The manufacturing enterprises has undergone a massive transformation in recent years with the help of smart factories. These cutting-edge facilities use advanced technologies like Internet of Things (IoT) devices, artificial intelligence (AI), robotics, automation, big data analytics, augmented reality (AR), and virtual reality (VR) to improve efficiency, quality, and safety. But what exactly are smart factories, and how can they benefit your business? This article will provide overview to understanding the key components of smart factories, the technologies driving their success, and the steps you should take to implement solutions that will revolutionize your manufacturing processes.
Understanding Smart Factory Approach
Definition and Key Components
Smart factories leverage connected technologies to optimize manufacturing processes and supply chain operations. At their core, smart factories rely on sensors and data to improve real-time decision-making. This approach allows for improved efficiency, flexibility, and productivity.
Key components of smart factories include:
- Sensors and connected devices
- Cloud computing infrastructure
- Artificial intelligence and machine learning algorithms
- Robotics and automation
- Advanced analytics tools
- Augmented reality and virtual reality systems
These components work together to create a sophisticated, interconnected system capable of managing and optimizing every aspect of the production process. By leveraging these capabilities, manufacturers can improve quality control, reduce errors, and speed up production times.
The Evolution of Manufacturing
Smart factories represent the latest evolution of the manufacturing industry, which has seen many changes over the years. In the early days of manufacturing, everything was done by hand, with workers manually performing every step of the production process. This manual work was slow and labor-intensive. In the industrial revolution, machines began to take over some of these tasks.
As technology continued to advance, more tasks were automated, culminating in the rise of computer-controlled manufacturing in the 1980s and 1990s. Now, with the advent of smart factories, we are entering a new era of manufacturing, where machines and humans work together in a seamlessly integrated system that maximizes efficiency and productivity.
With the rise of smart factories, there has been a shift towards a more data-driven approach to manufacturing. This change means that manufacturers now collect and analyze vast amounts of data that allowing to make more intellitent decisions and optimize their operations accordingly.
Benefits of Smart Factory
So, what benefits can smart factories offer your business? Here are just a few of the key advantages:
- Improved efficiency and productivity
- Better quality control and error reduction
- Faster time to market
- Increased flexibility and adaptability
- Lower costs and increased profitability
- Enhanced safety for workers
These benefits are achievable thanks to the advanced technologies that power smart factories. By leveraging the capabilities of IoT devices, AI and machine learning algorithms, robotics, automation, big data analytics, and AR/VR systems, manufacturers can drastically reduce downtime, optimize equipment utilization, and identify and address issues in real time. Additionally, they can gain valuable insights into consumer preferences and behavior, allowing for more precise supply chain management and inventory control.
For example, sensors and connected devices can monitor machine performance and detect potential issues before they become major problems. This new technology can help reduce downtime and maintenance costs and improve overall equipment utilization.
AI and machine learning algorithms can analyze data from sensors and other sources in real-time, allowing manufacturers to identify patterns and trends that may be difficult to detect otherwise. This model can help optimize production processes, improve quality control, reduce waste, and minimize the risk of errors.
Robotics and automation can be used to perform repetitive or dangerous tasks, freeing up workers to focus on more complex and creative tasks. This approach can help to improve efficiency and productivity, as well as enhance safety for workers.
AR/VR systems can provide workers with real-time information and guidance, allowing them to perform tasks more quickly and accurately. This solution can help reduce errors, improve quality control, and enhance worker training and development.
In summary, smart factories represent the future of manufacturing. By leveraging the latest technologies and data-driven approaches, manufacturers can optimize their operations, improve efficiency and productivity, and stay ahead of the competition.
Technologies Driving Smart Factories
Internet of Things (IoT)
IoT is a network of connected things that share data and communicate with each other in real time. In smart factories, IoT devices monitor and control every aspect of the production process. These devices can measure temperature, humidity, pressure, and other variables, allowing for precise control over environmental conditions. The Industrial IoT Platform track equipment performance and identify potential issues before they become critical.
For example, IoT devices can monitor a paint booth’s temperature and humidity levels. By maintaining optimal conditions, manufacturers can ensure that the paint dries evenly and produces a high-quality finish. IoT devices can also be used to monitor the performance of robotic arms, ensuring that they operate within safe and efficient parameters.
Artificial Intelligence (AI) and Machine Learning
AI and ML algorithms are used in smart factories to analyze vast amounts of data in real-time and make better decisions. These algorithms can identify patterns and trends humans might miss, allowing for more precise control over production. For example, AI can optimize energy usage, reducing costs and greenhouse gas emissions.
AI and machine learning can also predict equipment failures before they occur. These algorithms can identify patterns that indicate impending equipment failure by analyzing data from sensors and other sources. This new technology allows manufacturers to schedule maintenance before a breakdown occurs, reducing downtime and costs.
Robotics and Automation
Robotics and automation are the most visible aspects of smart factories. These technologies automate repetitive tasks, freeing workers to focus on more complex and creative work. Robotics and automation can also improve safety by reducing the risk of accidents and injuries.
For example, robotics and automation can assemble complex products like automobiles. Manufacturers can increase production speed and reduce errors by automating the assembly process. Robotics can also perform dangerous tasks, such as welding or painting, reducing the risk of worker injury.
