Manufacturing companies follow the traditional practice of preventive maintenance based on a predefined schedule regardless of asset age and usage conditions. However, this practice leads to unplanned downtime due to other factors such as production hours, quality of spare parts, etc.
Fault detection and diagnostics (FDD) have emerged as critical tools for addressing these challenges. Let’s explore FDD’s essence, its implementation in manufacturing, and its transformative impact on the industry.
What is Fault Detection and Diagnostics or FDD?
Fault Detection and Diagnostics is identifying abnormalities in machine health parameters and diagnosing their root causes. Think of it as a healthcare practice for your manufacturing equipment, which involves regular health checkups, precondition testing, spotting symptoms of issues, and determining the underlying root cause that needs a solution.
Fault detection means identifying the synthons of any abnormal conditions of machines when they occur, such as detecting overheating motors, high vibration in the conveyor belt, excess input voltage to machines, etc.
In contrast, diagnostics means exploring the root causes of these anomalies in machine health conditions and addressing them. Combined, these two processes create a powerful technique to identify potential machine failure ahead, reduce downtime, boost machine efficiency, and ensure manufacturing processes’ integrity.
As per the International Society of Automation, the average manufacturing plant loses up to 20% of productivity due to unplanned downtime since lack of FDD practice to predict and prevent the downtime earlier.
What are the benefits of FDD in maintenance operations?
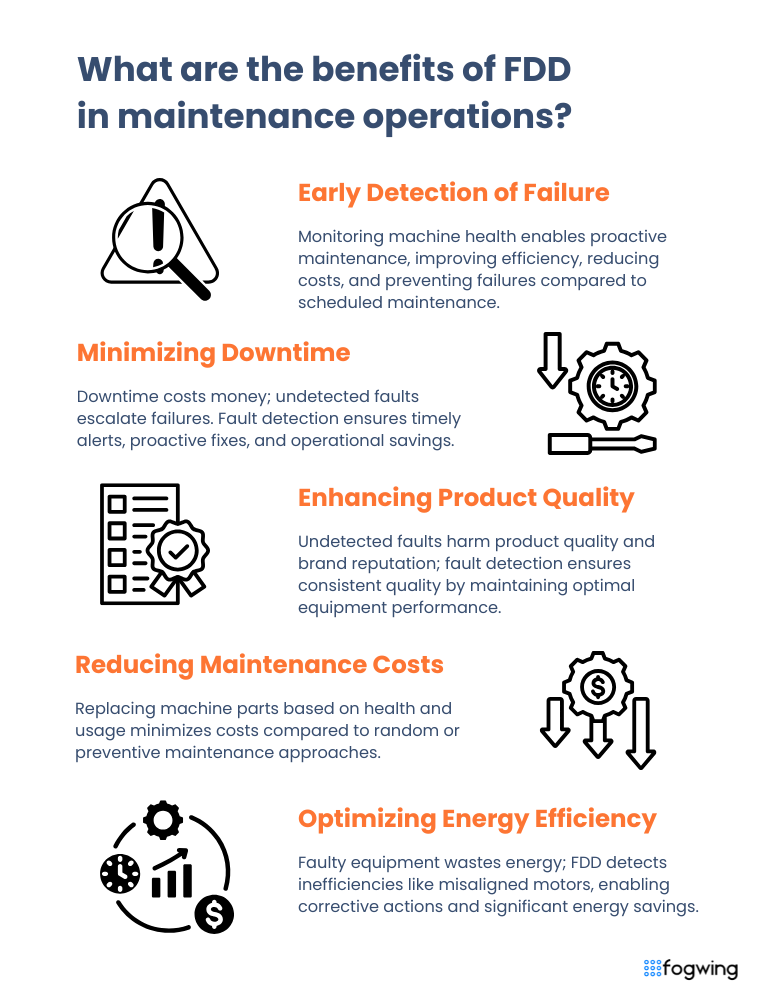
The following are the benefits of implementing FDD approach in asset maintenance operations.
Early Detection of Failure
Monitoring the health condition of machines or assets helps identify abnormalities early on, allowing proactive maintenance to prevent potential failures. Unlike traditional pre-scheduled preventive maintenance, condition-based maintenance improves machine efficiency and reduces operating costs.
Minimizing Downtime
In manufacturing, every minute of downtime can translate into significant financial losses. A single undetected fault can cascade into a major failure, halting operations. Fault detection and diagnostics provide timely alerts and insights, enabling proactive interventions that save time and money.
