Reliability centered Maintenance (RCM) is a cornerstone of maintenance strategies. RCM aims to optimize asset performance while minimizing costs and risks. This comprehensive guide delved into the intricacies of RCM, exploring its principles, methodologies, and applications.
Whether you’re a seasoned maintenance professional or a newcomer to the field, this guide will equip you with the knowledge needed to implement RCM effectively.
What is Reliability Centered Maintenance (RCM)
Reliability Centered Maintenance (RCM) is a systematic approach to asset maintenance that aims to ensure the reliability and performance of assets while optimizing maintenance costs. In this section, we delve deeper into the key concepts and principles of RCM, providing a comprehensive understanding of its significance in modern maintenance practices.
1.1 Definition and Significance of RCM:
Reliability centered maintenance (RCM) is a methodology focused on identifying the most effective maintenance strategies for critical assets based on their function and operational context. Unlike traditional maintenance approaches, which rely on fixed schedules or reactive interventions, RCM emphasizes a proactive and data-driven approach to maintenance decision-making.
The significance of RCM lies in its ability to:
– Improve asset reliability: By focusing on critical components and failure prevention, RCM helps organizations enhance the reliability and performance of their assets.
– Minimize maintenance costs: Since the focus is on critical components and failure prevention, RCM enables the maintenance team to optimize maintenance activities, reducing unnecessary maintenance tasks and maximizing the efficiency of the maintenance team’s efforts.
– Enhance safety and operational integrity: By proactively addressing potential failure prevention and risk mitigation, RCM helps mitigate safety hazards and ensure the operational integrity of assets.
– Support regulatory compliance: RCM provides a structured framework for ensuring compliance with regulatory requirements and industry standards, particularly in safety-critical industries such as aviation, oil and gas, and healthcare.
1.2 History and Evolution of RCM:
The roots of Reliability Centered Maintenance can be traced back to the aviation industry in the 1960s when the need for a systematic approach to Maintenance became apparent due to the increasing complexity of aircraft systems and the high stakes in ensuring flight safety. The pioneering work of organizations such as United Airlines and the U.S. Department of Defense laid the foundation for RCM as we know it today.
Over the decades, RCM has evolved from its aviation origins to become a widely adopted methodology across various industries, including manufacturing, transportation, utilities, and facilities management. The development of international standards such as SAE JA1011 and SAE JA1012 has further standardized RCM practices and terminology, facilitating its implementation and dissemination.
What are the Core Principles of Reliability Centered Maintenance?
At the heart of Reliability Centered Maintenance, several core principles guide its application in the practical world:
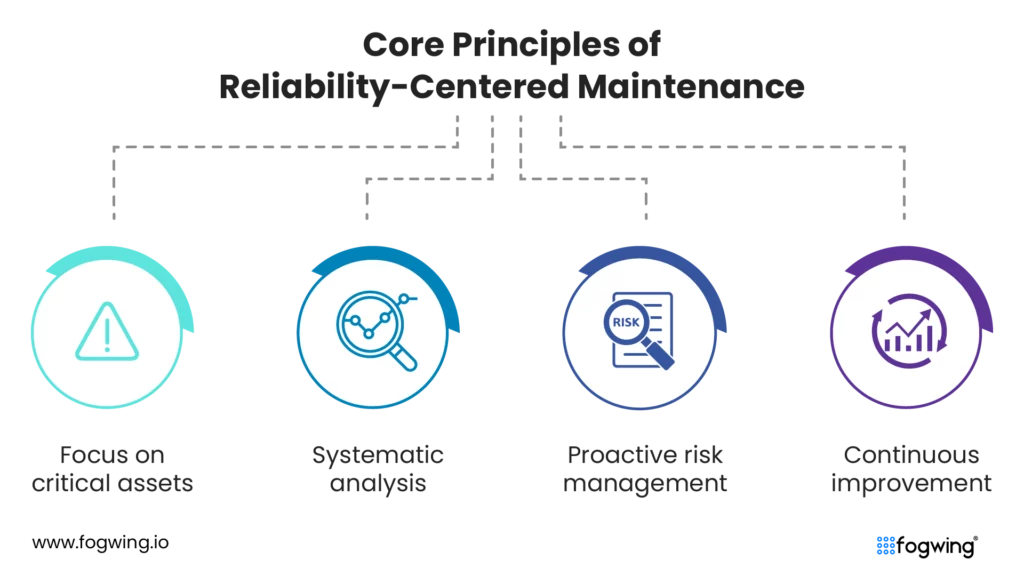
Principle 1: Focus on critical assets
RCM prioritizes maintenance efforts based on assets’ criticality and impact on organizational objectives. By identifying and prioritizing critical components, RCM ensures that resources are allocated effectively to mitigate the most significant risks.