Big Data and Analytics
Big data analytics is essential for smart factories, allowing manufacturers to gain insights into every aspect of their operations. By analyzing data from machines, sensors, equipment, and other sources, manufacturers can identify areas of inefficiency and to make data-driven decisions to improve productivity and reduce costs.
For example, big data analytics can be used to optimize the supply chain. By analyzing data from suppliers, manufacturers can identify potential bottlenecks and take steps to mitigate them. Big data analytics can also optimize production schedules, ensuring equipment and workers are utilized efficiently.
Augmented Reality (AR) and Virtual Reality (VR)
AR and VR systems enhance training and education programs for workers in smart factories. By providing immersive, realistic training scenarios, workers can gain valuable experience without risking injury or equipment damage.
For example, AR and VR can train workers on complex equipment like CNC machines. By providing a virtual environment, workers can practice operating the equipment without the risk of damaging the actual machine. AR and VR can also simulate emergency scenarios, allowing workers to practice responding to potential safety hazards.
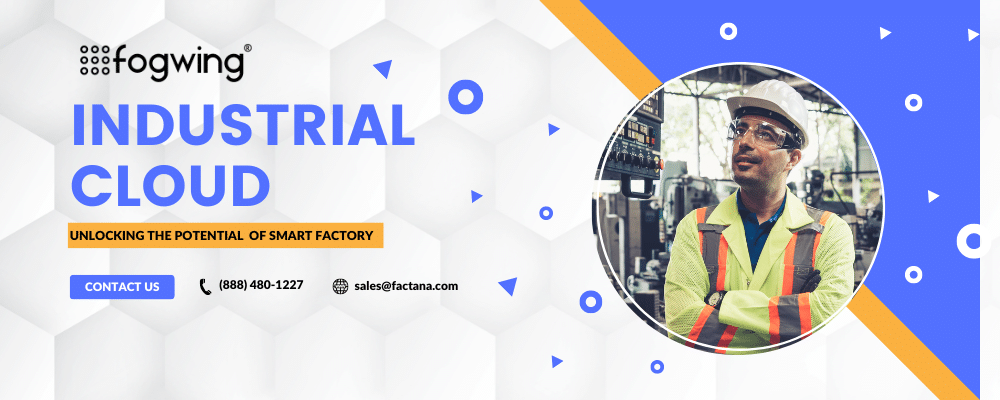
Implementing Smart Factory Solutions
Assessing Your Current Manufacturing Processes
The first step in implementing smart factory solutions is to assess your current manufacturing processes. This assessment involves analyzing every aspect of your production process. You will want to identify areas of inefficiency, waste, and potential safety hazards.
Identifying Opportunities for Improvement
Once you have identified the areas that need improvement, the next step is to look for opportunities to optimize your processes. This new opportunity might involve introducing new technologies like IoT devices, robotics, and automation or reorganizing your production line to reduce bottlenecks and speed up production times.
Developing a Smart Factory Roadmap
After identifying areas for improvement, it’s important to develop a detailed roadmap for your smart factory implementation plan. This roadmap should include timelines, budgets, and goals for each project phase. It should also include a plan for training and upskilling your workforce and measures to address any potential resistance to new technologies or processes.
Overcoming Implementation Challenges
Finally, it’s important to acknowledge that implementing smart factory solutions can be challenging. Some of the key challenges you may face include:
- Resistance to change from workers
- Cost considerations
- Security concerns
- Integration with legacy systems
However, these challenges can be overpowered with the right planning and preparation. By enlisting the support of your workers, investing in training and education programs, and partnering with experienced technology providers, you can create a smart factory that delivers enormous benefits for your business.
Unlocking the Potential of Smart Factories – The Future of Manufacturing is Here
Manufacturers can create smart factories that revolutionize the production process by leveraging advanced technologies like IoT, AI, robotics, automation, big data analytics, and AR/VR. With increased efficiency, flexibility, and productivity, smart factories offer various benefits for businesses. However, implementing these technologies requires careful planning and preparation. By assessing your current manufacturing processes, identifying opportunities for improvement, developing a detailed roadmap, and addressing any implementation challenges, you can unlock the full potential of smart factories and position your business for long-term success.
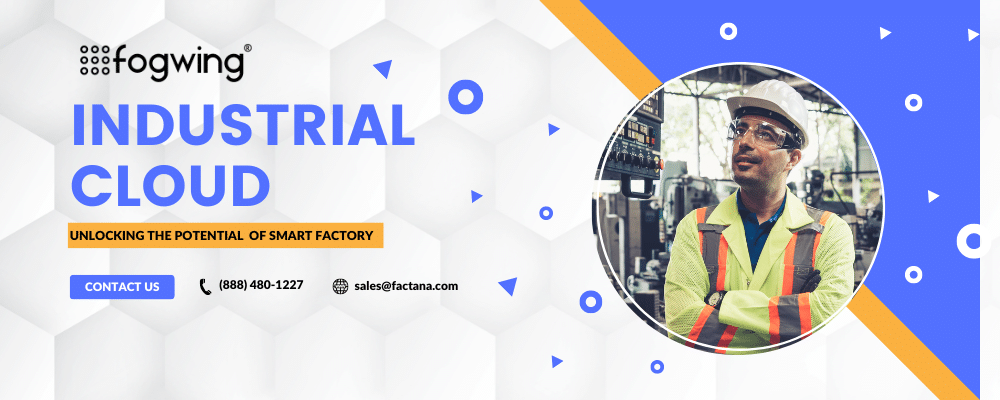