You might have heard the phrase,” A stitch in time saves nine”? Well, this saying holds profound wisdom for maintaining buildings and infrastructure.
In this fast-paced world, where people often prioritize everything over maintenance, it’s crucial to understand why this matters more than ever.
Deferred maintenance is the practice of postponing planned or unplanned maintenance, necessary repairs, and upkeep of buildings, equipment, and infrastructure.
In this blog, join us to uncover the stories behind the neglected repairs, unveil the hidden consequences they bring, and unlock the power of fixing things before they spiral out of control.
Trust them when experts say – that investing a little time today can save an astronomical amount of money and headaches tomorrow!
What is Deferred Maintenance?
Property management, facility management, and infrastructure maintenance generally use the term deferred maintenance. It refers to postponing essential maintenance and repair tasks for multiple reasons, like budget constraints, lack of time, or negligence.
At the same time, it may seem like a cost-saving strategy in the short term, but the long-term consequences can be severe. A deferred maintenance plan can majorly impact your organization’s value and safety.
Why Addressing Deferred Maintenance Matters?
Addressing defered maintenance is crucial. It prevents escalating costs and safeguards asset value and functionality. It upholds safety standards, protecting occupants and averting legal issues.
Moreover, it sustains operational efficiency, minimizing downtime and boosting productivity. Prioritizing maintenance is a strategic investment in an asset’s long-term functionality and value.
Additionally, it contributes to a positive reputation, instilling confidence in stakeholders. It also boosts employee morale and meets customer expectations for reliable products or services.
Lastly, it aligns with sustainability efforts, promoting energy efficiency and environmental responsibility. Addressing deferred maintenance safeguards an organization’s assets, reputation, and long-term success.’
What are the Risks and Dangers associated with deferred maintenance?
Deferred maintenance backlog is a common issue all maintenance managers face in factories and facilities. Delaying a repair or ignoring minor matters may seem like a budget-friendly decision at that time.
But it can do more damage in the long run to your organization’s assets. While some maintenance backlog is acceptable and unavoidable, maintenance managers must understand and create an appropriate maintenance plan according to the risk associated with organizations’ assets and business requirements.
If you are a maintenance manager facing excessive levels of maintenance backlogs, consider these consequences related to them:
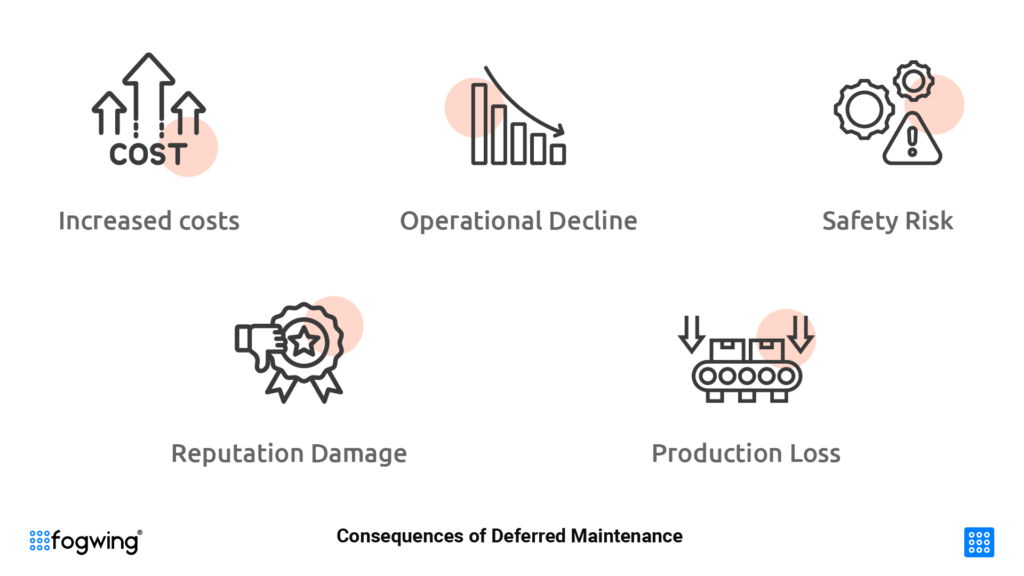
Increased costs –
One of the most apparent consequences is the increase in repair and replacement costs. Deferred maintenance might create a deceptive illusion of cost-saving in the short term, but it triggers a financial tremor. Neglecting minor repairs and replacements can often lead to significant issues that require extensive and expensive work. It strains the budget and introduces unexpected and burdensome financial pressure. This financial strain can disrupt planned expenditures, hinder the organization’s growth initiatives, and impede the organization’s ability to allocate resources efficiently. For example, not sealing and weatherizing your factories can result in much higher bills and extensive water damage over time.