Principle 2: Systematic analysis
RCM employs a structured and systematic approach to maintenance decision-making. It involves identifying functional failures, failure modes, and potential consequences. Through a series of analytical steps, RCM helps organizations develop tailored maintenance strategies that address specific risks and performance requirements.
Principle 3: Proactive risk management
RCM emphasizes proactive risk management, aiming to prevent failures before they occur rather than reacting to them afterward. By identifying and mitigating potential failure modes, RCM helps organizations minimize downtime, improve safety, and optimize asset performance.
Principle 4: Continuous improvement
Reliability centered maintenance (RCM) is not a one-time exercise but a continuous process of learning and optimization. Organizations that embrace RCM are committed to ongoing monitoring, evaluation, and refinement of their maintenance strategies to adapt to changing operating conditions, technological advancements, and business priorities.
Fundamentals of RCM Analysis
This section delves into the core methodology of Reliability Centered Maintenance (RCM) analysis, which forms the foundation of effective maintenance decision-making. We break down the seven steps of RCM analysis, providing detailed insights into each stage and highlighting the importance of systematic and data-driven approaches.
2.1 The Seven Steps of RCM Analysis:
Reliability Centered Maintenance analysis typically involves the following seven steps:
1. Identify Assets and Functions:
The first step in RCM analysis is identifying the assets or systems critical to organizational objectives. It includes understanding these assets’ functions and their role in supporting production processes. By defining the critical functions of assets, organizations can identify and prioritize maintenance efforts based on their criticality to overall performance.
2. Determine Functional Failures:
Once assets and their functions are identified, the next step is determining potential functional failures. A functional failure is any deviation from an asset’s intended performance that could result in undesirable consequences. These may include equipment breakdowns, performance degradation, safety hazards, or environmental impacts.
3. Identify Failure Modes:
Once functional failures are identified, the next step is to identify the specific failure modes or mechanisms that could lead to them. This involves analyzing the root causes of failures, including wear and tear, material degradation, operational stresses, and environmental conditions. By understanding failure modes, organizations can develop targeted maintenance strategies to mitigate risks.
4. Assess Failure Consequences:
Each failure mode is assessed based on potential consequences, including safety implications, operational disruptions, environmental impacts, and financial costs. This step involves evaluating the severity and likelihood of each consequence, considering factors such as asset criticality, regulatory requirements, and stakeholder priorities.
5. Prioritize Maintenance Tasks:
Based on the analysis of failure modes and consequences, maintenance tasks are prioritized according to their impact on organizational objectives. Tasks may be classified into different categories, such as preventive Maintenance, predictive Maintenance, condition-based Maintenance using IoT technologies, or run-to-failure strategies. Prioritization ensures that resources are allocated effectively to address critical risks and optimize asset performance.
6. Develop Maintenance Strategies:
Once maintenance tasks are prioritized, the next step is to develop appropriate maintenance strategies for each identified failure mode. This may involve a combination of preventive, predictive, and proactive maintenance approaches using IoT data tailored to each asset’s needs. Maintenance strategies should be cost-effective, practical, and aligned with organizational goals and constraints.
7. Implement and Review:
The final RCM analysis step is implementing the selected maintenance strategies and continuously reviewing their effectiveness. This includes monitoring asset performance, collecting data on maintenance activities, and analyzing the impact of interventions on asset reliability and operational efficiency. Regular reviews enable organizations to identify opportunities for improvement and refine their maintenance strategies over time.
