In the world moving towards the regime of Industry 4.0, smart manufacturing, advanced production, and quality assurance, one procedure that stands out is Destructive Testing. It is an unconventional asset testing approach followed by manufacturers to ensure the quality, safety, and reliability of materials used in diverse industries.
Dive into the blog and discover types of destructive Testing and its hidden insights, uncovering the science behind the realm of material Testing. Whether you are a seasoned professional or a curious enthusiast, we aim to deliver valuable information and foster a deeper understanding of destructive testing methods.
What is Destructive Testing?
Destructive Testing is a category of testing methods designed to evaluate the performance limit, mechanical properties, and structural integrity of materials or components by subjecting them to extreme conditions that cause permanent damage or failure, unlike non-destructive testing methods, which enable the manufacturers to evaluate or inspect materials without causing any damage or harm to the materials.
Destructive testing methods involve intentionally harming or causing damage to assess how materials or components perform under stress, load, or environmental factors. Standard methods include tension tests, impact tests, and hardness tests. These testing methods provide crucial data for quality control and research and ensure the reliability of materials and structures in various industries.
Critical Characteristics of Destructive Testing
Destructive testing methods have several critical features essential for understanding the nature and purpose of the testing approach. Here are a few characteristics of destructive testing examples:
Irreversible damage:
“Destructive testing refers to subjecting a particular specimen to extreme conditions, like stress, temperature, pressure, or impact, which may cause permanent and irreparable damage to the specimen.”
Non-destructive Testing achieves goals without compromising material integrity, distinguishing it from destructive Testing. The intentional damage allows for thoroughly examining the material’s response under challenging circumstances.
Material Behaviour Analysis:
The primary objective is to induce failure in the material or component to evaluate its performance under stress, load, or other extreme conditions. By intentionally including failure, destructive Testing provides detailed insight into the material’s mechanical, thermal, or chemical properties.
The analysis includes parameters like strength, hardness, flexibility, toughness, and fatigue resistance, contributing to a comprehensive understanding of material conduct.
Validation of Design and Manufacturing Process:
Destructive Testing is integral to design and manufacturing process validation. It serves as a crucial tool in ensuring product reliability and safety. The manufacturers employ this method to assess material properties, structural integrity, and performance under extreme conditions.
By intentionally inducing failure, destructive tests validate if materials meet design specifications and manufacturing processes consistently produce components with the anticipated properties. It provides insights into failure modes, prototype feasibility, compliance with standards, and overall product performance.
It enables engineers to optimize design, reduce risks, ensure that final products meet diverse industries’ stringent safety and quality standards, and withstand the expected conditions during their intended use.
Quality Assurance:
Manufacturers in different industries use destructive Testing as quality assurance. It’s used mainly in the sectors where safety and reliability are paramount. Quality assurance ensures that a product meets specified requirements and standards.
It involves a series of planned activities, reviews, and checks throughout the development or manufacturing lifecycle to prevent defects, enhance efficiency, and meet the customer requirements. With destructive testing methods, manufacturers can identify potential weaknesses, defects, or inconsistencies in materials or products before they reach the market as the end products.
Product Development and Improvement:
Destructive Testing is used in multiple industries to develop and improve products. Product testing and improvement is a continuous process of creating and enhancing products to meet growing market demands and surpass customer expectations.
It involves a systematic approach to innovation, design, and implementation, considering factors like performance, functionality, and user experience. The insights gained with the help of destructive testing software contribute to material quality improvements and structural configurations, leading to enhanced product performance.
Root Cause Analysis (RCA):
Root cause analysis is a fundamental aspect of destructive testing, and it serves as a critical characteristic in understanding and mitigating potential defects. By systematically investigating and identifying the primary cause of asset failures through destructive Testing, RCA enables manufacturers to address underlying asset-related issues, designs, or manufacturing processes.
It allows engineers to identify the factors leading to failures and implement corrective measures. The destructive testing software enables engineers to improve and foster a culture of quality and resilience in product development and manufacturing processes.
