What is the Bill Of Materials (BOM)?
Bill of Materials, colloquially identified as a recipe for the manufacturing of a product is a blueprint for manufacturing irrespective of the type of commodity being manufactured. The Bill of Materials in manufacturing is an all-inclusive or comprehensive catalogue of parts, assemblies, sub-assemblies, intermediate assemblies, documents, drawings and other materials required to build a product. The BOM is often recognized as representative of the hierarchical structure for the creation of a product.
The Bill of Materials is a detailed document that proceeds to mention the name, description, cost and quantity of each required component for manufacturing a product. Providing instructions on the methods of use for materials, designating sequence of manufacturing processes and establishment of procurement channels for acquisition of raw materials are all listed in the Bill of Materials. Commonly, several disciplines (design and development, engineering and manufacturing, operations, document management, vendors, marketing, logistics, and more will collaborate on BOM to effectively execute optimized production.
In the manufacturing business, the success of a finished product depends on the procurement and processing of different yet specific materials along with the execution of procedures. The development and completion of a product requires particulars on various parameters to be formally structured by each department of the industry for purposes of clarity, accountability and investment streamlining.
With inputs from each department, a final document concerning the specifics for the complete development and management of a product can be created to channel manufacturing and associated work. This document is formally addressed as the Bill of Materials in manufacturing and plays a pivotal role in the development, execution and commercialization of a product/commodity.
The manufacturer’s requirement decides the kind of BOM; it can either be an implosion or explosion in nature. The implosion view of BOM display from the lowest level of requirements like that of parts and sub-components with gradual development in each step to eventually achieving the final product. Whereas the explosion view of BOM displays the inverse of the implosion view, starting from the final product (highest level) to the division of each part or sub-components.
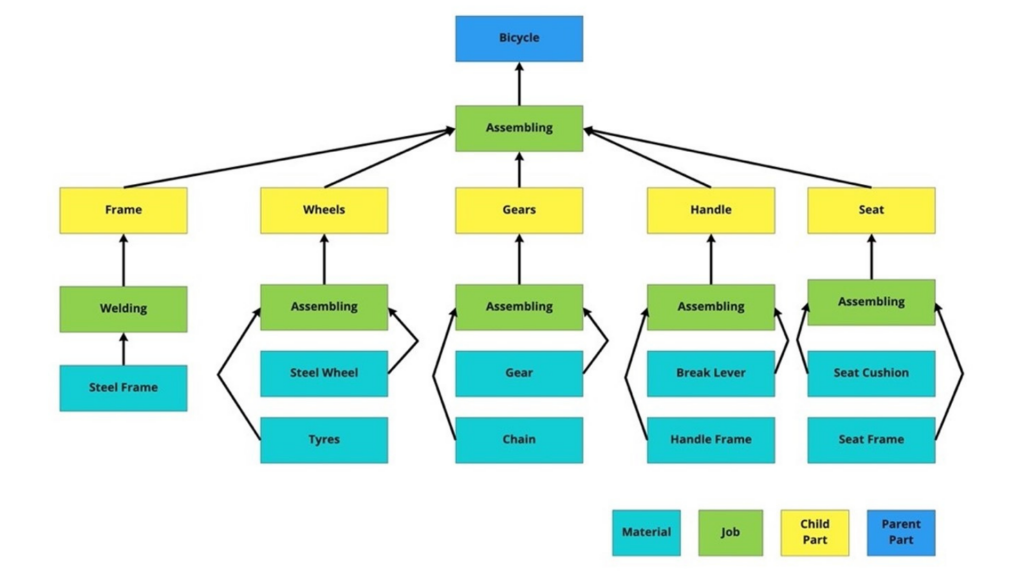
How to Create Bill of Materials in manufacturing?
In the product management cycle to ensure consistency, quality and efficiency throughout the manufacturing process, creation of a Bill of Materials is vital. Despite the many benefits of BOM, it cannot be denied that putting together a BOM needs invested time and efforts. Given the effort and time that goes into creating a Bill of Materials, it can be thought of as an exercise to know the product, explore potentials and add-ons while determining its margins too.
Single-Level Bill of Materials
A single level Bill of Materials structure is a simple list of requirements and processes to produce a product. The single level displays assembly, sub-assemblies and materials once or at one level with the required quantity.
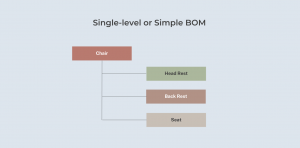
Multi-level Bill of Materials
A multi-level Bill of Materials structure depicts an elaborate intended view of parent and child parts, assemblies and intermediate assemblies required to build the product along with specific quantities. It is intricate in nature and specifies all components directly or indirectly used in the production process.
