In the fast-paced manufacturing world, ensuring product quality is paramount. One way to achieve this is through the First Time Right (FTR) concept. FTR is a crucial aspect of modern manufacturing that focuses on producing high-quality products correctly the first time, without rework or adjustments. In this blog, we will delve into First Time Right, why it is essential, how to calculate it, its impact on manufacturing processes and costs, strategies for achieving FTR, challenges, and solutions.
What is First Time Right?
First Time Right (FTR) in manufacturing refers to the process of producing products correctly and with the desired quality parameters from the very first attempt, eliminating the need for rework, adjustments, or defects. This approach strongly emphasizes prevention rather than correction, leading to increased efficiency and cost deductions.
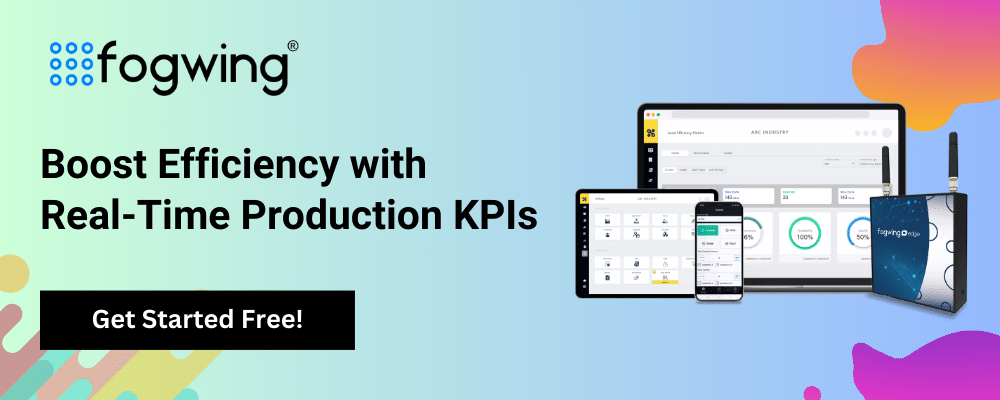
How to Monitor FTR?
Monitoring First Time Right (FTR) in manufacturing ensures consistent product quality and operational efficiency. To begin, it’s essential to establish clear and specific quality standards for your products or processes. These standards are the foundation for assessing whether tasks are completed correctly on the first attempt. The next step is implementing robust quality control measures, including inspections, testing, and real-time monitoring. These measures help promptly detect deviations from the established quality standards.
Collecting relevant data and metrics is key to monitoring FTR effectively. Metrics like the number of scrap rates or defects, rework rates, and the percentage of tasks completed correctly on the first attempt provide valuable insights into your FTR performance. Statistical Process Control (SPC) techniques can further enhance your monitoring efforts by analyzing process variations and ensuring stability.
Setting acceptable quality thresholds and implementing alarm systems or alerts that trigger when these thresholds are exceeded is crucial to maintaining First Time Right. Regular audits and inspections by quality control teams or independent auditors help ensure compliance with established standards. Encourage employees to report errors through a confidential error reporting system and establish feedback mechanisms for root cause analysis and corrective actions. Leveraging technology, such as sensors and data analytics, can provide real-time insights into process performance.
Regularly reviewing and analyzing data allows you to identify trends, patterns, and areas for improvement. Lastly, fostering a culture of continuous improvement within your organization ensures that you constantly strive to enhance processes based on insights gained from monitoring efforts. By following these monitoring strategies, you can effectively maintain FTR and reap the associated product quality and cost savings benefits.