2.2 Importance of Systematic Analysis in RCM:
The success of RCM analysis is due to its systematic and structured approach to maintenance decision-making. Organizations can ensure consistency, thoroughness, and accountability in their maintenance practices by following a defined methodology and sequence of steps listed above. Systematic analysis helps organizations identify hidden risks, prioritize resources effectively, and optimize maintenance strategies to achieve desired outcomes.
Implementing RCM Workflow
This section explores the practical aspects of integrating Reliability Centered Maintenance (RCM) into an organization’s workflow. We discuss the steps in implementing RCM workflow, including stakeholder engagement, data collection, analysis, and decision-making processes. Additionally, we highlight the role of technology in streamlining RCM workflows and maximizing the effectiveness of maintenance strategies.
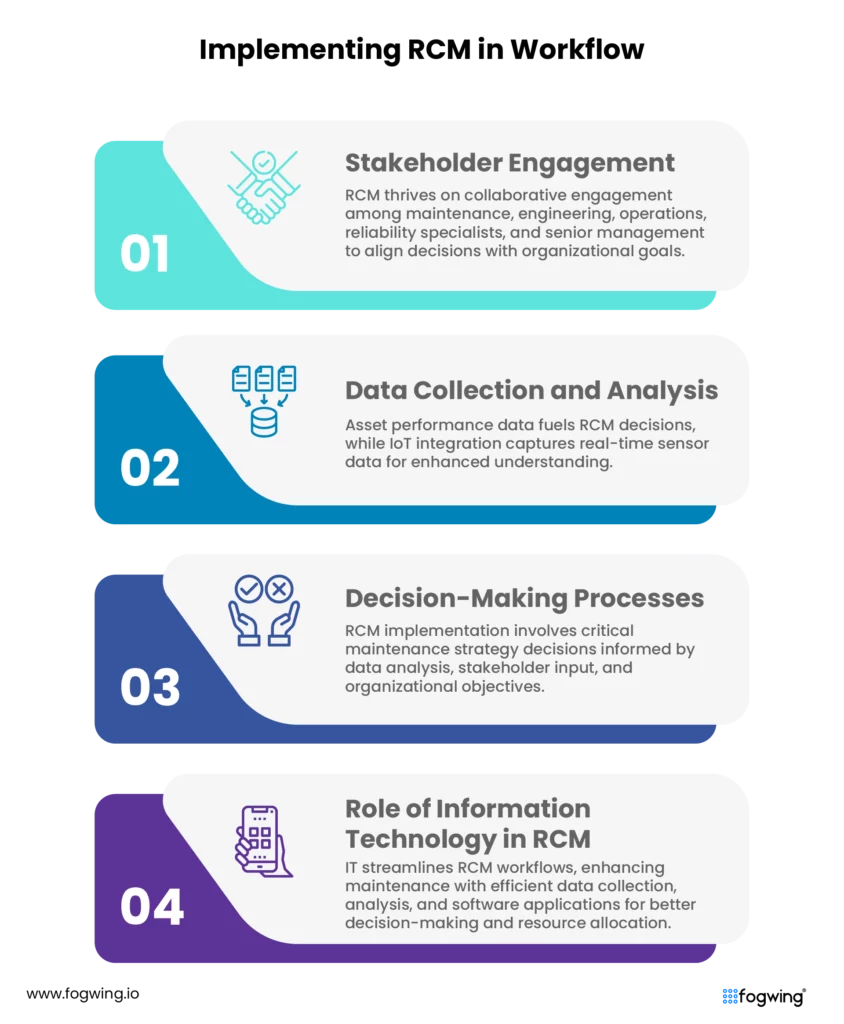
Stakeholder Engagement:
To successfully implement RCM (Reliability Centered Maintenance), various stakeholders within the organization must actively engage and collaborate. This includes maintenance teams, engineers, operations personnel, reliability specialists, and senior management. Stakeholder engagement ensures that diverse perspectives are considered and decisions are aligned with organizational goals and priorities.
Key aspects of stakeholder engagement in RCM implementation include:
– Establishing clear communication channels to facilitate collaboration and information sharing.
– Providing training and education to stakeholders to build awareness and understanding of RCM principles and methodologies.
– Encouraging active participation and feedback from stakeholders throughout the implementation process.