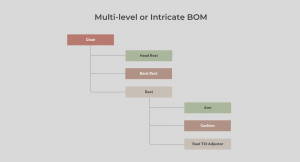
Although, simple structure of BOM seems ideal, it cannot suffice for the development and manufacturing of complex products. Complex products such as a laptop would require ample specific components and processes to be adhered and therefore choosing a simple structure BOM will hinder the identification of any quality or features issue without clear depiction of all components used/put together. Let’s further explore contents of Bill of Materials.
What does BOM include?
The product that is being manufactured typically impacts the content of Bill of Materials. Having mentioned that, some indicators in the Bill of Materials remain constant or are primary to a good BOM.
- Material Name – Each material, assemblies, and ingredient must have a name or given a unique name that is detailed in nature on the Bill of Materials.
- Process Name – Accounts for the processes in the manufacturing requirement to produce desired product. It is exclusive to the process names and types that materials are subject to undergo in the making of a product.
- Procurement Type – It reflects the documenting of how the purchase of each material is done (off-the-shelf or customized) with a goal to create efficiencies in manufacturing, planning and procurement activities.
- BOM Degree – Assign each material, assemblies and / or ingredient with an intelligent / non-intelligent / number scheme identifying its position in the of Bill of Material hierarchy and its phase in the production process. This helps easy recognition of materials within each hierarchy of product manufacturing.
- Description and Notes – A precise and concise description of each material used in the production process must be included in the Bill of Materials. Additional information to facilitate better understanding of the product must be stated in the BOM.
- Units of Measure – It is the unit employed to measure the quantity of material/part in stock or required. For example, it may be pieces (pcs), kilograms (kgs) or any other representing the measure unit of materials.
- Quantity – The quality of assemblies, sub-assemblies, and other materials required to produce each product/part is to be clearly mentioned in the Bill of Materials. This enables the BOM to serve as an accurate purchasing asset and establish a safety stock with insights on reorder and prediction-based maintenance.
- Lead time – The duration between initiation and completion of processes in manufacturing.
- Quality criteria – Upfront defined measurable tests and test results to indicate and confirm that quality objectives of products in manufacturing are being met.
- Scrap Count – The count or percentage of materials ruined while in the different processes of manufacturing.
With the contents of BOM, exploring the types of BOM is also essential in pursuing a holistic understanding of Bill of Materials.
Types of BOM
The classifications of the Bill of Materials are many and is a subjective matter given the project under consideration and the specific requirements of enterprise/company. While the types of Bill of Materials may vary, the two most popular and crucial ones for purchasing and supply chain management are the Manufacturing Bill of Materials (MBOM) and Engineering Bill of Materials (EBOM).
Some of the types of BOMs used in manufacturing are listed below:
Engineering BOM
This is usually identified as product recipe from design stand point. Predominantly, software (computer-aided design or electronic design automation) used in the engineering department becomes the origin of product design. The EBOM includes directions and components specific to engineering phase of the product. It is exclusive to parts, sub-assemblies, raw materials and tools from the engineering context/perspective.
Manufacturing BOM
This type of Bill of Materials is employed when a business needs to display all materials, parts, assemblies required to build a finished product/desired product. Materials/parts that require processing prior to being used in the manufacturing are to be included in the manufacturing bill of materials. Details that are disseminated to all integrated business systems from procurement of raw materials to processing materials to build product, inclusive of Enterprise Resource Planning (ERP), Manufacturing Execution System (MES) and Materials Resource Planning (MRP).
Assembly BOM
Assembly orders are used to make end items from components in a simple process by one or more basic resources. Assembly BOM lists parent and child parts/materials and categorizes the same as sales item. As defined by Microsoft, an assembly BOM is the master data that defines which component items go into an assembled end item and which resources are used to assemble the assembly item.
Configurable BOM
Customer-specific requirements form the basis of the configurable bill of materials. All components needed to design, develop and produce product inline with customization as directed by customer. The configurable bill of materials is largely employed by industries that are capable of accommodating customization through configurable products and processes to manufacture likewise.
Sales BOM
Ahead of assembly, during the sales phase, the sales bill of materials provides details of a finished product. In the sales BOM, the finished product and components appear separately in the document of sales order. Parent component is usually listed as the sales item and not as an inventory component, the child parts/components will be listed as sub-items.