Measuring and achieving First Time Right (FTR) in manufacturing involves a systematic approach to ensure that tasks are consistently completed correctly from the outset. Here’s a concise guide on how to measure and achieve FTR:
Measuring FTR:
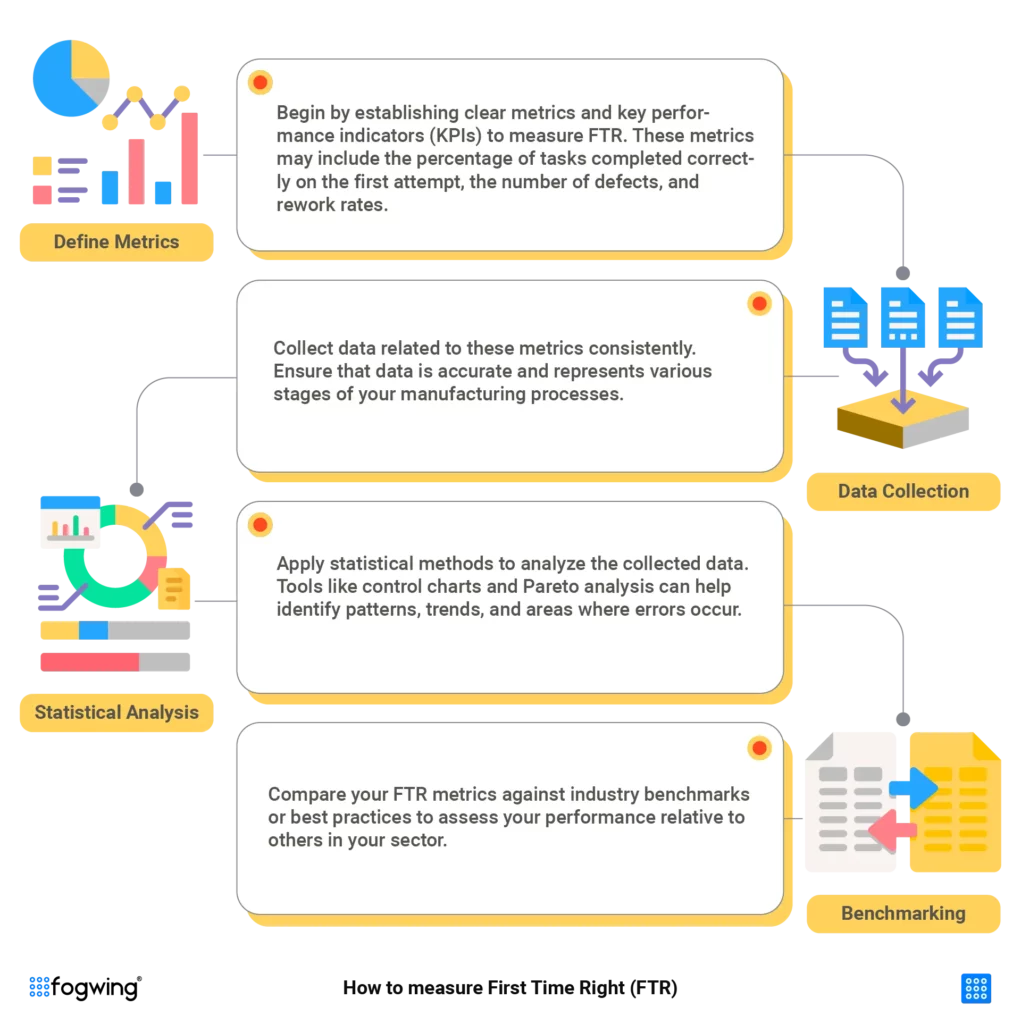
Define Metrics: Establish clear metrics and key performance indicators (KPIs) to measure FTR. These metrics may include the percentage of tasks completed correctly on the first attempt, the number of defects, and rework rates.
Data Collection: Collect data related to these metrics and KPIs consistently. Ensure that data is accurate and represents various stages of your manufacturing processes.
Use Statistical Analysis: Apply statistical methods to analyze the collected data. Tools like control charts and Pareto analysis can help identify patterns, trends, and areas where errors occur.
Benchmarking: Compare your FTR metrics against industry benchmarks or best practices to assess your performance relative to others in your industry.