– Fostering a continuous improvement and accountability culture, where stakeholders are empowered to contribute to maintenance decision-making and process optimization.
Data Collection and Analysis:
Asset performance data is crucial in RCM implementation, providing the foundation for informed decision-making and maintenance planning. Effective data collection and analysis enable organizations to accurately identify asset performance trends, failure patterns, and Maintenance requirements. Internet of Things (IoT)- based machine integration helps capture sensor data from machines to understand various performance parameters in real-time.
Key steps in data collection and analysis for RCM implementation include:
- An IoT connection with machine sensors is required to capture data such as running time, speed, temperature, vibration, current usage, etc.
- Gathering historical maintenance records, downtime, and failure reports to identify recurring issues and failure modes.
- Implementing IoT-based condition monitoring and predictive maintenance activities to assess asset health and anticipate potential failures.
- Advanced analytics tools and techniques, such as reliability analysis, fault tree analysis, and failure mode effects analysis (FMEA), are utilized to identify critical failure modes and their root causes.
- It incorporates insights from data analysis into the RCM decision-making process, such as prioritizing maintenance tasks, selecting appropriate maintenance strategies, and optimizing maintenance intervals.
Decision-Making Processes:
RCM implementation involves making critical maintenance strategies, resource allocation, and risk management decisions. These decisions are informed by data analysis, stakeholder input, and organizational objectives.
Key aspects of decision-making processes in RCM implementation include:
- Evaluating the cost-benefit trade-offs of different maintenance strategies, considering asset criticality, maintenance costs, and operational impacts.
- Balancing preventive maintenance activities with predictive and condition-based Maintenance approaches to optimize asset performance and minimize downtime.
- Incorporating risk-based decision-making principles to prioritize maintenance tasks according to their potential impact on safety, reliability, and operational integrity.
- Documenting and documenting decisions, rationale, and implementation plans to ensure transparency, accountability, and traceability throughout the RCM process.
Role of Information Technology in RCM:
Information Technology plays a vital role in streamlining RCM workflows and enhancing the effectiveness of maintenance practices. Software applications enable organizations to collect, analyze, and leverage maintenance data more efficiently, improving decision-making and resource allocation, from asset management to predictive maintenance.
Key technologies and tools for RCM implementation include:
- Smart Computerized maintenance management systems ( Smart CMMS) help to manage work orders, schedule preventive maintenance activities, and track asset performance using IoT.
- Asset Condition monitoring uses sensors and predictive maintenance software to monitor asset health in real-time and detect potential failures early.
- Reliability software for conducting advanced analytics, risk assessments, and optimization of maintenance strategies.
- Internet of Things (IoT) devices and connectivity solutions for collecting data from remote assets and integrating with existing IT infrastructure.
How to Maximize Operational Efficiency with RCM?
We delve into the operational benefits of Reliability Centered Maintenance (RCM) and how organizations can leverage RCM principles to enhance operational efficiency. We will explore how RCM contributes to increased asset reliability, extended asset lifespan, reduced downtime, and optimization of maintenance practices.
Increased Asset Reliability:
One of RCM’s primary objectives is to improve asset reliability by proactively addressing potential failure modes and implementing targeted maintenance strategies. Organizations can minimize the likelihood of unexpected equipment failures and unplanned downtime by focusing resources on critical components and failure modes.
Key aspects of how RCM increases asset reliability include:
- Identifying critical failure modes: RCM analysis helps organizations identify the most critical failure modes with the greatest potential impact on asset performance and operational objectives.
- Developing targeted maintenance strategies: Based on analyzing failure modes and consequences, organizations can develop tailored maintenance strategies designed to mitigate the identified risks effectively.
- Implementing proactive maintenance activities: RCM emphasizes proactive maintenance approaches, such as preventive Maintenance, predictive Maintenance, and condition-based Maintenance, to address potential failure modes before they lead to operational disruptions.
- Monitoring asset performance: RCM involves ongoing monitoring of asset performance and maintenance activities to identify emerging issues, assess the effectiveness of maintenance strategies, and make data-driven decisions for continuous improvement.
Extended Asset Lifespan:
RCM extends the lifespan of critical assets by optimizing maintenance practices and minimizing premature failures. By implementing proactive maintenance strategies and addressing underlying root causes of failures, organizations can maximize the longevity of their assets and achieve a higher return on investment.