Types of Destructive Testing
Destructive Testing encompasses various methodologies to understand materials’ mechanical properties, structural integrity, and performance limits. These tests involve subjecting specimens to extreme conditions, leading to irreversible damage. Here are some common types of destructive Testing:
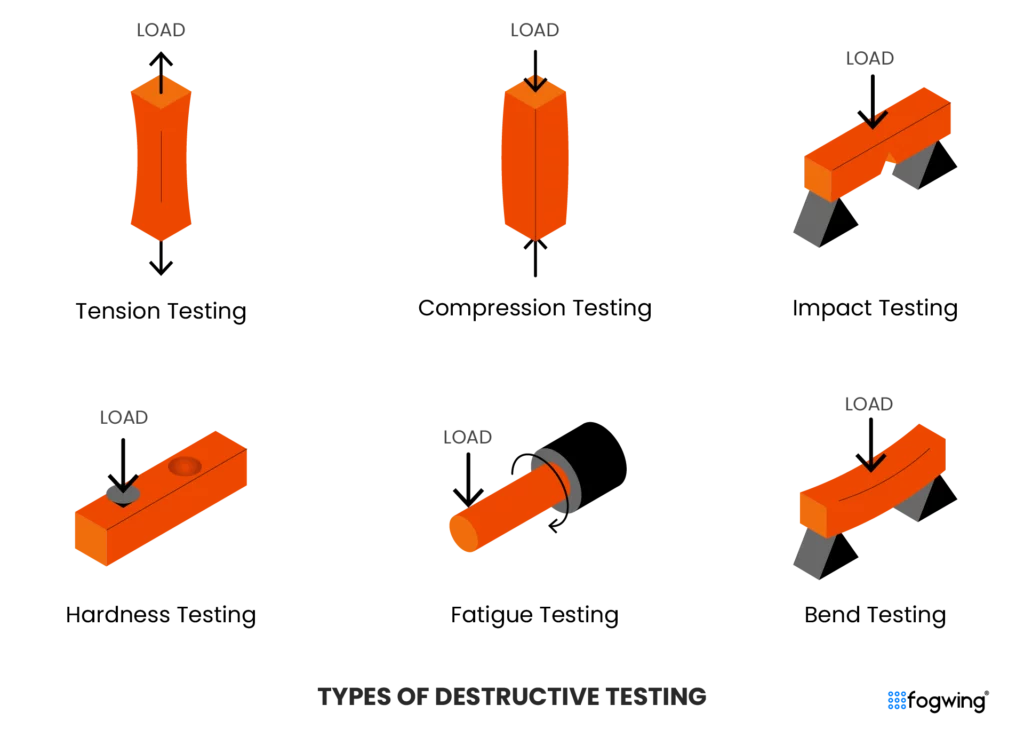
Tension Testing:
Tension testing, also known as tensile Testing, is a mechanical test generally utilized to estimate the mechanical properties of materials. The primary objective of tension testing is to determine how a material responds to tensile (pulling) forces.
During the test, a specimen is subjected to a gradually increasing tensile load until it fractures. The data obtained from the destructive testing methods is crucial for assessing the material’s strength, flexibility, and overall suitability for specific applications, aiding the manufacturers in material selection and quality control in manufacturing, construction, and materials science industries.
Compression Testing:
Compression testing is a destructive testing method that enables manufacturers to assess the conduct of materials under compressive force. In this destructive testing example, the specimen is subjected to an axial load, triggering it to undergo compression until deformation or failure happens.
Compression testing aims to determine properties such as compressive strength, modulus of elasticity, and deformation characteristics. These types of destructive testing are essential in industries such as construction, material science, manufacturing, and many more.
It provides insights into a material’s ability to withstand forces when subjected to compression, ensuring its suitability for specific applications and compliance with quality standards.
Impact Testing:
Impact Testing in destructive Testing is a material testing process that evaluates a material’s ability to absorb energy under sudden loading conditions. This destructive testing example subjects the specimen to a high-velocity impact to assess its toughness, conduct, and strength under dynamic loads.
