In the dynamic landscape of advanced manufacturing, businesses constantly seek innovative strategies to optimize their operations. Collaborative Planning, Forecasting, and Replenishment (CPFR) is groundbreaking. This blog aims to offer an in-depth exploration of CPFR and its transformative impact on manufacturing processes.
What is CPFR and How Does it Work?
Collaborative Planning, Forecasting, and Replenishment (CPFR) is a supply chain management strategy that integrates the efforts of suppliers and manufacturers to enhance efficiency, reduce costs, and improve overall performance. CPFR involves a collaborative and synchronized approach to planning and forecasting, fostering a seamless flow of information between trading partners.
Benefits of CPFR in Manufacturing:
Enhanced Visibility:
- CPFR provides real-time visibility into demand forecasts, inventory levels, and cycle times, allowing manufacturers to make informed decisions and adapt to market changes.
Improved Forecast Accuracy:
- By leveraging shared information and insights, CPFR helps refine demand forecasts, reduces the risk of overstocking or stockouts, and optimizes production schedules.
Cost Reduction:
- The collaborative nature of CPFR enables better resource utilization, minimizes excess inventory, and lowers carrying costs. This contributes to a more streamlined and cost-effective manufacturing process.
Efficient Order Fulfillment:
- With synchronized planning, manufacturers can align production with actual demand, improving order fulfillment rates and customer satisfaction.
The Role of Collaboration in CPFR
Collaborative Planning, Forecasting, and Replenishment (CPFR) are not merely buzzwords; they encapsulate a transformative approach to supply chain management that hinges on the power of collaboration. In this section, we delve into the pivotal role of collaboration in the success of CPFR strategies.
Understanding the Essence of Collaboration in CPFR
At its core, CPFR is founded on the principle of fostering collaboration among all stakeholders in the supply chain. Unlike traditional supply chain models, It emphasizes a shared responsibility for planning and forecasting, creating a symbiotic relationship between manufacturers and their partners. This collaborative approach breaks down silos and establishes a seamless flow of information.
1. Shared Information Leads to Informed Decision-Making:
The heart of collaboration in CPFR lies in the open exchange of information. Manufacturers and their partners comprehensively understand the supply chain by sharing real-time data on sales forecasts, inventory levels, and production schedules. This shared visibility allows for more informed decision-making at every stage, from production planning to order fulfillment.
2. Building Trust and Partnership:
Collaboration in CPFR is about sharing data, building trust, and forging solid partnerships. When all stakeholders collaborate effectively, a sense of shared responsibility and accountability emerges. This trust is the bedrock upon which successful strategies are built, as partners work together towards common goals, such as reducing costs, improving efficiency, and enhancing customer satisfaction.
Breaking Down Silos for Seamless Integration
Traditional supply chain models often suffer from siloed information and disconnected processes. CPFR, in contrast, breaks down these silos, encouraging cross-functional collaboration. This cross-functional approach involves teams from various departments – from marketing or sales to production and logistics – working together to align their efforts and contribute to a unified strategy.
1. Cross-Functional Teams:
Cross-functional teams play a pivotal role in breaking down departmental barriers. These teams bring together individuals with diverse skill sets and perspectives to collaborate on forecasting, planning, and replenishment activities. This integration of expertise ensures a holistic and well-rounded approach to supply chain management.
2. Alignment of Goals:
Collaboration in CPFR aligns the goals of different departments and partners. Whether achieving better forecast accuracy, optimizing inventory levels, or streamlining production schedules, the collaborative effort ensures everyone is dedicated to working towards common goals. This alignment is crucial for the success, as it prevents conflicting priorities and promotes a unified focus on overall supply chain optimization.
Evolution from Transactional to Collaborative Relationships
In traditional supply chain models, relationships between manufacturers and suppliers are often transactional – focused on orders, deliveries, and payments. Collaborative Planning, Forecasting, & Replenishment, however represents a shift towards more collaborative and strategic relationships.
1. Strategic Partnerships:
It encourages the development of strategic partnerships rather than purely transactional relationships. Manufacturers and suppliers become strategic allies, working together to navigate market uncertainties, adapt to changing demand patterns, and respond swiftly to challenges. This evolution from transactional to collaborative relationships creates a more agile and resilient supply chain.
2. Continuous Improvement:
Collaboration in CPFR fosters a culture of continuous improvement. As partners collaborate on production planning and forecasting, they can collectively analyze performance metrics and identify areas for enhancement. This collaborative approach to problem-solving ensures that the supply chain is not static but adapts and improves over time.