Enhancing Product Quality
Undetected faults often result in defective products, tarnishing a brand’s reputation. Fault detection and diagnostics ensure consistent product quality by maintaining equipment in optimal condition.
Reducing Maintenance Costs
When we replace parts and components of machines based on their health conditions and actual usage level, we reduce the unnecessary cost associated with random or preventive maintenance.
Optimizing Energy Efficiency
Faults in equipment often lead to energy wastage. For instance, a misaligned motor may consume more power to perform its function. FDD identifies such inefficiencies, paving the way for energy savings.
How to implement the FDD approach in maintenance operations?
The fault detection approach required real-time machine health data capture for fault identification, analysis, and maintenance actions. Implementing Fault detection and diagnostics involves several communication steps, each relying on sensors, data analytics, and domain expertise.
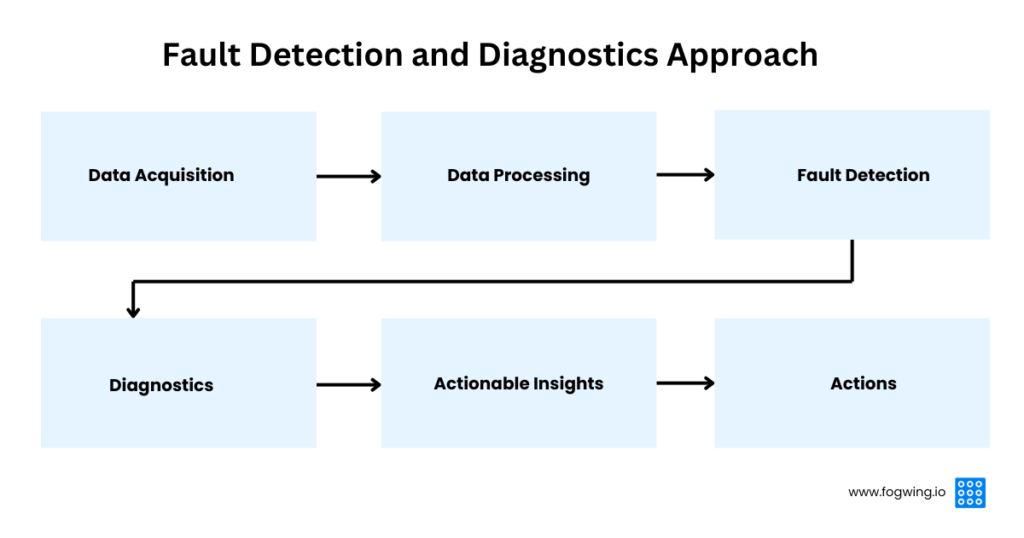
Step 1 – Data Acquisition
The acquisition of machine health data depends on the type of machine and its age. It is required to install sensors (if not already exist) based IoT devices in machines that continuously capture data such as temperature, pressure, vibration, vibration, and operational speed. These data should be transferred to a server for processing. These data form the foundation for detecting anomalies.
Step 2 – Data Processing
Once data is captured in common storage space, these raw data must go through a data integrity check, cleaned, and segregated for analysis. Advanced algorithms then analyze this data to detect patterns or deviations.
Step 3 – Fault Detection
Any machine health parameter that exceeds the threshold is also known as anomalies that require immediate attention. For example – unusual vibrations or temperature spikes are flagged as faults for the initial attack. This step often relies on machine learning models or statistical methods.
Step 4 – Diagnostics
Once a fault is detected, diagnostics help investigate its root cause. Diagnostics might pinpoint issues like worn-out bearings or misaligned components if a machine shows reduced efficiency.
Step 5 – Actionable Insights
Finally, based on the diagnostic analysis, the maintenance team should be directed to validate the machine’s physical condition again and apply the resolution to fix the problems.
Technologies to implement the Fault Detection and Diagnostics approach:
Traditionally, fault detection and diagnostics were part of preventive or inspection maintenance. However, advancements in modern technologies such as sensors, IoT, cloud computing, AI, and ML are helping implement the FDD practice on a fully automated, real-time basis for rapid actions.
1. IoT and Edge Computing for Machine Data Reading
Internet of things-based computing devices equipped with retrofit sensors can be attached to machines without modifying the machine functions. This retrofit solution will help capture machines’ health parameters in real-time and send them to a centralized or cloud server for data aggregation and processing.
