In the complex world of manufacturing, where product quality and operational efficiency are paramount, one key metric stands out as an essential measure of success: First Pass Yield (FPY). FPY, also known as First Time Yield (FTY), is a critical indicator of a manufacturing process’s effectiveness and the quality of its output. In this comprehensive guide, let us explore what FPY is, why it matters, how to calculate it, and, most importantly, how to improve it to drive better results in your manufacturing operation.
What is First Pass Yield (FPY)?
First-pass yield is a fundamental quality metric used in manufacturing. It quantifies the percentage of products or units that successfully pass through the entire production process without requiring any rework, repair, or corrective actions. In simpler terms, it tells you how often your manufacturing process gets it right on the very first try.
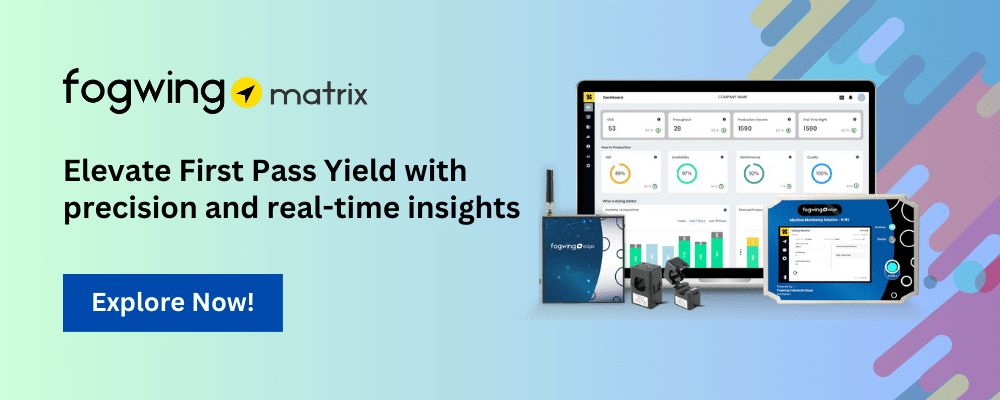
Importance of First Pass Yield (FPY)
In manufacturing, achieving a high FPY is crucial as it directly affects both the quality and cost of production. A low FPY can result in increased costs due to rework, scrap materials, and delays in production schedules. On the other hand, a high FPY indicates that the production process is running smoothly with minimal waste, leading to higher customer satisfaction and profitability.
Understanding why FPY matters is the first step in appreciating its significance in manufacturing. Here are some compelling reasons:
1. Cost Reduction: As mentioned earlier, a low FPY can result in increased costs due to rework and scrap materials. This not only adds additional expenses but also leads to longer lead times and delayed customer deliveries. By improving FPY, manufacturers can reduce these costs and improve their bottom line.
2. Improved Quality: A high FPY means that most of the products on the production line are defect-free. This translates into higher quality products for customers, leading to better customer satisfaction and retention.
3. Time-Saving: When a product fails during its first pass through manufacturing, it requires additional inspection, rework, or repair before it can be sent out to customers. This can delay the entire production process and affect delivery schedules. By improving FPY, manufacturers can save time and improve their overall production efficiency.
4. Process Improvement: Tracking First Pass Yield provides valuable insights into the efficiency of different stages of the production process. By identifying areas with a low FPY, manufacturers can focus on implementing improvements to reduce defects and increase productivity.
5. Better Decision-Making: FPY is an essential metric for decision-makers in manufacturing companies. It provides a clear understanding of the state of production. It helps make data-driven decisions to improve processes and reduce costs.
First Pass Yield Calculation
Calculating FPY is relatively straightforward, The First Pass Yield formula is:
FPY=Total Units Produced/ Total units Started ×100%
Let’s break down the components of this formula:
Good Units Produced: This refers to the number of units that successfully pass through the manufacturing process without needing any rework, repair, or corrective actions. These units are the ones that meet the required quality standards.
Total Units Started: This represents the total number of units that entered the production process. It includes both the good units and any defective units that require rework.
To calculate FPY, divide the number of good units produced by the total units started and then multiply by 100% to get the result as a percentage. The resulting rate is your First Pass Yield.