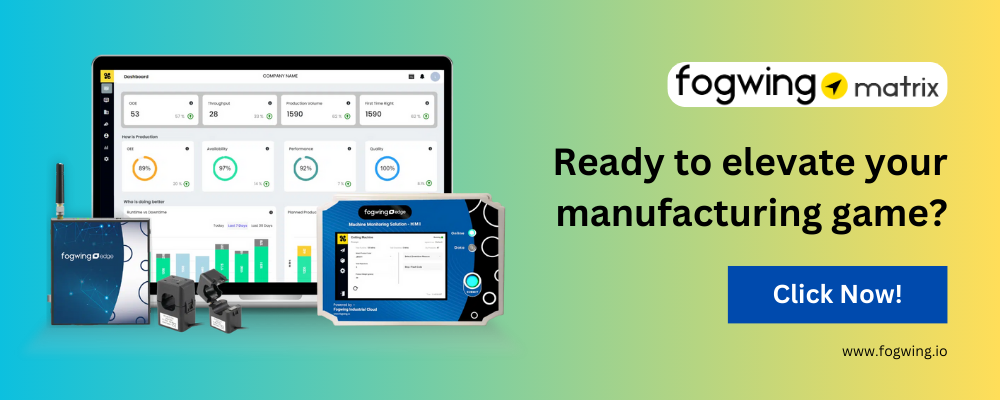
Overcoming Challenges Through Collaboration
While collaboration is a cornerstone of CPFR, its successful implementation comes with challenges. Resistance to change, varying technological capabilities, and data security concerns are among the hurdles that organizations may face. However, collaboration itself becomes a powerful tool in overcoming these challenges.
1. Change Management:
The collaborative nature of CPFR can catalyze change within an organization. By involving key stakeholders in decision-making and communicating the benefits of Collaborative Planning, Forecasting, and Replenishment, companies can overcome resistance to change and create a more collaborative and adaptive organizational culture.
2. Technology Adoption:
Collaboration requires the effective use of technology. While this may pose challenges for partners with varying technological capabilities, collaboration can be a solution. More technologically advanced partners can help others adapt to the collaborative platforms and tools by providing training and support, ensuring a smoother transition to CPFR.
Key Components of a Successful CPFR Strategy
Collaborative Planning, Forecasting, and Replenishment
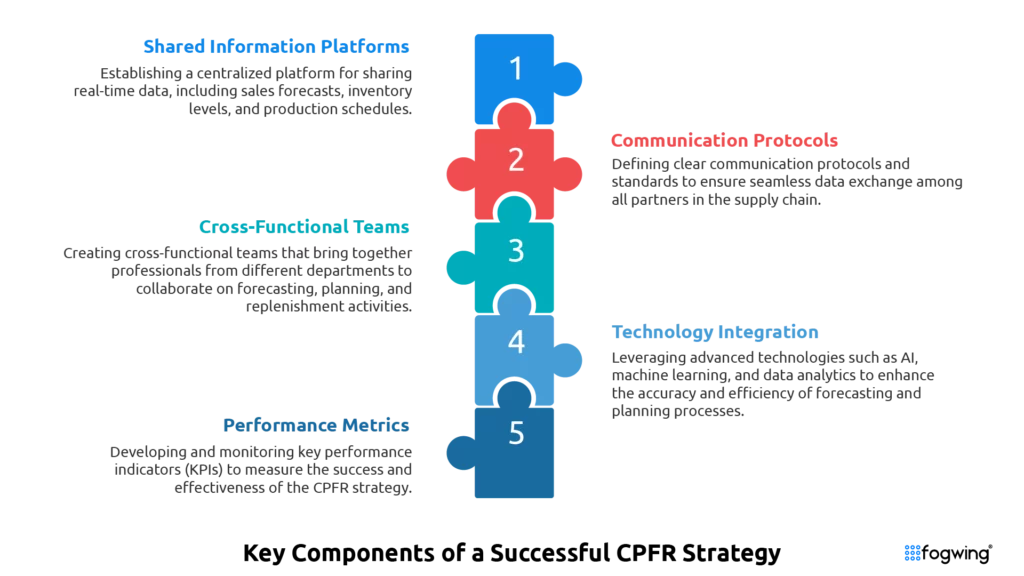
Implementing it requires careful planning and a structured approach. The following components are crucial for a successful strategy:
1. Shared Information Platforms:
- Establishing a centralized platform for sharing real-time data, including sales forecasts, inventory levels, and production schedules.
2. Communication Protocols:
- Defining clear communication protocols and standards to ensure seamless data exchange among all partners in the supply chain.
3. Cross-Functional Teams:
- Creating cross-functional teams that bring together professionals from different departments to collaborate on forecasting, planning, and replenishment activities.
4. Technology Integration:
- Leveraging advanced technologies like AI, and ML, and data analytics to enhance the accuracy and efficiency of forecasting and planning processes.
5. Performance Metrics:
- Developing and monitoring KPIs (key performance indicators) to measure the success and effectiveness of the CPFR strategy.
To know more about manufacturing KPIs, read this Key Manufacturing KPIs To Be Monitored |Fogwing.io
Challenges and Solutions for Implementing CPFR
While the benefits of CPFR are substantial, implementing this collaborative approach may encounter challenges such as resistance to change, data security concerns, and varying levels of technological maturity among partners. Addressing these challenges needs a strategic and proactive approach.