2. Data Processing and Predictive Analytics
Moving beyond fault detection, predictive analytics forecasts potential failures, enabling even more proactive interventions.
3 CMMS Integration
FDD systems will be critical in achieving sustainability goals and ensuring equipment operates at peak efficiency with minimal resource wastage.
The Role of Humans in Fault Detection and Diagnostics:
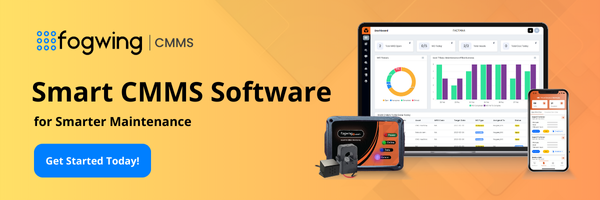
While technology is at the heart of FDD, the human element remains vital. Skilled technicians interpret diagnostic data, validate recommendations, and execute corrective actions. Their expertise ensures that the insights FDD systems provide translate into meaningful improvements.
Moreover, involving operators in FDD processes fosters a culture of collaboration. Employees who understand how FDD works and its benefits are more likely to trust and leverage the system.
What are all the Challenges in Implementing the FDD approach?
Despite its benefits, implementing FDD in manufacturing is not without challenges:
1. Data Overload
Manufacturing plants generate massive amounts of data. Filtering out irrelevant data to focus on actionable insights requires robust algorithms and computing power. A manual approach of filtering data, matching with events, and identifying the actions are impossible. Computing technologies such as big data processing and machine learning are required to automate data processing.
2. Integration Complexity
Many factories operate a combination of legacy and modern systems that may not seamlessly integrate with modern FDD technologies. Bridging this gap demands significant investment and expertise.
3. False Positives
Inaccurate fault detection can lead to unnecessary downtime and repairs. Continuous tuning of FDD models is essential to minimize false positives.
4. Cost Concerns
Advanced FDD systems often have a hefty price tag, which can be challenging for small and medium-sized manufacturers.
Real-Life Industrial Applications of FDD in Manufacturing
1. Automotive Manufacturing
In automotive plants, precision is non-negotiable. FDD systems monitor assembly lines for faults such as robotic misalignments or tool wear. Early detection prevents costly recalls and ensures vehicles meet stringent safety standards.
2. Food and Beverage Industry
Equipment like mixers, conveyors, and packaging machines are crucial for maintaining product consistency. FDD systems detect faults such as temperature fluctuations or inconsistent speeds, ensuring product quality and compliance with food safety regulations.
3. Semiconductor Manufacturing
The semiconductor industry demands ultra-clean environments and precise equipment calibration. FDD systems help maintain these standards by detecting even microscopic deviations in process parameters.
4. Battery Production Plants
Manufacturing involves complex chemical and mechanical processes, whether producing lithium-ion or lead-acid batteries. FDD identifies faults like electrolyte imbalances or overheating, safeguarding product quality and operational safety.
How does Fogwing AOM’s solution help implement FDD?
The Fogwing Asset Operations Management Software is a comprehensive suite of applications for enterprise asset management, asset maintenance, and asset performance management using IoT that empowers manufacturers with cutting-edge Fault Detection and Diagnostics (FDD) capabilities.
By seamlessly integrating real-time data from assets, sensors, and asset management processes, Fogwing identifies anomalies, diagnoses faults, and predicts potential failures before they disrupt operations. This proactive approach minimizes downtime, enhances asset reliability, and ensures consistent production quality.