This test lets manufacturers determine how a material withstands sudden shocks or impacts. Impact testing is crucial in construction and automotive industries where materials may experience sudden and forceful impact. Impact testing offers an understanding of material performance, fracture toughness, and resistance to brittle failure, aiding in designing materials that can withstand real-world scenarios.
Hardness Testing:
Hardness testing is a critical approach for evaluating the resistance of a material to deformation, indentation, or penetration. It measures the material’s ability to withstand localized stress or permanent deformation. Standard techniques for hardness testing include Rockwell, Brinell, and Vickers tests, each employing different methods and indenters.
This destructive Testing is essential across various industries, helping engineers select materials suitable for specific applications, ensuring durability, and predicting wear resistance. Hardness testing provides valuable insights into material strength, improving quality control and developing robust materials for diverse engineering purposes.
Fatigue Testing:
Fatigue testing in destructive Testing is a crucial evaluation method that assesses how materials endure repeated loading and unloading cycles over time. It is a process that stimulates real-world conditions, measuring a material’s resistance to fatigue-included failure.
These destructive testing methods are particularly crucial in aerospace, automotive, and structural engineering industries, where components are subjected to cyclical stresses. Fatigue testing enables engineers to understand how materials behave under varying loads, preventing catastrophic failure and enhancing the durability of structures and components.
These destructive testing examples ensure that materials used in critical applications can withstand the rigors of continuous stress, contributing to improved product reliability and safety.
Bend Testing:
Bend testing is a mechanical evaluation method used in destructive Testing to assess the flexibility and soundness of materials, particularly metals. It involves subjecting a specimen to a controlled deformation by bending it around a specific radius.
The test helps determine the material’s ability to withstand bending without fracturing. “Destructive testing methods are commonly employed in quality control and material certification procedures.” Bend testing ensures that materials used in construction, manufacturing, and infrastructure projects possess the required flexibility and structural integrity.
Each type of destructive Testing uniquely provides valuable insights into the properties and performance of materials, aiding in the design, manufacturing, and quality assurance processes across various industries. The choice of the test depends on the material, its intended use, and the desired information about its performance characteristics.
The Benefits of Destructive Testing
Despite their characteristics of causing irreversible damage to test specimens, destructive testing methods offer various benefits across various sectors, enhancing product quality and safety and facilitating the research and development processes. Here are some key benefits of destructive Testing:
1. Insightful Data:
Destructive testing examples provide in-depth insights into the mechanical properties of materials, including strength, flexibility, hardness, and toughness. This comprehensive data aids in understanding how materials behave under different conditions and loads.
2. Identification of Weaknesses:
By subjecting materials to extreme conditions, destructive testing methods help identify weaknesses, defects, or flaws. It is crucial for quality assurance processes, allowing manufacturers to detect and rectify potential issues before products reach the market.
3. Optimizing Designs:
Destructive Testing is instrumental in developing and improving products. It enables engineers and designers to optimize designs by refining material choices and structural configurations based on the performance data obtained from Testing.
4. Ensuring Reliability:
Industries such as aerospace, automotive, and construction rely on types of destructive Testing to ensure the reliability and safety of crucial components. This Testing helps validate that materials can withstand anticipated stresses and forces without catastrophic failure.
5. Meeting Industry Standards:
Destructive testing methods are often necessary to meet industry standards and regulatory compliance, especially in sectors where safety is critical, such as in the manufacturing of pressure vessels, pipelines, and structural components.
6. Understanding Failures:
When failures occur in real-world applications, destructive Testing allows for a thorough examination of the failed components. It helps manufacturers determine the root causes of failures, contributing to improved design practices and materials selection.
7. Ensuring Accuracy:
Destructive testing methods are used to calibrate and validate non-destructive testing methods. By comparing the results of destructive tests with NDT techniques like ultrasonic Testing or radiography, industries can enhance the accuracy of inspections without causing harm to the entire structure.
8. Research and Innovation:
Destructive Testing is vital for material science and engineering researchers. It enables the exploration of new materials and advancing innovative technologies by thoroughly understanding material behaviors and limitations.
9. Performance Prediction:
Destructive testing methods, especially fatigue and creep testing, assist in predicting the long-term behavior of materials under continuous stress or elevated temperatures. This information is critical for applications where components undergo prolonged operational conditions.