Key aspects of how RCM extends asset lifespan include:
- Preventing premature failures: RCM helps organizations identify and address potential failure modes before they lead to equipment breakdowns or performance degradation, thereby extending the lifespan of assets.
- Implementing condition-based maintenance: RCM encourages using IoT-based condition monitoring techniques and predictive maintenance tools to assess asset health in real-time and identify early signs of deterioration or wear, allowing for timely intervention and maintenance.
- Optimizing maintenance intervals: RCM enables organizations to optimize maintenance intervals based on asset conditions, performance trends, and operational requirements, ensuring that maintenance activities are performed at the right time to maximize asset reliability and lifespan.
- Incorporating reliability engineering principles: RCM incorporates reliability engineering principles into maintenance practices, such as reliability-centered design, failure mode effects analysis (FMEA), and root cause analysis (RCA), to address underlying reliability issues and design robust, resilient systems.
Reduced Downtime:
Minimizing downtime is a key goal of RCM, as unplanned equipment failures and maintenance activities can significantly impact operational productivity, profitability, and customer satisfaction. Organizations can reduce downtime and improve overall operational efficiency by implementing proactive maintenance strategies and optimizing maintenance schedules.
Key aspects of how RCM reduces downtime include:
- Implementing preventive Maintenance: RCM emphasizes preventive maintenance activities, such as routine inspections, lubrication, and component replacements, to prevent equipment failures and minimize unplanned downtime.
- Predictive Maintenance and condition monitoring: RCM encourages using predictive maintenance techniques and condition monitoring technologies to anticipate potential failures and schedule maintenance activities proactively, thereby minimizing downtime and maximizing asset availability.
- Optimizing maintenance schedules: RCM enables organizations to optimize maintenance schedules based on asset criticality, operational requirements, and resource constraints. This ensures that maintenance activities are performed at the most opportune times to minimize disruption to operations.
- Rapid response to failures: Equipment failures may still occur despite proactive measures. RCM emphasizes the importance of contingency plans and rapid response protocols to minimize downtime and expedite recovery in unexpected failures.
Overall Optimization of Maintenance Practices:
By integrating RCM principles into maintenance practices, organizations can optimize their maintenance processes, resources, and outcomes overall. RCM enables organizations to prioritize maintenance tasks, allocate resources efficiently, and continuously improve maintenance strategies based on data-driven insights and performance feedback.
Key aspects of the overall optimization of maintenance practices with RCM include:
- Prioritizing maintenance tasks: RCM helps organizations prioritize maintenance tasks based on asset criticality, failure risks, and operational impacts, ensuring that resources are allocated to address the most critical issues first.
- Allocating resources efficiently: RCM enables organizations to optimize resource allocation by focusing resources on critical assets and failure modes, reducing unnecessary maintenance activities, and minimizing costs.
- Continuous improvement: RCM promotes a culture of continuous improvement, where organizations actively monitor asset performance, collect feedback from maintenance activities, and identify opportunities for optimizing and refining maintenance strategies over time.
The Future of Reliability Centered Maintenance
We delve into emerging trends, technological advancements, and evolving best practices shaping the future of RCM and driving innovation in maintenance strategies.
Emerging Trends in RCM:
The future of Reliability Centered Maintenance is characterized by several emerging trends reshaping how organizations approach maintenance practices. These trends reflect technological advancements, changes in industry standards, and evolving customer expectations.
Key emerging trends in RCM include:
- Embrace of Internet of Things (IoT): The proliferation of IoT devices and sensor technologies allows organizations to collect real-time data on asset performance, environmental conditions, and operational parameters, enabling more effective condition monitoring and predictive Maintenance.
- Shift towards asset performance management (APM): RCM is evolving towards a broader framework of asset performance management, which encompasses not only maintenance practices but also asset lifecycle management, reliability engineering, and performance optimization across the entire asset portfolio.
- Adoption of predictive analytics: Predictive analytics and machine learning algorithms are increasingly being integrated into RCM processes to enable more accurate prediction of equipment failures, optimization of maintenance schedules, and proactive identification of performance trends.