How to Calculate First Time Right in Manufacturing
Calculating First Time Right involves measuring the ratio of products produced correctly on the first attempt to the total number of products manufactured. The FTR formula is:
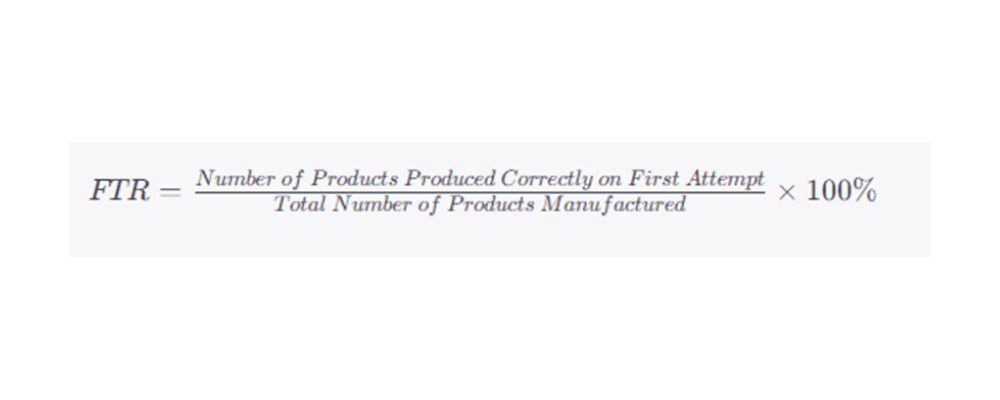
For example, if a company manufactures 1,000 products and 950 of them are produced correctly without rework or defects, the FTR would be calculated as follows:
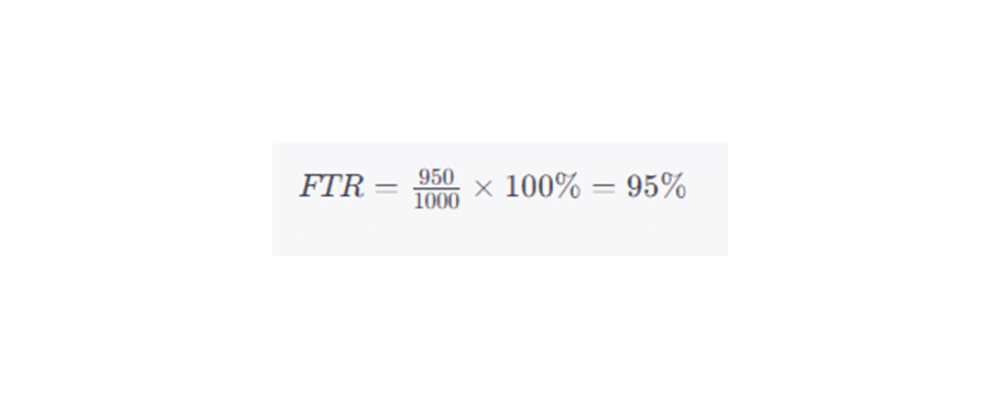
In this case, the FTR is 95%, indicating that 95% of the products were produced correctly on the first attempt.
The Impact of FTR on Manufacturing Processes and Costs
First Time Right has a profound impact on manufacturing processes and costs:
Improved Efficiency: FTR reduces the need for rework and adjustments, leading to a streamlined manufacturing process. This results in quicker production cycles and reduced lead times.
Lower Costs: FTR reduces material wastage and labor costs by minimizing rework and scrap rates. It also saves on the resources needed to address defects and customer complaints.
Enhanced Quality: FTR ensures that products meet quality standards right from the start, leading to fewer defects and lower chances of recalls or warranty claims.
Predictable Outcomes: FTR allows for greater predictability in manufacturing outcomes, making it easier to plan production schedules and allocate resources effectively.
Strategies for Achieving FTR in Manufacturing
Achieving First Time Right in manufacturing requires a combination of strategies and best practices. Achieving a high FTR score significantly depends on how well you implement the following five approaches. Here are the five fundamental approaches:
Step 1: Implement Comprehensive Training:
Properly train employees to perform their tasks accurately and efficiently. Well-trained workers are less likely to make errors.
Step 2: Develop and Implement Robust Process Design:
Introduce and implement robust, well-documented manufacturing processes and follow them consistently. Creating and sharing digital standard operating procedures (SOPs) with your workers or operators is essential.
Step 3: Adopt Quality Control Measures:
Implement quality control measures monitored at various stages of production to identify and rectify issues early in the process.
Step 4: Encourage Continuous Improvement:
Encourage and embrace a culture of continuous improvement, where employees are encouraged to implement process enhancement measures.
Step 5: Adopt Technology Integration:
To improve process accuracy, utilize advanced manufacturing technologies, such as automation, IoT (Internet of Things), and real-time monitoring.
Challenges and Barriers to Achieving FTR
While the benefits of First Time Right are clear, several challenges and barriers may hinder its implementation:
Resistance to Change: Employees may resist changes in established processes, making it challenging to implement new FTR strategies.
