Any manufacturing facility should be efficient enough to manage a large volume of inventory in raw materials, finished goods or products, and other packing materials to operate production seamlessly. A Bill of Materials, or BOM preparation, is necessary for any manufacturing or production process as it confirms all the necessary components for creating a finished product.
What is a Bill of Materials or BOM?
Bill of Materials or BOM means a structured way of organizing all raw materials and processes required to make a product. BOM also helps estimate each product’s total production cost by consolidating raw materials, process, and labor costs. It is usually represented in a hierarchical structure to understand the manufacturing requirements better and manage the total production costs.
Importance of BOM in manufacturing
Bill of materials helps to ensure that all necessary preparations are available before production begins. This way, BOM helps prevent production delays due to a lack of materials available and ensures the final product meets specifications. In addition, it helps estimate the cost of production by identifying all the necessary components, timelines, efforts, and associated costs. BOM is essential for determining a product’s profitability and setting prices.
Finally, the BOM effectively manages inventory levels. Supply chain managers can ensure they have enough raw materials inventory to meet demand without overstocking by knowing the necessary materials requirements for a product.
Why is a BOM Crucial for Production?
With the Bill of Materials, manufacturing, and production processes would be much more efficient. The BOM ensures that the correct parts are ordered and stocked correctly and helps minimize production errors. With a BOM, manufacturers can determine each product’s exact cost and ensure they profit from it.
The BOM is also essential for quality control and traceability purposes. By comparing the BOM to the finished product, the quality control team can identify any manufacturing and production errors that may have occurred while building the product.
In addition to these benefits, the BOM can also help with product design. By analyzing the BOM, designers and engineers can identify opportunities to reduce costs, improve quality, or enhance the product’s features. BOM analysis can make the product more competitive and increases profitability. Bill of materials management is essential to manufacturers and suppliers in the electronics, automotive, aerospace, and construction industries.
Following are the few benefits of having an effective bill of materials in manufacturing:
- Cost Savings: An effective BOM helps reduce costs related to excess inventory, wasted materials, surplus purchasing, and production downtime.
- Increased Efficiency: A BOM ensures that all necessary materials and components are available for the manufacturing line, which can improve production output and reduce lead times.
- Improved Quality: An accurate BOM ensures that suitable materials and components are used in the manufacturing process, which can improve the quality of the finished product.
- Better Planning: An effective BOM leads to effective production schedules, ensuring that the right product is produced at the right time and quantity.
What are the types of Bills of Materials?
There are three major categories of the bill of materials available.
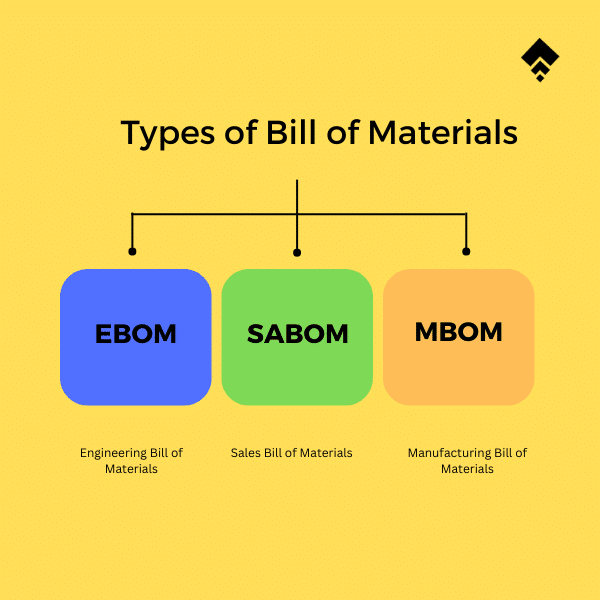
Engineering Bill of Materials (EBOM)
This type of BOM describes the product in terms of its engineering specifications, including the materials, parts, sub-assemblies, and quantities needed to complete the finished product.
Sales Bill of Materials (SABOM)
A sales bill of materials is designed for sales and marketing teams to provide technical customer service by giving a product breakdown regarding its features, functions, and benefits.
Manufacturing Bill of Materials (MBOM)
A manufacturing bill considers the production process, including the availability and cost of materials, tooling, labor, and manufacturing processes. The MBOM informs the procurement and production teams of the materials and assets resources needed to produce the product.
A manufacturing BOM structure consists of two layers.
- Single-level and
- Multi-level BOMs.
A single-level BOM is a plain list specifying a product’s different parts. It shows the relationships between components and the overall product and provides a comprehensive overview of the product’s assembly. Single-level BoM is suitable for small-scale production.
A multi-level BOM is a hierarchical representation of each part and assembly that forms a product. It demonstrates a product’s components and sub-components. A multi-level Bill of materials helps to determine the assembly process of production and identify the necessary parts for each step of production.
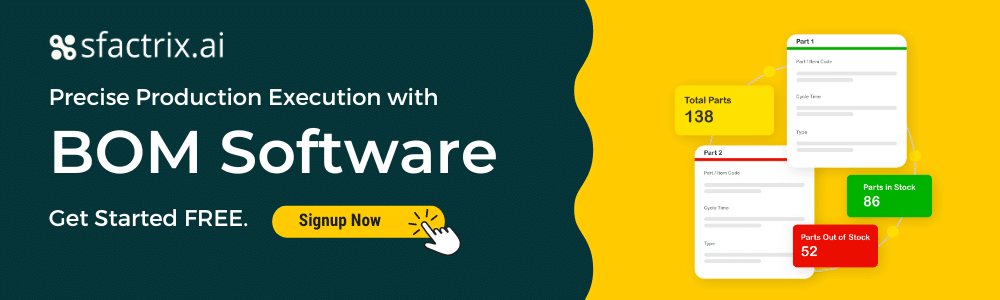
What are the components of a Bill of Materials?