- Focus on sustainability and resilience: As organizations increasingly prioritize sustainability and resilience in their operations, RCM is adapting to address environmental impacts, resource efficiency, and the long-term sustainability of assets and infrastructure.
- Generative AI in Decision Making: The newer innovation of Generative AI plays a critical role in assisting the maintenance operations team in exploring asset performance and predictable failures deeper to define the new way of RCM.
Integration of Digital Technologies:
Digital technologies play a pivotal role in the future of Reliability-Centered Maintenance, enabling organizations to collect, analyze, and leverage data more effectively for maintenance decision-making and asset management. From advanced analytics to cloud computing, digital technologies offer new opportunities to optimize maintenance practices and enhance operational efficiency.
Data gathered from the machine should be combined with organization data such as parts, inventory, and supplier master required data and integrated between IT / OT systems. Application integration and digital APIs are the ways to build data consolidation for comprehensive decision-making.
Importance of Sustainability and Resilience:
In the future of Reliability Centered Maintenance, organizations are emphasizing sustainability, resilience, and environmental stewardship in their maintenance practices. As the impacts of climate change, resource scarcity, and regulatory pressures become more pronounced, RCM is evolving to address these challenges and promote more sustainable and resilient operations.
Key aspects of sustainability and resilience in RCM include:
- Environmental impact mitigation: RCM is increasingly focused on minimizing the environmental footprint of maintenance activities, reducing energy consumption, emissions, and waste generation, and promoting resource efficiency and circular economy principles.