For example, if manufacturing starts with 100 units and 90 units pass through the process without any rework, your FPY would be:
FPY= Total Units Produced/ Total units Started ×100%
FPY=90/100 X100% = 90
In this scenario, your First Pass Yield is 90%, indicating that 90% of the units were produced correctly on the first attempt.
Steps to Improve FPY
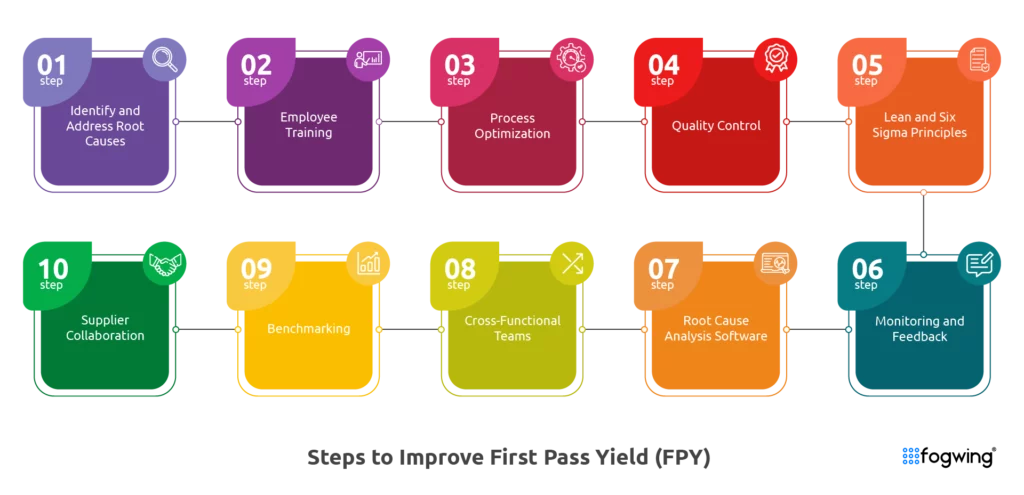
Improving FPY is an ongoing process that requires dedication and a systematic approach. Here are the steps you can take to enhance your manufacturing process and increase your first-pass yield:
1. Identify and Address Root Causes:
Begin by conducting a thorough analysis to determine why defects are occurring. Pinpoint the root causes of these defects. Common root causes may include equipment malfunctions, human errors, or issues with raw materials.
Once you’ve identified the root causes, implement corrective actions to address them. This might involve machine maintenance, process adjustments, or changes in supplier relationships.
2. Root Cause Analysis Software:
Implementing specialized software for root cause analysis can streamline the process of identifying and addressing the root causes of defects. This can lead to more effective and faster improvements in your manufacturing process.
3. Employee Training:
Invest in training programs for your employees. Well-trained staff are less likely to make errors, and they’ll be better equipped to identify and address issues in the manufacturing process. Continuous education and skill development are key to improving First Pass Yield.
4. Process Optimization:
Constantly refine and optimize your production process. Streamline operations to reduce the likelihood of errors occurring. Implement Lean principles, which focus on eliminating waste, and Six Sigma methodologies, which aim for process improvement and error reduction.
5. Quality Control:
Introduce robust quality control measures at key points in the production process. It includes inspection and testing to catch defects early. The earlier you detect and address issues, the less impact they will have on your FPY.
6. Lean and Six Sigma Principles:
As mentioned, Lean and Six Sigma principles can significantly contribute to your FPY improvement efforts. Lean principles help eliminate non-value-adding steps in the production process, reducing errors and defects. Six Sigma emphasizes data-driven decision-making and process improvement, leading to higher quality and better FPY.
7. Monitoring and Feedback:
Regularly monitor your FPY and collect data. Data is a powerful tool for making any informed decisions. Use this data to provide feedback to employees and management. Implement a culture of continuous improvement where everyone is focused on achieving higher FPY.
Tools and Technologies for Tracking and Analyzing FPY Data
In today’s fast-paced and competitive manufacturing industry, it is essential for companies to continuously monitor and improve their FPY rates. This requires effective tools and technologies for tracking and analyzing FPY data, which can provide valuable insights into production processes and help identify areas for improvement.