Creating a BOM is an essential step in the product or parts development process. A bill of materials, or BOM, lists all the components and materials required to manufacture or assemble a product. The essential elements, parts, and more that are included in a BOM are as follows:
- BOM Level: This number indicates where the part or item falls in the BOM hierarchy.
- Part Number: Manufacturers assign part numbers to equipment spares. The part number shows a particular item with its specification.
- Part Name: The part name indicates a distinctive identification. It aids the users in identifying the part, just like the part number.
- Description: The description provides detailed information on the part ahead of the part name or number. A description helps to distinguish between pieces that seem identical. For instance, “screws” might refer to a specific type of screws, such as machine screws that are 1/2- and 5/8 inches long.
- Quantity: The number of components used in an assembly process.
- Metric Units: This specifies the unit of measurement used when buying and using a component. The exact amount is ordered when the measure is defined. For example, you purchase screws in numbers or tons. Bulk items may be acquired by weight or by the box.
- Type of Procurement: This details the method of obtaining the part or component. Options include buying the part using cash, supply agreement, consignment, etc.
Bill of Materials Creation Process:
A Bill of Materials creation process involves a comprehensive list of all the components, parts, and materials required to manufacture or assemble a product. Let’s see the process of how to make a bill of materials.
The creation of a BOM involves the following steps:
- Identifying design requirements: The first step in creating a BOM is identifying the product’s design requirements. This design includes determining the product’s functionality, performance, and necessities and identifying the necessary components.
- Listing components: The next step is to list all the components required to assemble the product. This list includes part names, numbers, descriptions, quantity, etc.
- Gathering data: Once the components are identified, the next step is to collect data on each component. This step includes product specifications, pricing information, lead times, and availability.
- Organizing the BOM: The BOM is then arranged in a structured manner, typically using a spreadsheet or database. The BOM should include part numbers, descriptions, quantities, and sources.
- Review and optimization: Finally, the BOM is reviewed and optimized to ensure that it meets the requirements of the product and is cost-effective. This step involves reconciling component availability, cost, and lead times to ensure timely and cost-effective delivery of components.
The BOM creation is crucial in product development, manufacturing, and supply chain management. It helps ensure that products are manufactured according to design specifications and meet quality, performance, and estimated cost.
BOM software for Preparation:
Bill of Materials or BOM software tools are highly significant for manufacturing or production businesses. A bill of materials management software provides specific instructions on assembling the product from procurement of raw materials to the finished product ready – including all the packaging and instruction, materials, costs, etc. Bill of materials software helps to centralize and streamline the entire supply chain.
Bill of Materials software helps monitor inventory levels, tracks usage, forecasts stock requirements, and places purchase orders for required components well in advance. It also helps automate and schedule production processes and ensures that goods are produced efficiently and within the specified timelines.
BOM software tools allow operation teams to share information and communicate effectively, which is particularly useful when working with teams in different locations or with remote workers.
Bill of Materials using SFactrix.ai:
SFactrix is an AI-based manufacturing execution system designed for small and medium businesses. SFactrix Smart MES offers an inbuilt Bill of Materials module for manufacturers. SFactrix.ai helps centralize the BOM through Cloud Service, which can be accessed anytime from anywhere to plan materials availability and restocking for production execution.
SFactrix offers both Single level BOM as well as complex multi-level BOM to meet all your manufacturing needs.
SFactrix offers a digitalized Bill of Materials (BOM) module that efficiently plans and executes production for simple or complex materials processes.
Following are the features provided by the SFactrix BOM module,
- SFactrix BOM solution provides complete visibility of materials planning, production planning, and execution.
- SFactrix BOM Solution provides features to estimate the making cost accurately by combining the materials requirements and processes.
- SFactrix BOM enables stakeholders, Plant managers, and operators to keep track of materials and processes.
- SFactrix BOM keeps track of the stock availability of parts and raw materials.
- SFactrix BOM helps manage work orders, Job allocations, Production scheduling, etc.
Conclusion:
Manufacturers can ensure that all necessary components are available before production begins by creating a bill of materials. It is also critical for calculating the cost of production, managing inventory levels, and ensuring product quality. Manufacturers can create efficient and profitable production processes by understanding the key components of a BOM and the complete BOM creation process.
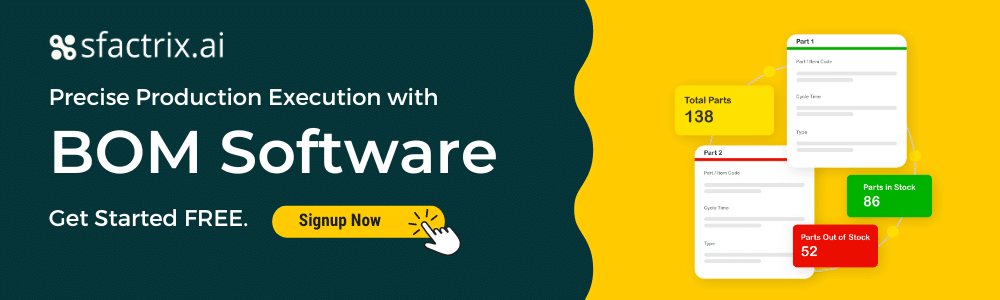