Operational Decline –
A gradual deterioration of assets due to postponed upkeep is one of the consequences of deferred maintenance. This decline in operation causes gradual asset deterioration, reducing efficiency, reliability, and output quality and increased operational cost. Equipment inefficiencies and unplanned breakdowns disrupt regular operations, leading to productivity loss. Reliability falters as assets wear down, affecting consistent service delivery. The decline in quality affects the customer satisfaction. Besides this, the frequency of reactive maintenance increases, straining the organization’s budget. So, promptly addressing the factory’s maintenance needs is vital to mitigate these detrimental effects and sustain excellence.
Safety Risk –
Deferred Maintenance backlog escalates safety risks, jeopardizing facilities and equipment. Neglecting upkeep paves the way for potential accidents or compliance violations, posing significant threats to the organization’s assets. Faulty equipment or infrastructure can lead to hazardous conditions, increasing the likelihood of accidents. Moreover, compromising with the safety standards can lead to legal consequences and reputational damage. So, prioritizing maintenance is paramount in safeguarding the well-being of individuals and the integrity of assets.
Reputation Damage –
When the clients and Stakeholders witness neglected upkeep or maintenance, they easily interpret it as a lack of care and responsibility. So, deferred maintenance carries the hidden cost of reputation erosion. This perception of negligence can tarnish the organization’s reputation, potentially resulting in diminished trust and credibility. The clients or shareholders might hesitate and question the organization’s commitment to excellence and long-term sustainability after seeing its negligence towards its assets. Thus, It impacts physical assets and has long-lasting impacts on the organization’s image and guidelines in the industry.
Production Loss –
Maintenance is essential to an organization’s production rate. And maintenance backlog can take a toll on productivity, masking as a cost-saving measure. Deteriorating assets disrupt daily operations and reduce productivity, eventually leading to unplanned downtime, impeding workflow, and delaying project timelines. The loss of productive hours reduces output, hindering overall business performance. The ripple effect is felt across departments, affecting customer service levels and profitability. Ultimately, what initially appeared to be a cost-saving technique drained productivity and profitability, heightening the importance of proactive maintenance.
Best Practices for Addressing Deferred Maintenance
Addressing deferred maintenance is crucial, especially for factories and facilities that rely on machines, equipment, and assets. Maintenance managers should create a facility maintenance plan by prioritizing tasks based on their requirements and impact.
They should develop a detailed plan that includes budget estimates, allocate adequate resources for critical repairs and replacements, and involve skilled professionals for quality work.
Documenting the maintenance progress with records and photos and implementing preventive maintenance to avoid future damage is essential, which helps organizations run smoothly.
Fogwing Asset+, a CMMS and asset performance monitoring software, can help factories and facilities with preventative maintenance. It also enables the automatic creation of preventative maintenance with the help of advanced IoT.
It allows the Maintenance managers to foster a proactive maintenance culture and to conduct timely action required to save costs and preserve property value in the long run. Addressing deferred maintenance requires a strategic and systematic approach.
Here are some best practices –
Prioritize and Assess:
Identifying critical assets and areas that need immediate attention is vital. Conduct thorough assessments to determine the extent of the maintenance backlog.
Prioritizing and assessing the maintenance needs is a fundamental step in effective asset management. A comprehensive evaluation of assets provides a clear understanding of its current state.
It involves inspecting every component, from structural elements to mechanical systems and aesthetics. Prioritize the structural issues or safety hazards to ensure safety and prevent further damage.
On the other hand, organizations can schedule less urgent tasks like cosmetic enhancements or minor repairs for a later date. Additionally, prioritization considers factors like budget constraints and regulatory needs.
It ensures resource allocation and the prompt addressing of significant issues. Categorizing the requirements according to urgency and impact enables the maintenance managers to make informed decisions that maximize the long-term functionality and value of the assets.
Create a Maintenance Plan:
A robust maintenance plan is essential to track deferred maintenance. This comprehensive plan outlines specific tasks, schedules, and required resources to address deferred corrective maintenance.
It works as a roadmap, ensuring no critical maintenance needs are overlooked. By specifying responsibilities and timelines, the plan streamlines the execution of repairs and upgrades.
Additionally, it provides a clear framework for budget allocation and resource management. Regularly reviewing and updating this plan enables organizations to lay the foundation for a proactive long-term maintenance approach.