Services BOM
Typically developed by engineers during the product design phase, the service bill of materials is an inclusive list of all parts/components, installation steps, repair instructions to service technicians to employ when installing or servicing the product onsite at the customers.
Listing few of the types of BOM further brings to the next phase of exploring. In order to understand the nuances of BOM, the benefits are to be clearly stated. On the same lines, exploring the benefits of BOM is the next task.
Benefits of BOM
The BOM becomes the basis of furthering with manufacturing a product. It adds structure and value to a variety of procedures and processes in manufacturing. This section points to some of the critical benefits of Bill of Materials.
Cost Optimization
Accurate costing of finished products are essential and the BOM helps with the same. Additionally, creating Bills of Material eliminates inaccurate calculation of cost of goods sold (COGS). With the reliable calculation of COGS using BOM, profits and margins are rightly recognized leaving no room for incorrect costing. All costs are accounted and therefore optimized.
Transparency
Bill of Materials provides a framework for all teams to follow, it allows the chance for teams in the procurement, processing and repair to understand and execute their expertise inline with the requirements of product design, development and quality assurance.
Availability
Creating a BOM ensures to outline the necessary requirements (parts, sub-components, materials, processes, procedures and so on) thereby guides the purchasing of items / materials and helps efficient inventory management. While the BOM forecasts for the production of a product, subsequently it helps forecast other components / sub-specifications to create the final product by keeping availability flexible.
Reduced Wastage
Excess inventory generates unnecessary waste. Accurate Bill of Materials can significantly optimize stock levels. It prevents unwanted assembling of wrong parts that triggers incurring value depreciation in the manufacturing. BOM helps with ordering the right amount of stock to suffice for production, or meet schedules and or fulfill forecasted sales. BOM allows industries to adopt and practice just-in-time method of inventory management.
Process Improvement
Bill of Materials provides a structure and framework for production processes. With a formal structure in place, workflows adhere and improve subsequently. The overall production process can be impacted positively to improve profitability and total efficiency.
With briefly looking into the benefits of Bill of Materials, it’s time to step further to explore and unwrap Manufacturing Execution System in creating and following BOM.
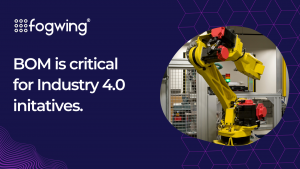
MES software and BOM
MES software can become a catalyst for progressive change in the manufacturing industry. Industrial automation, real-time monitoring of factory operations, process optimization, digital inventory management, smart logistics/supply chain management and much more potentials of MES can transform manufacturing to become Industry 4.0 enabled.
One of the many potentials of an MES software is its ability to integrate processes, tools and operations. With integration comes a centralized system of communication for close knit management of factory operations at real-time. MES software serves as a platform to integrate BOM along with the many processes and operations of factory in the pursuit of transforming legacy manufacturing to self-reliant smart manufacturing.
Integration
MES facilitates the integration of Bill of Material to further with the work order management, job management and overall supply chain management. Each procurement and processing channels connected via AI-enabled MES allows BOM to be structured, executed and maintained throughout manufacturing thereby furnishing accurate documentation and profit-oriented financial implications.
Accountability
Accounting for every penny spent in manufacturing is crucial in determining the prospective growth of the business, else chances of failure rise. A sense of accountability in induced into the people and activities in manufacturing with MES software that serves as a single entity holding together the many aspects, phases and operations of a factory. All activities and costing drafted in the BOM will reflect at real-time in the MES software leaving no loop-holes for unaccountability.
Materials and Process Tracking
An MES that provides BOM feature enables stakeholders, managers and floor operators to keep track of materials and processes, simultaneously. From material procurement to each phase in processing real-time data and performance metrics are available for quick access that calls for customizing workflows if required.
Upon the completion of a brief read on MES and BOM, it’s natural to want to explore MES software solutions that specifically aim to provide a holistic solution in the pursuit of achieving of achieving industry 4.0.
SFactrix, an MES Software with BOM Management
SFactrix is an MES software that digitizes manufacturing operations for agile operational execution, higher quality production and maximum ROI. SFactrix is an AI based manufacturing execution system specifically engineered for small and medium businesses (SMEs). From Planning and execution to monitoring and ensuring progress, SFactrix enables Smart manufacturing.
