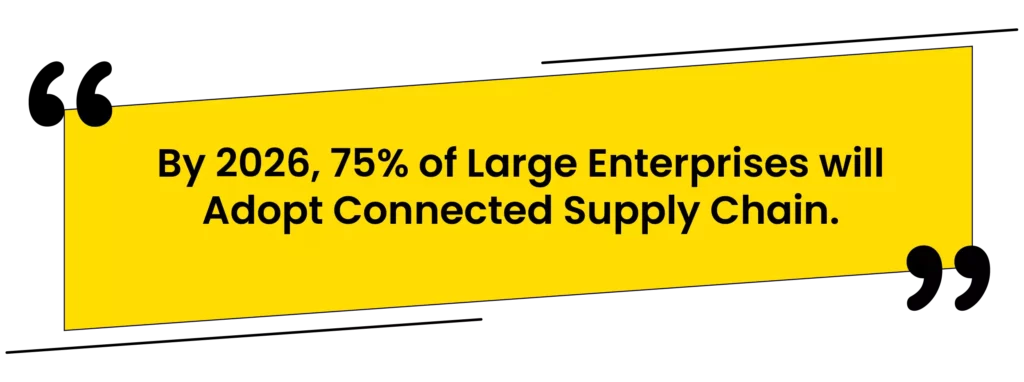
Those were some of the key components of the connected supply chain. Moving further, let’s explore the next smart manufacturing use case.
Robotics Automation
Robotics automation simply refers to employing/using robots for accomplishing physical work automation. The robotics automation concept is increasingly becoming a crucial and common attribute of the present and futuristic manufacturing companies. Robots are designed and developed with capabilities to perform tasks like welding, assembly, inventory handling, product packaging and so on. The early 1960s witnessed the working of robots in manufacturing industries, from then on employing robotics automation in manufacturing has been growing.
It is a common sight to witness more manufacturers leveraging robotics automation for wider number of operations in manufacturing. Robotics automation in manufacturing increases productivity, decreases wastage, ensures adequate inventory management, advances supply chain management, performs hazardous tasks and so on. The benefits of robotics automation will be elaborated in the following section.
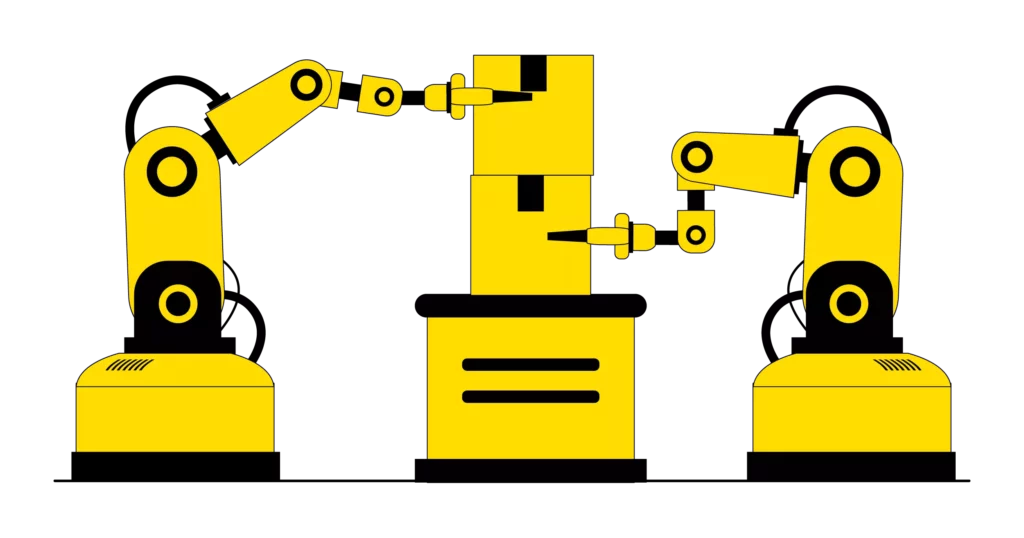
Benefits of Robotics Automation
The leveraging of robotics automation in manufacturing has benefits that are unique to the capabilities of robotics automation. This section identifies and attempts to elaborate on the same.
i) Saves Money and Time – Innovation has led to the enhancement of robots and that has led to increased sales of robots. With an increase in the sale of robots, prices have significantly reduced. Built-in capabilities of robots that mimic specific actions to accomplish tasks in manufacturing. Robots facilitate quality enhancements and regulatory standards in manufacturing operations and processes that translate to savings on labour costs and unplanned downtime. Robots are equipped to accommodate work round the clock (24/7) and can thus contribute to increasing production and mitigating unscheduled downtime.
ii) Highly Scalable – Robotics automation can function efficiently in both, high production environments as well as small-scale low production businesses. Recent advancements have powered faster transforming and re-setting of robots to be equipped to perform new and dynamic tasks within high as well as low medium work atmospheres.
iii) Ensure Work Efficiency and Reliability – Robotics automation automates physical work in manufacturing whilst replacing humans where dangerous and tedious tasks persist. The robots are programmed to conduct automated functions within the specific scope of manufacturing processes, this helps with achieving efficient work that is reliable.
iv) Creates More Jobs – Robotics automation creates growth opportunities that facilitate cost reduction, optimize production and stay competitive on the global frontiers. Robotics automation requires skills specific to its development and implementation, therefore accommodating more talent and expertise relating to robotics, automation and associated fields. The ROI generated equals growth that increases profits, creating jobs for the community as well as savings for customers.
Conclusion
On a concluding note, manufacturing industries are on the road to transformation with evolving technological advancements from time to time. The 5 manufacturing use cases listed and briefed in this article point to the potential and value of software and technology in the realm of manufacturing. These smart manufacturing use cases can be adopted by manufacturing industries to initiate and grow in achieving smart factory whilst competing in the global market for products and services.
The smart manufacturing use cases listed here do not limit thus far, the scope is vast and extends with emerging innovations and technologies.