Welcome to our blog post about the dynamic duo of production planning and quality assurance! If you’ve ever wondered how successful companies consistently achieve flawless products, this article is for you. We’re diving into the synergy between planned production and quality assurance – a powerful combination that ensures efficiency and guarantees supreme product excellence. Get ready to uncover the secrets behind seamless operations, impeccable standards, and customer satisfaction like never before. So, buckle up as we embark on a journey exploring how these two essential elements work hand in hand to create an unstoppable force in manufacturing.
What is Planned Production?
It is a systematic approach to manufacturing that involves forecasting market demand, creating sales plans, developing detailed production schedules, preparing for required materials, assessing production capacity, and executing the production process accordingly. The goal is to optimize efficiency, minimize costs, and meet customer demand consistently. This strategic framework helps businesses align production activities with overall goals and market dynamics, ensuring a streamlined and effective manufacturing process.
What are the six steps in production planning?
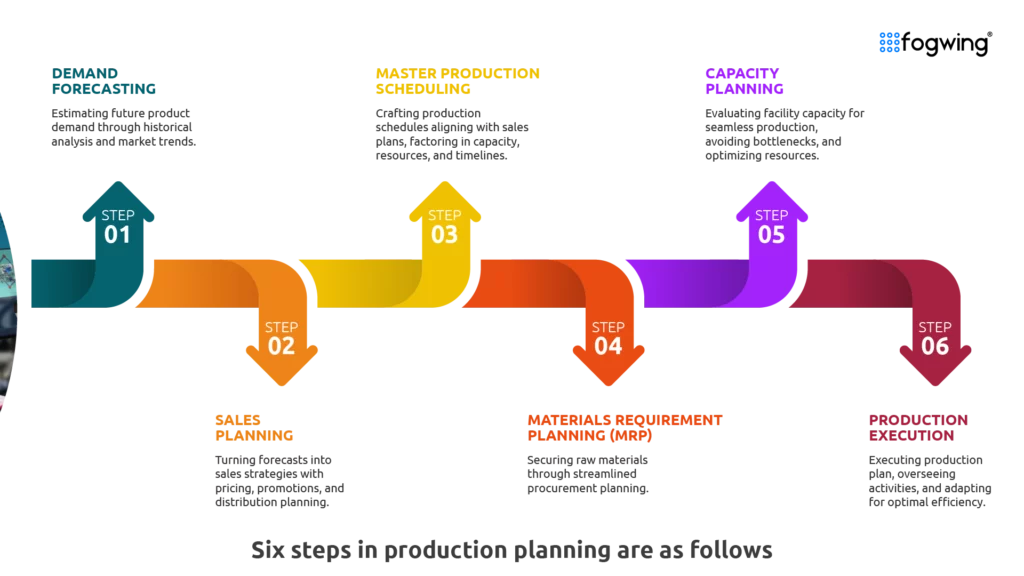
The six steps in production planning are as follows:
Demand Forecasting
Anticipating market demand is the initial step involving analyzing historical data, market trends, and other factors to estimate future demand for the product.
Sales Planning
Translating the demand forecast into tangible sales plans, considering factors such as pricing, promotions, and distribution channels.
Master Production Scheduling
Developing a detailed planned production schedule based on the sales plans, considering production capacity, resource availability, and timeline constraints.
Materials Requirement Planning (MRP)
Ensuring the availability of necessary raw materials and components by planning and managing the procurement process.
Capacity Planning
Assessing facilities’ production capacity to ensure alignment with the production schedule, avoiding bottlenecks, and optimizing resource utilization.
Production Execution
Implementing the planned production, coordinating activities on the production floor, monitoring progress, and adjusting as needed to maintain efficiency.
These steps form a cohesive framework that helps organizations optimize their production processes, minimize inefficiencies, and meet market demand effectively.
What is quality in production planning?
Quality, within the context of production planning, transcends mere compliance with specifications; it embodies a commitment to excellence. It involves a continuous commitment to adhering to stringent standards, consistency, and an unwavering pursuit of improvement throughout the production lifecycle.