Allocate the budget Appropriately:
Stable financial conditions are crucial for successful asset maintenance management. Therefore, allocating the budget carefully while addressing deferred maintenance in factories and facilities is essential.
Always allocate ample resources for the immediate maintenance backlog and ongoing maintenance requirements. It’s prudent to consider the potential long-term cost savings from proactive maintenance.
Implement various maintenance strategies to safeguard your assets and mitigate the risk of more extensive and costly repairs in the future. This calculated move preserves the asset’s value and promotes sustained functionality.
It’s a careful financial decision that ultimately benefits the overall health and longevity of the assets in factories and facilities.
Utilize Technology and Software:
Leveraging technologies and specialized software, like Computerized Maintenance Management System (CMMS), is pivotal in streamlining maintenance efforts.
These systems enable precise tracking, scheduling, and management of maintenance tasks. Most industries are moving towards digitalizing maintenance activities with the fourth industrial revolution.
These platforms provide a centralized platform for creating work orders, tracking work orders, managing work orders, part inventory maintenance, and resource allocation. Additionally, CMMS can generate reports and alerts, ensuring timely attention to critical issues and reducing deferred maintenance.
With the implementation of technologies like Fogwing Asset+, a Smart computerized maintenance management software, and asset performance monitoring software, a maintenance manager can enhance operational efficiency, reduce downtime, and extend asset lifespan. This digital approach ultimately leads to more cost-effective and streamlined maintenance practices.
Train and Equip Staff:
Proper training and equipment are paramount for efficient maintenance operations. They were so, providing comprehensive training for your maintenance personnel, covering technical skills and safety protocols.
It is essential to make sure that maintenance personnel understand the proper procedure and working of the assets and maintenance software so that they can handle various tasks, from routine inspection to complex repairs and replacements.
Additionally, please provide them with the tools, equipment, and protective gear to execute their maintenance-related responsibilities effectively and safely. Investing in staff development enhances proficiency, reduces the likelihood of deferred maintenance, and ultimately contributes to a well-functioning and secure environment for the staff and assets.
Set Performance Metrics:
Establishing performance metrics is crucial to ensure that maintenance efforts are effective and accountable. It is essential to establish clear KPIs (key performance indicators) that align with the objectives of your maintenance plan.
The KPI matrix could include response times for urgent repairs, the percentage of preventive maintenance tasks completed, or the overall equipment uptime.
Regular tracking and analysis of these KPIs provide valuable insights into the effectiveness of your maintenance program. It allows for timely adjustments and improvements, ensuring that resources are allocated efficiently and that maintenance activities contribute to the long-term functionality and value of the property.
Prioritize Safety:
The well-being of employees and occupants is a top priority in any maintenance plan. It is crucial to address safety hazards first to protect them. Therefore, focus on critical systems and equipment that pose the highest risks.
Immediately rectify safety hazards such as asset breakdowns, structural instabilities, electrical issues, and fire risks. By addressing deferred maintenance promptly, you ensure a secure environment and demonstrate a commitment to the welfare of all stakeholders. This proactive approach lays the foundation for a responsible and effective maintenance strategy.
Engage Stakeholders:
Communication is the key to a successful maintenance initiative. So, communicate transparently with stakeholders, including staff, management, and facility users, to manage expectations and gain support.
Transparent communication is crucial for successful maintenance. Keeping everyone informed about progress and potential disruptions will help organizations manage expectations and gather essential support required for the process. Encourage feedback and address concerns promptly.
Engaging stakeholders in maintenance-related discussions fosters a sense of responsibility and ownership, creating a collaborative environment for practical maintenance efforts.
It also ensures that everyone associated with the asset or equipment understands the significance of timely repairs and issues with deferred maintenance, ultimately aiding the long-term functionality and value of the assets.
Document and Record-Keeping:
Keeping and managing detailed records of all the maintenance activities, including work performed, materials utilized, and costs incurred, enables the organizations to track progress and plan future maintenance tasks.
Systematic documentation and record-keeping are indispensable in maintenance management. Keep records of every maintenance activity, including specific work performed, materials utilized, and associated costs.
This data will accurately track work order progress, identify patterns or recurring issues, and provide valuable reference for future maintenance needs.
Documentation and record-keeping also help in budgeting and enable organizations to make informed decisions regarding resource allocation and deferred maintenance. Detailed record-keeping is a cornerstone of a well-organized and forward-thinking maintenance strategy.