1. Statistical Process Control (SPC) Software:
One of the most used tools for tracking and analyzing FPY data is SPC software. This powerful tool uses statistical methods to analyze data from various stages of the production process. It helps identify any variations or trends that may affect the overall yield. SPC software also allows manufacturers to set control limits, generate charts and graphs, and create reports to track FPY over time.
2. Production Monitoring System:
Production Monitoring Software is another popular technology used in modern manufacturing facilities to track and analyze FPY data. It offers real-time monitoring of production processes, allowing manufacturers to identify deviations or issues that could impact yield. It also provides detailed reporting features highlighting specific areas where improvements can be made.
To explore a readily available production monitoring solution, click here; Best Production Monitoring Solution | Fogwing Industrial Cloud
3. Barcode Scanners:
Barcode scanners are widely used in manufacturing facilities to track products as they move through different stages of the production process. By scanning barcodes at each stage, manufacturers can collect real-time data on product flow, cycle times, quality checks, and final yields. This information can then be used to identify bottlenecks or inefficiencies in the production line that may be impacting First Pass Yield.
4. Internet of Things
IoT sensors are becoming increasingly popular in manufacturing as they provide real-time data on various aspects of the production process. These sensors can be placed on machines, equipment, and even products to collect data on temperature, humidity, vibration, and more. By analyzing this data, manufacturers can identify potential FPY issues and proactively improve.
5. Quality Management Systems (QMS):
QMS software is designed to help companies manage quality control processes and continuously improve their products and processes. It offers document management, corrective action tracking, and root cause analysis – essential for tracking and analyzing FPY data.
6. Cloud-based Data Analytics:
Cloud-based data analytics platforms allow manufacturers to store, manage, and analyze large amounts of First Pass Yield data in a secure and accessible way. With advanced analytics capabilities and machine learning algorithms, these platforms can identify patterns or anomalies in the production process that may impact yield.
7. Digital Dashboards:
Digital dashboards are user-friendly tools that provide real-time visualizations of key performance indicators (KPIs) such as FPY rates. By displaying this information in a centralized location, digital dashboards enable manufacturers to identify any issues affecting FPY and take immediate action quickly.
Which Tool Leads to Higher FPY?
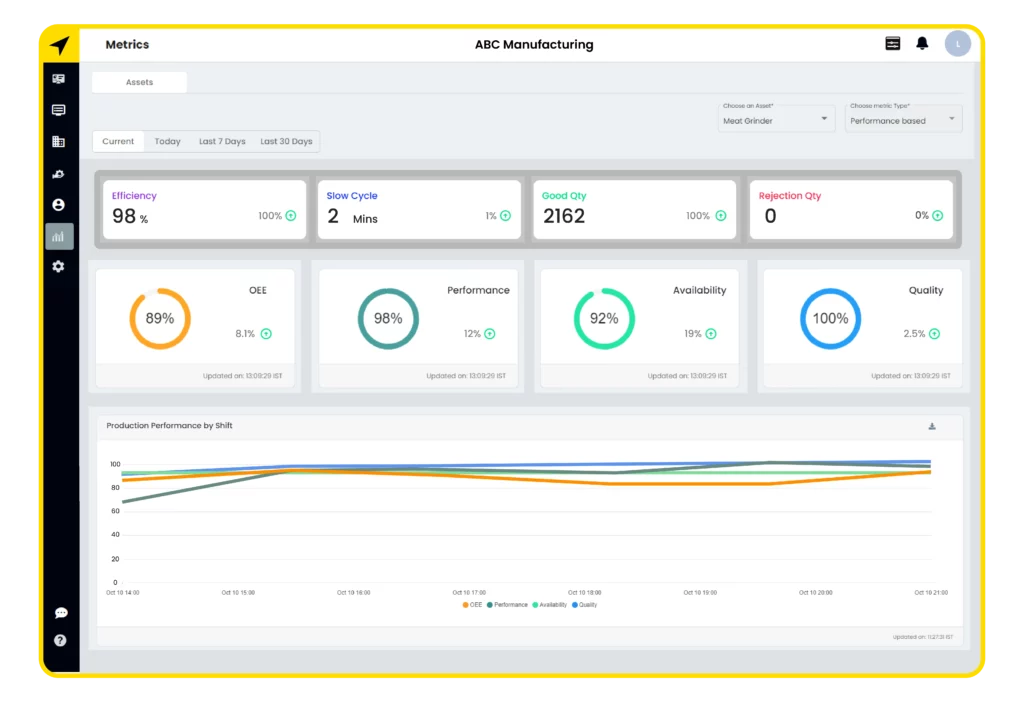
Fogwing Matrix is an IoT-based production monitoring solution designed to help improve various aspects of manufacturing and industrial processes, including First Pass Yield (FPY). Fogwing Matrix is crucial in improving First Pass Yield (FPY) in manufacturing by providing real-time visibility, data analysis, and process control. Here’s how Fogwing Matrix contributes to FPY improvement:
- Fogwing Matrix can collect and analyze real-time data from various sensors and devices on the shop floor. This data includes information about machine performance, environmental conditions, and the quality of materials. Monitoring these parameters in real-time can help identify issues or deviations that could lead to product defects.