- Implementing it often involves a significant shift in organizational culture. To effectively address resistance to change, it is essential to communicate the benefits of Collaborative Planning, Forecasting, and Replenishment clearly and involve key stakeholders in the process.
- Establishing robust cybersecurity measures to protect sensitive information exchanged during collaboration. Implementing secure data-sharing protocols and encryption technologies can help mitigate security risks.
- Providing training and support to partners with varying technological capabilities, ensuring that all stakeholders can use collaborative platforms and tools effectively.
- Ensuring practices align with legal and regulatory requirements in different regions and industries.
Future Trends in Collaborative Planning for Manufacturing
The landscape of collaborative planning in manufacturing is constantly evolving, marked by ongoing trends and innovations shaping the future of CPFR.
1. Predictive Analytics:
- Integrating predictive analytics to anticipate future demand patterns and proactively adjust production plans.
2. Internet of Things (IoT):
- Utilizing IoT devices to collect real-time data from production processes, enabling more accurate forecasting and decision-making.
3. Digital Twins:
- Implementing digital twins to create virtual replicas of the supply chain, allowing for simulation and optimization of processes.
How Fogwing Matrix works as CPFR?
Fogwing Matrix is an IoT-enabled production monitoring solution that monitors and analyzes the production processes in a manufacturing environment. It collects real-time data from various sources on the shop floor, such as machines, sensors, and workers. The Fogwing Matrix is crucial in supporting CPFR initiatives by providing real-time production data that can be shared among trading partners. Integrated with CPFR, it can enhance the effectiveness of supply chain planning and execution by providing real-time insights and fostering better collaboration among partners. Let us know a few features of the Fogwing Matrix and its strategies for Collaborative Planning, Forecasting, and Replenishment.
- Fogwing Matrix provides historical production data and trends into the forecasting module of CPFR to improve the accuracy of demand forecasts.
- Fogwing Matrix enables real-time sharing of production data with other supply chain partners. This includes current production rates, inventory levels, and order fulfillment status data.
- It facilitates collaboration between production teams and other stakeholders.
- It provides production forecasts, cycle times, and other relevant information from the Production process.
- Fogwing Matrix offers a performance metrics dashboard that comprehensively views key performance indicators (KPIs) related to production efficiency, on-time delivery, and overall supply chain performance.
- Continuous improvement within the software, allowing users to analyze historical data, identify areas for optimization, make data-driven insights to enhance the overall performance of the supply chain through informed decision-making.
Integrating the CPFR features into the Fogwing Matrix fosters a collaborative and responsive supply chain where partners can work together efficiently to meet market demands and optimize production processes. It helps in creating a more adaptive and resilient supply chain ecosystem.
To learn more about production monitoring and forecasting, read this blog 5 Why Analysis For Production Monitoring | Fogwing.io
Conclusion
To conclude, Collaborative Planning, Forecasting, and Replenishment (CPFR) represents a paradigm shift in manufacturing processes, fostering unprecedented levels of collaboration and efficiency. With the advancement of technology and supply chains becoming more interconnected, the adoption of CPFR is poised to become a crucial competitive advantage for manufacturers.
By understanding the benefits, key components, challenges, and future trends in CPFR, businesses can strategically position themselves to thrive in the ever-changing landscape of modern manufacturing. Embracing the collaborative spirit of CPFR enhances operational efficiency. It lays the foundation for a more resilient and adaptive supply chain ecosystem.
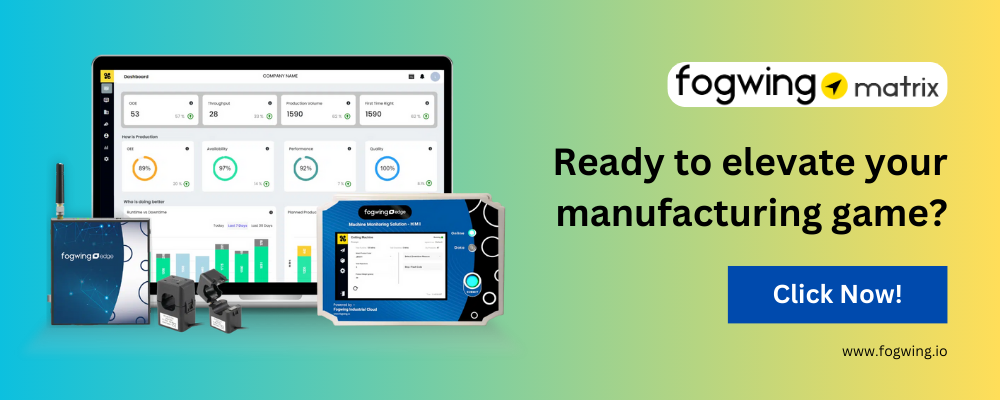