Schedule Downtime Strategically:
Planning and scheduling the asset maintenance activities during periods of low demand or downtime minimizes disruptions to regular maintenance operations. Strategic scheduling of asset maintenance activities is vital for reducing disturbances and optimizing operational efficiency.
Ensuring that the organization maintains systems and equipment without affecting productivity is crucial. While scheduling asset maintenance activities, consider factors like production schedules, customer traffic, or peak usage time when setting maintenance dates.
By aligning maintenance with periods of reduced activity, you can maintain the integrity of assets and understand the operational needs. This approach leads to a smoother and more cost-effective maintenance process overall.
Seek Professional Guidance:
Professional guidance on efficiently addressing complex or critical maintenance tasks is vital for any organization. Consult experts or hire specialists who effectively manage complex or critical deferred maintenance tasks.
And bring proficiency and knowledge that ensures the maintenance task is handled precisely and complies with industry standards and guidelines.
This approach minimizes the risk of errors or subpar artistry associated with deferred maintenance backlog. Investing in the expert’s knowledge and expertise is a proactive step toward maintaining the long-term functionality and value of the property or asset.
How to Calculate Deferred Maintenance?
Deferred maintenance calculation is a process that helps organizations estimate the current cost of all the repairs and maintenance tasks that have been postponed for their assets or facilities.
This process involves identifying the maintenance tasks that have been overlooked, such as HVAC or roofing repairs, and evaluating their current conditions through inspections or expert consultation. Once you know these tasks’ present-day costs, you can calculate the total cost of deferred maintenance.
This calculation enables organizations to prioritize and allocate a budget for essential maintenance and repairs, which helps prevent further deterioration of assets.
It, in turn, leads to more cost-effective repairs or replacements in the long run. Tasks are prioritized based on safety, compliance, and cost-effectiveness, after which a detailed maintenance plan is created, allocating resources and setting schedules. Progress is monitored regularly, and priorities and budgets are adjusted as required.
Ultimately, the deferred maintenance calculation ensures that factories and facilities can keep their assets in good working condition and comply with safety and regulatory standards.
Step-by-Step guide to calculate deferred maintenance:
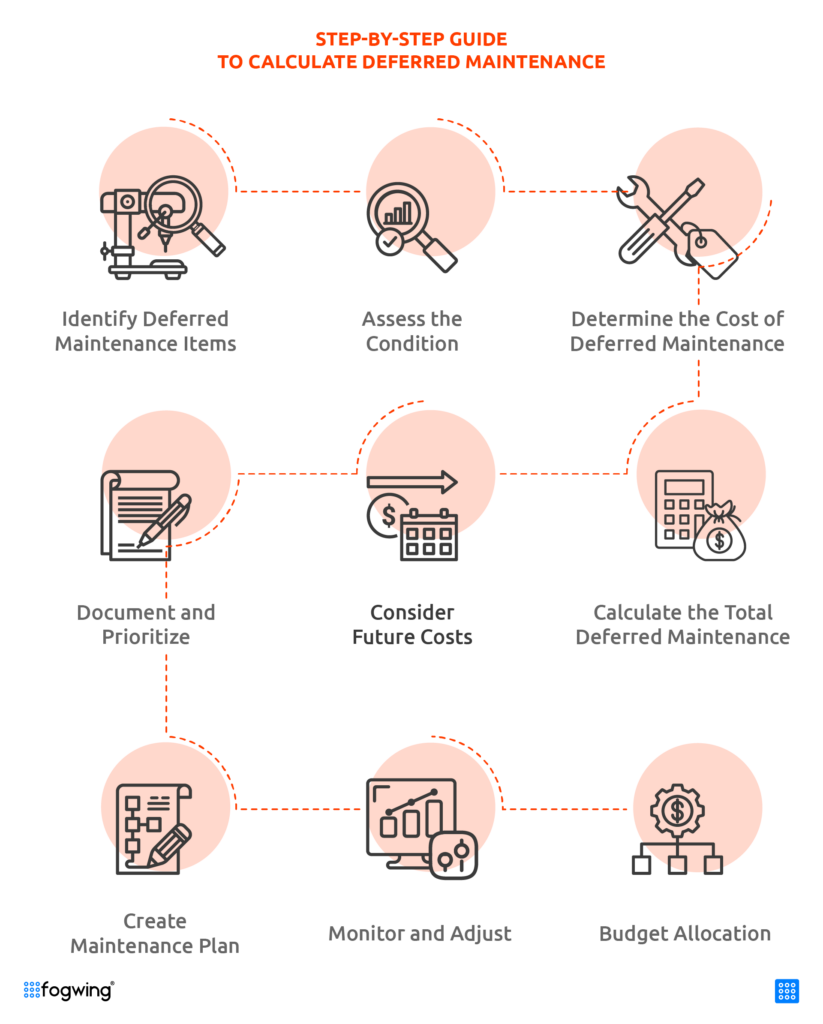
- Identify Deferred Maintenance Items: Make an inclusive list of all the maintenance tasks and repairs that have been ignored or postponed. This list could involve HVAC system repairs, Greasing, calibrating, painting, etc.