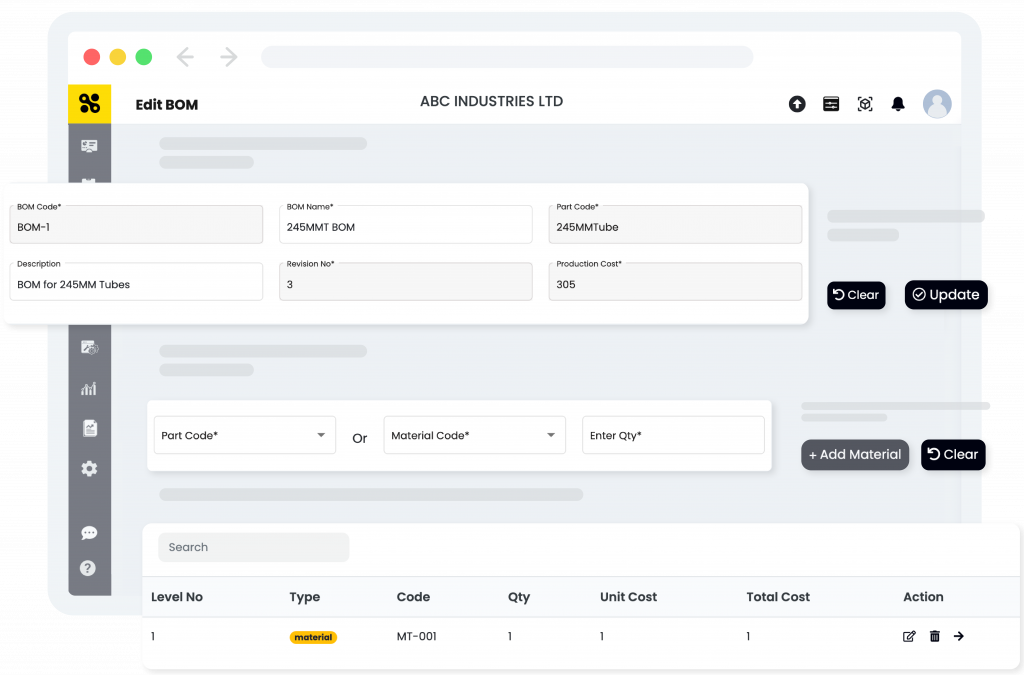
SFactrix is recognized as a holistic solution that facilitates automation and smart operations execution from shop-floor to top-floor. The features of SFactrix does not limit to offering an integration with BOM, learn more of the solution’s capabilities.
Specifically, SFactrix helps organize parts, materials and BOM for production planning. This feature in SFactrix focuses on facilitating cost optimization and tracking of revision counts performed on each BOM.
i) Create and manage parts availability, stock and production planning
ii) Define raw materials, availability and stock updates in just a few clicks
iii) Define simple and complex Bill of Materials (BOM) and processes as templates for rapid job allocations.
Conclusion
In conclusion, the Bill of Materials is a vast subject with plenty of facets, many of which have been attempted to be captured in this article. Nonetheless, the Bill of Materials is crucial in the development of a product, its execution, and commercialization. BOM helps manufacturers stay rooted in the vision, mission and objectives of product manufacturing from procurement to commercialization and logistics. Manufacturers can vouch for Bill of Material in the effective management and optimization of operations and costing in the process of manufacturing.
FAQs
1. What is a Bill of Materials (BOM) in manufacturing, and why is it important?
A Bill of Materials (BOM) is a detailed list of all the raw materials, components, sub-assemblies, and instructions needed to manufacture a product. It acts like a recipe, helping manufacturers plan, source, and assemble products accurately. A well-structured BOM helps in improving production efficiency, ensures quality, and reduces costly errors.
2. How does a Bill of Materials help in optimizing production costs and inventory management?
BOM provides precise quantities and specifications for each part, helping teams avoid overstocking or shortages. This control leads to accurate cost calculations, better budgeting, and optimized inventory levels, all of which reduce wastage and improve profitability.
3. What are the different types of BOM used in manufacturing industries?
Manufacturing uses various BOM types, including Engineering BOM (EBOM), Manufacturing BOM (MBOM), Assembly BOM, Configurable BOM, Sales BOM, and Service BOM. Each serves a unique purpose in different stages—from design to production and servicing.
4. What is the difference between Engineering BOM (EBOM) and Manufacturing BOM (MBOM)?
An Engineering BOM is created by the design team and outlines product structure from a design perspective. In contrast, a Manufacturing BOM focuses on how the product is actually built, including all components, raw materials, and processes required on the production floor.
5. Why should manufacturers use a digital BOM system instead of spreadsheets?
Spreadsheets are prone to errors and version conflicts. A digital BOM system offers centralized data, real-time updates, revision tracking, integration with MES/ERP, and better collaboration—essential for scaling and modernizing operations.