To learn more about effective production planning/ scheduling, read this 7 Best Practices For Production Scheduling | Fogwing.io
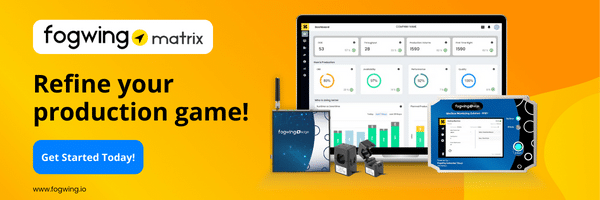
Benefits of Planned Production:
The benefits are numerous and help enhance manufacturing processes’ effectiveness. Here are some key advantages:
Efficiency Improvement: It minimizes downtime and optimizes the utilization of resources, leading to increased overall efficiency in the manufacturing process.
Cost Reduction: By streamlining processes and avoiding inefficiencies, planned-production helps minimize unnecessary expenses, reducing costs.
Consistent Product Quality: The systematic approach of planned production ensures that each step in the manufacturing process adheres to predetermined standards, resulting in consistent and high-quality products.
Resource Optimization: Efficient planning allows for the optimal use of resources, including workforce, materials, and equipment, preventing underutilization or overutilization.
Improved Customer Satisfaction: Meeting market demand consistently and delivering products of high quality enhances customer satisfaction, fostering loyalty and positive brand perception.
Better Inventory Management: Planned production helps maintain an optimal balance in inventory levels, preventing excess stock or shortages, thus reducing holding costs.
Adaptability to Market Changes: As planned production involves forecasting and strategic planning, businesses can better adapt to changes in market demand, allowing for proactive adjustments in production schedules.
Enhanced Production Visibility: Through the planning process, there is increased visibility into each production stage, enabling better tracking, monitoring, and control over the manufacturing process.
Improved Time Management: Detailed production schedules help manage time effectively, ensuring that tasks are completed within specified timelines, reducing delays, and improving overall productivity.
Strategic Business Alignment: Planned production aligns manufacturing activities with broader business goals, ensuring that production efforts contribute directly to the company’s strategic objectives.
Waste Reduction: By minimizing inefficiencies and optimizing resource utilization, planned production helps reduce waste in terms of materials and time.
Understanding the Synergy Between PPQA and Production Planning
PPQA (Process and Product Quality Assurance) and production planning are critical elements of any successful manufacturing operation. While they may seem like separate functions, a strong synergy between these two aspects can significantly enhance the overall efficiency and quality of a company’s production process.
In simple terms, PPQA ensures that all processes and products meet the desired quality standards set by the company. This includes monitoring the production process, identifying potential issues or bottlenecks, and implementing corrective measures to ensure consistent quality output. On the other hand, production-planning or planned-production refers to creating an organized framework for scheduling and managing all aspects of production, including inventory management, resource allocation, and delivery timelines.
At first glance, it may not be apparent how these two seemingly distinct functions work together. However, upon closer examination, it becomes clear that they have a symbiotic relationship crucial for achieving optimal results in manufacturing.
PPQA and production planning work together by identifying potential quality issues during the planning stage. By integrating quality control checks into the production planning process, companies can identify potential flaws or defects in their product design or manufacturing processes before they become expensive problems down the line. This proactive approach ensures higher quality standards and helps prevent delays in production and costly rework.
Moreover, effective communication between PPQA and production planning teams can help streamline processes further. For instance, if a product requires specific testing procedures during its production phase as part of the quality assurance process, production planners can adjust the production schedule to accommodate these tests without causing delays or disruptions.
Another essential aspect of this synergy is the continuous improvement cycle. Both PPQA and production-planning rely on data and analytics to identify areas for improvement. By sharing data and insights between both functions, businesses identify patterns and trends that help optimize production processes and improve overall product quality.
Furthermore, with an increased focus on sustainability and environmental responsibility in manufacturing, companies need to integrate eco-friendly practices into their production processes. PPQA teams can work closely with production planning to ensure sustainable practices are integrated into every production stage, from sourcing resources to packaging and delivery.