- Assess the Condition: Evaluate the current state of each deferred corrective maintenance item on the list. It could involve inspections, consultation with experts, or utilization of maintenance records to evaluate the condition of each asset.
- Determine the Cost of Deferred Maintenance: Once you evaluate the asset condition of each asset on the list, estimate the current cost of maintenance or repair for each item. To determine the project’s cost, connect with contractors, consult price guides, or utilize historical data as a reference.
- Calculate the Total Deferred Maintenance: Add all the estimated costs once you estimate each asset’s maintenance cost. It will give you the total amount of deferred maintenance.
- Consider Future Costs: It is essential to remember that the cost of deferred maintenance may vary over time because of inflation, and the condition of assets may worsen. So, the organizations must consider future costs or potential consequences of further delays.
- Document and Prioritize: It is essential to keep detailed records of calculations and assessments and prioritize deferred corrective maintenance based on safety, regulatory compliance, potential for further damage, and cost-effectiveness.
- Create Maintenance Plan: Developing a plan that addresses deferred maintenance items is essential. Allocate resources, schedule repairs, and establish an ongoing maintenance budget to prevent further delay.
- Monitor and Adjust: Once you create an asset maintenance plan, the next step is adjusting priorities and budgets based on changing circumstances and fresh insights. Continual monitoring of the maintenance plan is crucial. It involves tracking progress and making necessary changes. This approach ensures that resources are allocated effectively, preventing further deterioration of assets.
- Budget Allocation: Budget allocation is pivotal for managing deferred maintenance effectively. It involves assigning adequate funds in your financial plan to cater to immediate and ongoing maintenance. This strategic allocation ensures that resources are available for timely care, preventing the escalated deferred maintenance cost.
Extend your Asset Lifespan by Implementing Smart CMMS Software
Implementing Smart Computerized Maintenance Management System Software is a proven strategy to extend asset lifespan. It enables proactive maintenance planning, scheduling, and execution, preventing deferred corrective maintenance.
This advanced software efficiently tracks maintenance scheduling, work orders, and equipment performance. It ensures timely inspections and repairs, reducing the likelihood of costly breakdowns and maintenance backlogs.
By leveraging IoT technology, Smart computerized maintenance management platforms identify potential issues before they escalate. It saves cost and enhances operational efficiency, ensuring that assets operate at peak performance for an extended period.
Fogwing Asset+ is a smart CMMS and asset performance monitoring software that provides a comprehensive solution to tackle deferred maintenance for factories and facilities.
It seamlessly integrates with IoT sensors and AI technologies, enabling factories and facilities to conduct efficient asset maintenance. Additionally, it allows organizations to schedule timely preventive maintenance to avoid costly breakdowns and downtime.
The platform simplifies maintenance resource allocation and part inventory management, saving costs and enhancing operational efficiency. Real-time monitoring ensures that the organization’s assets remain in prime condition, reducing the deferred maintenance backlog and extending the lifespan of critical assets.
Organizations can use the Fogwing Asset+ platform to manage their assets more effectively, reduce maintenance costs, and improve operational efficiency. You can easily register for an account and gain access to all of Fogwing Asset+ platform’s features without any cost by visiting https://app.assetplus.ai/ and signing up today.
Conclusion
In the fast-paced world, it’s easy to prioritize immediate needs over maintenance. However, addressing deferred maintenance is crucial for sustaining the functionality and value of buildings and infrastructure.
In conclusion, deferred corrective maintenance can snowball into a significant crisis with far-reaching consequences. This blog highlights the importance of timely maintenance, shedding light on the hidden implications of neglecting repairs. From increased costs to declining operation and safety risks, the repercussions of maintenance backlog are far-reaching.
Implementing a computerized maintenance management system, like Fogwing Asset+, can help factories and facilities address deferred maintenance backlogs. The advanced technologies embedded in the Fogwing Asset platform ensure the longevity of their assets.