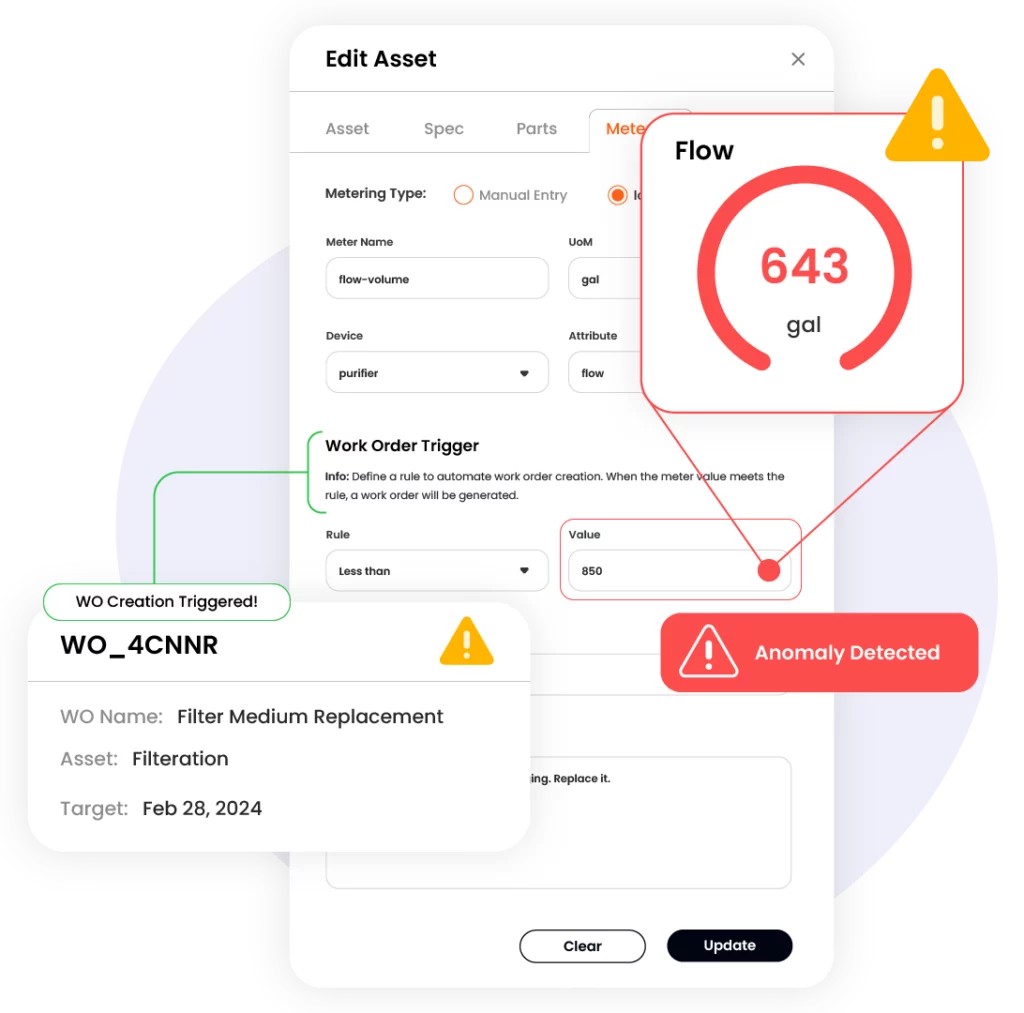
With its AI-powered analytics, the platform processes vast volumes of data to uncover hidden patterns and root causes of faults. Fogwing APM’s customizable dashboards provide actionable insights, enabling teams to prioritize corrective actions and streamline maintenance strategies. Its compatibility with diverse industrial equipment and scalability make it a perfect fit for manufacturing environments of all sizes.
Key Benefits of Fogwing AOM Solution:
- Proactive Fault Prevention: Early detection reduces unplanned downtime and prevents costly breakdowns.
- Enhanced Efficiency: Streamlined diagnostics improve response times and minimize maintenance delays.
- Cost Optimization: Reduces operational and repair costs through predictive insights and targeted actions.
- Improved Reliability: Boosts equipment uptime and operational efficiency.
- Real-Time Visibility: Continuous monitoring ensures round-the-clock operational insights.
Fogwing AOM transforms FDD into a strategic advantage, ensuring seamless operations, reduced costs, and improved reliability for manufacturers aiming to thrive in a competitive landscape.
Conclusion
Fault Detection and Diagnostics is not just a technological innovation; it’s a paradigm shift in how we approach manufacturing. By combining cutting-edge technology with human expertise, FDD empowers manufacturers to tackle challenges head-on, turning potential crises into opportunities for improvement.
For manufacturers striving to stay competitive in a rapidly evolving landscape, embracing FDD is not just an option—it’s a necessity. As we look to the future, the fusion of technology and human ingenuity will undoubtedly redefine the possibilities of modern manufacturing.
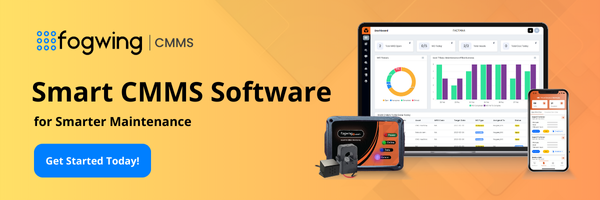