Technology’s Role in Enhancing Synergy:
As we hurtle into the future, the impact of technology on manufacturing cannot be overstated. It has revolutionized processes and catalyzed the synergy between planned production and quality assurance.
Automation: Integrating automated systems into the production line minimizes human errors, enhances efficiency, and ensures precision in execution.
Data Analytics: The power of big data analytics comes to the fore, providing manufacturers with invaluable insights into their production processes and facilitating continuous improvement and proactive issue resolution.
IoT Integration: The interconnectedness of devices through the Internet of Things (IoT) grants real-time visibility and control over the production line, optimizing responsiveness and adaptability.
Quality Management Software: Specialized software solutions dedicated to quality management streamline the quality assurance processes, ensuring adherence to standards and rapid issue resolution.
How Fogwing Matrix Help in Production Planning?
Fogwing Matrix is an IoT-based production monitoring software that enhances planned production and quality assurance in manufacturing processes. Here are ways in which it contributes to these aspects:
Production Planning:
- Real-Time Visibility: Fogwing Matrix provides real-time visibility into the entire production process.
- Data Collection: IoT sensors and devices collect real-time data on various aspects of the production process, such as machine performance, production rates, and resource utilization.
- Live Monitoring: Production managers can access live data dashboards, providing real-time visibility into the status of production lines, equipment, and resources.
- Preventive Maintenance:
- Condition Monitoring: IoT sensors on machinery collect data on equipment health and performance.
- Preventive Analytics: Fogwing Matrix can prevent potential equipment failures using this data, allowing for proactive maintenance scheduling to minimize downtime.
- OOE Monitoring:
- Fogwing Matrix provides OOE (Overall Operations Effectiveness) monitoring as a powerful manufacturing KPI. OOE assesses the effectiveness of operations throughout a shift, irrespective of whether the allocated time was intended for job execution. Monitoring OOE helps in identifying and rectifying issues affecting product quality.
- Planned-production schedules can be adjusted based on the insights gained from OOE monitoring to account for planned maintenance activities and reduce unplanned downtime.
Quality Assurance:
Real-Time Quality Monitoring:
Sensor Integration: IoT sensors on production lines continuously monitor product quality parameters.
Alerts and Notifications: Fogwing Matrix generates alerts if quality deviations are detected in real-time.
Product Traceability: IoT technology enables the tracking of products throughout the entire production process.
Root Cause Analysis: In the event of quality issues, the software can assist in identifying the root causes, enabling corrective actions.
Early Issue Detection: Identifying quality issues early in the planned-production process helps prevent defective products from reaching customers.
Quality assurance at every stage supports planned production by avoiding defects or unnecessary consumption of resources.
To know more about Fogwing Matrix, explore here Best Production Monitoring Solution | Fogwing Industrial Cloud
Conclusion:
The synergy between planned production and quality assurance is essential in any manufacturing process. These two elements work hand in hand to ensure that productions are happening efficiently, effectively, and with the highest level of quality.
Manufacturers can optimize their resources and minimize waste by implementing a well-planned production schedule. This leads to cost savings and allows for consistent delivery of high-quality products. With a clear plan, manufacturers can identify potential bottlenecks in the production process and take proactive measures to mitigate them.
At the same time, quality assurance plays a crucial role in ensuring that products meet or exceed customer expectations. With rigorous testing procedures and quality control measures, manufacturers can detect and rectify any issues before the final product reaches consumers. This helps maintain customer satisfaction and saves costs associated with recalls or product returns due to defects.
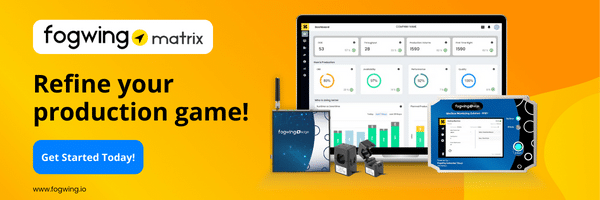