- Resilience and risk management: RCM helps organizations build resilience against external threats, such as natural disasters, supply chain disruptions, and cybersecurity risks, by identifying critical assets, assessing vulnerability, and implementing contingency plans to mitigate risks and ensure business continuity.
- Asset lifecycle management: RCM extends beyond the operational phase of assets to encompass their entire lifecycle, from design and construction to decommissioning and disposal, enabling organizations to optimize asset performance, minimize lifecycle costs, and maximize environmental and social benefits.
Fogwing Asset+ for RCM Management:
Fogwing Asset+ Smart CMMS is the most advanced CMMS software with an asset reliability management solution leveraging IoT and AI technologies. Fogwing Asset+ provides modules to digitalize the maintenance operations (from MRO to Preventive) and monitor machine conditions using Fogwing Asset+ Kit devices. The Asset 360 view module within the asset+ application provides all aspects of the asset, including the reliability score.
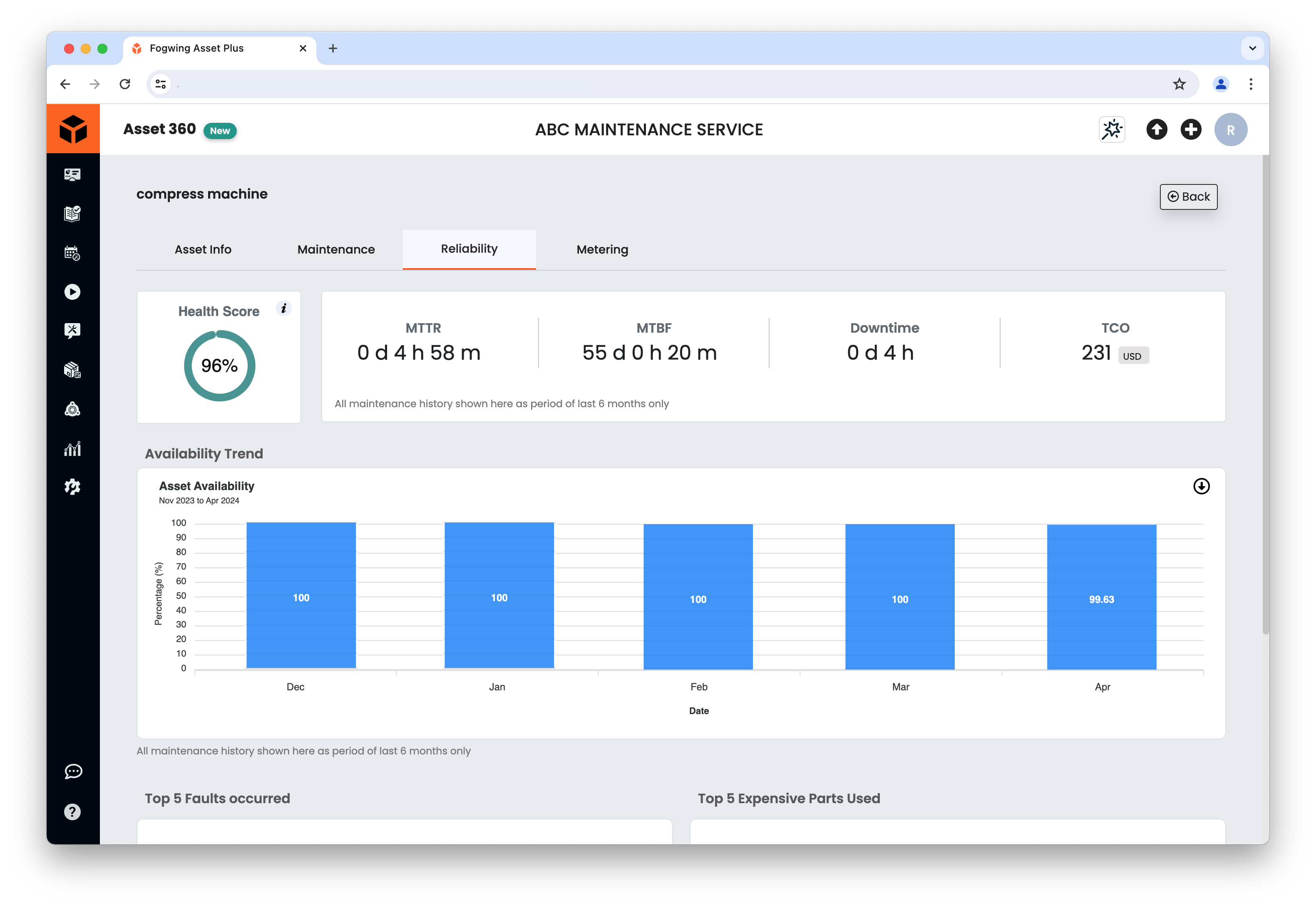
Conclusion:
Reliability Centered Maintenance (RCM) becomes evident that the future holds boundless opportunities for organizations striving to optimize their maintenance practices and achieve operational excellence. The evolution of RCM is not merely a response to technological advancements or industry trends; it represents a fundamental shift in how organizations approach asset management, risk mitigation, and sustainability.
From adopting predictive analytics and IoT technologies to integrating reliability-centered design principles and embracing sustainability and resilience, RCM is poised to revolutionize maintenance practices and drive innovation across industries. However, realizing RCM’s full potential requires more than technological prowess—it demands a culture of collaboration, continuous learning, and bold experimentation.
Are you ready to unlock the full potential of Reliability Centered Maintenance for your organization? Contact us today to learn how you can embark on your RCM journey and achieve operational excellence like never before.
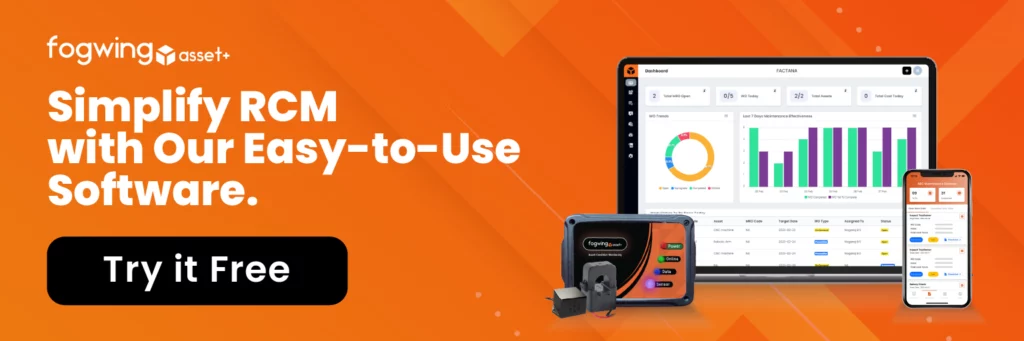