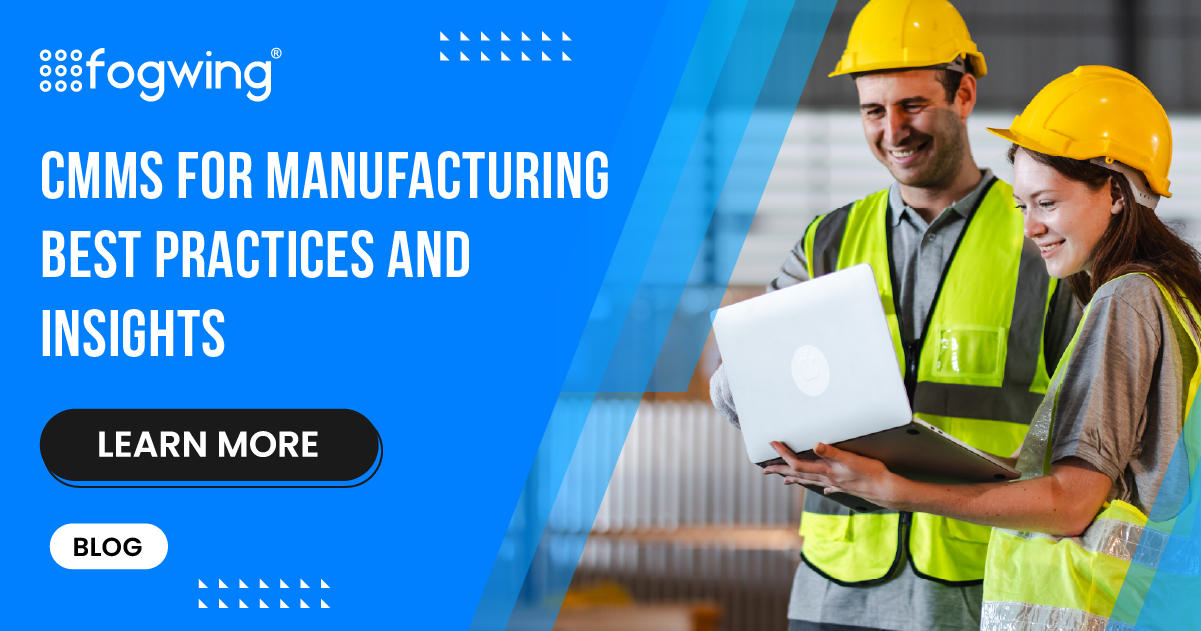
CMMS for Manufacturing: Best Practices & Insights
Manufacturing industries rely heavily on automation machinery and equipment for daily productivity. Any machine downtime during production will have a financial impact due to non-productive work hours, quality degradation, and