- Fogwing Matrix is empowered with automated quality control checks by integrating sensors and inspection systems. It can, thus, quickly identify defects or deviations from quality standards, enabling timely intervention to prevent defective products from progressing through the manufacturing process.
- Fogwing Matrix offers analytics capabilities that allow manufacturers to gain insights from historical data. By analyzing past performance, it can identify patterns, root causes of defects, and improvement areas, all of which can contribute to a higher first-pass yield.
- Fogwing Matrix leverages machine learning (ML) and artificial intelligence (AI) algorithms to predict and prevent defects by learning from historical data. This can help identify correlations and subtle patterns that might not be possible for humans to detect.
- Fogwing Matrix software also alerts and sends notifications when deviations or anomalies are detected. This enables immediate action to correct the issue, reducing the likelihood of producing defective products.
- Fogwing Matrix provides automated OEE calculations, a key metric for measuring equipment efficiency. By identifying and addressing factors that reduce OEE, such as downtime, performance losses, or quality defects, the software helps improve overall equipment effectiveness and, by extension, first-pass yield.
To know more about how Fogwing Matrix helps in monitoring and improving various other manufacturing KPIs, read this. Key Manufacturing KPIs To Be Monitored |Fogwing.io
Conclusion
In conclusion, first pass yield (FPY) is a crucial metric for manufacturers to track and improve. By adequately calculating FPY and identifying areas for improvement, companies can reduce waste, increase efficiency, and ultimately save time and money. Implementing the strategies mentioned above, such as focusing on quality control processes, investing in employee training, and utilizing data analysis tools, can help to achieve a higher FPY rate. With continuous efforts towards improving first-pass yield, manufacturers can optimize their production process and deliver high-quality products to their customers.
To get a comprehensive outlook of the Fogwing Matrix Solution, click here Best Production Monitoring Solution | Fogwing Industrial Cloud
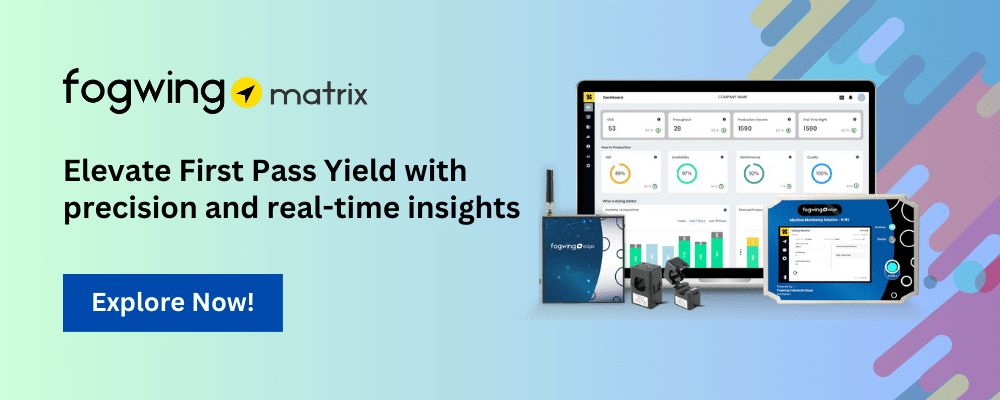