Lack of Training: Inadequate training and skill gaps can result in errors, reducing the chances of achieving FTR.
Complex Products: Manufacturing complex or customized products may make it more challenging to achieve FTR due to the inherent variability.
Cost of Technology: Investing in advanced technology can be costly, and some manufacturers may struggle to justify the expense.
Supply Chain Variability: Dependencies on external suppliers and fluctuations in the supply chain can introduce uncertainties that affect FTR.
Monitor and improve your FTR with Fogwing Matrix.
Monitoring and improving First Time Right (FTR) goals in manufacturing is critical for quality control and cost efficiency. Fogwing Matrix, empowered with the Industrial Internet of Things (IIoT), helps you achieve this. Here’s how to monitor and improve your FTR goals in manufacturing using Fogwing Matrix:
Data Collection and Integration:
Integrate the Fogwing Matrix with your manufacturing equipment, sensors, machines, and systems to collect real-time data on production processes and quality parameters.
Define FTR Metrics:
Fogwing Matrix Identifies the specific FTR metrics you want to monitor, such as defect rates, rework rates, scrap rates, and production cycle times.
Real-time Monitoring:
Use the Fogwing Matrix to monitor your manufacturing processes in real-time. Set up alerts and notifications for any deviations from quality standards.
Quality Control Systems:
Implement quality control systems within your manufacturing processes. Fogwing Matrix enabled with sensors helps in monitoring and controlling critical parameters.
Root Cause Analysis:
Fogwing Matrix’s analytics capabilities present the historical data and production records at the dashboard to identify the root causes of any particular defects.
Data Visualization and Traceability:
Fogwing Matrix offers digital records of each process at the dashboard, maintaining a comprehensive data visualization and traceability of the entire manufacturing process.
Remote Monitoring:
Fogwing Metrix, enabled with IIoT, provides remote monitoring of your entire manufacturing process, which helps to notify the plant manager if there’s any quality deviation. Plant managers can prompt the operators to take preventive measures before the process gets over.
Benchmarking:
To set improvement goals, compare your FTR performance against industry benchmarks or historical data.
Implementing and utilizing the capabilities of Fogwing Matrix, you can effectively monitor and improve your First Time Right (FTR) goals in manufacturing, resulting in higher product quality, reduced costs, and improved customer satisfaction.
To learn how to increase your manufacturing throughput while maintaining a high FTR, read this blog Maximizing Manufacturing Throughput: Strategies | Fogwing.io
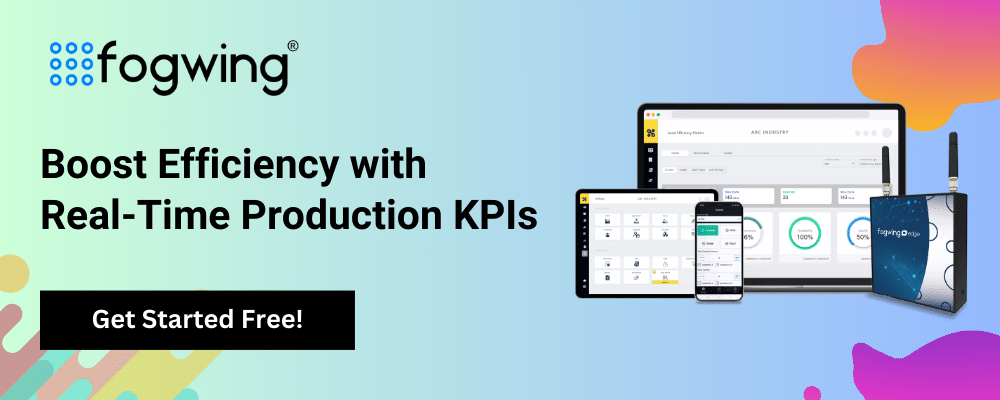
Conclusion
First Time Right (FTR) is not just a manufacturing concept; it’s a philosophy that can transform products, leading to efficiency, cost savings, and customer satisfaction. Achieving FTR requires training, process improvement, quality control, and technology integration. While challenges exist, companies implementing FTR can gain a competitive edge in today’s manufacturing landscape. As technology advances, FTR will play an increasingly critical role in delivering high-quality products efficiently while minimizing environmental impact. The journey towards FTR is ongoing, but the rewards for those who embark on it are substantial and enduring.