10. Validation of Computer Simulations:
The results obtained from destructive Testing are often used to validate computer simulations and finite element analyses. This iterative process enhances the accuracy of virtual models, ensuring that they align closely with real-world material behavior.
The Difference between Destructive Testing and Non-destructive Testing
Destructive testing and non-destructive testing methods are two distinct methodologies employed across various industries to assess materials’ and structures’ quality, integrity, and reliability. Each method serves specific requirements and is chosen based on the nature of the materials involved and the desired outcome of the testing process.
Objective and Purpose:
Destructive Testing involves subjecting forces, conditions, or environments that cause permanent changes or damage to the material. The primary goal is to understand the material’s characteristics under extreme conditions and to identify its ultimate limits and failure points.
Non-destructive Testing aims to inspect and evaluate materials without causing any permanent alteration. This method allows for examining structures, components, and materials while preserving their integrity. It is precious in industries where the cost of replacing or repairing damaged items is high.
Techniques Used:
Destructive Testing techniques include tension levels, impact tests, compression tests, and fatigue tests. These destructive testing methods provide insight into the material’s strength, flexibility, and mechanical properties. Still, the tested specimen becomes unusable after the assessment.
Non-Destructive Testing employs numerous testing techniques such as radiography, ultrasonic Testing, radiography, magnetic particle testing, liquid penetrant testing, visual testing, and eddy current testing. These testing methods enable the detection of flaws, discontinuities, or structural weaknesses without causing any harm to the tested specimen.
Application:
Destructive Testing is utilized in the early stages of product development, during quality control processes, or when specific data about a material’s breakpoint is required. It is common in sectors such as metallurgy, construction, and aerospace.
Non-destructive Testing is widely applied in industries where the preservation of materials is crucial, such as aerospace, automobile, and oil and gas. It is ideal for routine inspections, quality assurance, and ensuring the ongoing reliability of critical components.
Conclusion:
In the dynamic landscape of Industry 4.0, Destructive Testing emerges as a crucial procedure for ensuring materials’ quality, safety, and reliability. By intentionally causing irreversible damage under extreme conditions, this method provides invaluable insights into material behaviors.
From tension and compression testing to impact and hardness testing, each approach optimizes designs, ensures reliability, and meets industry standards. Despite its destructive nature, the benefits extend across industries, influencing product development, innovation, and safety.
Destructive Testing methods are a cornerstone in material science, contributing to advancements and shaping the future of engineering practices. Destructive testing software is a powerful and necessary tool in engineering and manufacturing. Destructive testing methods ensure the safety and reliability of products while driving innovation forward.
By embracing the insights gained from intentional destruction, industries persist in pushing the boundaries of what is achievable and creating a future where products are not only cutting-edge but also built to withstand the tests of time.
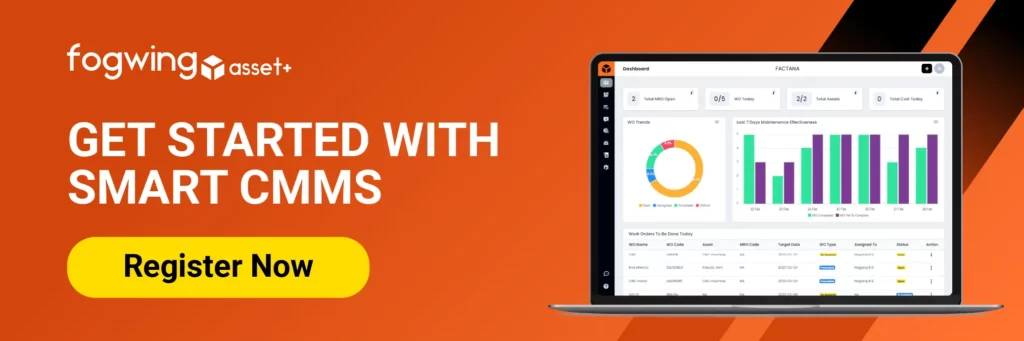