In the fast-paced manufacturing world, success is measured by more than just production numbers. Reliability and maintainability are key factors that can make or break a company’s long-term success. Without them, even the most impressive machines and skilled workers will eventually falter. In this blog post, we’ll explore why reliability and maintainability are important for manufacturers and how they can achieve these goals in their operations. From reducing downtime to improving safety, there are countless benefits to prioritizing these critical factors – let’s dive in!
What is Reliability and Maintainability?
Asset Reliability and maintainability are key factors for long-term success in manufacturing. In this blog article, we’ll introduce these concepts, including their importance in manufacturing. We’ll also discuss some challenges associated with reliability and maintainability and how to overcome them.
Definition of Maintainability
The definition of maintainability refers to the ease with which a system or product can be maintained over time. This includes everything from routine maintenance tasks like cleaning and lubrication to more complex repairs and upgrades. A highly maintainable product should be designed with serviceability in mind, using modular components that can be easily replaced or upgraded as needed. It also requires clear documentation and training materials to ensure that technicians have the knowledge they need to perform maintenance correctly.
In addition, maintainability is an important consideration when it comes to cost-effectiveness; products that are difficult or expensive to maintain may not be worth the investment in the long run. Ultimately, prioritizing maintainability ensures that products remain functional and useful for their intended lifespan, reducing waste and maximizing value for users.
The Role of Maintainability in Manufacturing
Maintainability is a critical factor in the long-term success of any manufacturing operation. By definition, maintainability is the degree to which an item can be maintained in specified conditions and performance for a given period. In other words, it calculate how easy it is to keep something running smoothly.
Several factors, including design, materials, construction, and environment, contribute to maintainability. The goal is to ensure all these elements work together to minimize downtime and maximize efficiency.
One of the most important aspects of maintainability is preventive maintenance. This is a proactive approach to keeping equipment and machinery in good working order. It involves regularly scheduled inspections, servicing, and regular replacement of worn or damaged parts.
Another key element of maintainability is troubleshooting. This is the process of identifying and resolving problems as they occur. The most important solution in place to quickly identify and resolve issues so they don’t cause further damage or downtime.
An effective maintainability program requires buy-in from everyone involved in the manufacturing process. From management to frontline workers, everyone must follow best practices for preventive maintenance, troubleshooting, and repairs. When everyone is on board, it’s easier to keep things running smoothly and avoid costly disruptions down the line.
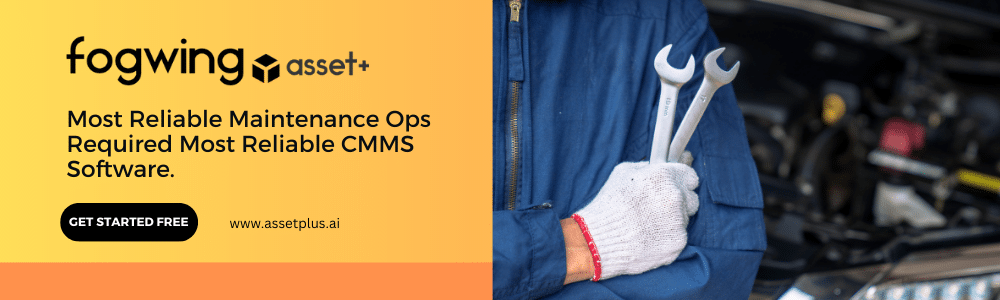
Strategies for Ensuring Reliability and Maintainability
Several strategies can be employed to ensure the reliability and maintainability of manufacturing equipment and processes.
One key strategy is to design for asset reliability and maintainability from the outset. This means, taking into factors such as ease of access for maintenance, use of durable materials resistant to wear and tear, and incorporating redundancy into critical components or systems.
Another important strategy is implementing rigorous testing procedures during the development and production phases. This includes testing under various conditions (e.g., temperature, humidity, vibration) to simulate real-world conditions as closely as possible.
Once equipment or processes are in operation, monitoring them closely and performing regular maintenance according to manufacturer specifications is important. This will help to identify all potential problems before cause downtime or expensive repairs.
Benefits of Investing in Reliability and Maintainability
There are many benefits to investing in asset reliability and maintainability in manufacturing. The benefit is that it can help to reduce downtime and increase production efficiency. In addition, investing in these areas can also help to improve product quality, safety, as well as reduce scrap and rework costs.
In the long run, investing in reliability and maintainability of a system can help to improve your company’s bottom line. Industry can sell more products at a higher price by reducing downtime, increasing production efficiency, and improving product quality. In addition, you can save on manufacturing expenses by reducing scrap and rework costs. All these factors can add to your company’s significant financial savings.
Challenges with Implementing Reliability and Maintainability
As with any initiative, some challenges come with implementing asset reliability and maintainability programs. The biggest challenge is usually organizational. It takes time to get everyone with the program and to buy into the changes that need to be made. There is a need of understanding of the program’s goals and how everyone can contribute to achieving those goals.
Another challenge is finding balance between maintaining equipment and keeping production running. There is always tension between these two factors; finding the right mix can take time and effort. Too much focus on maintenance can lead to downtime and lost production, while too little focus can result in more breakdowns and increased costs.
It is a must plan, when things go wrong. There will always be unexpected breakdowns and issues that arise, no matter how well you plan or how good your maintenance program is. Having a solid contingency plan will help you minimize the impact of these events when they occur.
Steps to Maximize Outputs from Reliability and Maintainability Programs
Reliability and maintainability of a system are key factors for long-term success in manufacturing. Manufacturers can improve equipment uptime, reduce maintenance costs, and enhance product quality by maximizing outputs from reliability and maintenance programs.
Here are some tips for maximizing outputs from reliability and maintainability programs:
- Set realistic goals for reliability and maintainability.
- Work with suppliers to ensure that components and materials meet specifications.
- Use statistical methods to identify trends and analyze data.
- Implement preventive maintenance programs to keep equipment running efficiently.
- Conduct regular audits of the reliability and maintainability program to identify areas for improvement
Conclusion
Manufacturing organizations must ensure that their products and processes are reliable and maintainable to achieve long-term success. Asset Reliability and maintainability are essential components of a good product but can be difficult to measure and quantify.
This article has explored the importance of these factors in the manufacturing process, providing insight into why reliability and maintainability should take precedence over other considerations when creating a successful manufacturing organization.
By understanding how reliability and maintainability of a system affect production efficiency, cost reduction, customer satisfaction, quality control assurance, safety compliance standards, environmental protection practices, and overall risk management strategies, manufacturers can use this knowledge to create an effective approach for achieving long-term success with their products.
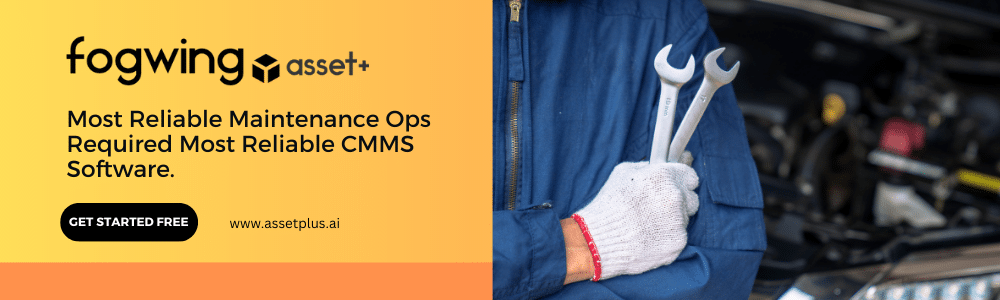